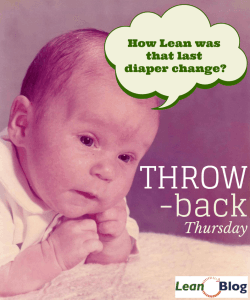
Episode #403 of the public radio program “This American Life” originally aired in 2010, telling the story of the NUMMI plant that was a joint venture between GM and Toyota (it's now where they build Teslas). As a joint venture, that meant the closed-down GM Fremont plant was re-opened to be managed under the Toyota Production System.
The This American Life story asks why GM didn't learn more of the lessons from NUMMI. Well, GM did learn many lessons, but it wasn't enough to save the company from bankruptcy (going from 50% market share to just over 20% will do that, regardless of how Lean your factories are, when you have more retirees than active employees).
The story re-aired on NPR stations last weekend, which I learned of when many of you emailed me or tweeted at me about the program… and even some of my personal Facebook friends who don't share my passion for Lean shared the link with me.
What makes it a throwback, in a way, is that I first blogged about the episode in 2010 in this post: NPR on the “End of the Line” at NUMMI and My Story About an Interviewee.
You can listen to the This American Life story using the player below or read the transcript.
Also floating around the Twitterverse was a link to a blog post from the “Labor Notes” website that was critical of the This American Life episode. I tried unsuccessfully to create an account that would allow me to comment (technical glitches on their side, it seemed), so I'll share my thoughts below.
Many conservatives complain that NPR is part of the “liberal media,” but Labor Notes apparently views This American Life as part of some vast corporate right-wing conspiracy.
Labor Notes has often lashed out about Lean, as I blogged about here (see more posts). They are usually either just complaining about management (if Lean is an idea from management types, it must be evil) or they're complaining about bad practices that aren't really Lean (and I'd line up with them to complain about L.A.M.E. stuff that happens… although they said once that LAME should mean Lean As Mainly Experienced… touché).
From their recent post:
Trouble is, the “team concept” program of standardization, deskilling, and continuous speedup wasn't such a boon for workers as the show portrays–neither the imported version, nor even the original in Japan. Mike Parker wrote books and articles on the Toyota Production System–dubbed “management-by-stress”–as it was coming to dominance in the '80s and '90s.
Ah, the scare quotes around “team concept.” Asking people to work in teams, or the idea of management being part of a team with workers… it must be a trap! Ah, it reminds me of this Star Wars internet meme:
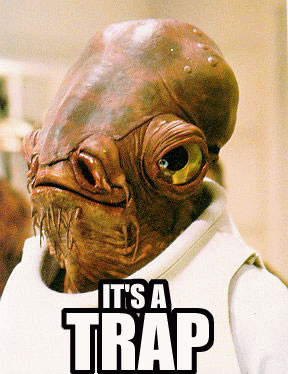
Labor Notes complains about “deskilling” of work, when a Lean auto factory actually does a lot of cross training so that employees have MORE skills.
Speeding up the line, management by stress — those sound like the concepts of the OLD General Motors management system, pre-Lean. I was around for some of that era 20 years ago, before we got a new plant manager — Larry Spiegel, quoted in the This American Life piece.
When Larry was asked about the difficulty he faced in bringing the NUMMI/Toyota/Lean approach to another factory, this was the exchange:
Frank Langfitt
For this workforce, there were no trips to Japan, no tearful sushi parties. And from the start, workers were skeptical.
Larry Spiegel
The lack of receptiveness to change was so deep.
Frank Langfitt
Larry Spiegel was another NUMMI commando. He moved down to Van Nuys to help launch the Japanese system there.
Larry Spiegel
There were too many people convinced that they didn't need to have to change.
Frank Langfitt
Hadn't General Motors threatened to close the plant?
Larry Spiegel
They didn't believe them.
Frank Langfitt
Why?
Larry Spiegel
It's not logical. They just didn't.
Frank Langfitt
This was one of the biggest differences between Fremont and Van Nuys. Van Nuys hadn't been shut down [Mark's note: As NUMMI had been when it was a failed GM plant]. Turns out it's a lot easier to get workers to change if they've lost their jobs, and then you offer them back. Without that, many union members just saw the Toyota system as a threat.
And they had a point. Under the Japanese system, Van Nuys stood to lose a fourth of its workforce, because the more efficient a plant becomes, the fewer workers it needs. And just as bad, the team concept hurt their seniority rights. This had been a problem for union members back at NUMMI also.
In my experience, Lean transformations do NOT require the threat of closure. In healthcare, organizations like ThedaCare and Virginia Mason Medical Center have transformed themselves without having some sort of crisis like that.
Now, the threat of not needing 25% of your employees anymore. I can totally understand why the UAW and the Van Nuys plant wouldn't like that. What's not explored in the story is if GM would have made any “no layoffs due to Lean” commitments as many organizations do. Would GM have re-trained or redeployed workers in a way that was more constructive than the infamous Jobs Bank? Would GM have tried to grow the plant's business, so they could avoid firing employees?
It's hard to see how you could blame employees for not liking something that might cost them their jobs.
Labor Notes also criticizes This American Life and Spiegel for “blaming workers.” I always thought that “militant” attitudes from employees or unions were the result of bad management.
Larry Spiegel, in my experience with him, was a great leader. A truly Lean leader who had the courage to do things a new way at my GM plant.
What I tried to write on the Labor Notes site:
——–
Larry Spiegel was the GM plant manager who was quoted in the story. I worked at GM from 1995 to 1997 as an engineer at the Livonia Engine Plant and Larry was brought in as our plant manager in 1996 after a number of major quality problems. Under the old plant manager and his regime, the workers were blamed and it was extremely unfair. Bad managers literally got in the way of UAW members putting quality first.
When Larry became the plant manager, he addressed an all-hands meeting of hourly and salaried employees and he told them that the days of blaming the workers were over. The problem wasn't the workers — the problem was the old management style. Larry made that quite clear and lived by his desire to manage in a new way, putting quality first, and listening to the workers.
The factory made a lot of progress under his leadership.
I work today in healthcare. The problem there, also, is the management system,not the workers. That's why the application of Lean and the Toyota Production System works so well. The new management style allows people to put quality and patient safety first. Managers actually listen to their employees… it's nothing to complain about.
——–
But, then again, Labor Notes complains about Lean healthcare as if it's as evil as they think Lean manufacturing is.
GM's history is complicated. I was never one to blame the union for the company's problems. I blamed leadership (or a lack thereof, as I wrote about here and here).
I don't demonize the union. I wish the union folks wouldn't demonize Lean.
What do you think? Please scroll down (or click) to post a comment. Or please share the post with your thoughts on LinkedIn – and follow me or connect with me there.
Did you like this post? Make sure you don't miss a post or podcast — Subscribe to get notified about posts via email daily or weekly.
Check out my latest book, The Mistakes That Make Us: Cultivating a Culture of Learning and Innovation:
[…] an article from “Labor Notes” (a union publication that I’ve sparred with before): “Allina Nurses Go All […]