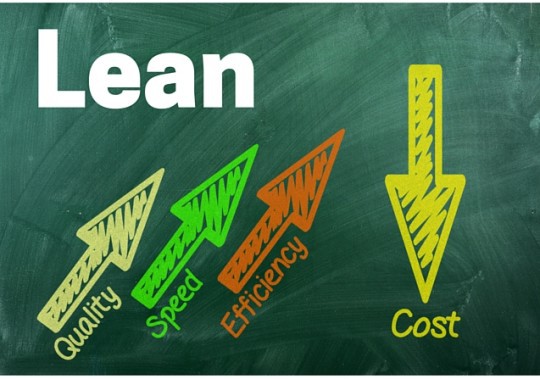
I had a bit of a new year's resolution about being positive and not fretting about organizations that don't “get it” when it comes to Lean. But, resolutions are meant to be broken, I guess.
It's very frustrating when I hear people in healthcare complain that their hospital or health system has equated Lean with cost savings — only focusing on cost reduction or primarily focusing on it. Hospitals that say to their staff that Lean is just about cutting costs (or demonstrate that) will fail to engage their most important asset — their employees.
I visited one hospital recently where standardized metrics boards in the hallways of different departments had a sheet of paper that summarized their Lean efforts… it simply listed the number of improvements (projects or other ideas) and the cost savings. It was millions of dollars. So, good for them. What was missing was anything equating Lean to safety, quality, patient satisfaction, patient flow, or other meaningful measures.
One can argue that it's an ineffective strategy to focus only on cost. By the way, that's been a very traditional healthcare management focus and hospitals can do cost cutting without even bringing the word “Lean” into the discussion. Health systems have been cutting costs by laying off staff for the longest time. Lean is a great alternative to that cost cutting approach.
I'd also argue that it's not Lean at all to focus only on cost cutting. A hospital's leadership can choose to focus on cost cutting… just please don't call it “Lean.”
A hospital's leadership can choose to focus on cost cutting... just please don't call it #Lean. Share on XLean comes from the Toyota Production System, whether we are practicing Lean in manufacturing, healthcare, or other industries. The core definitions of the Toyota Production System that come straight from Toyota emphasize that Lean is focused on improving flow and improving quality. Cost reduction is an end result, not a primary goal.
Hear Mark read this post (as part of this podcast series):
If an organization is only focused on cost… and they're calling that Lean, it's disrespectful to Toyota, for what that's worth. It's also disrespectful to their patients and to their staff, which is more important. Saying Lean is only about cost is a classic case of L.A.M.E. – Lean As Misguidedly Explained.
I wonder, “How do hospitals get the idea that Lean is primarily about cost cutting?”
I wonder, 'How do hospitals get the idea that Lean is primarily about cost cutting?' Share on XThere is a consultant out there who peddles Lean as a cost reduction strategy. There's probably many of them. There are traditional healthcare “cost cutting” consultants who have latched onto the Lean buzzword, but they're not really teaching Lean.
One hospital I visited recently is about two years into their “Lean journey.” That journey is off to a bumpy start because they've focused primarily on cost. They had a national consulting firm “helping” them with this. They're now trying to adjust their strategy (at least that's some high level PDSA at work).
It's also possible that healthcare leaders have an existing bias toward cost cutting. When they learn about Lean, they are maybe only learning about tools… so they think about how to apply those tools to cost reduction. They're probably doing so because they haven't learned that Lean is also a philosophy and a managerial approach.
I can't imagine anybody has gotten the impression from my blog or my book Lean Hospitals (2nd edition) that Lean is only about cost cutting.
In the second edition, the word “cost” appears on 89 pages.
The word “quality” appears on 115. “Safety” on 86.
It's intentional that the word cost is not in the subtitle: “Improving Quality, Patient Safety, and Employee Engagement.”
Even if people haven't bought and read my book, I make the first chapter available as a free PDF on my website. I wish we could get that PDF into the hands (or iPads) of every healthcare leader and manager in the world.
Relevant Excerpts from Lean Hospitals:
Dr. John Toussaint says, in the foreword:
“These [Lean] improvements all lead to better quality and lower cost–in other words, better value.”
In various parts of Chapter 1 (which you can read for yourself), it says:
“In today's world, the “need” for Lean in healthcare is very clear in terms of quality and patient safety, cost, waiting times, and staff morale.”
…
“Lean is very different from traditional “cost-cutting” approaches that have been tried in multiple industries, including healthcare.”
…
“Lean is a tool set, a management system, and a philosophy that can change the way hospitals are organized and managed. Lean is a methodology that allows hospitals to improve the quality of care for patients by reducing errors and waiting times. Lean is an approach that can support employees and physicians, eliminating roadblocks and allowing them to focus on providing care. Lean is a system for strengthening hospital organizations for the long term–reducing costs and risks while also facilitating growth and expansion.”
…
“In 1945, Toyota set out to improve quality, while improving productivity and reducing costs…”
…
“Rather than reducing spending by slashing payments or rationing care, Lean methods enable us to reduce the actual cost of providing care, allowing us to provide more service and care for our communities. A hospital that saves tens of millions of dollars by using Lean methods to avoid costly expansion projects is a hospital that costs society less, while providing the same levels of care, if not more.”
…
Good Quality Costs Less
Hospitals do have many opportunities, however, to improve the quality of healthcare delivery methods and processes in a way that also reduces costs. Across all U.S. hospitals, there is a large cost-savings opportunity from preventing errors and improving quality. For example, preventable adverse events from medication errors are estimated to cost hospitals $4 billion per year.
David Fillingham, CEO of Royal Bolton Hospital NHS Foundation Trust in the United Kingdom, has said, quite simply, “Good quality costs less.” This was proven to be true as a result of Bolton's Lean improvements; the hospital reduced trauma mortality by 36% and reduced a patient's average length of stay by 33%. ThedaCare documented similar results in cardiac surgery; mortality fell from 4% to nearly zero (11 lives saved per year), with a length-of-stay reduction from 6.3 to 4.9 days, and 22% lower cost. It might sound too good to be true, but many hospitals are proving that you can simultaneously improve quality, access, and cost.
Lean teaches us to see quality improvement as a means to cost reductions, a better approach than focusing directly and solely on costs. Bill Douglas, chief financial officer at Riverside Medical Center (Kankakee, IL), summed it up as the hospital began its first Lean project by saying, “Lean is a quality initiative. It isn't a cost-cutting initiative. But the end result is, if you improve quality your costs will go down. If you focus on patient quality and safety, you just can't go wrong. If you do the right thing with regard to quality, the costs will take care of themselves.”
In another sense, Lean is proving to be an effective methodology for improving patient safety, quality, and cost, while preventing delays and improving employee satisfaction. It can be done. Lean is working; it is effective. Lean helps saves money for hospitals, while creating opportunities for growth and increased revenue. Lean methods can benefit everyone involved in hospitals. Understanding Lean principles is just a starting point. The real challenge is finding the leadership necessary to implement these strategies and to transform the way your hospital provides care.
…
Lean Lessons
- Quality improvements are a means to cost reductions.
- Productivity improvements and cost savings can be accomplished in ways other than layoffs or head count reductions.
- Lean is focused on patient safety, quality of care, and improved service, not just efficiency, cost, and productivity.
Why is the “Lean is about cost cutting” mindset fairly widespread? What can we, as a Lean community, do about this?
If you have stories to share about your own experiences, please post a comment (which can be anonymous) or contact me (anonymity assured).
Please scroll down (or click) to post a comment. Connect with me on LinkedIn.
Let’s work together to build a culture of continuous improvement and psychological safety. If you're a leader looking to create lasting change—not just projects—I help organizations:
- Engage people at all levels in sustainable improvement
- Shift from fear of mistakes to learning from them
- Apply Lean thinking in practical, people-centered ways
Interested in coaching or a keynote talk? Let’s start a conversation.
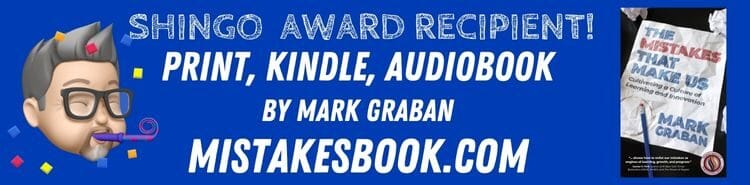
Thanks for this Mark! I share your frustration. Several “Lean consultants” use the new management buzz word that is Lean to sell just anything. As a (true) Lean community we need to continue, like you do, to denounce this malpractice.
Reducing Lean to cost cutting or chasing waste is what happens to Lean is not properly understood. Lean is a scientific approach with a clear object of study: FLOW. Flow is defined as the movement of energy (work) through a system. Everything in flow is about conserving energy, finding the most efficient and safe way to deliver value to clients, patients, citizens. PDSA (learning from experiment) is the scientific method used in Lean.
Thanks for the comment, France.
I’ve noticed a big difference between Lean consultants whose roots are in Lean and generalist consultants (such as those doing traditional healthcare consulting) who then also “get into Lean” as a “new offering” or something.
You’re right about flow… flow and quality both, actually.
The Toyota corporate web page on TPS emphasizes the pillars of just in time (flow) and jidoka (built in quality).
The word “cost” does not appear on the page once.
