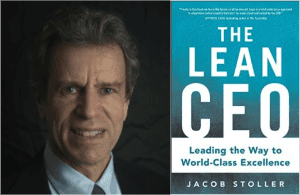
My guest for episode #221 is Jacob Stoller, author of a book that was just released: The Lean CEO: Leading the Way to World-Class Excellence. It's available now through Amazon or you can learn more through his book's website. As Jacob explains, he's a journalist, not a Lean practitioner, and he interviewed CEOs across different industries to get their thoughts on Lean management.
In this podcast episode, Jacob Stoller, author of The Lean CEO, discusses his insights from interviewing various CEOs across industries about their experiences with Lean management. He highlights how CEOs define Lean differently based on their company's needs but shares that common principles, such as respect for people and the importance of culture, are universal. Stoller also touches on the challenges CEOs face in adopting Lean, especially when traditional business practices and MBA thinking clash with Lean principles. He underscores the role of leadership humility, continuous learning, and creating a culture of engagement as crucial elements for successful and sustainable Lean transformations.
Streaming Player (run time 38:22):
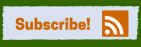
We also discuss topics including how CEOs get exposed to Lean thinking, why humility is so important, what “respect for people” means in the Lean context, and reasons why more CEOs don't embrace Lean. Did Six Sigma and Dr. Deming come up in his interviews? You'll also hear a bit about Bob Brody, the CEO at Franciscan St. Francis Health, which was featured in my Healthcare Kaizen books (learn more about visiting Franciscan this April).
Read Jacob's bio and blog.
You can also read some “CEO Insights” including two of my favorite healthcare CEOs:
“These principles and practices we've established are a way out from the cynicism, from the overworking, from the overburden, from the massive waste that exists in the delivery of healthcare. As we expose managers, leaders, CEOs, senior executives to this by having them come and actually see it in action, they absolutely get it, they absolutely say this is the way we should be working and this is what we should be doing.”
John Toussaint, CEO, Thedacare
And:
“Lean is one of the most advanced people systems in the world for getting people to realize their capabilities in terms of coming to work every day to do their jobs and to improve their jobs.”
Gary Kaplan, CEO, Virginia Mason Medical Center
For a link to this episode, refer people to www.leanblog.org/221.
For earlier episodes of my podcast, visit the main Podcast page, which includes information on how to subscribe via RSS or via Apple Podcasts. You can also subscribe and listen via Stitcher.
Questions and Topics:
- Can you share your background and what led to writing The Lean CEO?
- How do CEOs define Lean, and is there consistency in their definitions?
- What role does respect for people and culture play in Lean adoption?
- How were CEOs initially exposed to Lean, and what challenges did they face?
- How does Lean challenge conventional business school thinking and “common sense”?
- What impact does Lean have on organizational structures and systems?
- Can you share any surprising findings from your interviews with Lean CEOs?
- How do Lean CEOs balance long-term results with short-term business pressures?
- What role does humility play in Lean leadership, and how do CEOs maintain it?
- Did Dr. Deming or Six Sigma come up in your discussions with Lean CEOs?
- What barriers prevent more CEOs from adopting Lean, and how can they be addressed?
- What are your reflections on Bob Brody's Lean journey at Franciscan St. Francis Health?
- How do Lean practices in healthcare differ from other industries, particularly in Japan?
- What common traits do successful Lean CEOs share, despite their diverse personalities and industries?
Automated Transcript:
Mark Graban:
Welcome to episode 221 of the podcast for April 8, 2015. My guest today is Jacob Stoller, author of The Lean CEO: Leading the Way to World-Class Excellence, which is now available on Amazon. Jacob is a journalist, not a Lean practitioner, but he interviewed many CEOs from various industries to capture their thoughts on Lean management. In this episode, we'll discuss how CEOs get exposed to Lean, why more don't embrace it, the importance of humility, and the meaning of “respect for people” in a Lean context. We'll also talk about Bob Brody, the CEO of Franciscan St. Francis Health, who was featured in my Healthcare Kaizen books. For more information on Jacob's book and related resources, visit leanblog.org/221.
Jacob, thanks so much for joining us today.
Jacob Stoller:
It's great to be here, Mark.
Mark Graban:
I'm excited about your new book, The Lean CEO. Could you tell us a bit about your background and what led you to write this book?
Jacob Stoller:
Sure. Unlike most of the people you talk to, I'm not a Lean practitioner. I'm more of a journalist and facilitator. I've worked across various fields like IT, accounting, and engineering, and in recent years, I've focused on Lean. I'm particularly interested in the role of CEOs, as they are responsible for communicating Lean to stakeholders like shareholders and unions. CEOs also serve as spokespersons for Lean, helping explain it in terms outsiders can understand.
Mark Graban:
When you spoke to CEOs, did you find a consistent way they defined Lean, or was there variation?
Jacob Stoller:
There was a lot of variation. CEOs tend to define Lean based on the problems they're trying to solve, so it often takes different directions depending on the company. However, a shared belief in “respect for people” was universal. CEOs believe in trusting and empowering their employees, which is crucial for success.
Mark Graban:
It's encouraging to hear that culture and respect for people are at the forefront. I might expect CEOs to focus more on hard measures like cash flow and inventory, but it sounds like culture plays a major role. Can you expand on that and share some examples of CEOs you talked to?
Jacob Stoller:
Definitely. There were several in healthcare, like John Toussaint, Gary Kaplan, and Bob Brody. They emphasize breaking down physician-centric cultures and promoting collaboration. In manufacturing, people like Art Byrne had immense trust in the front-line workers from the start. The common theme was fostering a collaborative and trusting culture, regardless of industry.
