After arriving at the hotel in Beijing at about 8 pm the night before, I participated in a day-long Lean Healthcare conference that very next morning. I'm glad I always presented in the mornings because I was always fresh (I woke up before my alarm each morning) and was groggy every afternoon, thanks to jet lag.
The session was kicked off by Dr. Wu (I'm pictured with him, below), a hospital executive who was formerly part of the hospital management consulting group that organized my China tour.
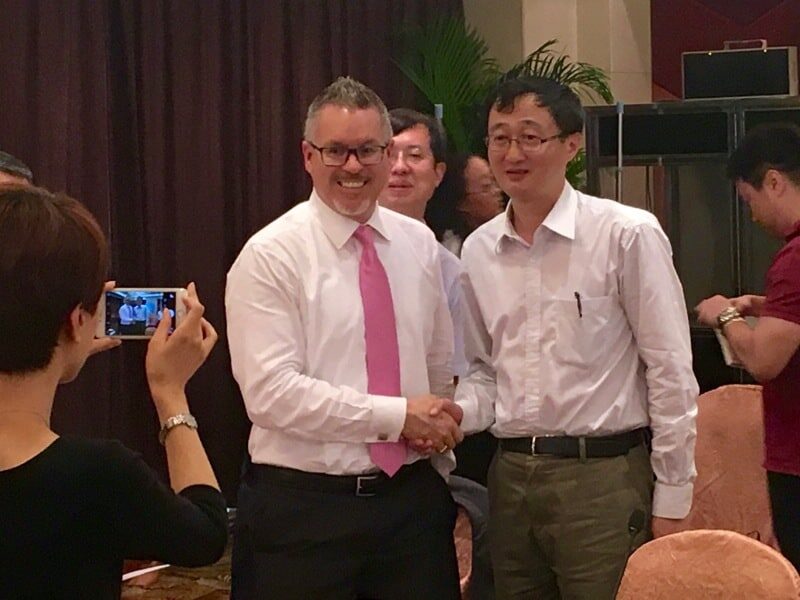
Dr. Wu started the morning by saying (as said by the simultaneous translator), “People are realizing the importance of hospital management as a focus.”
The first presenter talked about using Lean at Chongqing General Hospital (a city and hospital I'd visit on days 3 and 4 of the trip — see future posts). They have an enormous hospital by U.S. standards — 3200 beds in an academic medical center setting.
Their goals with Lean would be familiar to those doing it well in other countries (those not just focused on cost):
- Improve the happiness of employees
- Improve customer satisfaction and experience
They took a stand that reminds me of the book with a somewhat controversial title Patients Come Second (I interviewed one of the authors in Podcast #200):
“Only by satisfying personnel can patients be satisfied.”
They aim to “establish teams” and “unite personnel.” They are working to “cultivate awareness of quality and safety.” The hospital says they have surveyed nurses and have received 200 suggestions from them (I'm not sure how many were implemented). The hospital is working to improve “working conditions and learning” opportunities for staff.
The hospital says the patients' goals and needs are understood to be:
- Keep me safe
- Heal me
- Be kind to me
That lines up with my own personal preferences. Achieving all three of those at the same time is possible. But if I had to choose, I'll take patient safety over better customer service (and patient satisfaction) any day.
Hear Mark read this post (subscribe to the podcast series):
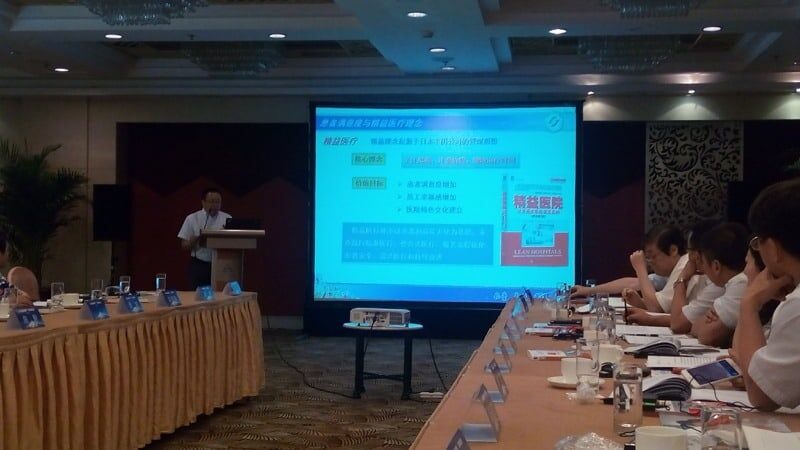
They talked about the use of PDCA as an improvement methodology.