Cost cutting is what top leaders want to hear, so that’s what consultants tell them. Otherwise, they likely won’t get the job and the hospital won’t get its costs cut (or appearance thereof).
In the bigger picture, this is what the old Taylorists/Scientific Management community dealt with 100 years ago. They too were largely unsuccessful at getting top managers to embrace the overall (win-win) management system. Top managers were more interested in the mechanisms that yielded the results they wanted; i.e. tools for cost cutting (win-lose).
The Lean community ignores Scientific Management, largely due to mis-perceptions about Taylor and his work, and therefore did not learn from many things that could have helped us. His work, and that of his followers, continues to be ignored. We think “We’re different.” Sound familiar?
I totally agree with this article. As an individual that works within the healthcare industry and has studied lean, it is a total misconception that lean is just cutting costs. Cost are cut by ensuring consistency and totally eliminating gaps. I strongly believe that all hospitals should have someone who is certified and can ensure that the definition of lean is addressed appropriately.
Hi – Thanks for your comment.
Unfortunately, being “certified” doesn’t say much about somebody’s knowledge, experience, and competence with Lean.
Too many hospitals are putting somebody with ZERO Lean experience into a week of “belt” training and then putting them in charge of Lean. That’s a recipe for failure.
Paul Critchley: “True for all companies and industries.”
Peter Gardner: “No its not just health care problem, too many companies just look at it that way and take the low hanging fruit without changing the company’s internal focus to the customer and NVAs.
Anthony Head: “Because its often easier to control than growth.”
Cory Maukonen: “Sometimes we forget about the numerator in the value equation.”
Bob Rush: “Cost reduction is a side benefit of fixing the true problems, not the focus. If cost reduction is your focus just cut your headcount and beat your suppliers up on material costs, it would be easier but much less permanent than practicing lean.”
Bob Rush is, by the way, the author of the new Chapter 8 in the eBook “Practicing Lean.”
His chapter is OUTSTANDING and I’ll share an excerpt on the blog soon.
Mark
One of the tragedies of starting out with cost cutting as the primary objective is that these efforts often cut into value-adding functions as much as they reduce waste/interruptions/defects/etc., thereby creating even more problems.
This leads to some of the horror stories from healthcare and the anger of doctors and nurses who tell them. Trying to hustle caregivers through patient contact, for example, when this is actually a value-adding step. Identifying increased “patients/hour” as an objective (rather than improved patient care) is one shocking outcome.
Understanding (as a group!) the creation and flow of value to the customer and the things that interfere with it (waste) is the starting place. Then embracing Shigeo Shingo’s improvement priorities (easier, better, faster, cheaper) is a great way to proceed. We usually find that we do not need to go beyond “easier” to get the other three!
Totally agree on your first point. Cutting costs too often means cutting value and reducing services… not good.
Yes, rushing people through the value added work isn’t good either, and I understand the frustration. I think having a goal for seeing more patients/hour isn’t necessarily bad. It might be very necessary to reduce waiting times and improve the quality of care and outcomes.
That said, reducing WASTE is the key, not speeding up the value added work. There are situations where a physician is seeing MORE patients per hour and spending MORE time with each because of reducing interruptions, wasted motion, miscommunications, etc.
We need to focus on things in that order… easier, better, faster (which really means “less delay”)… those lead to cheaper.
I think the reason that hospitals and many others associate Lean with cost reduction is the word itself. Lean as an adjective means “containing little or no fat.”
Using the common definition of the word, a Lean Hospital would be a hospital with little or no fat.
So the word lean automatically creates an association with fat. In a business context, fat is considered unnecessary waste that should be cut away.
I hypothesize that if you did a literature search that predated using lean as a word to describe the Toyota Production System, you would find examples of executives saying things like “we need to get lean and cut the fat.”
Because the word lean already has these preexisting connotations related to “fat” that should be “cut away”, I think it is understandable that people hear “lean” and think “cut.” Very few people appreciate the term Lean in all the glorious goodness held by the lean community. Even Mark Graban has mentioned that when working in hospitals he finds it useful to leave out the Toyota manufacturing roots of the lean tools he is introducing.
It might help if when people used the term lean, they clarify that they are using the word in its more positive definition of “fit, strong and healthy.” When the word is framed in that context, it conjures up images of exercise, hard work and self-disciple to achieve a desired state.
Personally, I think trying to explain lean to the general public in terms of the Toyota Production System is a lost cause. Even within the Lean community people argue about what it means to be “lean.”
Boiling a complex idea with many nuances into a single word is tough. It doesn’t seem fair but that is the way it is. (“Fair” is an example of a word that represents an important concept but determining what is fair can be tough and has been the source of endless arguments.)
Thanks for the thoughts, Bill.
