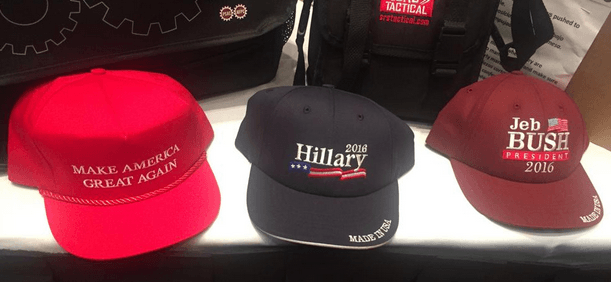
Last week, I attended the Northeast Lean Conference in Massachusetts, produced by GBMP. I had a great time, teaching a half-day workshop on Kaizen, leading a session where I facilitated Dr. Deming's “red bead experiment,” and hearing my friend Dan Markovitz talk about his new book Building the Fit Organization.
The conference had a “Lean Mall” where various companies had displays about their Lean efforts. I saw a very recognizable red hat — it's the Donald Trump “Make America Great Again” hat.
These hats (and hats for other candidates including Hillary Clinton and Jeb Bush) are made by a Newark company, Unionwear. Lean is their strategy and their production system. That's how they are competing against China.
I wrote an article about this on LinkedIn, but you can also read the full text below and I'll share more photos here.
Hear Mark read the post (subscribe to the podcast):
Full Article
Politicians have long sold merchandise as a way of raising money and allowing supporters to spread their names. In the current American presidential primary season, Donald Trump's red “Make America Great Again” hat has been all over the news. Of course, politicians from both parties are generally going to use American producers instead of importing hats. The more interesting part of the story is that many of these hats come from a Newark, NJ manufacturer that uses “Lean” as a competitive business and operations strategy.
Last week, I participated in a conference in Springfield, MA that focused on “Lean,” a management system and improvement methodology that's based, primarily, on the Toyota Production System. Companies around the world have been adopting these methods for more than 25 years, including in healthcare for the past decade or so.
At the conference, a company called Unionwear had a humble display that explained how Lean has helped them. In my opinion, the key ingredient isn't the use of common Lean tools, like 5S and value stream mapping. What really matters is leadership and, more specifically, senior leaders embracing the Lean philosophy, as illustrated in this letter from Mitch Cahn, Unionwear's president that was posted.