They also talked about “zero tolerance for violence against MDs and RNs” (and I'd presume violence against anybody). See this Washington Post article about patients stabbing medical professionals out of frustration due to different causes. There's no justification for violence, but I'd encourage hospitals to work on eliminating the causes of frustration, such as long waiting times and high costs (people in China don't have universal health coverage or free healthcare).
The presenter said, “personnel are suffering from a lot of pressure,” and they are receiving “training to help address” that (which I hope means training on Lean methods to improve processes and reduce waste instead of just asking people to be “more resilient,” as we see in some cases here in the U.S. (and as some adamantly oppose). Again, we have to address the root causes of these problems.
Value stream analysis has been part of the hospital's approach, as shown here… it's either a very long end-to-end value stream map, or it's perhaps a bit too detailed, given there are about 24 main steps in the map (VSMs are often more high level with fewer steps or “chunks,” as some of the LEI faculty members call them in training). But either way, it's good to see them learning and using this approach instead of just focusing on traditional silos.
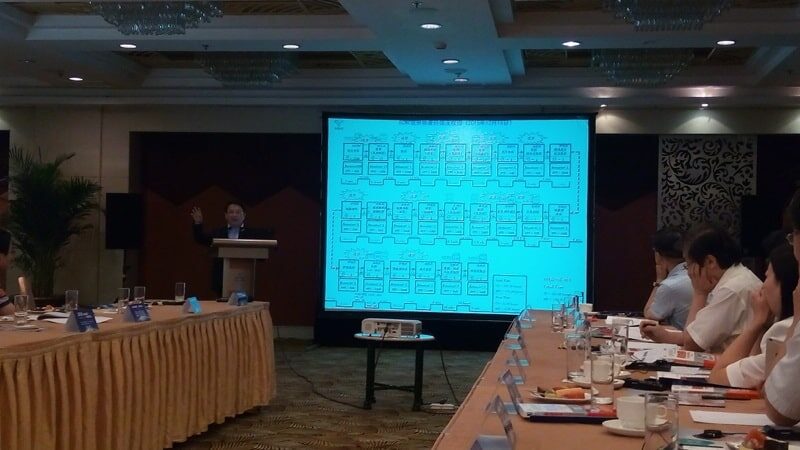
The hospital's aim is to “establish a unique culture, focused on patient safety and engaging all in continuous improvement.” They want to “integrate C.I. into the culture” and move toward the “better analysis of problems.” They are asking patients for suggestions and advice about how to improve.
The hospital is using third-party satisfaction surveys to get input from patients after discharge and measuring their employee satisfaction and patient satisfaction.
