Today's post is an addendum from Saturday's post on the apparent death of a health system Lean program: “Why Would a New Healthcare CEO Kill a Lean Program?“
If you read that post, there's an interesting comment from a Presence Health employee that doesn't shed too much more light on this:
“From the standpoint of a current Presence Health Employee~ my opinion is that the RIEs failed because they were aggressively site specific. At a time when Presence Health is “Becoming One” I do not believe the RIEs took the entire ministry into consideration when planning events. Decisions and “experiments” where being made and conducted through a site specific lens, and this was often in contradiction to the spirit of the new organization.”
As I commented in response, I'm not sure why a goal of common processes or a health system that's actually a system would be a reason to stop with Lean. Unless, hopefully, they are really just re-booting the effort instead of killing it altogether.
As I alluded to in the post on Saturday, there was a sad story about a hospital that I featured in the 2008 1st edition of Lean Hospitals that basically killed their promising program when a new CEO was hired from the outside. As Adam Zak, one of the top Lean-focused executive recruiters, said, it's a shame that the board (apparently) didn't hire a CEO with Lean experience.
Looking back at my notes from 2011, one hospital leader at this other hospital said, basically:
- Even though there was progress in the lab and with ER design, “management was not leading with Lean principles.”
- “We never did anything with it,” she said (I think meaning that they didn't build upon the initial early results that were somewhat isolated instead of being a hospital-wide initiative)
Another middle-level leader who was deeply involved with Lean said:
- Lessons learned? There's a risk that comes with leadership changes.
- She asked, “Is it worth even trying at a departmental level if senior leadership isn't on board?”
- The CEO needs to want it as a culture for the organization, not just for improving departments.
- “Lean has become a dirty word” around here, she lamented.
She also said, in a different conversation:
- We abandoned things… (meaning Lean principles)
- Every single department director has changed, and the CEO has changed. Some aspects of LEan they are doing maybe, but not keeping up with data, except for the lab.
- Not using the “Lean tracks” in the E.D. anymore (this was a “split flow” design)
- Kanban system in the O.R. was falling apart.
- “It's really all about leadership. It's not about the workflow, things will go down the drain without leadership support.”
That's all really sad. It goes to show that early progress doesn't always turn into an organization-wide culture change and Lean transformation.
Hear Mark read this post — subscribe to Lean Blog Audio
I had titled the section about the hospital as:
“The Beginnings of a Lean Enterprise”
I guess there was a question mark. It sure seemed like it had been heading in that direction.
The corporate VP for Lean had talked about their “no layoffs due to Lean” commitment:

That was a good sign.
They had improved the E.D. significantly:
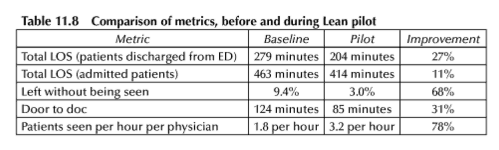
And they anticipated that the use of “Lean Design” methods (and they were early adopters of this) had made a huge difference:
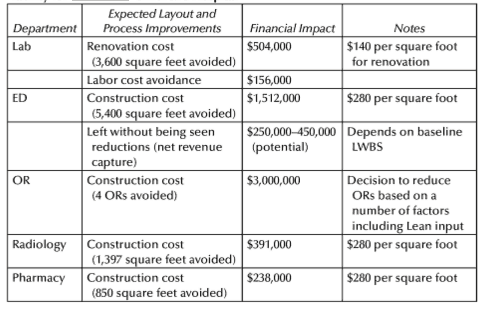
They didn't just “design” it Lean – they built it using these designs that engaged staff in understanding how to build smaller spaces (thereby reducing costs) that worked better for everybody involved.
In reading what was in the book, it becomes clear that the hospital was using projects as a way to improve. Many of these were 12- to 16-week projects that really transformed a department, not the typical week-long Rapid Improvement Events. The consulting group I used to work for, ValuMetrix Services as part of J&J, helped lead these projects and helped teach Lean methods and Lean management (that was one goal of these long projects… to not just do stuff, but learn how to manage differently).
That said, the method didn't spread quickly enough or high enough. After about three or four years, the whole Lean approach was disowned when the new executive leadership came in. The corporate VP of performance excellence got it… but it seems that the executives and the board weren't impacted, educated, or involved enough as they had been at systems like ThedaCare and Virginia Mason Medical Center.
I wonder how many stories are out there like that today… a promising Lean program that won't survive beyond the first few years… and what the right countermeasures are?
Please scroll down (or click) to post a comment. Connect with me on LinkedIn.
Let’s work together to build a culture of continuous improvement and psychological safety. If you're a leader looking to create lasting change—not just projects—I help organizations:
- Engage people at all levels in sustainable improvement
- Shift from fear of mistakes to learning from them
- Apply Lean thinking in practical, people-centered ways
Interested in coaching or a keynote talk? Let’s start a conversation.
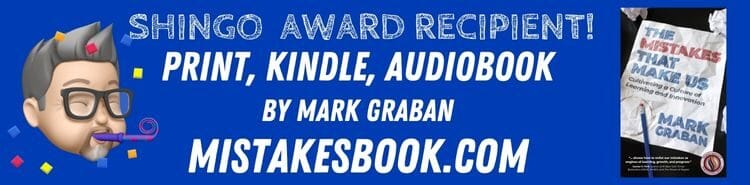
“Lean Design” methods that result in “cost avoidance” (and square feet avoided) don’t count because costs remain the same and saved space seems not to have been converted into new revenue. Leaders need to see improved productivity, actual cost reduction, profitable growth, etc., to recognize Lean as something worth doing and sticking with for the long-term.