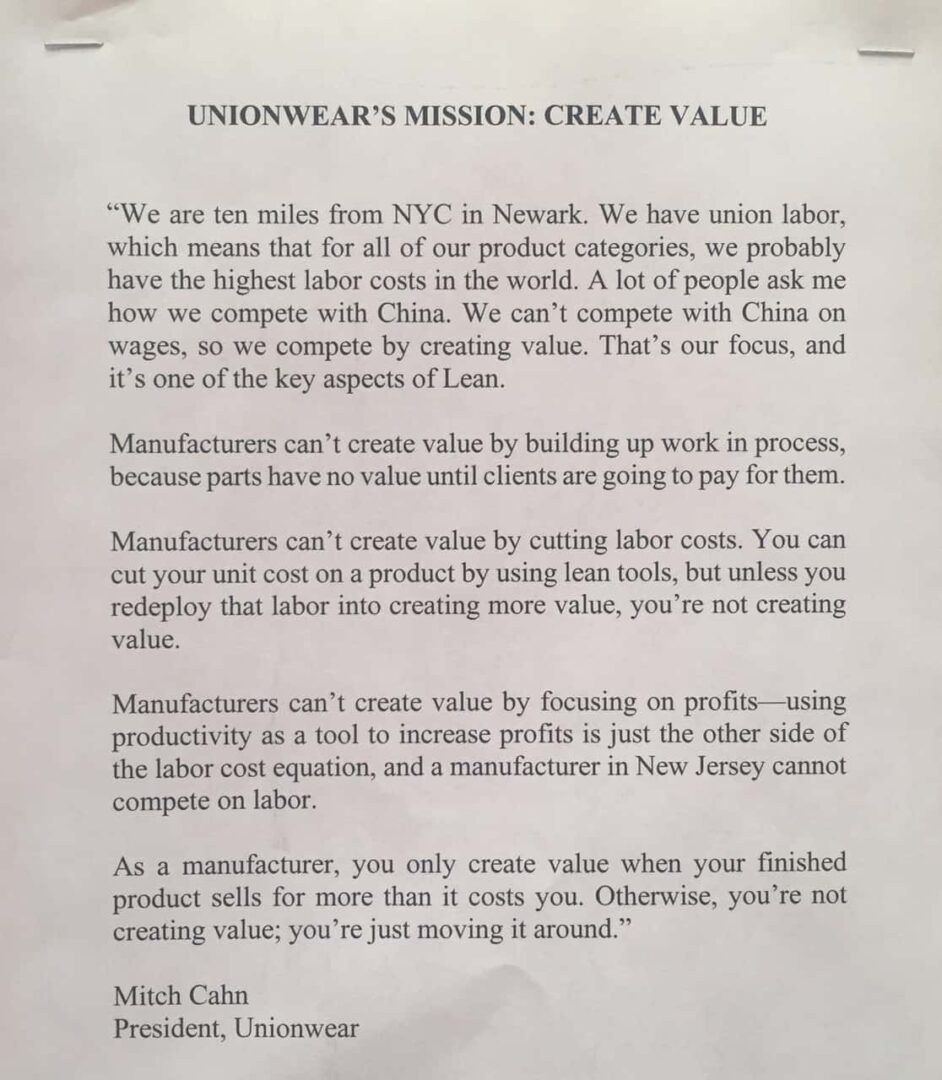
Unionwear, as their website explains, has employees represented by a union, Workers United. They undoubtedly have high rent, high wages, and some high costs in other areas, but Lean has been their strategy for countering those disadvantages. Candidate Trump blames China for “killing us” through smart trade negotiations. The reality is that American companies (and global manufacturers) have been flocking to China (and other countries) over the past 20 years as they chase cheap labor. However, as Cahn explains, companies can compete by creating value, such as being able to get hats to candidates more quickly, competing on speed, not just labor cost.
Maybe Washington can help, but even with the current political, legal, and tax environment, this “reshoring” strategy can work. Companies like General Electric have brought some manufacturing back to the United States, using Lean and being close to their customers to their advantage. Among other things, being a Lean manufacturer means keeping inventory low and, ideally, making only the hats that are ordered by their customers. Not having excess inventory keeps costs down. Any company can have low inventory levels. But, without Lean methods, that company might not be nimble or agile enough to produce the right hats in the right quantities at the right times (and at the right quality levels).
A Lean manufacturer also works to create a more respectful workplace, engaging employees in continuous improvement efforts, as shown in the conference displays. Toyota calls this approach “respect for people” or “respect for humanity” and it goes far deeper than being a slogan. Lean is an alternative to traditional cost cutting, which usually means layoffs (in manufacturing or in healthcare). Lean companies help protect jobs in a number of ways, as they commit to their employees instead of laying them off as productivity improves.
The hats made to promote Hillary Clinton and Jeb Bush have an obvious “Made in U.S.A.” label on the brim. The Trump hats have a label inside the hat that says the same thing.
