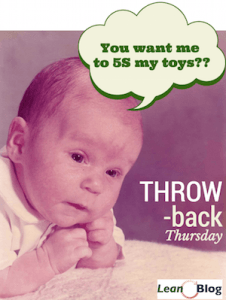
It's time for another Throwback Thursday where I revisit a blog post from the past. To the left, that's a baby Mark Graban… probably not actually thinking about Lean.
I referenced this post in my recent Keith Olber-Lean parody video… the post goes all the way back to 2007, the early days of Lean Blog:
“Bad Lean/5S Hits the UK Media“
It's not the only “bad 5S” story that I've featured here, situations that are arguably L.A.M.E. (Lean As Misguidedly Executed) because the use of 5S in those office settings only annoyed the employees while adding no value to customers (and not even preventing any waste).
Lean is not about banning bananas from people's desks or banning sweaters hanging on chairs.
We should be solving problems that matter, for customers and employees, through Lean. We should be engaging people rather than throwing silly top-down mandates at them.
I tend to get on a soapbox and rant about the “bad office 5S” examples… but I got an email this week that made me smile, because it helped an organization avoid the L.A.M.E. office 5S trap.
Hear Mark read this post (subscribe to the podcast):
The email, shared with permission:
I worked for a company that was very focused on implementing Lean concepts into all areas of the business, and that eventually grew to include support functions in the office area.
When management gave the directive to implement concepts like 5S into our work, some well-intentioned people in the office took this quite literally, and I was part of discussions deciding things like:
- Should external monitors be on the back right or left of each cubicle?
- How many pens or pencils were ok to keep out on your desk at a given time?
- Should we standardize desk calendars, or allow people to choose their own?
- Should we leave room for a personal item, like a picture frame?
As luck would have it, I had recently discovered your blog, and a post around that same time on the topic of office 5S caught my eye . This was shared around the group, and we all agreed that we were on the verge of stepping into the realm of LAME: “Lean” As Misguidedly Executed. Our attempts to 5S were based on the tool, as opposed to the principles behind 5S.
Circulating the blog post led to a lot of questions. In an office where everyone used the same desk every day (people rarely changed seats), would standardizing the placement of monitors have any real impact on quality or productivity? None that we could see. And removing personal items from the desk? Not exactly respectful of people, in our opinion.
Instead of directly copying the version of 5S that had worked so well in the manufacturing area of the business, we started asking questions about what areas of our work would benefit from 5S. This eventually led to several positive changes: how we name and manage files on the server, how emails are handled by the team, and an aggressive redesign of common areas like the supply cabinet and copier areas.
As with many other Lean tools, the transition from manufacturing to service/office work means the tools may change, but the same principles still apply.
I'm glad they came to that realization for focused on the key question of “what problem are you solving?” (as John Shook advocates) or “how are you better serving the customers and employees?” instead of just blindly copying a tool.
Removing personal items from the desk? Not exactly respectful of people, in our opinion. Share on XBad office 5S implementations helped inspire this video that I created, which now has almost 150,000 views on YouTube:
Be Lean, not L.A.M.E.! Have you had any near misses with bad office 5S or near-L.A.M.E. that you avoided or quickly changed?
What do you think? Please scroll down (or click) to post a comment. Or please share the post with your thoughts on LinkedIn – and follow me or connect with me there.
Did you like this post? Make sure you don't miss a post or podcast — Subscribe to get notified about posts via email daily or weekly.
Check out my latest book, The Mistakes That Make Us: Cultivating a Culture of Learning and Innovation: