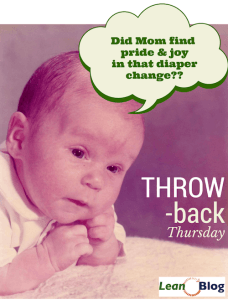
I stumbled across an article from the Inc. magazine archives from 1987, so it's today's “Throwback Thursday.”
In 1987, I was starting high school and that was probably right about the time when my dad, an engineer for General Motors, was able to attend one of Deming's famed four-day seminars. Hearing about that was my first exposure to Deming or anything vaguely related to Lean thinking.
The picture at left is me, circa 1973.
Here's the article:
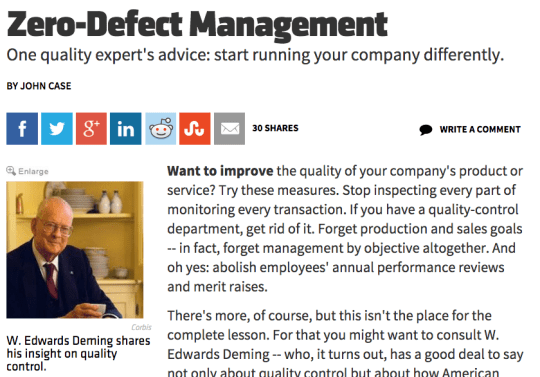
Their first paragraph summarizes some of the key Deming ideas that were (and still are) so revolutionary:
- “Stop inspecting every part or monitoring every transaction. If you have a quality-control department, get rid of it.” (I think there was a typo in the article)
- “Forget production and sales goals — in fact, forget management by objective altogether.”
- “And oh yes: abolish employees' annual performance reviews and merit raises.”
It's interesting, to me, that Toyota (a company influenced greatly by Deming) still has final inspection areas at the end of their assembly lines (see pictures). This surprises people who visit the plants. “I thought Toyota built in quality at the source??? It says so on their website!”
Hear Mark read the article (subscribe to the podcast):
Well, Toyota, for all of their efforts, still does not have a perfect process. So, they've decided that having final inspection (while technically “waste”) is better than passing defects on to customers. Would Deming be disappointed in them? I don't know.
From the article:
“You'd think, for example, that a quality expert would favor 100% inspection. In fact, Deming would argue, it often makes no more sense than a shopper's opening every package in the supermarket before buying. If the production system is good enough, mass inspection is likely to be a waste of time. Similarly, to rely on a quality-control department is to tell workers, indirectly, that high quality isn't their job. Quality has to be built in, not inspected in.”
I love Deming's analogy. If quality is good enough, you don't have to inspect everything. Sadly, I've learned from experience with one of my local gourmet grocery stores that I *do* have to often inspect packages of fruit or cheese to check for mold. But, I don't open every box of cereal nor do I test their meat for e. coli.
In the Inc. article… the writer paints a picture of Deming as being influential, but flawed.
“For all his newfound popularity, though, Deming's impact has been curiously limited, partly because of his own communication problems. His manner can be inscrutable, even off-putting — “insulting more than enlightening,” one would-be client described it. He has a propensity for overblown imagery, referring, for example, to “the seven deadly diseases” of management.”
I guess Dr. Deming wasn't trying to be liked. But, it raises important questions about how we bring up issues and concerns as change agents (inside an organization or as outsiders).
Again from Inc.:
“And he speaks in the broadest of generalities. “When we were through watching the tapes, we thought, ‘Great philosophy . . . but what do we do?” a small-company chief executive officer who sampled the videocourse told INC. a couple of years ago.”
Jack Welch, former CEO of GE, said a similar thing in one of this books, as I blogged about.
I thought many of Deming's recommendations were quite specific… such as ending the annual performance appraisal. But, that wasn't something Welch was going to really consider. I think Deming was pretty specific… but saying Deming was too vague could be a handy excuse for not trying his radical ideas?
Another excerpt:
“To Deming, high quality can't be inspected in, added on, coerced, demanded, or achieved through exhortation (“Quality is everyone's responsibility!“). Rather, high-quality goods and services are the natural products of an organization that's working right. To oversimplify only a little, “working right” means identifying problems, then encouraging everyone involved — workers, managers, suppliers, whomever — to help solve them.”
Ah, now I remember how I found this article. I saw somebody quote Deming as saying, un-ironically, that “quality is everyone's responsibility.” My impression is that Deming mocked such slogans and posters.
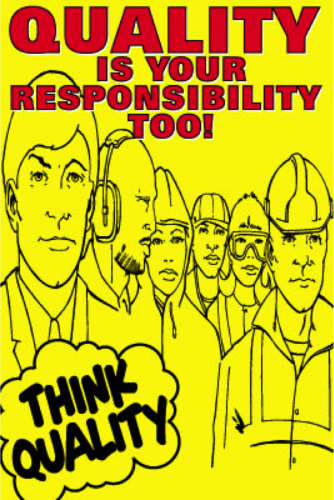
It's the type of saying he would have said “hogwash!” about. Deming said and wrote that quality starts in the boardroom. Yes, everybody plays a role, but as the Red Bead experiment teaches us, quality is most the product of the system. The workers and front-line staff don't design the system — management does.
Everybody should be involved… but everybody is not equally responsible for quality. I think that's the main takeaway.
Saying “quality is everybody's responsibility” makes it too easy for management to think they have delegated quality to their employees or that they are magically empowered. Leaders must play a role.
Anyway, there's a lot of wisdom in the article, including discussion about the need to understand variation… and to ask ourselves if judging employees is fair if their performance is within the ranges of normal variation.
As always, provocative and relevant stuff, even 28 years later.
Please scroll down (or click) to post a comment. Connect with me on LinkedIn.
Let’s work together to build a culture of continuous improvement and psychological safety. If you're a leader looking to create lasting change—not just projects—I help organizations:
- Engage people at all levels in sustainable improvement
- Shift from fear of mistakes to learning from them
- Apply Lean thinking in practical, people-centered ways
Interested in coaching or a keynote talk? Let’s start a conversation.
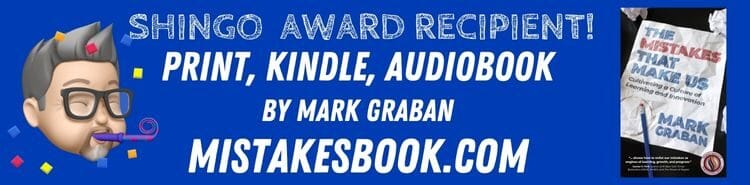
Another timely throwback, Mark. Thanks for sharing.