My two previous trips to Japan have been incredible experiences, both personally and professionally. I'm planning to go back in December with a tour group I'm helping organize with Kaizen Institute (learn more about joining us).
When people go to Japan, I think they are expecting to see perfect Lean practices. But, no. “Lean culture” is not the same as “typical Japanese business culture.” My friend Katie Anderson, a Lean healthcare specialist who is now living in Japan, wrote a great post about this for LEI.
She wrote, as one of her five key reflections:
Lean isn't inherently Japanese. It's not easy for the Japanese, just as it isn't easy in other cultures. Lean really is a blend of Western and Japanese cultures and practices – as it was from the beginning when Kiichiro Toyoda came to the U.S. to learn about automotive and management principles and brought them back to Japan. In many ways, some aspects we consider foundational to lean thinking (developing people as problem solvers, leader-as teacher) are counter to traditional Japanese business practices. Toyota and other lean thinking companies are unique in Japan, as are organizations in the West who practice deep lean thinking.
The Toyota Production System in some ways is a countermeasure for a “command and control” authoritarian leadership style, a culture of rigid rule following, and fear of failure. On the other hand, some principles and habits may be easier in the Japanese culture. Kata (routines) are common in everyday life, from pouring tea to exchanging business cards to the sport of sumo. Traits such as adherence to standard work and diligence to constantly improve one's job may be easier due to the culture of compliance and seeking perfection.
I love her description of TPS as a countermeasure to some typical Japanese business culture concepts. As I've written about, I think the andon cord was a specific countermeasure against the challenges of speaking up in the workplace. The andon cord didn't come naturally. Not even at Toyota.
Hear Mark read this post (subscribe to the podcast):
I've visited five different Japanese hospitals in two visits. They are all practicing an evolution of Total Quality Management (many for 15 or 20 years). See my earlier post about quality circles still being alive and well in Japan. TQM often creates a great foundation for what we'd recognize as Lean practices or Lean daily management practices. In these organizations, TQM has top executive support and participation. There's a strong focus on quality and the customer, and employees are expected to participate.
But, the shift from formal six-month quality circle projects to daily Lean practices is not necessarily easy or natural.
One artifact of Lean thinking, or a basic Lean practice, is 5S.
Did I see 5S or visual management everywhere I looked in hospitals? No! It doesn't come naturally. People in the U.S. (or other countries, I'm sure) make excuses or give up too easily on Lean, saying “well, this would be easy if we were Japanese.” No. Quit hiding behind that excuse.
Here is a cabinet from a surgery department, outside of operating rooms. Does that look very organized or 5S-ed?
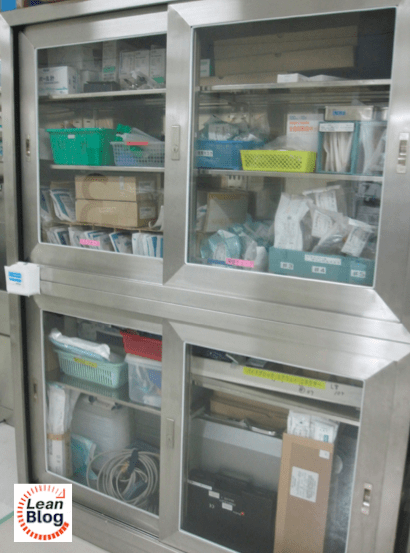
Now, sometimes the most thoughtful 5S activity doesn't look very impressive. Putting tape outlines or labels on shelves for everything might look noticeably 5S-ish, but the real benefit often comes from just putting items near the point of use, making them easy to find, reducing walking and motion time, etc.
Even in that cabinet, if you take a closer look, things are just sort of jammed and piled in there. Our hosts admitted that they still had not made much progress on 5S.