Mark Graban:
I'd like to circle back to Bob Brody later, but first, you mention in your book that Lean is a different way of thinking. How were CEOs initially exposed to Lean, and what challenges did they face?
Jacob Stoller:
Many CEOs heard about Lean through different avenues, sometimes from other CEOs or their boards. Some even “shopped” for a different operating system. The challenge isn't just understanding Lean, but getting the whole organization on board. CEOs must change compensation plans, reporting structures, and accounting mechanisms, which is a lot to manage.
Mark Graban:
That's a big shift. You mentioned earlier about slowing down equipment. Is that related to matching production to customer demand rather than overproducing?
Jacob Stoller:
Exactly. The idea is to match production to demand. Overproduction might reduce costs from a traditional accounting perspective, but Lean challenges that by focusing on customer needs and eliminating waste.
Mark Graban:
That's a key point. In the book, you talk about leadership humility. How does humility manifest in these Lean CEOs, and how does it impact their leadership style?
Jacob Stoller:
It's less about personality and more about beliefs. These CEOs understand that they don't know everything–similar to Deming's philosophy of intellectual humility. They're willing to learn, listen, and challenge their own assumptions. This willingness to be wrong and learn from the shop floor is a common thread.
Mark Graban:
Did Dr. Deming or Six Sigma come up in your discussions with the CEOs?
Jacob Stoller:
Deming came up, especially with Bob Brody, who was part of Deming discussion groups in the '90s. However, Six Sigma didn't come up as much as I expected, which surprised me. I didn't prompt for it, but CEOs tended to focus on Lean without diving into Six Sigma.
Mark Graban:
You spent a lot of time talking to CEOs who “get it.” Did they have thoughts on why more CEOs aren't adopting Lean, and what barriers exist?
Jacob Stoller:
Many CEOs aren't aware of Lean or don't understand it fully. There's also resistance, even among those who seem interested. CEOs might visit Lean plants, get excited, but then not take action. Some Lean CEOs admitted they wouldn't have fully embraced Lean without a burning platform, like financial crises.
Mark Graban:
That's an important insight. Looking at the long-term benefits, how do Lean CEOs articulate the value they're creating for their companies, shareholders, and customers?
Jacob Stoller:
The results are often spectacular, but many CEOs are humble about it. They might say, “Oh, by the way, we multiplied our revenue by 500%.” It's clear that Lean drives financial success, but for these CEOs, it's part of a larger commitment to culture, respect for people, and long-term value.
Mark Graban:
I want to bring the conversation back to healthcare and Bob Brody at Franciscan St. Francis. What are your reflections on his approach to Lean?
Jacob Stoller:
Bob's approach contrasts with John Toussaint and Gary Kaplan. He took a more evolutionary, patient approach, working closely with Joe Swartz to enable change rather than pushing aggressively. However, he mentioned that financial pressures may require him to be less patient moving forward.
Mark Graban:
It sounds like Franciscan's approach has focused heavily on staff engagement and continuous improvement, which is a bit different from the more aggressive Lean transformations at ThedaCare and Virginia Mason. Is that accurate?
Jacob Stoller:
Yes, and Bob mentioned that they had been practicing Deming's ideas long before Lean became a term. It's been a gradual, long-term evolution for them.
Mark Graban:
In Japan, hospitals talk more about total quality management (TQM) than Lean. They never stopped doing TQM and now incorporate Lean to improve cycle times. It's a different approach than in the U.S., where TQM often faded away. There's always a lot to learn from different approaches.
Jacob Stoller:
Lean is flexible and accommodates different approaches and personalities, which is one of its strengths.
Mark Graban:
Exactly. There's room for CEOs to adopt Lean in ways that fit their own leadership styles, rather than following a set mold. Jacob, thank you for taking the time to talk. I've enjoyed our conversation, and I know listeners will be excited to check out The Lean CEO. Where can people find more information?
Jacob Stoller:
The best place is my website, jacobstoller.com, where you can find links to purchase the book on Amazon and other resources. The book officially launches on April 10th, published by McGraw Hill.
Mark Graban:
Thanks again, Jacob. I hope we can talk again sometime.
Jacob Stoller:
Thank you, Mark. I'd love to.
Feedback & Comments:
If you have feedback on the podcast, or any questions for me or my guests, you can email me at leanpodcast@gmail.com or you can call and leave a voicemail by calling the “Lean Line” at (817) 372-5682 or contact me via Skype id “mgraban”. Please give your location and your first name. Any comments (email or voicemail) might be used in follow ups to the podcast.
Please scroll down (or click) to post a comment. Connect with me on LinkedIn.
Let’s work together to build a culture of continuous improvement and psychological safety. If you're a leader looking to create lasting change—not just projects—I help organizations:
- Engage people at all levels in sustainable improvement
- Shift from fear of mistakes to learning from them
- Apply Lean thinking in practical, people-centered ways
Interested in coaching or a keynote talk? Let’s start a conversation.
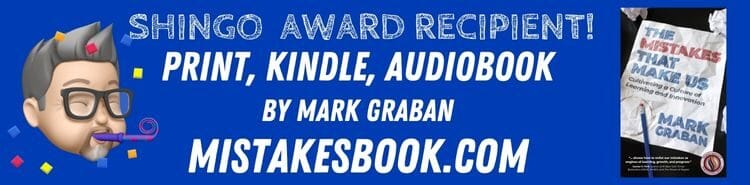
[…] https://www.leanblog.org/2015/04/podcast-221-jacob-stoller-the-lean-ceo/ […]
Great interview Mark! I really enjoyed the discussion about how CEO’s were exposed to lean. Awesome episode!
[…] year, you might have heard my podcast episode with author Jacob Stoller, talking about his book The Lean […]