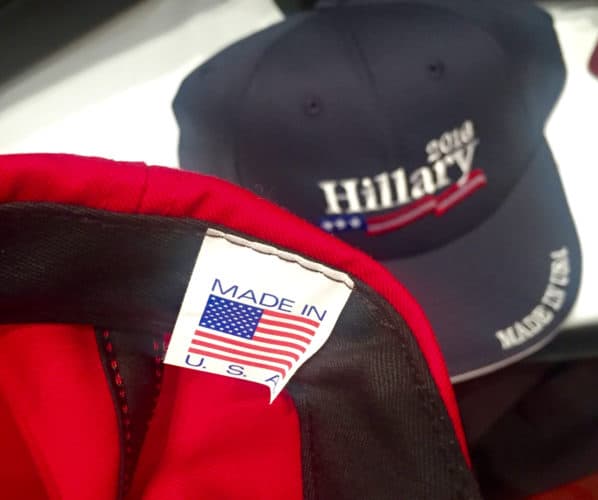
Instead of “looking for the union label,” we might start looking for the Lean label as a way to improve competitiveness and our economy, regardless of what's being said in stump speeches or what's happening (or not happening) in Washington.
More Photos
Click on any of the photos for a larger view.
Part of the display (I didn't get a picture of the width of the entire display, unfortunately):
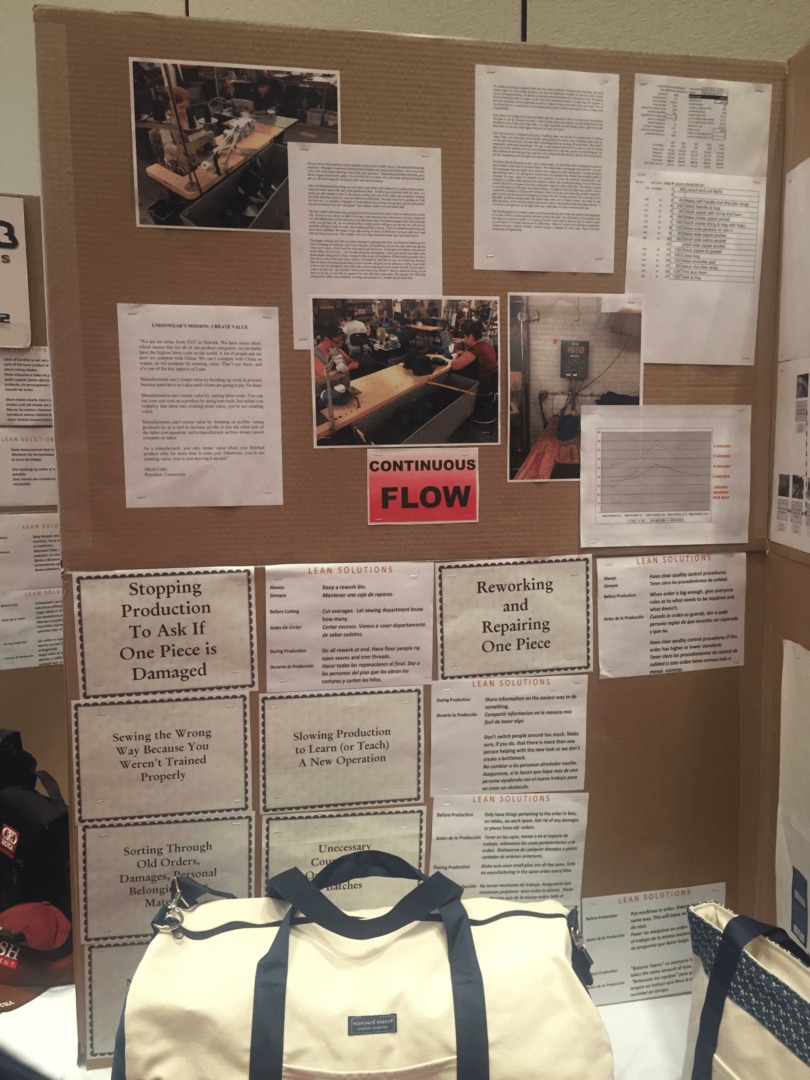
The storyboards emphasize core Lean concepts like:
- Continuous flow or one-piece flow
- Quality at the source
- Stopping the line
- Effective training
- Reducing waste
There's one story that was posted about improving flow by reducing batching:
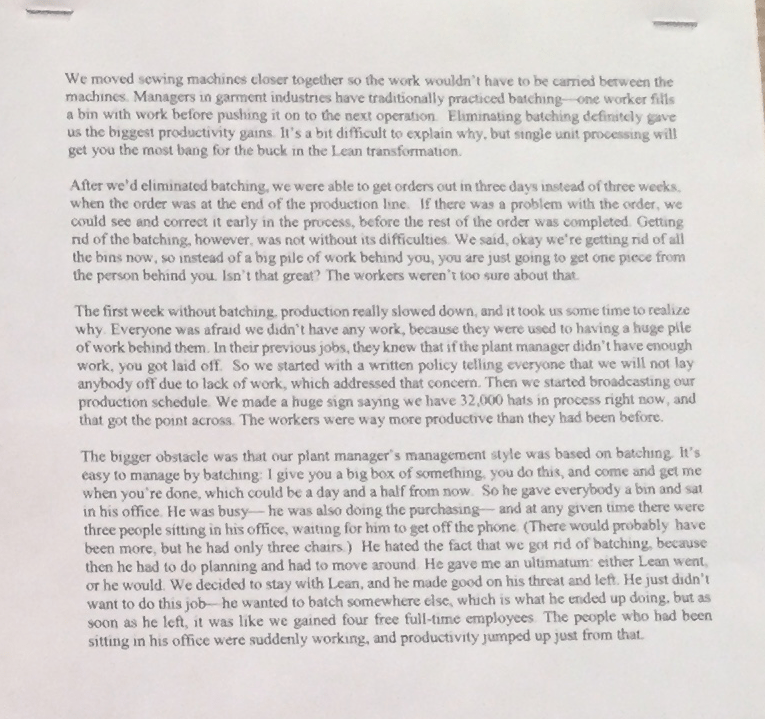
