Lean healthcare really is a global movement. Last year, when I went to Japan, we had people in the group from all across Asia, Denmark, Canada, the U.S., and Saudi Arabia. Health systems all around the world need to improve quality and patient safety, reduce waste and create better work environments, reduce waiting times, and get costs under control. These are universal challenges.
Thankfully, Lean is helping.
Here's a story from Malaysia that caught my eye: “How assembly lines inspired Asia's hospitals.”
Hear Mark read this post (subscribe to the podcast):
From the article:
Malaysia piloted the technique in Sultan Ismail Hospital in 2013. Its orthopaedic clinic, which previously operated from 8am to 5pm, was able to clear patients by 2:30pm on most days. “We use lean management techniques to remove bottlenecks and focus on the speed at which processes are completed,” wrote Idris Jala, CEO of Malaysia's Performance Management and Delivery Unit, in his Transformation Unplugged blog.
The article also talks about the use of Lean in India:
Take India's Narayana Hrudayalaya Hospital, set up by cardiac surgeon Devi Shetty. Using lean practices, Shetty has dramatically increased the number of heart surgeries performed, almost like a car assembly line.
While “efficiency” is sometimes a dirty word in healthcare, increasing throughput can be of benefit to the patients when waiting times are reduced (also see the example of how Toyota helped UCLA-Harbor reduce waiting times for patients who were otherwise going blind while waiting).
Through focusing on these efficiencies, more patients can be treated – more lives can be saved.
In the Lean approach, we engage people in redesigning and continuously improving the way the work is done, which leads to a reduction in waste. Reducing waste helps us improve patient safety and quality while also improving patient flow and efficiency.
Efficiency is an end result. Lean is not about setting “efficiency targets.”
The author of the article doesn't quite understand that, writing:
There could, however, be downsides of the technique. Setting efficiency targets could encourage the wrong behaviour from employees. For example, they could focus on efficiencies at the expense of patient care. A patient might be treated faster, but if something is missed because they weren't asked enough questions, they may have to return.
Setting efficiency targets (or targets of any type) without also having a METHOD for improvement can lead to all sorts of problems. See the examples of the NHS emergency departments and the VA waiting time scandals for examples of people “fudging the numbers” or “gaming the system” instead of improving.
Setting efficiency targets without also having METHOD for improvement leads to all sorts of problems Share on XIt's not Lean to “focus on efficiencies at the expense of patient care.” If you look at the roots of Lean, the Toyota page on the Toyota Production System shows how TPS is about both flow and quality. It's not “efficiency only.”
The author also writes:
Equally, if lean techniques are not introduced correctly, they can demoralise employees. For example, when the British tax office introduced it, employees went on strike. They assumed it was being used to find evidence to make job cuts.
Yes, Lean “not introduced correctly” would be what I call L.A.M.E., not Lean. Lean is actually the best alternative to healthcare layoffs and Lean organizations (in any industry) realize they won't get people engaged in improvement if they fear for their jobs.
But, as the article concludes:
But lean is intended to be a supportive, inclusive process. It tells every employee that their view is valued. Rather than management consultants or senior figures guiding an organisation, everyone has a say in how to improve operations.
That's all very true. Lean is NOT about efficiency at the expense of quality or safety. It's definitely not about management consultants or executives (or managers) telling people what to do.
Let's hope the true spirit and practice of Lean spreads around the world.
Please scroll down (or click) to post a comment. Connect with me on LinkedIn.
Let’s work together to build a culture of continuous improvement and psychological safety. If you're a leader looking to create lasting change—not just projects—I help organizations:
- Engage people at all levels in sustainable improvement
- Shift from fear of mistakes to learning from them
- Apply Lean thinking in practical, people-centered ways
Interested in coaching or a keynote talk? Let’s start a conversation.
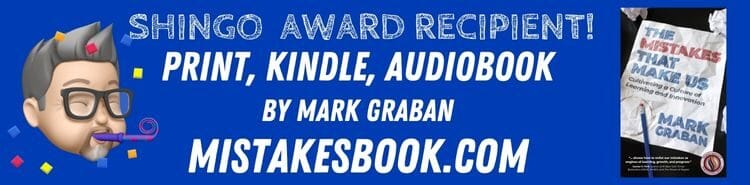