Continuing from Part 1 of my post about my first day of my first China trip, I'd like to share more about the Lean healthcare conference and presentations that took place.
In the next presentation from a Chinese hospital, the speaker started talking about the need to “improve [patient and employee] satisfaction through Lean management” and that “we have the same goals and purpose” as I expressed in my presentation… namely safety, quality, waiting times, cost, and employee morale (SQDCM).
I showed a “spaghetti diagram” in my talk, shown below, of a podiatrist running around an Illinois clinic searching for supplies (this was the walking required for ONE patient… 10 minutes of waste):
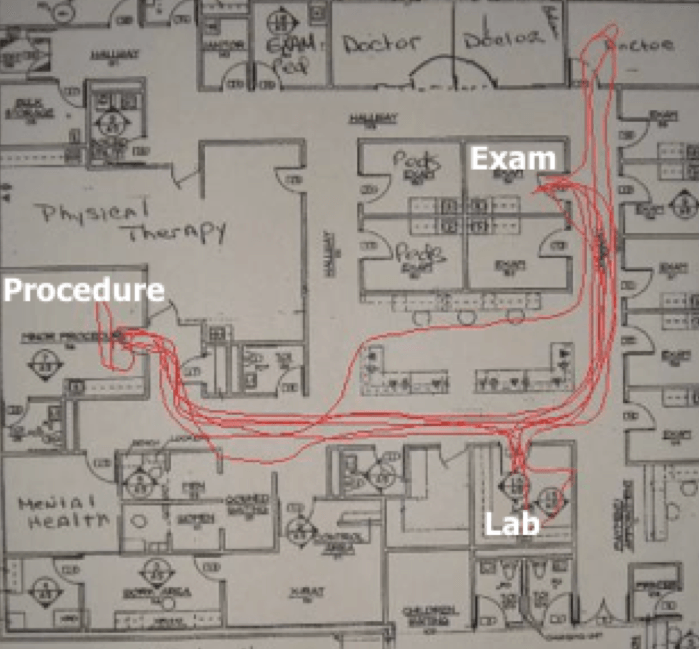
The Chinese presenter showed something similar, saying their walking pattern was “very messy” and it was made much better with Lean (I don't have a photo of their slide). The problem, of course, isn't the doctor or the nurses they shadowed.
The doctor in my diagram isn't disorganized or inefficient… it's a badly designed and poorly organized system. That's a universal problem (spaces, inventory, and supply locations not being well thought out) and the staff are left to suffer and do the best they can. 5S and Lean methods seem to be a pretty universal solution.
Hear Mark read this post (subscribe to the podcast):
The hospital also discussed the “very important” goal of reducing pharmacy errors and working toward “zero medication error.”
There are pressures to reduce prices for patients, with “reform proposals to reduce price gradually.” This creates a need to improve productivity the right way… by reducing waste instead of getting rid of people. There are cost pressures that prevent Chinese hospitals from “throwing people at the problem,” as Chinese factories might have done before labor costs started increasing… using cheap labor as a strategy instead of Lean manufacturing.
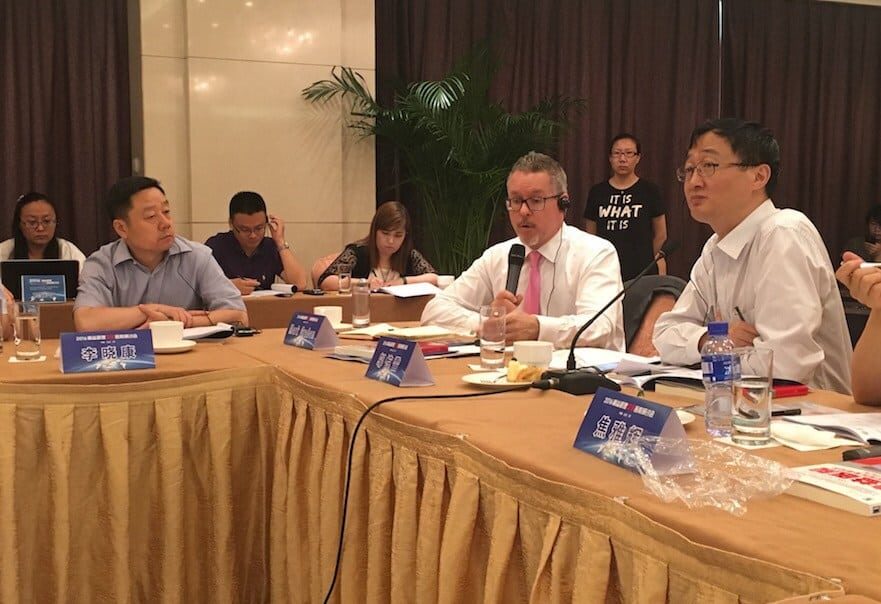
For hospitals, it's not just an issue of labor costs but an increasing shortage of doctors and nurses (a problem made worse by the “one-child policy“).
