I first blogged about this article back in 2009 and it's still online:
The sub headline talks about hospitals being “desperate to cut costs.” Has that changed?
I wish the motivation was more often about hospitals being “desperate to improve patient safety and quality.” Lean can address that too and should be mentioned, even in a publication for CFOs.
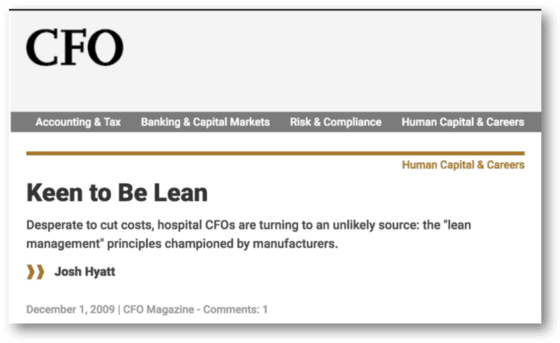
As quoted in my book Lean Hospitals, Bill Douglas, chief financial officer at Riverside Medical Center (Kankakee, IL), said:
“Lean is a quality initiative. It isn't a cost-cutting initiative. But the end result is, if you improve quality your costs will go down. If you focus on patient quality and safety, you just can't go wrong. If you do the right thing with regard to quality, the costs will take care of themselves.”
Hear Mark read this post — subscribe to Lean Blog Audio
The CFO article talks about Lean being a tough, but necessary, cultural transformation. It reminds me of LEI's Jim Womack's expression that “managers will try anything easy that doesn't work before they will try anything hard that does.”
“Hospitals need to eliminate anything that does not add value to the customer,” says Mike Chamberlain, president of consulting firm Simpler North America and general manager of its health-care division. “They can't generate that amount of savings through easy measures. They need to undertake a cultural transformation.”
Can hospitals, here as we're going into 2017, generate significant cost savings by sending staff home early and other traditional cost-cutting measures? Are layoffs really helping? Some CEOs have learned that layoffs can be counterproductive.
What's the benefit that comes from redesigning care delivery, as ThedaCare has done? From changing the culture and the management system, as ThedaCare and others have done?
Also from the CFO article:
“The move to lean management is just such a transformation, and it certainly doesn't come easily. “People sometimes have a bad reaction to change,” says Kevin Higdon, CFO of Elkhart General, a $600 million (in gross revenues) hospital near South Bend, Indiana. Elkhart has implemented lean techniques for the past two years.”
If people are having a bad reaction to change, is that the employees' fault or a lack of leadership? A lack of communication? People don't react badly to improvement… if you're listening to them and engaging them. That's why Kaizen and Change Management strategies can make this Lean transformation go more smoothly.
The CFO article also said:
“The lean-manufacturing approach — which evolved from the Toyota Production System that W. Edwards Deming influenced — progresses in a never-ending series of kaizen (Japanese for “incremental improvements”) intended to identify process failures.”
The article gets it right. It still frustrates me that too many healthcare organizations would say they are “implementing Lean,” but they aren't trying to engage everybody in ongoing continuous improvement. Without Kaizen, it's not really Lean, since “continuous improvement” (along with “respect for people”) are the core pillars of the Toyota Way management system.
It's also unfortunate that more organizations don't embrace Deming principles as their foundation for Lean. That's why I'm doing a series of workshops about Deming principles and how they should influence “daily Lean management” efforts:
- Lean Healthcare Transformation Summit – Europe (March)
- Catalysis Workshops – Seattle (May)
- Lean Healthcare Transformation Summit – America (June)
From the article again:
“Elkhart General stages “Rapid Improvement Events” one week a month, assigning a different team of employees to figure out how to improve a process or eliminate waste. All told, the hospital has saved about $6.5 million.”
Rapid Improvement Events are good. They're helpful as a way to solve relatively complex and cross-departmental problems. I hope Elkhart General built upon those monthly events to also engage people in continuous improvement each and every day (as ThedaCare made that transition).
