I saw this story when it originally appeared online as part of a local public radio station in California. It was now picked up nationally by NPR and a number of you emailed me about this Lean healthcare piece about UCLA Medical Center:
Hospitals Turn To Toyota To Make Care Safer And Swifter
It's a generally positive story about a large hospital system working to improve… and turning to Toyota (directly to Toyota) for help. To be fair, they did far more than organize closets… but that was the story that started the piece.
From the story:
“Until recently, nurses at Los Angeles County Harbor-UCLA Hospital had to maneuver through a maze of wheelchairs, beds, boxes and lights to find surgical supplies in the equipment closet for the operating rooms.”
That's still such a common story even though Lean has been used in healthcare for over 15 years. There are still many health systems missing basic 5S practices. That surprises me in this case since UCLA has had a formal Lean program for a while. I had a chance to visit a few years ago and they had hired people who formerly worked in manufacturing.
Again, from NPR:
“They are adapting the carmaker's production system to health care — changing longstanding practices such as how to store equipment, schedule surgeries and discharge patients. The philosophy, known as lean, depends on a continuous team effort to pare inefficiency and improve quality.”
Thankfully, the story didn't incorrectly portray Lean as just being about speed or efficiency. It's also, at the core, about quality — as Toyota explains.
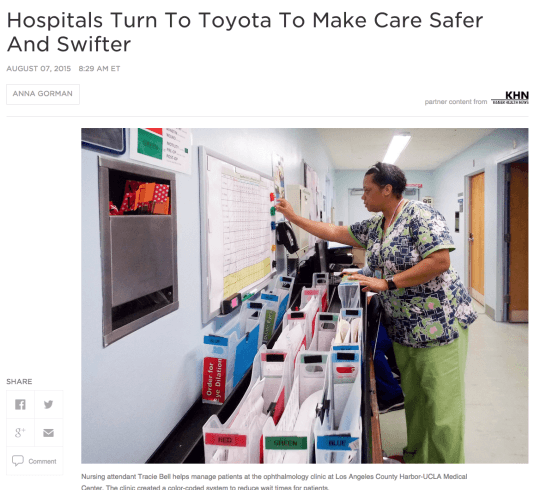
Hear Mark read this post (subscribe to the podcast):
Journalists always have to present both sides of a story. I was interviewed a few years ago for a story in the New York Times about Lean at Seattle Children's Hospital and the reporter was having trouble finding anybody with an opposing view about Lean. I was afraid they wouldn't be able to run the story without that opposing view, so I actually made introductions to a nurses' union who had a history of criticizing Lean (incorrectly, I think).
So a similar thing happens here:
DeAnn McEwen, a health and safety specialist with National Nurses United, says lean management reduces nursing to a series of standardized tasks, as if nurses were robots applying nuts and bolts to identical patients.
“The problem with that is patients, of course, are not widgets and nurses are not robots,” she says. “And nursing care is not a commodity but a service. It's a process that requires critical thinking and the application of judgment.”
It's not true that Lean turns people into unthinking robots. That's not true at Toyota and it's not true in a Lean hospital. McEwen is arguing against a “straw man.” Of course, patients are not widgets or cars.
It makes me think of this Captain Obvious meme:
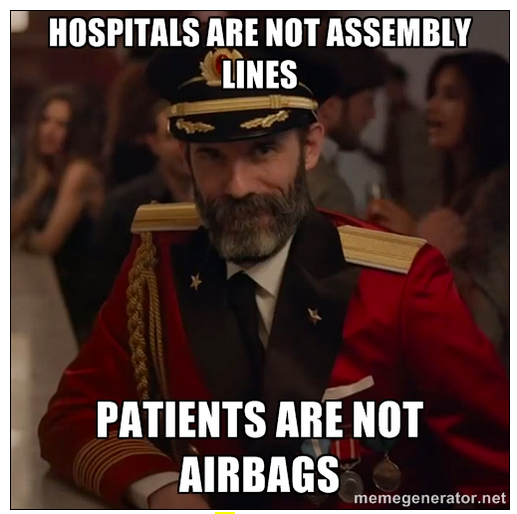
By the way, THESE are hospital robots… and I'm not convinced they are necessarily the right thing to do when you consider all of the pros and cons and all of the other ways you could free up time for people through process improvement. I worked with one hospital that tore out its pharmacy robot because it wasn't really saving any labor and the robot choosing the right med still had some risk of human error in the medication supply chain… so they decided it wasn't worth it. Lean organizations don't throw technology and robotics at everything (see past posts about hospital robots here, here, and an article here).
