For decades, manufacturers have been tripped up by the simplistic idea that Lean is about “zero inventories.” It probably didn't help that one of the earliest and most prominent books about what many used to call “Japanese manufacturing practices” had that exact title: Zero Inventories. It was published in 1983, well before “Lean” was a term used for this.
Not even Toyota has zero inventories. They don't have zero raw materials. They have non-zero buffer inventories in between parts of their assembly lines. And it's not hard to see INVENTORY of unsold cars at Toyota dealers (realizing those are independent businesses and the inventory's not on Toyota's book, but still…)
Being able to have low inventory levels — low raw materials, low work-in-progress (WIP) and/or low finished goods inventory is an end result. It's a function of a number of things, such as:
- Stable demand and/or leveled production
- Suppliers that are located near by
- High equipment or machine uptime
- Short changeover times and the ability to produce small batches
- Low variability
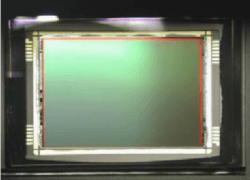
When I was a grad school intern at Kodak in 1998, I worked for six months in their Microelectronics Technology Division. They made semiconductor-based image sensors for scanners, early digital cameras, the Mars Rover, etc. The “cycle time” through the semiconductor fab was measured in months, meaning it took that long to go from a raw wafer to finished chips (see an example in the photo, at left).
A previous general manager had erred in thinking they could (or should) be “Lean” by intentionally draining down their finished goods inventory levels (of finished sensors). This turned out to be a really bad mistake. They couldn't meet customer demand, given they had long cycle times, highly variable cycle times, and highly variable quality yields (hence my master's thesis).
It was a huge mistake because the lack of image sensors became a bottleneck in the production and sale of Kodak Professional Digital Cameras that were being bought by photojournalists for $15,000 a piece… except Kodak couldn't make enough of them. Oops. That's not Lean at all to not meet customer demand.
Later, when I was consulting for a software startup called Factory Logic, I had a chance to go visit a manufacturer of enormous cranes. This was in 2003 or so. The company, who would have been quick to say, “we don't build cars!”, had made a similar error in getting inventory levels down too low.
I was traveling with a Japanese consultant who was helping the startup and he shook his head at the situation.
He said very clearly, and it's a lesson I'll never forget:
“Job one… meet customer demand. Job two… low inventory.”
Too many companies made low inventory the primary goal. The goal is more like the lowest inventory level required to meet customer demand today. Over time, you can make improvements that ALLOW you to reduce inventory levels. You don't put the cart before the horse and just lower inventory below required levels.
You might “lower the water” a little bit to “expose rocks” as the Toyota / Lean cliche goes, but you don't drain the swimming pool completely before jumping in.
Hear Mark read this post (subscribe to the podcast)
Let's Avoid This Mistake in Healthcare
It's possible that a hospital or health system could make a dangerous error by thinking it's “Lean” to cut inventory levels of supplies or medications too much. In manufacturing, you might accept that the line occasionally goes down because you ran out of parts. That's a cost of doing business that's lower than making sure you have so much inventory so that production NEVER stops.
In healthcare, we need to err on the side of slightly too much inventory since lives might be at stake. Some medications might expire (but not if we properly rotate our supply over time).
Lean isn't about being cheap or having low inventory, it's about meeting patient needs. Share on XThe parallel to inventory in healthcare is not just the physical supplies… we can draw a parallel to waiting rooms.
Waiting rooms are like warehouse space, basically. Why do clinics and emergency departments have waiting rooms? It's because of poor flow or it's due to an imbalance between capacity and demand. Today's process (and level of variation) requires a certain amount of waiting room space.
Over time, you can take actions that improve flow and better match capacity to demand… which means you could reduce the size of the waiting room. Look at Sami Bahri DDS, the “world's first Lean dentist.” He doesn't have patients use his waiting room, but he improved his processes in a very systematic way. He didn't just open a new office without a waiting room, trusting he could quickly figure it out. He didn't put the cart before the horse. By the way, the 2nd edition of his book Follow the Learner is now available from LEI.