She said:
“How to establish a Lean Hospital in China is a very important challenge.”
To meet that challenge, she said they “need to include the patient experience… we've been trying to improve healthcare a long time, but now use the word ‘Lean'” (and I presume some new approaches and methods for improvement). They are also using Six Sigma (something that GE Healthcare introduced to China, as they've done around the world).
I saw an article on the way home, in the China Daily newspaper that talked about the need for price/cost controls and reduction… they are struggling through their own version of “healthcare reform” (sound familiar?). The hospitals I visited had signs for the “Price Control” department, part of the government's efforts to set and control prices.
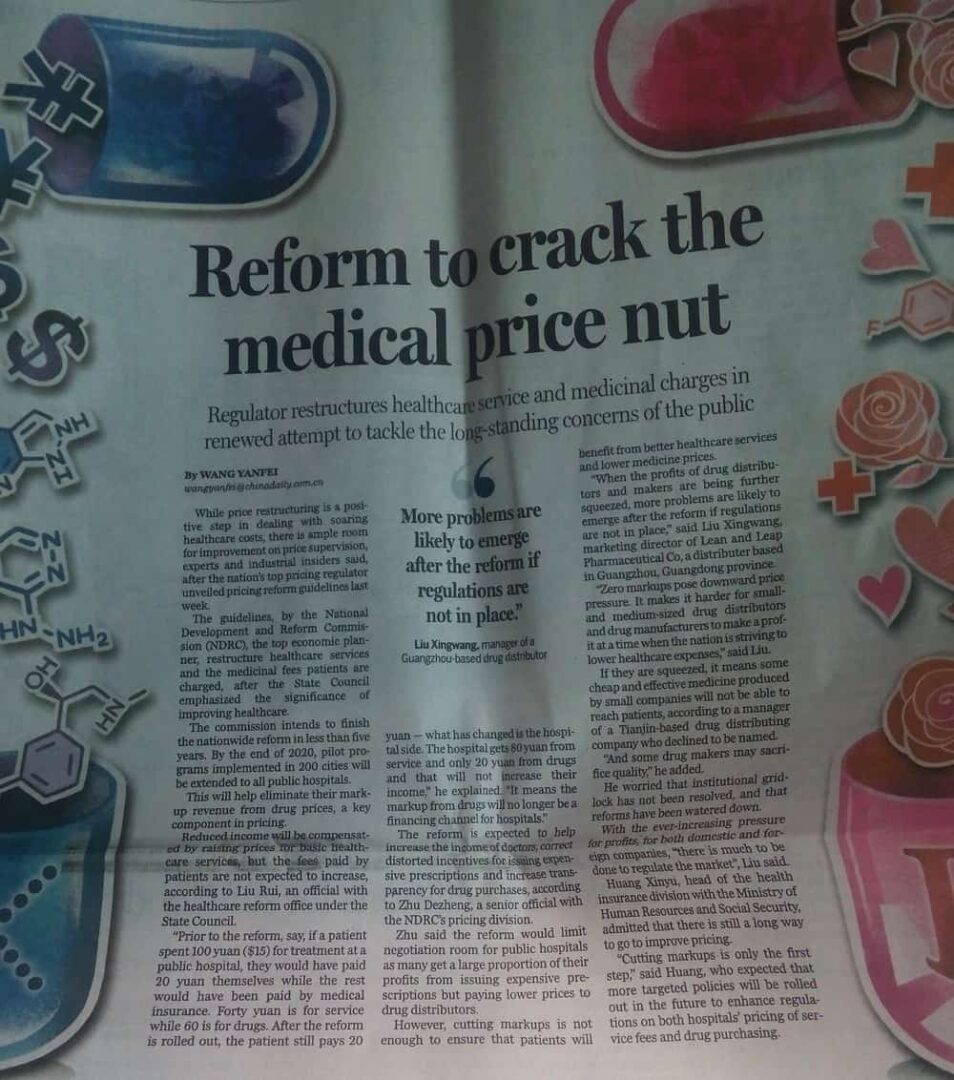
It said, in part:
“While price restructuring is a positive step in dealing with soaring healthcare costs, there is ample room for improvement on price supervision, experts and industrial insiders said, after the nation's top pricing regulator unveiled pricing reform guidelines last week.”
