Hear Mark read the post (subscribe to the podcast series):
I don't normally pay too much attention to TV commercials, but I was working out the other day and had TV streaming through my iPhone. Appropriately enough, a Nutrisystem ad with Marie Osmond started playing.
I wouldn't have really watched the ad, but the app froze up and this image got stuck on the screen as the audio continued… so I was able to take a screenshot.
Lean? All those phrases on screen made me think of the Lean methodology in organizations, too.
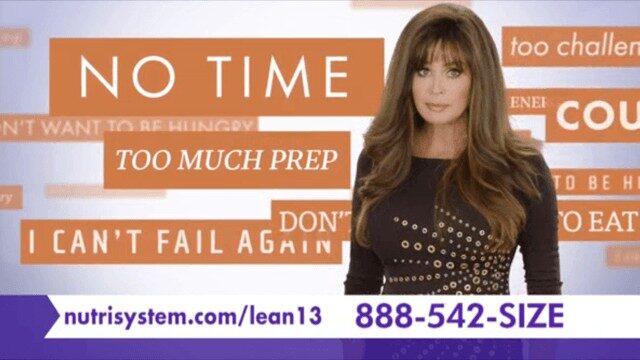
It's a weight loss program called “Lean 13.” It's the everyday use of the word “lean,” as in thinner, that has nothing to do with the Lean methodology and the Toyota Production System. They're promising that you'll lose 13 pounds in the first month.
Here is the video:
As with the Lean methodology, in hospitals, factories, or wherever, your results might vary based on a number of factors. For example, Nutrisystem can't stop a customer from supplementing their food with Buffalo wings and chocolate milkshakes.
We have situations out there where people say, “We tried Lean and it didn't work.” Maybe it was because they were cherry picking a few Lean tools or they just thought Lean was about cost cutting, instead of focusing on safety, quality, patient flow, and employee engagement.
There are also many situations where leaders don't really try Lean. They say things like “our culture isn't ready for continuous improvement.” That's a self-defeating excuse (more about this in a future post).
But look at the words and phrases that were floating on screen with Marie. This is what really caught my eye.
These are excuses for not starting a weight-loss program or a fitness program. They're also excuses for not starting with Lean:
- No time
- Too much prep
- Too challenging
- I can't fail again
If you think you have no time, that's a problem to solve. See my article about making time for improvement.
See also the thoughts of some Lean authors and consultants:
If leaders failed in the past with TQM, Six Sigma, and other methods, they might be skeptical about trying something new.
See my post about the book Why TQM Fails and why that's relevant to today's Lean movement.
I guess the same is true when it comes to health and fitness. Sometimes, people have tried other programs and, whether it's the fault of the program or not, they might be afraid to try something new.
It's a shame, since health and fitness are so important. It's also a shame that healthcare organizations miss out on the opportunity to use Lean to improve patient care, create better workplaces, and to improve the organization's bottom line.
How can we shift from making excuses to solving problems, as I've talked about before?
What can we do about that? How can we shift from making excuses to solving problems and making progress?
What do you think? Please scroll down (or click) to post a comment. Or please share the post with your thoughts on LinkedIn – and follow me or connect with me there.
Did you like this post? Make sure you don't miss a post or podcast — Subscribe to get notified about posts via email daily or weekly.
Check out my latest book, The Mistakes That Make Us: Cultivating a Culture of Learning and Innovation:
Mark;
What a great comparison. As our group reflected on our lean focus for 2016, a common theme was “we’re too busy.” I’ve used a similar analogy that at times, eating vegetables and drinking water is a good thing. Yet deep in the heart of Texas few are interested when at times the healthy items just don’t seem to taste great. Certainly change, adapting, pulling continuous improvement forward, and simply making those daily choices to improve are challenging. Both “leans” remind me of my favorite Deming quote, “Change is not required, because survival is not mandatory.”
Great analogy and food for thought!
Thanks for always making the message relevant!
Thanks, Rick. I think the key is knowing how to cook healthy stuff in a way that makes it taste better. Although, in Texas, that often means adding bacon to your vegetables :-)