But back to the non-robot humans… working in a car factory requires critical thinking and the application of judgment… the same is true with Lean healthcare. Lean has, in so many cases, resulted in improvements in patient safety and quality and it's not like hospitals without Lean are safe to begin with (see the stats). Saying “patients are not cars” is true, but not a compelling argument against Lean.
Back to the article and UCLA… Susan Black is the hospital's “chief kaizen promotion officer” as of 2013. She says Lean “is not a flavor of the month.” For that to be true, I'd add, the other hospital chiefs need to be on board with Lean and Kaizen, not just the main Lean person.
Jamie Bonini (who I've written about before) is the head of the Toyota Production System Support Center. They famously helped the NYC food bank as you can see here.
“Before, it was total chaos,” says Tracie Bell, a nursing attendant. “We had piles and piles of paper. With this new color-coded system … it makes it a whole lot easier for us to do our jobs.”
Within several months, staffers doubled the average number of new patients seen each day. In addition, the time patients spent at the clinic dropped from 4 1/2 hours to just over two. Surgeries also got scheduled more quickly.
Those are great results and, it seems, a great start (or a reboot) for Lean at UCLA Medical Center.
NPR Readers Chime In
The reader comments on the story are interesting – some advocates for Lean and some who are, shall we say, not impressed.
The first comment says:
These people couldn't re-organize a closet without taking inspiration from an external source? Remind me never to go there.
It made me think of the “McKayla is not impressed” meme, as it would look like here:
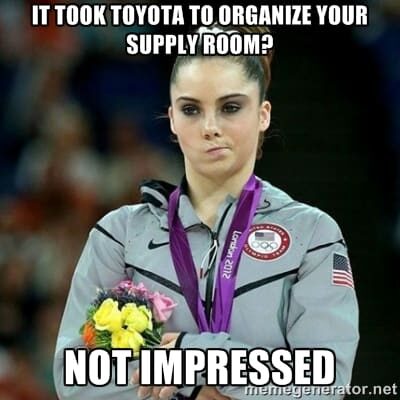
Another commenter says:
I continue to be appalled at the sloppiness of hospitals. Why does surgery require the lessons of pilots to have a simple check list before commencing? Do they not see the need for being careful and thorough to avoid cutting off the wrong leg?! I think it goes back to the arrogance of doctors and males and the way they treat their underlings. Organizing the closet is a new concept?! Almost any business which does not even work with life and death has an organized closet. I work with them; I see them; I'm even paid to do the organizing. You don't need Toyota to figure out what is needed. I have great fear of being in a hospital, particularly for surgery. Will they ever get their act together?
Well, aviation has shown that safety does not come from “being careful.” It comes from teamwork, processes, training, and checklists. Healthcare could use all of that…
Another person wrote:
Improving efficiency is not a ‘toyota strategy'. It's common sense for any business or organization.
If it's just “common sense,” why isn't it more common, even in manufacturing? Some things about Lean are actually quite counterintuitive (such as the smaller batches can be more efficient).
Anyway, there are other comments that bash hospitals, mock Toyota, and complain about something called “standardization mania.” I'm not sure what “standardization mania” is, but it's probably a misapplication of Lean.
I'm working on a 3rd revised edition of my book Lean Hospitals and every edition has emphasized, going back to 2008 and the original publication, that we should never standardize for the sake of standardizing. Standardization must be done thoughtfully and it must solve or prevent important problems that matter. We must engage the people who the work to make sure we standardize things that matter and to the right level of detail.