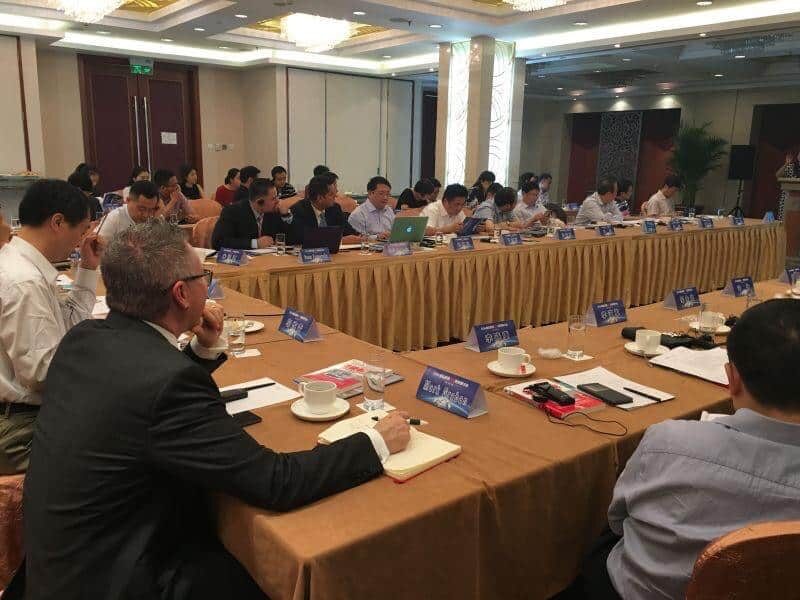
The next presenter was, I believe, from the government and their National Health and Family Planning Commission.
She said that Lean and TPS ideas were relatively new to her, but “we unconsciously practice many of these ideas.” It's funny that I hear that same idea in the U.S. when people in healthcare hear about Lean… it sounds really simple, and they say, “Yeah, we already do a lot of that… we just don't call it Lean.” That's often not actually the case.
The presenter said she has visited a Toyota plant… mentioning 5S and saying “we can learn a lot from TPS” in healthcare.
When I presented earlier in the morning, giving an overview of Lean principles, I used this “iceberg” slide that illustrates how Lean tools are visible when you visit a Toyota or a ThedaCare. But, those tools are less important than the underlying ways of thinking and philosophies of those organizations… the part of the iceberg that you can't see (but is bigger):
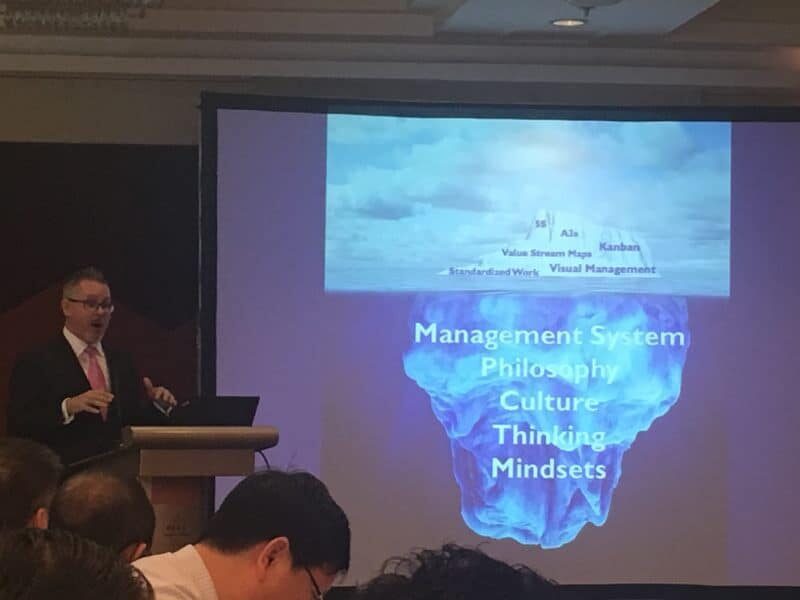
She said “the iceberg slide was great… what's under the water is important as we strive to improve satisfaction.”
