There's a weeklong nursing strike at Allina Health in Minnesota: Seven-day nurses strike starts at five Twin Cities hospitals. The main issue is health insurance coverage for the nurses, it seems.
One reason for higher health insurance costs is rising healthcare delivery costs… one reason hospital costs are higher than they'd otherwise need to be is due to a lack of Lean thinking, teamwork, and leadership in many organizations. The lack of real cost reduction (through the elimination of waste and the improvement and redesign of processes) leads organizations to “squeeze” people through benefits, pay, and jobs. It's a negative spiral that leads to, among other things, poor labor relations (it could be called “poor management relations).
Disclosure: I previously did some consulting work for Allina Health, coaching some of their employees, leaders, and staff in some “Kaizen Kickoff” workshops at various sites, where we introduced a working continuous improvement system into departments, including nursing units. Everybody was wonderful and there were no objections from nurses or the union.
While some other unions are positive about Lean, the Minnesota Nurse's Association has made it clear that they don't like Lean (as I blogged about here). See their video from 2010:
The MNA seems to dislike executives (and their paychecks) more than they dislike Lean… but they've staked out a position that Lean is bad and they're going to stick by that, it seems.
The union does bring up a good point in the video… far too often, people err by timing the value-adding work instead of focusing first on eliminating all of the waste, delays, and non-value-added time that surrounds the work. Timing people is fine if you have THEM participating (see my post) and if the goal is to figure out how to make work easier and results better… the goal isn't to pressure people to work faster.
But, they disingenuously mock up a patient on an assembly line as the voice over from the Lean video says specifically that Lean is not about turning patient care into an assembly line. Sigh. The Lean model IS about better patient safety… not just cost. Again, if an organization is only focused on cost or the bottom line, that's not really Lean.
Here's an article from “Labor Notes” (a union publication that I've sparred with before): “Allina Nurses Go All In“
The article talks about something I've long decried… nurses and other healthcare professionals NOT getting proper breaks and lunch times. This leads to fatigue and errors and dissatisfaction… hospitals need to figure out a way to provide staffing and coverage so people can actually sit and eat.
“There is a problem with nurses not getting their breaks,” Olson said. “We now have a break room in almost every unit, because people don't feel comfortable leaving.”
This is a common problem in hospitals… which is why my “vision for a Lean hospital” from Chapter 13 of my book Lean Hospitals includes this basic (and legal) right to have a proper break:
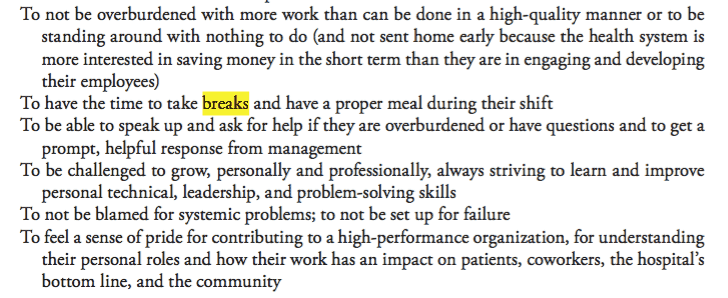
There are also other issues in the strike related to how to set staffing levels. Setting staffing levels in a hospital is more complex than knowing how many production workers need to be assigned to a line. A car factory is a repetitive and highly engineered environment in a way healthcare is not (yet Lean still applies, of course).
Allina wants nurse staffing determined by computer, based on patients' electronic records. The union objects to removing charge nurses' judgment from the staffing equation. Charge nurses consider factors not documented in a chart–family and psychosocial issues, the intensity of nursing required, the experience and skill of particular nurses.
Besides, Swehla points out, the computer data may be out of date. “Nurses do first and chart later, because it's more important to take care of the patient,” she said. “The input into the computer about a patient's conditions may happen two hours after you've delivered the care. They're deciding staffing in real time with this program–but we're not charting in real time, because we don't have the time.”
I could certainly see room for judgment in a standardized scheduling and nurse assignment process… and that could still be “Lean.”
Actually being able to chart in real time would be better, too, and something I'd hope to see happening more in a hospital that practices Lean.
But back to the “All In” article, it says:
“The approach will sound familiar to anyone who watched the “lean production” craze sweep auto manufacturing. Quality and savings are achieved by standardizing work into rote steps. Skill and individual judgment, which introduce unacceptable variation, must be ironed out.”
There's another dubious definition of Lean. It sounds more like “Lean As Misguidedly Explained,” or L.A.M.E.
Yes, standardized work is an important aspect of Lean. But, remember… Toyota has long said that standardized work should be created by (and improved by) those who do the work. I've never hear anybody in healthcare call for the elimination of “skill and individual judgment.” Yes, “unnecessary variation” can be bad, but not all variation is unnecessary or harmful.