Good luck to everybody at UCLA (and every other health system that has big opportunities for improvement).
Please scroll down (or click) to post a comment. Connect with me on LinkedIn.
Let’s work together to build a culture of continuous improvement and psychological safety. If you're a leader looking to create lasting change—not just projects—I help organizations:
- Engage people at all levels in sustainable improvement
- Shift from fear of mistakes to learning from them
- Apply Lean thinking in practical, people-centered ways
Interested in coaching or a keynote talk? Let’s start a conversation.
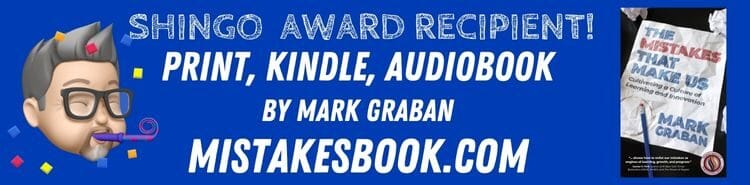
A friend who recently got back into bedside nursing laments being a robot. Nurses (and other hospital staff) complain about being like robots BEFORE Lean.
Lean is a path out of that trap.
In response to this article, she wrote:
I don’t think hospitals need any help from lean to treat their employee’s like robots. Much like layoffs, they have figured that out pretty well on their own. What they do need from lean, is to help develop a management system that results in an environment where employees can think critically to improve their work. Most importantly, management needs to provide the time and resources to make this happen.
I agree it’s a similar situation with a fear of layoffs… hospitals have relied too much on layoffs in the past, without Lean.
Again, Lean is the best alternative I can think of to layoffs and lazy, ineffective cost cutting. Some are learning that lesson, as you can read here.
Thank you, Mark, for another well-written post! The robot comment irks me. One of the medical centers I worked with had the most abysmal nursing morale I’ve seen (and I’ve seen very poor morale nearly everywhere) and they were working in a very run-down hospital. One of the complaints was lack of storage and wasted time looking for equipment and supplies.
A single four-day 5S rapid improvement event freed 15 drawers, 7 large storage closets, and 22 shelves. It also resulted in freeing 42 hours of searching for “stuff” per nursing employee per year, which was used to increase the number of bedside nursing hours. Morale went through the roof.
When people poo-poo 5S, I always remind them of how a little saved time can really add up.
Thanks, Karen. Yes, as simple and basic as 5S sounds to people, it often DOES solve some real problems and can really reduce a lot of waste. Making work less frustrating and freeing up time for patient care should be something that every nurse (and nurses union) can support.
Not all nurses unions bash Lean by the way.
Thanks for sharing your example.
I get frustrated when I see a hospital that has been “doing Lean” for years, yet they haven’t addressed these basics to support the staff through 5S.
Every hospital should do basic 5S even if they aren’t going to fully embrace a Lean culture and management system.
Hello Mark,
Another great post!
It seems that often when people speak negatively about lean, it’s because they think it means ‘stingy’. If only McEwan and others could see that implementing lean will allow nurses to do more ‘critical thinking and application of judgement’ instead of searching for the stethoscope.
I am reminded of a quote of Stephen Covey’s: “…but common sense in not necessarily common practice.” I would love for all stay-at-home moms to learn Lean at Home, as well as have Lean taught in our schools. It is applicable to so much more than any one market sector or industry.
Exactly, Lynn. Like I said in my comment to Karen above, nurses and the unions should LOVE 5S, as it frees up time for critical thinking and patient care.
But, if 5S is forced on people in a clumsy way or “done to people” instead of engaging them… that’s not really Lean and I’d understand why they would get upset.
Well, the critic of Lean is from National Nurses United. the union that just endorsed Bernie Sanders for president. So, take their comment for what it’s worth..
http://www.cnn.com/2015/08/10/politics/bernie-sanders-nurses-endorsement-2016/index.html