Development of people, ideas, creativity, enthusiasm for Lean – which helps keeps Lean going- is generally not recognized by leaders unless they have participated in kaizen.
As you know, Virginia Mason’s top leaders initially learned Lean via kaizen (with Shingijutsu USA) on the manufacturing shop floor and transferred those learnings to healthcare processes. And they still participate in shop floor kaizen (did so last week in Connecticut).
If they spent less on construction, how do “costs remain the same?”
Cost structure is unchanged as a result of cost avoidance. If costs today are 1.0, and construction is not undertaken, costs remain 1.0.
I should have added that Shingijutsu USA sensei explain things in ways that few others can. If leaders are part of kaizen, they not only learn what is possible to achieve in kaizen, they also learn valuable things directly from senseis that I think can make the difference between committing to Lean or not.
Agreed – the most success I’ve seen out there is when leaders and executives participate in Kaizen and Lean rather than just endorsing it or sponsoring it.
i was at an American College if Healthcare Exectives Congress session a few years back and it was strongly suggested that Lean be incorporated in every MHA program and healthcare MBA program. Definitely not a short-term countermeasure but in line making standard work and tying into the concept of “it’s just how we do work around here.” I was working at the Joint Commision in the early 1990s when the first wave of hospitals starting using Lean. I even trained at the Deming Institute. Once someone learns Lean and sees it work, it’s hard to go back. While staff can’t carry a Lean program if there is no leadership support, they will find ways to keep using The concepts and tools because Lean makes sense and works.
Yeah, individuals will keep using the concepts, but the organization won’t come close to reaching its full potential. As Dr. Deming said, the last thing we need is everybody’s best efforts, if senior leaders aren’t doing their part to change the system.
I just read both articles. They are interesting but not at all surprising. I don’t think it is weird at all that a new CEO comes in and abolishes the lean program. I don’t even necessarily think that he is wrong.
My experience with Rapid Improvement Events is that they serve only one purpose and that purpose is the education of future/current leaders. Your best example of this (Thedacare) admitted that it realized that it had to abandon them in order to be successful. Good things happen in RIE’s but they just aren’t sustainable given the resources dedicated to them. In the long run, you have to go to continuous improvement. The problem is that one doesn’t necessarily lead to another and it is a complete crapshoot whether the future leaders will be people who embraced RIE’s or not. In general, the RIE’s have a pretty low overall success rate at making sustainable improvement. Leaders who embrace them are only slightly more likely to make bottom line improvements that actually show up in short term metrics. Leaders who do not embrace them likely spend their energy manipulating metrics in other ways that have proven to be successful in the past. Flip a coin on who gets promoted between those two camps. RIE’s do not predict lean success no matter how well they are run. You can find examples of lean adoption with events or without and you can find examples of lean failure in both camps as well.
I’m not a CEO but I am a general plant manager. When I took over in my current position, one of the most critical questions I asked my new boss was what kind of a lean program they had in place already. I was actually VERY excited to hear that there wasn’t one at all. If there was one in place and it had been an RIE focused program with Lean Experts and Facilitators in place, you could have been writing articles about me pretty quickly. I would have quickly rolled out a new program with any name other than “Lean” and the “Lean Experts” would have found themselves being assigned to very different tasks that would have tested their ability to quickly get things done. Keep in mind that this is coming from a “Lean Expert” and “Event Facilitator” who has facilitated 50+ events. I would keep the experts around if I could and I would talk to them about the change in tactics but more than likely they are going to go find new jobs. The market for people that can facilitate events is pretty darn lucrative and dealing with simple day to day problems starts to look a little beneath them at that point. You also would have heard quiet rumors that the CEO isn’t a “big fan” of lean when in reality, I’m not a big fan of that type of lean. Convincing people that we need to redefine “lean” is just a lot harder than starting over with a new term. In fact, I’m not sure that a term is at all useful. Walking in and showing the teams what you really care about based on where you spend your time is WAY more important. I can tell you right now that where I spend my time as a new leader will NEVER be on Improvement Events.
The problem with RIE’s is that they focus on one type of problem (problems that can be solved in a week…) regardless if those types of problems are the most critical. My experience is that lean programs focused on RIE’s end up with their priorities completely out of proportion to their needs. I need people who can create systems to effectively address the 1,001 problems that surface every day, not people who are working on the 101 problems that surface every year. If you work on the 1,001, you will be more than adequate at addressing the 101 when they come up. I’m not saying that this CEO has any clue what he is doing but everything reported could have been reported on me.
Kris – thanks for your comments and sharing your experiences.
I totally agree with you. I’ve seen organizations take a path other than the “start with RIEs and then move to management systems” path. I’ve seen organizations do really well starting with “daily continuous improvement” as Kaizen or starting with more transformational projects.
Either way, success or failure comes down to leadership effort and behaviors. Are they willing to let others shine through improvement? Are they willing to face reality instead of making excuses? Are they humble? Do they stop blaming others?
Easier said than done.
I truly hope your optimistic scenario (throwing out what might have been “Fake Lean” and replacing it with a better form) is what’s happening.
Mark