I think people realize the need to use Lean to reduce waste and take real cost out of the system… rather than arbitrarily setting lower prices.
One competitive factor in China is patient choice. I heard many stories about how Chinese patients from rural areas will take the train all night to get treatment at a big-name, big-city hospital. The government encourages people to utilize their rural hospitals for routine care… although this article said that published Chinese hospital rankings exacerbate this problem as people see the lists and want to get the “best care” by going to Beijing or Shanghai.
“Bao Yong, a public health professor from Shanghai Jiao Tong University, said the recent hospital rankings would help direct more people into those already crowded facilities, which ran counter to the goal of health reform. The authorities want the bulk of patients, especially those with chronic diseases, to attend class-B or class-C hospitals, with class-A ones left to deal with rare or difficult medical problems.”
The conference presenter said that an increasing number of Chinese go to the United States or Australia for care. One U.S. hospital she visited even had a “special department for working with Chinese patients.”
It's interesting that Americans often think of “medical tourism” as us traveling to low-cost countries in Asia (although there are HUGE opportunities for Americans to travel domestically for lower cost and better quality care). The Chinese who can afford to do so are probably traveling to other countries for quality and service, not costs, as the presenter said, “Chinese doctors and hospitals can match the standard of Western care… we should be confident.” She added, “We can learn from Western hospitals,” however.
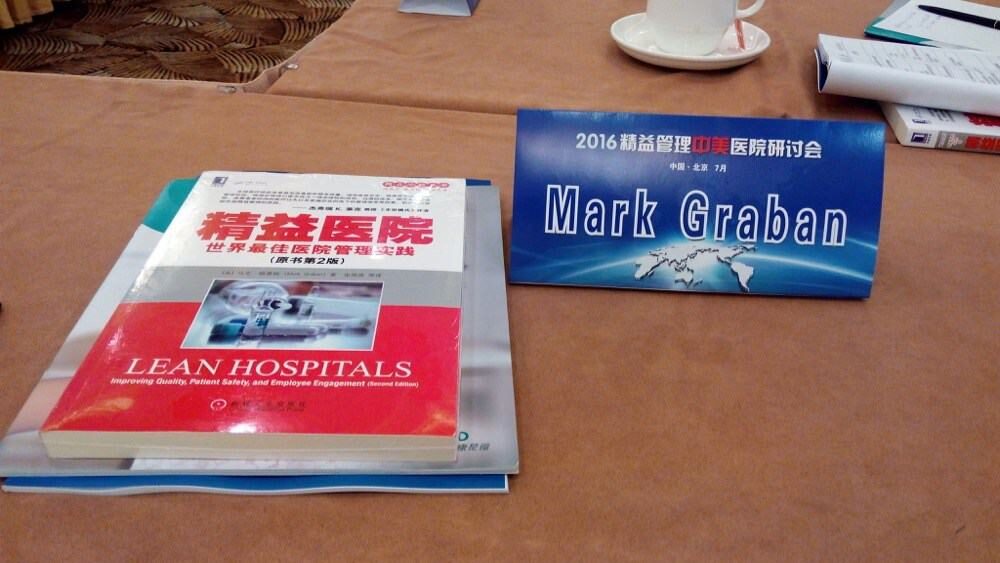
One need, the speaker said, is to “pay more attention to details,” and “that's where we're lagging behind the U.S., Hong Kong, and Taiwan.” I'd argue that American hospitals still need to pay more attention to detail… Lean and basic operations management methods often require us to get into the details of the work, and that seems boring or unexciting to too many healthcare leaders… but the “blocking and tackling” is critically important… not just having the latest technology, but putting the time into developing good processes, training people, engaging them, and supervising them over time.
She added:
“Some think healthcare is not the service industry, but it's about service. Medicine and service are connected. Focusing on the patient is a milestone reform for our industry. We need to treat the patient, not the disease… combining medical science and social science.”
Familiar themes and aims, right?
She said 1994 was the first time “the idea of focusing on patients was put forward.” More recently, they've realized that they also need to improve staff satisfaction. “Engagement of staff here is not as good as in the U.S.” (and I'd add that engagement levels here are far lower than they could be… hence the need for Lean and Healthcare Kaizen – a book that has not yet been translated into Chinese).
She generalized and said, “U.S. staff are more willing to make suggestions and to be proud of them.”
That might be true… I'm not sure if it's a matter of national culture or organizational culture. Yes, there are Lean- and Kaizen-focused hospitals in the U.S. where that statement is very true. There are, sadly, too many hospitals where staff have been trained to NOT speak up.
This journal article compares “patient safety culture” attitudes based on surveys in China and the U.S.