They moved machines closer together to reduce traditional batches. They were able to reduce lead times from three weeks down to three days. Smaller batches means, also, that you're going to find quality problems (and solve them) more quickly. Reducing batching isn't easy (I know that's true in more recent experiences in hospital labs), but if you work together to sort through the challenges, it's worth it.
I love, also, how they talk about having to change their management styles. That's key, of course, with Lean. It's not about fixing broken workers.
Here's a photo of their value stream analysis (for a type of bag they produce):
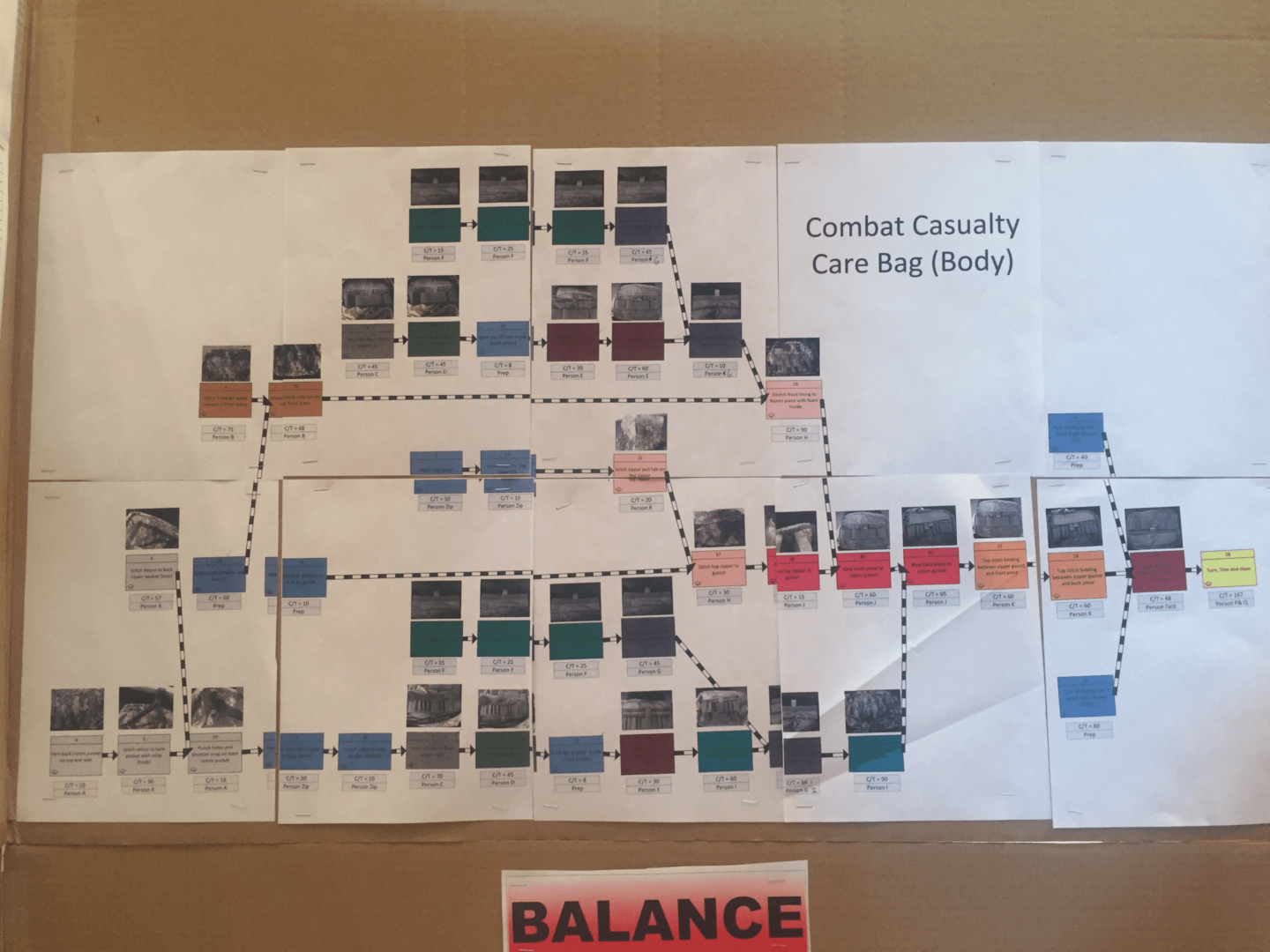
I'm hoping to connect with Cahn to learn more about this story and, hopefully, do a podcast with him.
Update — I did do a podcast with Mitch! Two of them actually.
Please scroll down (or click) to post a comment. Connect with me on LinkedIn.
Let’s work together to build a culture of continuous improvement and psychological safety. If you're a leader looking to create lasting change—not just projects—I help organizations:
- Engage people at all levels in sustainable improvement
- Shift from fear of mistakes to learning from them
- Apply Lean thinking in practical, people-centered ways
Interested in coaching or a keynote talk? Let’s start a conversation.
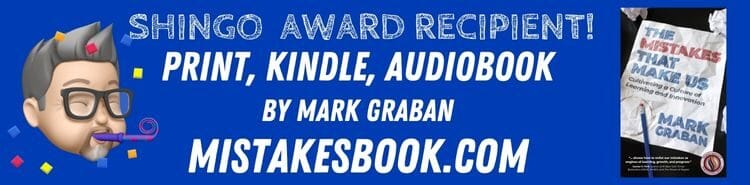
[…] learned about Mitch and his company because of a display they had at the Northeast LEAN Conference, which I blogged about here. What caught my eye was their display of politician hats they produce, including the famous red […]
[…] generally avoid politics here on the blog… In October, I broached the subject I blogged about a company that uses Lean principles to make Donald Trump hats in New Jersey (and interviewed the owner of the company), but that was during a time when Trump seemed like a […]