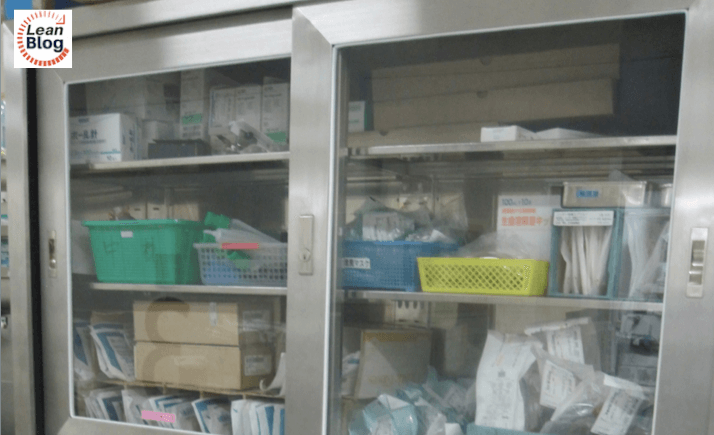
That cabinet and that hospital were not really an isolated case.
In some hospitals and some areas, you could see the 5S progress. They had before and after pictures to show. You could see the CEO doing 5S audits.
Here's a pharmacy employee showing some of their before and after:
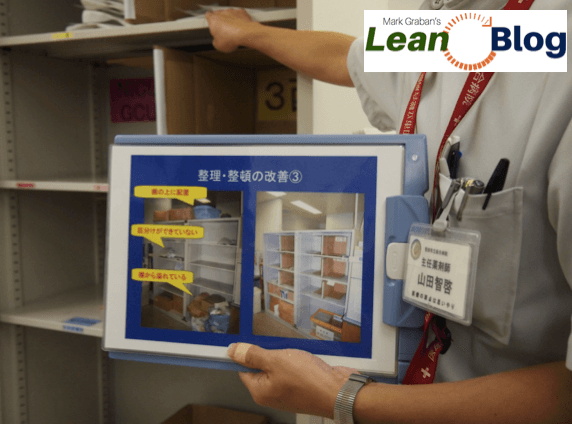
Here's another before-and-after with crutches:
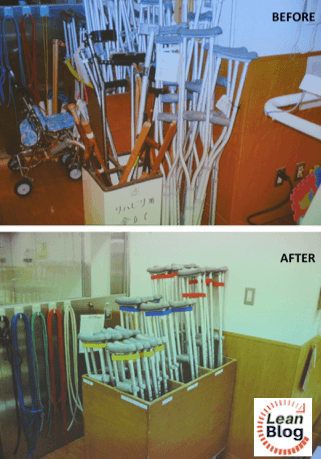
So, yes, you see some good examples of 5S and people will explain the process they went through and the progress they made.
One hospital had made small bags, sort of like fanny packs, that kept the most commonly and frequently used supplies right on the nurse's person, saving them time and motion. See the picture below, along with how the bags are hung and stored. This makes work easier for the nurses.
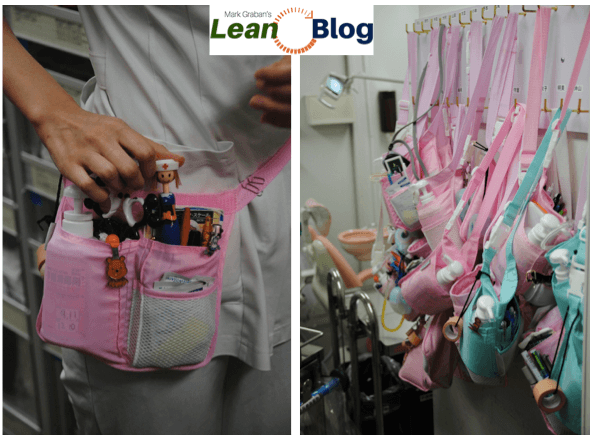
Here's an example of how they organized power strips. I know when I store power cords and strips at home, they become a tangly mess. Not here, with 5S:
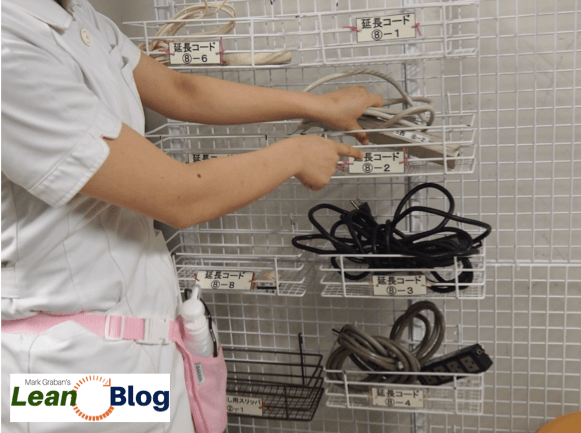
And, then, you see some examples that would make some 5S advocates drool… the organization, the precision, and visual management of some drawers, like this “crash cart” cabinet. See the foam cutouts that make sure you can't pile too many unnecessary medications into a segment of the drawer. 5S helps make sure there's the right AMOUNT in the right place at the right time. Having too much doesn't help if you're having to then dig through a cluttered drawer.
