Continuing my series of blog posts about my July trip to China, today's post is about the second city I visited: Shanghai.
This post has some photos and descriptions of the high-speed train trip and other travel-related details. You can also read previous posts about the Lean healthcare conference held in Beijing on the first day.
The last presentation on Day 1 was a segue to the Shanghai visit, as it was by a VP from Shanghai Children's Medical Center. I wasn't able to visit the hospital, unfortunately.
Some highlights and notes from the presentation – quotes from the speaker or my best attempt at paraphrasing and my comments are in italics.
Their JCI (Joint Commission International) system “helped us do more with continuous improvement.”
They have 200 Q.C. (Quality Control) metrics. This begs the question of what the “KEY Performance Measures” or KPIs are… are more measures necessarily better?
“Continuous improvement cannot be done well without the support of IT or ‘big data' to try to visualize metrics.”
They have (or desire, I wasn't sure) a “non-punishment” system for reporting events (something aviation safety experts have long called for in American healthcare).
In the model of PDCA (or PDSA), we have to try to find more problems so we can have more improvement.
The hospital reduced “sentinel events” from 70 in 2014 to 14 in 2015.
Hospitals should not just improve themselves but need to communicate and share with others for the sake of improving our country's health system.
They had a partnership with GE in 2013 on Six Sigma, following the Work-Out model (something I've seen be effective in the context of Lean, too).
They introduced Six Sigma last year, with two-day training classes and introduced Lean projects.
They are “facing more pressure on appointment waiting times” and are working to reduce MRI waiting times (as I did with a children's hospital in Dallas, cutting waiting times from 12-14 weeks to just 2-3 weeks, results that have been sustained since 2009).
They are using root cause analysis and showed a fishbone diagram, as pictured below:
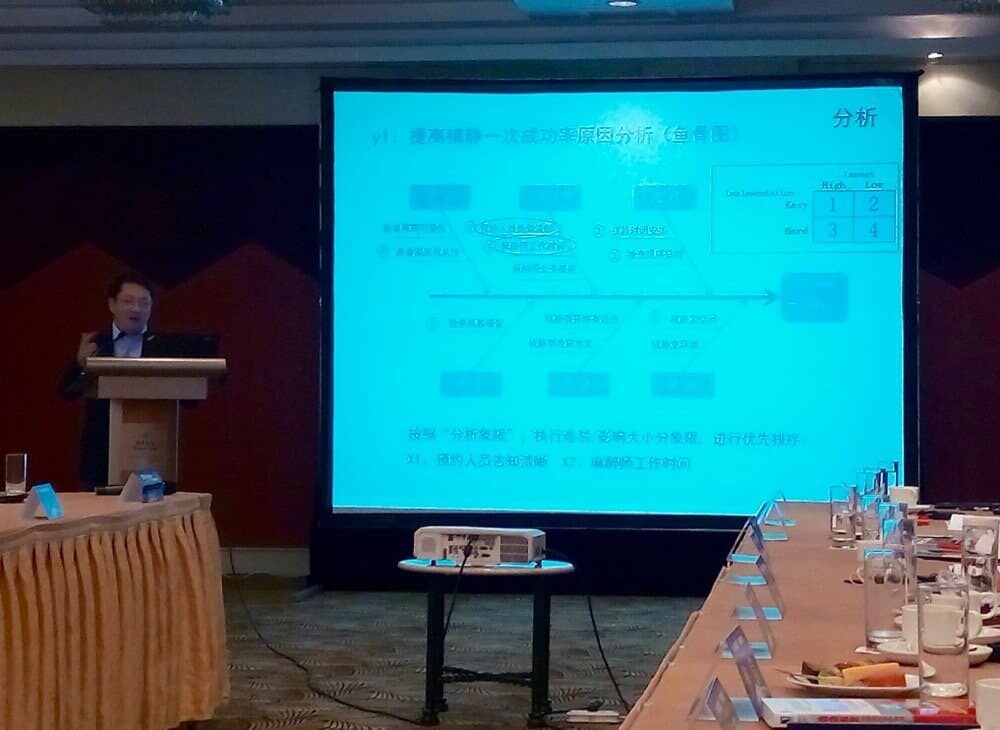
They have “Lean Care” projects that are focused on engaging front-line staff, asking what, when, who, and why (in Lean problem solving, the “who?” question isn't about blame — who is at fault? — but more a matter of checking facts — who is involved?)
Their final thoughts were, “Continuous improvement is very important… and should engage everyone, not just hospital presidents.” I'm really glad that message is being spread in China!
There was also a group Q&A discussion within the room:
Q: Are there incentives for employees to participate in improvement? Will people not want to change if their burden increases?
This question was asked a few times during the trip – incentives or rewards for participation. It was a bit surprising, but I guess it shows that current-day China is more capitalistic than communist (it's “socialism with Chinese characteristics“).
I've found that people participate in continuous improvement because they WANT to. Intrinsic motivation (making things better for patients and creating a better workplace) is a powerful thing. Formal rewards, bonuses, and incentives can get in the way of that improvement process.
The speaker from Shanghai and their goal is “making work easier” and that providing value to patients isn't a “burden.”
That's exactly what I've been teaching and seeing through my Lean and Kaizen work.
Q: In China, we want every patient to be satisfactory… the U.S. has ESI (Emergency Severity Index) and limited resources, so they have to prioritize?
I think there's an interesting bias or perspective in that question, as asked by a Chinese participant. American hospitals should want every patient to have a satisfactory experience. The ESI process doesn't deny care to anyone… it helps prioritize those who need help most urgently (who would potentially die or be harmed by waiting?).
The Shanghai presenter said that “FIFO” (First-In-First-Out) has been the norm there and “we should learn from the US & ESI system.”
There was also discussion about the “need to reduce the number of medical disputes and settlements and judgments paid out.” If you take the initiative to talk to patients, you reduce the number of disputes (similar things have been found in the U.S., where admitting mistakes leads to fewer lawsuits). Chinese hospitals have to buy medical accident insurance for physicians, so everybody has an interest in reducing harm (not just reducing lawsuits).
In Shanghai, I repeated the same presentation in a hospital auditorium full of doctors, nurses, and leaders.
There was construction taking place at the hospital… and this was a statue of Chiang Kai-Shek that we saw as we walked in.
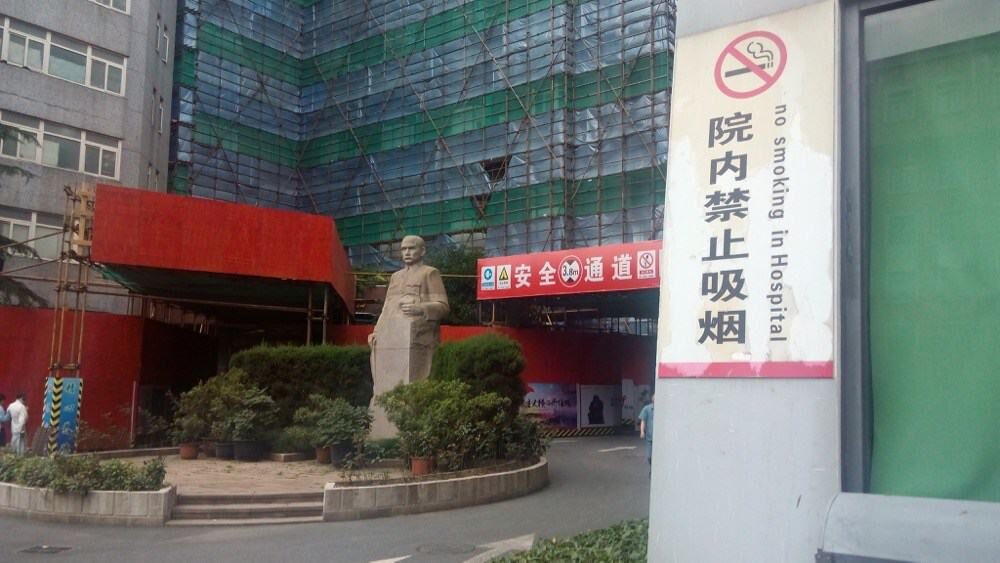
During Q&A time, there were familiar questions and concerns raised:
- The head of a respiratory hospital said, “But people say they are too busy to improve…” I've long said you have to “make time for improvement” and I've done a webinar on that topic.
- “If people try to make an improvement and they're not good at it, should I punish them?” The short answer to that is “No.” Leaders need to be coaches, not judges. It's our job to help people get better at improvement… learning by doing, with good coaches.
- “Does this require a department?” Probably at first… but over time, as Lean shifts from a new program to “the way we do things,” the size of that group can shrink, and Lean is coached more by line managers than process improvement specialists.
People were, again, very nice and asked me to sign books for them:
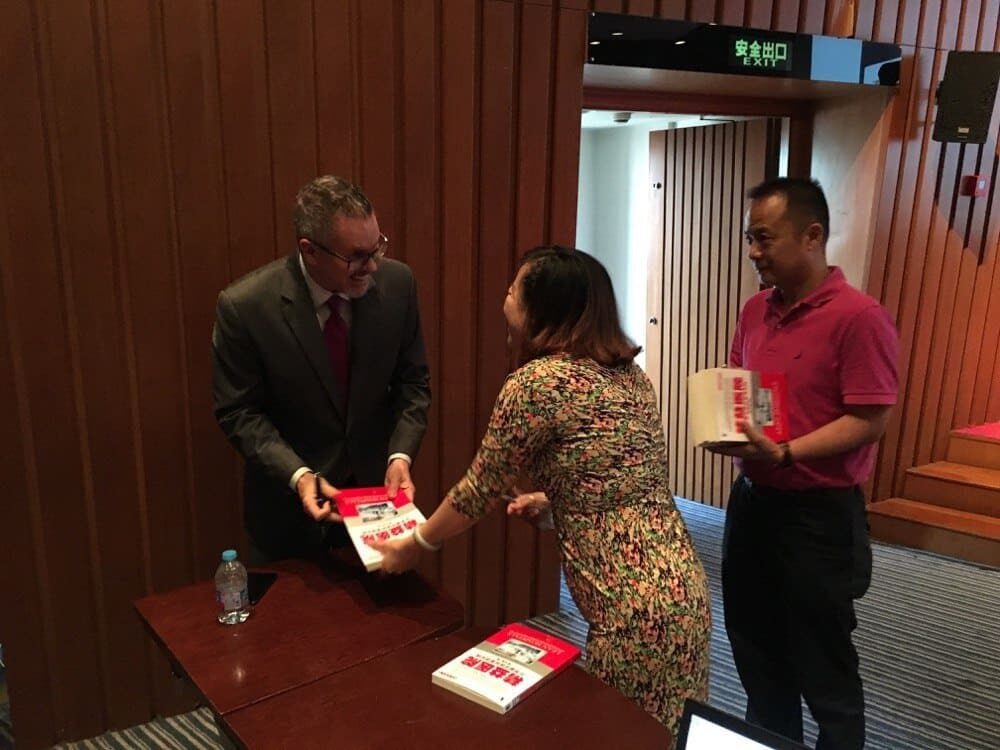
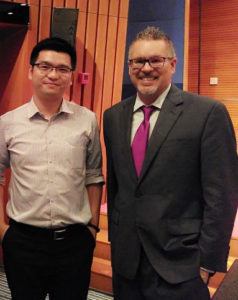
I met a young Industrial Engineer, Dan, who was in the audience at the Shanghai event. He was a math major, who worked in banking in Singapore, and then realized he wanted to do something different with his life and career. So, he moved to a hospital there, where he was introduced to Lean before returning to China.
I bet he'll do great things to help improve healthcare.