Yes, the word “Lean” is an albatross around this whole movement’s neck. I understand the need for Womack, Krafcik, Jones, etc. to have a term that’s not Toyota-centric, especially in the auto industry.
The word lean usually means “not having enough.” Headlines talk about “living in lean times” during a recession and it means not having enough money or resources.
In terms of “fit” – have you seen Dan Markovitz’s book “Building The Fit Organization”??
http://amzn.to/1JKlrzd
As for Toyota… I realize that people don’t want to hear about Toyota. Sometimes, they NEED to hear about Toyota, though. I’ve actually started incorporating more stories from my auto industry days because they are “human stories” not “manufacturing stories.”
Toyota isn’t perfect, they have a clearly defined true north. Ask 100 Lean consultants about Lean and we get 70 different answers (many of which are just wildly incorrect.
Toyota is pretty consistent in their definitions. That’s what Lean is to me.
http://tssc.com/tps.asp
Maybe we’d be better off calling it “TPS” since the word Lean is pretty tainted by stuff that’s not Lean. Would Toyota sue people who said “We’re TPS consultants… it’s just a toolbox… it’s all about ROI and saving money”??
Here is a post by Rob van Stekelenborg, from The Netherlands:
Sorry, But Lean Is About Cost Reduction…
As I responded there:
Thanks for linking to my post and sharing your thoughts. Of course cost is important, as is long-term profitability of an organization.
The problem is when a healthcare organization only focuses on cost reduction. It’s not really Lean if they are just removing resources from an organization instead of reducing waste.
It’s not really Lean if they’re not also focused on improving flow and building in quality at the source.
It’s interesting to me that the word “cost” doesn’t appear even once on the Toyota page on TPS.
Thanks to Rob for his perspective.
Hi Mark,
Thanks for providing the inspiration to write my post and for having posted the link to my thoughts here.
Cheers, Rob
BTW, Ohno himself also used the analogy of fat and wrote that “rationalization means getting rid of fat”.
Thanks, Rob.
My question would be “Did Ohno say those words in Japanese or English?”
If in English, how much context or tone was lost in translation?
I’d never try to use the phrase “cutting the fat” in an American organization, because that would get people upset in different ways.
[…] not really Lean when an organization focuses exclusively on cost or […]
[…] organizations are only focused on cost cutting, that’s not really Lean (see my recent post). If you’re not focused on the patient as a customer, that’s not really […]
[…] the key to a culture of continuous improvement. That and not focusing primarily on cost savings, even though cost is […]
[…] ignorant about Lean. They don’t have any experience with it. Maybe they’ve somehow gotten the idea that Lean is all about cost cutting and they’re already good at cost cutting (which probably means layoffs, which is NOT the Lean […]
[…] Where Do Hospitals Get the Idea that Lean is Only About Cost Reduction? […]
[…] There’s also a financial cost that’s especially significant in healthcare. Errors and harm not only destroy lives, but they can destroy trust that people have in our healthcare providers and facilities. Lean is often a “safety first” philosophy in manufacturing companies and we need more of that thinking in healthcare, instead of focusing just on cost and efficiency. […]
[…] But, they disingenuously mock up a patient on an assembly line as the voice over from the Lean video says specifically that Lean is not about turning patient care into an assembly line. Sigh. The Lean model IS about better patient safety… not just cost. Again, if an organization is only focused on cost or the bottom line, that’s not really Lean. […]
[…] Their goals with Lean would be familiar to those doing it well in other countries (those not just focused on cost): […]
[…] COO says “a lot of people think Lean is cost cutting… it’s not” (I’ve said the same thing). Huebbers rightly points out that Lean is also about effectiveness and […]
[…] too hard to get alignment between improvement and goals can stifle participation. If leaders only want ideas about cost reduction, staff might not care and might not participate. That’s natural and to be […]
[…] Where Do Hospitals Get the Idea that Lean is Only About Cost Reduction? […]
[…] Mark Graban, auteur et praticien reconnu dans le domaine du Lean Healthcare, en fait partie. Je vous invite à lire son livre Lean Hospitals et un de ses posts : https://www.leanblog.org/2016/01/where-do-hospitals-get-the-idea-that-lean-is-only-about-cost-reducti… […]
[…] I invite you to read the book by Mark Graban, Lean Hospitals and his blog . Several of his articles denounce the clichés on Lean. I particularly like this one: Where Do Hospitals Get The Idea That Lean Is Only About Cost Reduction? […]
Hi Mark Graban,
Thanks for this post, i am with you according to the topic, I have one question, Lean concept in healthcare for quality and patient safety, cost, waiting times, and staff morale, but why most of the health care managements looking for cost cutting mainly, by instead of above all things?
You’d have to ask those executives. It’s an old habit to be focused mainly on costs. Many of them were taught to do this.