Once again, in the spirit of “Lean publishing” (referring to publishing in-progress books), my book Practicing Lean has another new incrementally-added chapter. For now, you can buy the book through LeanPub.com, which has options including naming your own price and receiving updates as they are added. Eventually, when the book is “done,” I'll make it available through more traditional Amazon channels, including as a paperback and Kindle book.
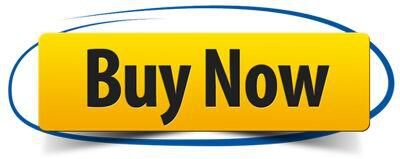
Chapter 8 is written by Bob Rush, who currently works as a Lean Manufacturing Group Leader at Tesla Motors. Tesla, of course, is in the building that was the former NUMMI factory (the famed joint venture between Toyota and GM). Bob has been writing a series of posts on LinkedIn in the theme of “Lean observations from an old guy.” I enjoyed the first few posts and, since what he was reflecting on was right in the spirit of “Practicing Lean,” I reached out and asked if I could edit them into a chapter for the book… so, here we are.
If you'd like to buy the book, remember that 100% of author proceeds are being donated to the non-profit Louise H. Batz Patient Safety Foundation. That said, the minimum price in the “name your own price” model is $2.99. You can pay the recommended $6.99 or other prices (even voluntarily pay more, if you like — it's for a good cause). Somebody chose to pay $10 the other day, so thanks to them!
Here is an excerpt from the middle of the chapter:
Learning From an Expensive Mistake
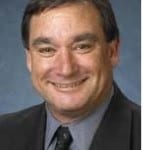
To my racing buddies, we always say you are either on the throttle or you are off the throttle. No race has been won by being off the throttle. Ted Lin, founder of Lin Engineering, told us to “Play to win, don't play to not lose.” Your efforts could have the same results, but the effort and the feelings about that effort are totally different. My sensei has told me repeatedly that there are lessons in everything you do, but the best ones come from a spectacular failure. I have done this as an employee and I have seen it as a Lean consultant.
Early in my career, I was moved around quite a bit in operations. Our VP of operations believed in cross training and in placing talent where it could have an impact. I moved from shipping clerk, to industrial engineer, to production planner, and then to buyer. This was in the days when MRP was first coming on the scene, but we were still on the Kardex system. Yes, that is how old I am. I had a need for a certain electronic component and worked the supplier for a price break and got it. I ordered $1 million worth of this product, and it was delivered as promised on time and to specification. Unfortunately for me, I had transposed numbers on my order and we received a product that was unusable for our needs.
Rather than fire me, the VP told me to find a solution and then to let him know when I did. It took me weeks, but I found a competitor that used this model AND they paid more for the product than we had. I gave them a 3% discount off of their regular price and we made 5% on the material. I more than learned my lesson from that and, to this day, I check numbers very closely.
I am always asked about what causes failures in Lean implementations and, in my experience, the biggest one is Management (with a capital M). But, not just from the lack of commitment, but from both micromanagement and from playing to not lose.
If a company bets their future on Lean, it is easier to try to not lose than it is to try to win. What happens is that the new people aren't allowed to do as much as they could, being limited to safe projects overseen by a manager and/or a Lean leader.
The new person gets micromanaged, I can just hear it now; NO! I said the “I” goes inside the inventory triangle on a VSM, or your data box has to look exactly like this, or here's what your VSM will look when you are done as the teacher draws it on a whiteboard.
If they make their VSM wrong or if the Kaizen event is not held to the exact standards someone else wants, does that make it any less successful? Not really and, if we are truly Lean coaches or champions, we will take these chances as a real learning time and show them where they went wrong or even suggest some solutions but we will let them make more mistakes if we want them to learn. One of the people I have worked with over 10+ years on Lean recently told me that he learned more when he failed and we talked about that failure then when he succeeded and had no idea why it worked. He is now a Lean coach and tells me of some failures he's seeing.
So, I say let your junior people go try something, anything and, if it doesn't work, have them tell you what lesson they learned from it. You can then work on helping them along their Lean journey by teaching them a better way.
Thanks to Bob for allow me to edit and share his work. I'm sure he'll keep writing over on LinkedIn.
Please scroll down (or click) to post a comment. Connect with me on LinkedIn.
Let’s work together to build a culture of continuous improvement and psychological safety. If you're a leader looking to create lasting change—not just projects—I help organizations:
- Engage people at all levels in sustainable improvement
- Shift from fear of mistakes to learning from them
- Apply Lean thinking in practical, people-centered ways
Interested in coaching or a keynote talk? Let’s start a conversation.
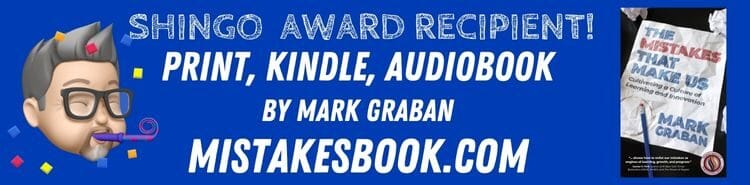
Here is a podcast that Gemba Academy did with Bob:
http://blog.gembaacademy.com/2016/01/21/ga-094-how-to-with-bob-rush/
Check it out!
Just met Bob today through a mutual colleague. We discussed Lean Maturity Assessments, and his advice was 100% on point, informed from some great experience! Great to see he was part of your book. He is a great coach.