So, I wasn't happy to see this tweet recently, referring to a scale model of a new hospital that will be built (I'm using a picture of the tweet to avoid calling the person out by name)… she wrote this directed at me:
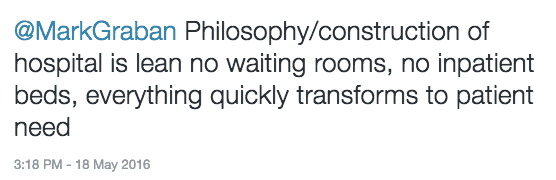
Lean doesn't mean “no waiting rooms” as an absolute.
I'm not sure what she meant by “no inpatient beds.” Maybe it means beds/ rooms that are flexible for different needs (such as ICU vs regular rooms?)… that doesn't sound bad on the surface.
But let's talk about “no waiting rooms.” That's likely to be a big disaster unless they have the processes and capabilities in place:
- Leveled patient demand
- Matching staffing and capacity to demand at different times
- Predictable process times
- Slightly excess capacity for exam rooms
Be careful about absolutes. Lean means no waiting rooms? Only if that's possible given a Lean process.
Saying “Lean means no waiting rooms” might be an example of L.A.M.E. or Lean As Mistakenly Explained.
Even in the most Lean of processes, we might still need waiting space. I was talking recently with an allergist who said, “We need a large waiting room.”
I asked, “Why?”
The allergist pointed out need for some patients to wait 30 minutes to check for bad allergic reaction. Maybe that's a required inspection step… either way, having “no waiting space” would mean that patient clogs up an exam room and hampers patient flow. Having some waiting space makes sense.
And isn't that what it's all about? Making sense, making incremental changes, testing things out, and seeing what works instead of following Lean dogma?
Please scroll down (or click) to post a comment. Connect with me on LinkedIn.
Let’s work together to build a culture of continuous improvement and psychological safety. If you're a leader looking to create lasting change—not just projects—I help organizations:
- Engage people at all levels in sustainable improvement
- Shift from fear of mistakes to learning from them
- Apply Lean thinking in practical, people-centered ways
Interested in coaching or a keynote talk? Let’s start a conversation.
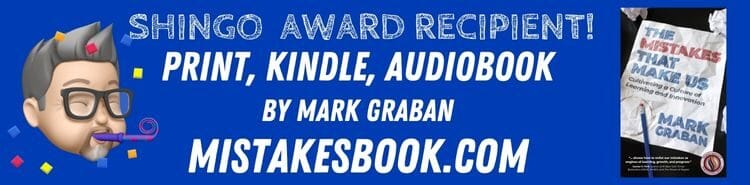
So true Mark! Thanks for posting — I get so tired of hearing people wanting to create spaces with no waiting rooms at all. Have a great week!
Hi Mark – timely topic as I’m currently helping a client with a HIMSS submission on “Eliminating the Waiting Room.” She’s giving a similar presentation at MGMA this fall. Another client is submitting on the topic of direct-rooming in the ED.
We have multiple clients (EDs and multi-specialty clinics) who use our system and directly bring patients to the exam room (or have them self-room).
Perhaps the better way to frame this concept: “Eliminate the Waiting Room *As You Know It*” or “Eliminate the Wait” … In most cases there is still a waiting room (one client calls it a “Pause Area”) but very few patients use it, and in clinics, it’s much smaller than most.
In the case of an ED, you’re right – with the fluctuating patient demand, you simply cannot eliminate the waiting room. But, you can improve processes to the point where patients are more often than not directly roomed.
As our clients are showing, it is possible! And more and more clinics and EDs are doing it – with the right attention to workflow processes and technology that helps keep the whole ED/Clinic on the same page.
Thanks for your comment, Jeanne. That’s exactly my point… healthcare organizations need to improve so patients don’t need to use a waiting room as much… not just get rid of the waiting room. A smaller waiting room might be the end result, not “no waiting room.”
The waiting room isnt just used by patients. Where would family members wait if there is no waiting room?