“Only those motions that produce quantifiable results–services the hospital can bill for, health outcomes it can tally up–count as productive. That leaves out, say, brushing a patient's hair, comforting a family member, or mentoring a younger nurse.”
I've never heard anybody in healthcare say that any of those activities in the last sentence should be eliminated. For quite the opposite view, remember the “Loving Care” approach of a Dutch hospital that focuses on freeing up nurse time so they can be more caring and loving… the MNA sounds like they would support that approach… an approach that sounds more like “Real Lean” than some of the “Fake Lean” cost-cutting efforts that hospitals try to pass off as Lean.
“Any downtime is waste. In auto plants, lean managers pushed to keep workers busy 57 seconds out of every minute. (Of course, this dramatically increased injuries like carpal tunnel.) Nurse productivity, according to Health Catalyst, can be measured in nursing hours per patient day. That ratio improves when you burden nurses with so many patients that they start skipping breaks to keep up with care.”
In the typical hospital, nurses are already busy for something like 80 minutes out of every hour. Nurses and hospital employees are already getting hurt too often. If you see a Toyota plant, it's not “management by stress,” as the unions like to call it. Doing a well-engineered 57 seconds worth of work on an assembly line that's paced properly and ergonomically correct can less stressful than scrambling to do work that might take 45 seconds one time and 75 seconds another time (especially when workers in a non-Lean environment get yelled at for falling behind).
Lean isn't about overburdening nurses, eliminating skill, or being cold to patients. Lean is the best solution I've ever seen for the problems the MNA complains about. It's a shame that hospital leaders can't get the union on board with working together to solve these important problems that matter for nurses and patients. Why hasn't Lean been more a part of the solution instead of being a point of argument?
Please scroll down (or click) to post a comment. Connect with me on LinkedIn.
Let’s work together to build a culture of continuous improvement and psychological safety. If you're a leader looking to create lasting change—not just projects—I help organizations:
- Engage people at all levels in sustainable improvement
- Shift from fear of mistakes to learning from them
- Apply Lean thinking in practical, people-centered ways
Interested in coaching or a keynote talk? Let’s start a conversation.
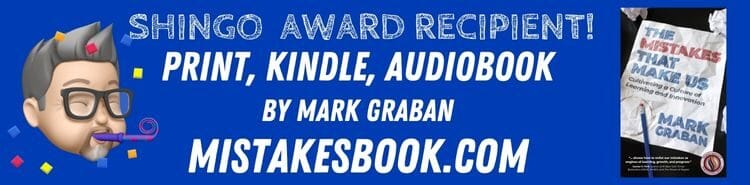
RE: “It’s a shame that hospital leaders can’t get the union on board with working together to solve these important problems that matter for nurses and patients. Why hasn’t Lean been more a part of the solution instead of being a point of argument?”
In my experience, if leaders cannot explain Lean management and its associated benefits (and pitfalls to avoid), then they cannot gain the buy-in of unions or anyone else. The vast majority of leaders do not know Lean well enough to explain it and also seem to think they already know it.
Unfortunately, Lean management quickly becomes a part of the political rhetoric in the tussle between labor and management, thereby becoming a point of argument. The facts don’t matter in such circumstances.
That’s why I generally put the burden on management in these standoffs… leadership needs to lead. They need to learn and listen. You’re right that those things don’t happen enough.
The union might be just as ignorant about Lean as management, if the union is learning about Lean from “Labor Notes” and academic papers with a political slant against management, against business, and against Lean. Or they’re purposefully mis-portraying Lean because their audience and membership doesn’t know any better (shame on leadership for not educating them).
Does the Veterinarian I talked to yesterday in my podcast love the idea of Lean because it would make a practice more money? He’s more interested in making his own work easier and better for the patients and clients they serve… Chip Ponsford has read Ohno and Shingo and learned what Lean really is… he’s inspired by Lean and I’ve seen nurses be very inspired by Lean when they learn what it really is and they’re given a chance to participate in the Lean journey. Podcast link below:
It obviously does not help that most/all union leaders prefer to stay ignorant about Lean and its potential to be part of the solution. I’ve often said that labor unions should be the most strident supporters of Lean and demand the practice of REAL Lean from management.
“Most/all” might be a bit of an overstatement just as somebody on LinkedIn tried to claim that no hospitals truly care about patients, that they only care about money.
There’s good and bad… good union leaders and bad… those who learn and those who want to stay ignorant… same is true with hospital executives, but I’ve always gotten more frustrated at the business leaders (in for-profit manufacturing or non-profit healthcare) who are supposed to be leading their organizations as if they care about results… and we all know Lean is the best way to get results over time.
But, if there’s no trust between labor and management, it’s hard to get down that path.
Look at the book “Comeback” from 1994 that I was tweeting about last week. The union had a great distrust of GM leadership, but learned to see that the Toyota way was different.