Oh, and there was a bar in Shanghai with a fantastic whiskey selection (Bar Constellation):
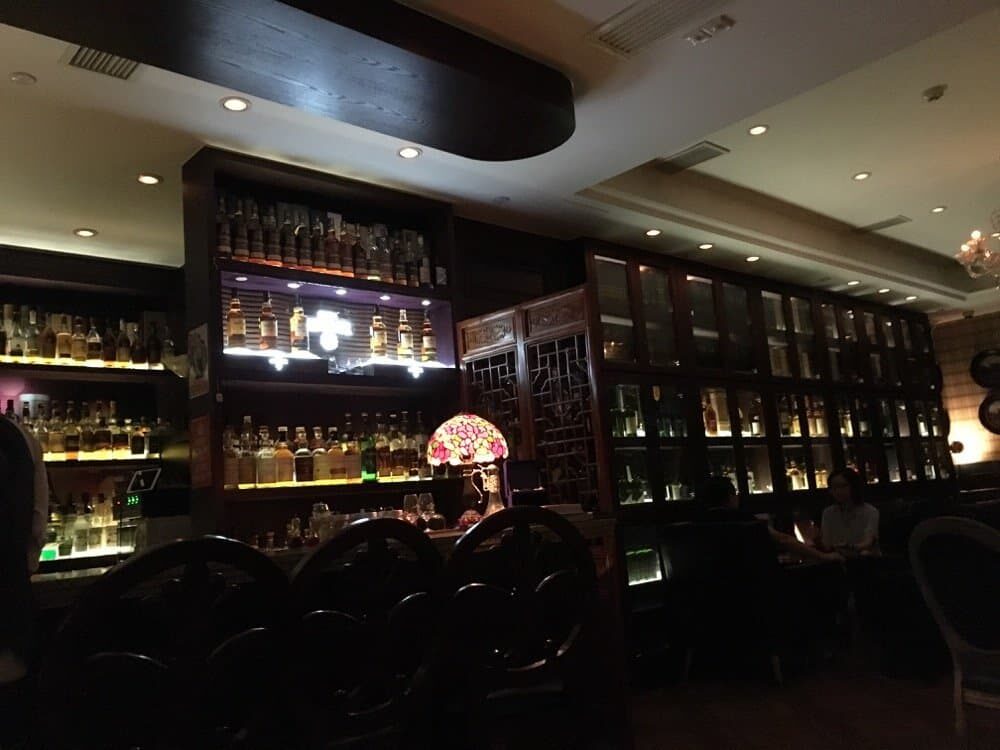
And some fantastic food at a restaurant nearby (duck – basically just the skin here):
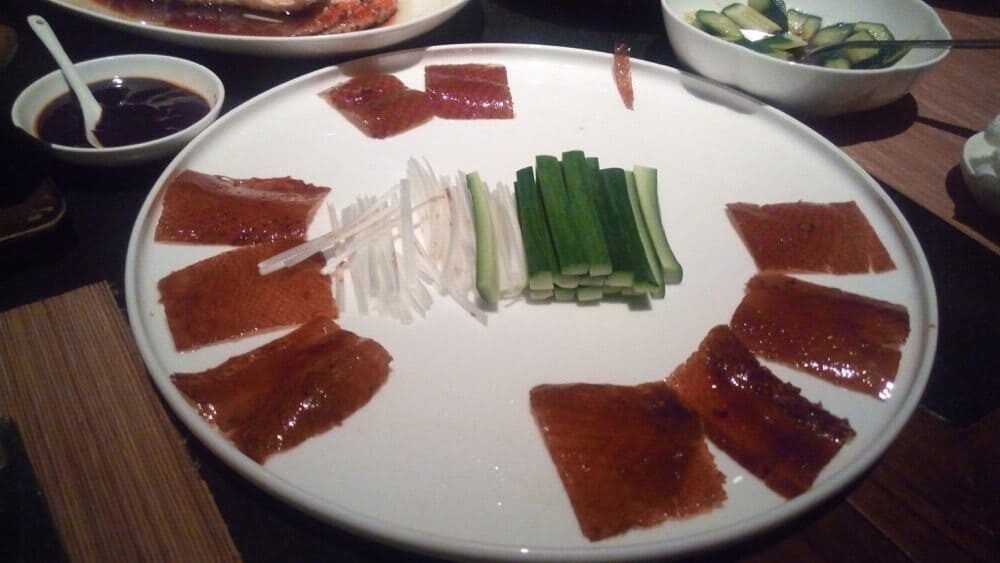
My next posts in this series will be about visits to the actual hospitals, with my notes, thoughts, and photos.
Please scroll down (or click) to post a comment. Connect with me on LinkedIn.
Let’s work together to build a culture of continuous improvement and psychological safety. If you're a leader looking to create lasting change—not just projects—I help organizations:
- Engage people at all levels in sustainable improvement
- Shift from fear of mistakes to learning from them
- Apply Lean thinking in practical, people-centered ways
Interested in coaching or a keynote talk? Let’s start a conversation.
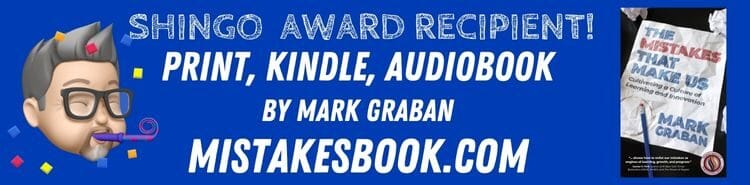