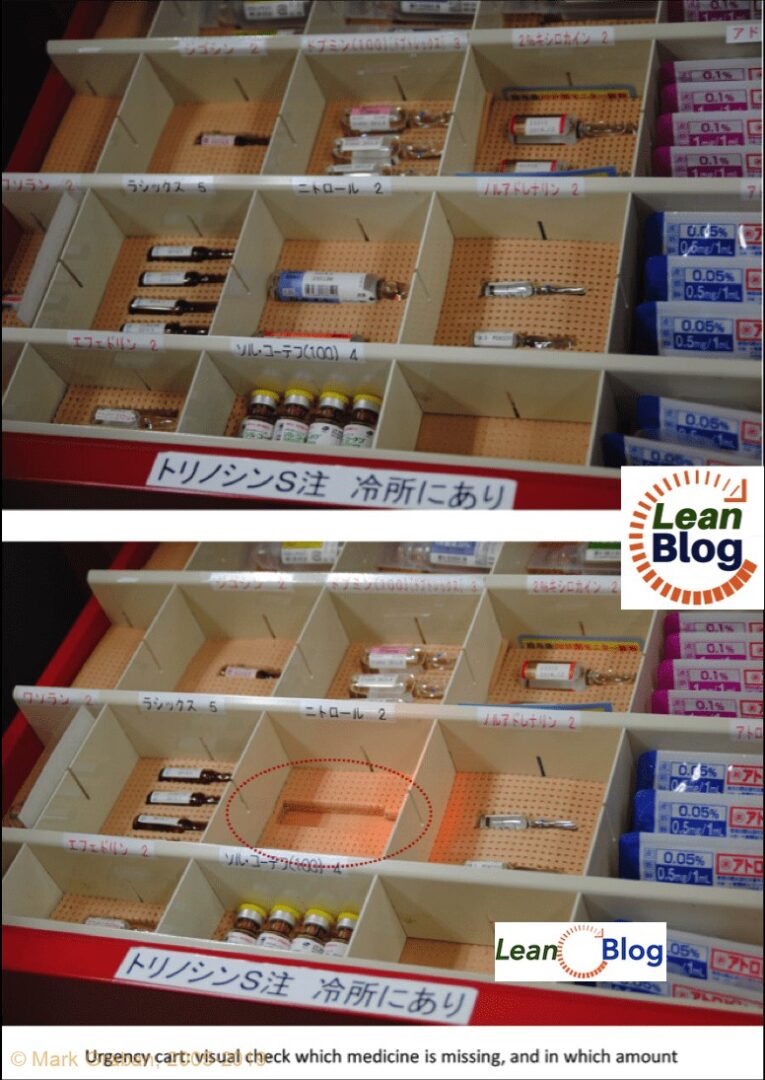
See the bottom picture and the red circle and how it's obvious if something is missing?
At one hospital, they even took that level of precision and detail to a desk drawer in the nurse's station. The question I would ask, respectfully, is if that's helping prevent a problem? Are they taking 5S practices too far? Or, are they building discipline within the workplace?