Excerpts from their results:
Table 2
Positive response rate of each item:
US | China | |
C2. Staff will freely speak up if they see something that may negatively affect patient care. | 75% | 51% |
C4. Staffs are afraid to ask questions when something does not seem right. | 47% | 80% |
C6. Staff feel free to question the decisions or actions of those with more authority. | 63% | 64% |
Now, speaking up about patient safety isn't exactly the same as the Kaizen culture of speaking up about ANY problem or opportunity. But, it seems patient safety is the most important and compelling reason to speak up, even if you're a bit fearful.
Those results seem to confirm the speaker's generalization (and it's interesting to look at the whole survey, something I might write a separate post about). China is a single-party, authoritarian country (although it's seemingly more capitalistic than communist), so does that teach people to not speak up?
Japan is not an authoritarian country. When I visited there in 2012 and 2014, they talked about the Japanese priority of “big harmony” and how people generally don't speak up there either… that the Toyota culture is decidedly different than the typical Japanese company. So, is it a factor of management, government, or Eastern societies? See previous posts here and here on that topic.
It's also interesting that the willingness to question authority is the same in both countries… what does that tell us?
But back to the speaker, and I'll wrap up, she also said MDs are likely to raise suggestions, but RNs are “more creative maybe,” and there are “more chances to improve their daily work.” Doctors are “too busy… they make complaints, but need to raise suggestions instead… which will lead to Lean being better adopted.”
I agree that it's an important function of leaders to build this culture of trust, speaking up, questioning things, and improving. How can it be called “Lean” without trying to engage everybody in Kaizen?
She added, “We need to understand what our staff want and we need to think from their perspective to improve satisfaction.”
She also said there's a Chinese saying that says, “Outsiders pay attention to different things than insiders.” I think that's true and an important aspect of Lean and workplace observation, as I write about in Chapter 4 of Lean Hospitals. We need to teach people to observe their peers (looking for process problems), but an outsider can be a “fresh set of eyes” to raise questions and see things the local experts can't see anymore.
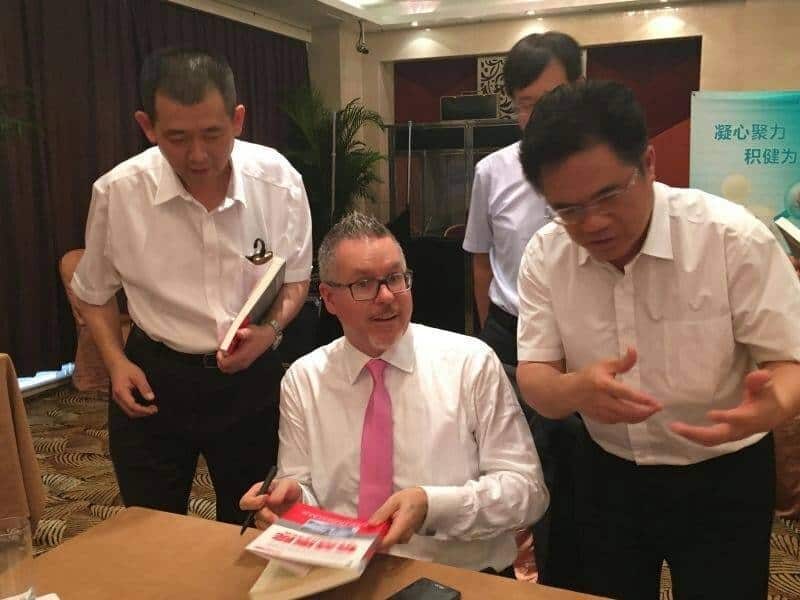
This has run long… there will be a Part 3 post to come about that first day. There's much to reflect on as I go through my notes. I hope this is interesting and thought-provoking to you, too.
Please scroll down (or click) to post a comment. Connect with me on LinkedIn.
Let’s work together to build a culture of continuous improvement and psychological safety. If you're a leader looking to create lasting change—not just projects—I help organizations:
- Engage people at all levels in sustainable improvement
- Shift from fear of mistakes to learning from them
- Apply Lean thinking in practical, people-centered ways
Interested in coaching or a keynote talk? Let’s start a conversation.
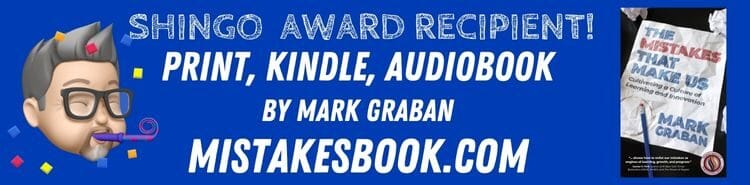