The article was published at a time when Toyota's quality reputation was near it's lowest point in modern times. That added another wrinkle to the “patients aren't cars” argument. People were saying things like, “Toyota's quality is terrible now, so why should we emulate them?”
The article asked:
“Are doctors and nurses to be thought of as assembly-line workers focused on efficiency and speed at the expense of care and compassion?”
The answer is NO.
With Lean, we get quality and efficiency at the same time, by focusing on the customer (the patient) and reducing waste. We can have more compassionate care (more “loving care“) by freeing up staff member time.
I was quoted in the article:
“A lot of the anxiety about lean comes from the fear that all of the methods from Toyota will be copied,” says Mark Graban, a former industrial engineer who has worked in manufacturing as well as health care and who is now a senior fellow at the nonprofit Lean Enterprise Institute. “But hospitals are implementing lean methods to help them support what they are trying to do, not to make them into any less of a caring environment.”
We're not turning hospitals into factories. We're not just copying blindly from Toyota (or from ThedaCare). We're learning, adopting and adapting. We're making hospitals better hospitals. Integrated health systems should become better systems that help keep people healthy.
Bob Emiliani was also quoted:
“Lean management focuses on improving processes, so its principles and practices are applicable to any business,” says Bob Emiliani, a lean educator who works with senior managers. “There's a potential role for it any time there's a need to reduce costs, although to think of it solely as a cost-cutting method is a misinterpretation.”
I agree and blogged about that idea here:
The article also says:
“Physicians, of course, may be less amenable to being told how to do their jobs.”
I'm not sure ANYBODY likes to be told how to do their jobs. That's why the process of creating standardized work involves staff members, regardless of their role or level. The process of Kaizen, or continuous improvement, is done BY the people doing the work — it's not done TO them. Or it shouldn't be.
The article also talks about the importance of not using Lean to drive layoffs… a message that hasn't always been understood in the years that have passed since 2009:
“In fact, that's one of the paradoxes of the lean approach: in order for it to work, employees have to be committed to it, but “if it leads to layoffs, then people will quit participating,” says Graban. At Denver Health, management announced a no-layoffs philosophy at the same time it instituted lean.”
I've blogged about this theme:
As much as you can generalize, how far do you think healthcare has progressed since 2009? How has your organization done? What are your goals for 2017?
Please scroll down (or click) to post a comment. Connect with me on LinkedIn.
Let’s work together to build a culture of continuous improvement and psychological safety. If you're a leader looking to create lasting change—not just projects—I help organizations:
- Engage people at all levels in sustainable improvement
- Shift from fear of mistakes to learning from them
- Apply Lean thinking in practical, people-centered ways
Interested in coaching or a keynote talk? Let’s start a conversation.
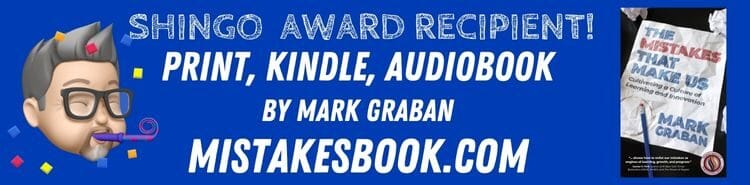
Hello, I enjoyed your article a lot. It has been tough to us to address these initiatives here in Mexico. We have struggled with mentality challenges due to the cultural aspects of people.
When you mention “The CFO article talks about Lean being a tough, but necessary, cultural transformation. It reminds me of LEI’s Jim Womack’s expression that “managers will try anything easy that doesn’t work before they will try anything hard that does.”
What would be the right approach to convince CFO and get support from them to implement LEAN?
Kind Regards
I’m not sure how much you “convince” executives as much as you help them learn and discover.
Maybe a CFO is inspired by other CFOs, like Orry Fiume who have shared their experiences with Lean.
I guess you could talk to the CFO about how Lean should benefit financial measures. Or, I’d hope you have a CFO, like Bill Douglas, who realizes that quality is also really important.
We didn’t have to convince Bill about Lean… he just sort of “got it” intuitively.