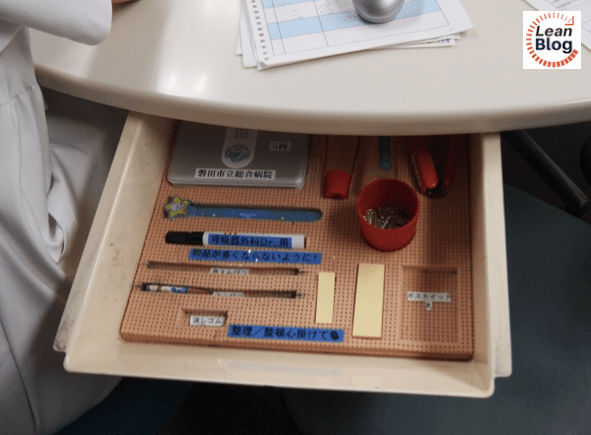
When you see “good 5S” in the Japanese hospitals, it's not the norm. It's not natural. It's not easy. It's something they've had to work at. It requires leadership. I think that's a valuable lesson to take home. It's worth seeing with your own eyes (such as through our tour).
The benefit of a trip like this is not just about seeing good 5S or a lack thereof. It's about seeing and learning about Japanese culture and how it sometimes helps with Lean and sometimes gets in the way (as Katie writes about).
The tour is about a shared experience… learning the other great practices from Japanese hospitals and businesses and comparing notes with a global group of visitors… learning from each other and learning from people in Japan.
It's a great experience, on many levels.
What do you think? Please scroll down (or click) to post a comment. Or please share the post with your thoughts on LinkedIn – and follow me or connect with me there.
Did you like this post? Make sure you don't miss a post or podcast — Subscribe to get notified about posts via email daily or weekly.
Check out my latest book, The Mistakes That Make Us: Cultivating a Culture of Learning and Innovation:
Hi Mark – It’s been a fascinating experience to live in a different culture and to see how Lean is practiced in Japan. I’m glad that enjoyed my LEI Lean Post article!
Thanks for sharing the article and your thoughts about Lean as countermeasures to cultural traits. I think this is true not just in Japan, but in the U.S. too. For example, many of the healthcare organizations I’ve worked with are drawn to Lean management because of the emphasis on A3 thinking and PDCA. Americans are great at Plan-Do, but as good at Check-Adjust. Going through the rigor of working through an A3 helps them learn to better slow down, reflect, and more deeply understand the problem they need to solve. In contrast, the Japanese have a deep cultural practice of hansei (reflection).
I’ve too have been surprised that Lean is not practiced as a management system in service industries and healthcare. In that regard, the U.S. and other countries are farther ahead than Japan.
I look forward to seeing you here in Japan in December and to sharing some learning experiences (and good food)!
-Katie
Yes, although I’ve seen people have the mechanics of an A3 form still pretty much Plan and Do instead of PDSA… jumping to conclusions/solutions within the framework of an A3. That’s a great example of copying the tool without copying the mindset.
[…] 5S: The Good, the Bad, and the Extreme in Japanese Hospitals (768) […]
[…] My friend Mark Graban has also observed this in previous trips to Japanese hospitals and organizations. […]
Hi Mark-
Great article! It is very true that “Lean culture” is not the same as “typical Japanese business culture.” Certain processes we describe as “lean” are just already embedded in Japanese culture, and are a way of life for them. A few of the images you shared seemed to be an example of lean thinking, but other images just displayed discipline, but each process or way of thinking can be interpreted differently by everyone. Some may think it is extreme, but others may say it is demonstrating organization and discipline. All the images can be up for interpretation.Thank you for sharing!
Thanks for reading and for commenting, Abigail!
[…] My friend Mark Graban has also observed this in previous trips to Japanese hospitals and organizations. […]
Love the article. I would have assumed that lean would be a major focus in Japan so that surprised me. It’s cool to see how much of a difference the 5’S can make on a business. Especially in hospitals you don’t want to waste time looking through inventory because you need to focus on the patient. Great article overall.