I also used a slide that adds photos to six words used by an NHS hospital in England to describe their goals and ideals for Lean:
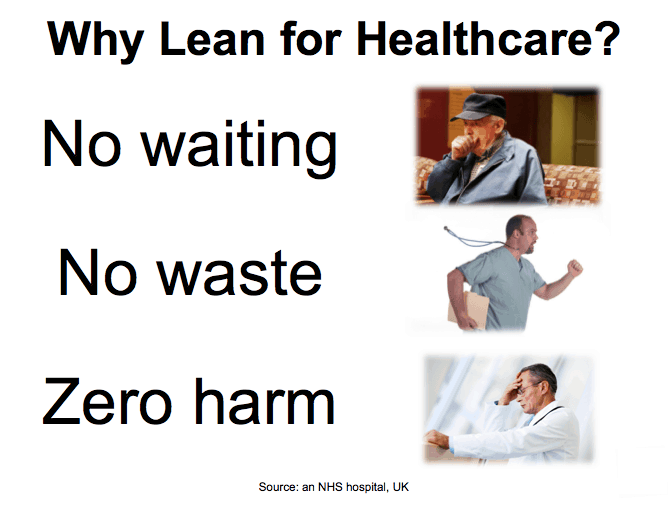
I've sometimes used a photo of a toe tag on a patient as an illustration for “zero harm,” but I've been told that's inflammatory (I think the idea of patient harm due to preventable medical error is far more offensive than a photo, but I digress).
The photos illustrate what we're trying to reduce: patients waiting, staff running around stressed out by waste, and doctors who are shamed or frustrated by patient harm.
A cardiologist in the room asked a great question about the slide:
“How can we have zero waiting? We see 20 patients per morning and are very busy.”
I responded that these three goals are an ideal state or a long-term goal that we should keep working toward. We're unlikely to have “zero harm” or “no waste” right away through Lean, either. But, instead of tolerating waiting as “the way it has to be” or tolerating hospital-acquired infections because “our patients are sicker,” we need to work tirelessly to improve systems and processes. Hospitals and clinics probably won't have “zero waiting” any more than Toyota, or a Lean factory has “zero inventory,” as I've written about before.
I'll write more about Day 1 in Beijing in future blog posts… and will have more posts about hospital visits and other days of the trip.
Please scroll down (or click) to post a comment. Connect with me on LinkedIn.
Let’s work together to build a culture of continuous improvement and psychological safety. If you're a leader looking to create lasting change—not just projects—I help organizations:
- Engage people at all levels in sustainable improvement
- Shift from fear of mistakes to learning from them
- Apply Lean thinking in practical, people-centered ways
Interested in coaching or a keynote talk? Let’s start a conversation.
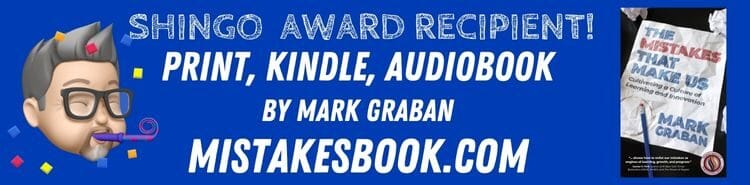
Fascinating insights! Truly inspiring to see you bringing the philosophy of lean to a health system that can truly benefit! I have been part of a non profit that is also trying to introduce modern healthcare management practices to Chinese physicians and emerging healthcare leaders via executive training programs and observerships, including a cohort of 30 presidents in NYC this August. How did you help translate these Lean concepts to the audience? Simultaneous translation?
Kevin – thanks for your comments. It’s good to learn about your efforts.
We had simultaneous translation at the Beijing event. For the other sessions, we had “consecutive translation” where I’d speak a few sentences, then stop and they’d translate. That took twice as long to say everything in either direction, of course.
So you have Chinese MDs and leaders coming to NYC?
Mark
Thanks for the reply! Yes, we have them coming as part of a joint program with the Chinese National Health and Family Planning Commission, the USTDA, and the American Chamber of Commerce in China. It’s a 2 week trip including 1 week of executive training at Columbia University’s Mailman School of Public Health.
Would be great to discuss as we are always interested in developing more course content and develop a robust faculty that can deliver engaging course content on ways to improve quality, access, and cost in healthcare.
[…] Continuing from Part 1 of my post about my first day of my first China trip, I’d like to share more about the Lean healthcare conference and presentations that took place. […]