It's time for another “Throwback Thursday” post, which is, as always, accompanied by one of my thoughtful-looking baby pictures :-)
Back in 2002, back when I worked for a software startup, Factory Logic, I was able to sit in on some Lean training that was created and presented by a large electronics manufacturer that will remain unnamed (and it wasn't Dell). The class was for the company's suppliers, primarily.
An Unhappy Supplier
I recently found the training guidebook and was flipping through it. On the inside cover, I found this story that I had written down after talking with one of the suppliers in attendance… in the words of the supplier:
“[Company] wanted us to produce all we could. They told us to produce without a purchase order. “Trust us,” they said.
Well, the downturn (after 9/11) hit, and we got stuck with the inventory. Now, we're here in this class being lectured that inventory is bad.”
He wasn't a happy supplier… and I couldn't blame him. The company's practices (the customer in this relationship) didn't seem grounded on mutual respect.
Toyota has long had a reputation in the auto industry, well earned it seems, for being fair and collaborative with their suppliers. One of our Factory Logic customers was an auto supplier that made similar parts for GM, Chrysler, and Toyota.
Listen to Mark read this post (and subscribe to the series):
That supplier LOVED working with Toyota because Toyota had level loaded and STABLE production schedules. Whereas GM and Chrysler would jerk the supplier around by changing their schedules at the last minute, meaning that the supplier had to change what they were producing or shipping. The supplier had to hold MORE inventory of finished product for GM and Chrysler in order to meet their whims and changing schedules, compared to what they held for Toyota.
It was LESS expensive for that supplier to do business with Toyota, due to the stability and the lessened need for inventory.
Toyota is still a “preferred” OEM customer today, looking at this survey of suppliers from 2014:
From the study, what makes a preferred customer?
The variables comprise five components of the Working Relations Index®that cover quality of the overall supplier relationship, communication, help given the supplier, working together, and supplier profit opportunity.
The second set of factors includes foundational business areas involving leadership, execution and fairness. These factors must be present to achieve good relations, but do not themselves impact the WRI® rating. Foundational areas include such things as paying invoices on time, resolving payment issues fairly, allowing suppliers to recover some material cost increases, and OEM terms and conditions regarding intellectual property.
What's the lesson for hospitals, especially large major health systems? Be fair to your vendors and suppliers. That's the Lean thing to do… not just because it's nice, but because it's good business.
Kaizen Tips
A large portion of the training was on technical methods as opposed to management systems, philosophy, culture, and developing people (the things Toyota leaders also include).
The electronics supplier had a ton of material on technical methods like 5S, visual management, just-in-time, error proofing, and kanban systems.
To their credit, the section on Kaizen covered MORE than just “Kaizen Events.”
Here's one slide on “Kaizen Rules” – in a mnemonic called “RULES KAIZEN.”
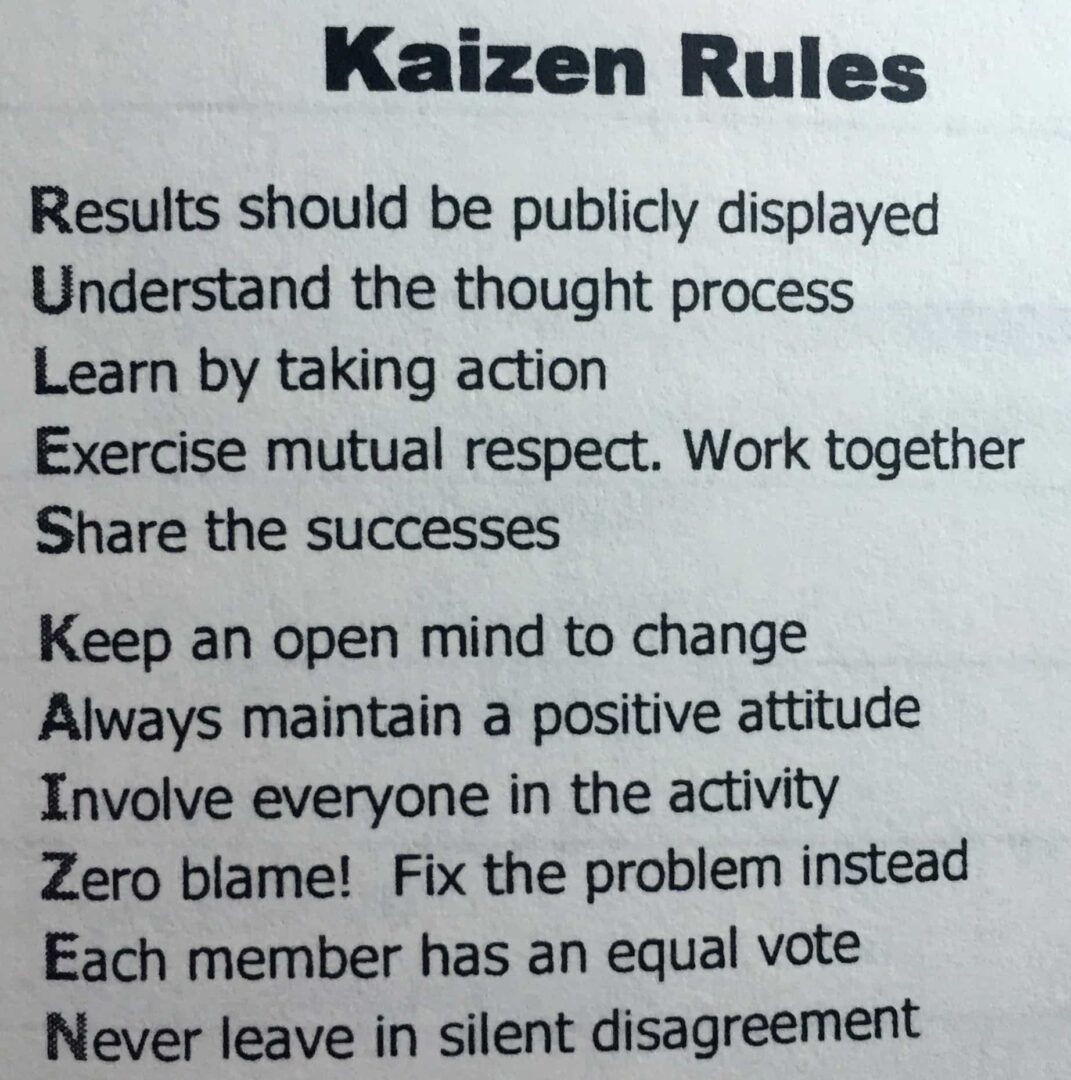
I'm on board with nine of those ten rules.
The one I'm not sure about is “Each member has an equal vote.” I don't think of Kaizen (or Lean) as a democracy-driven workplace where people vote on what to do. It's certainly not a top-down dictatorship, either. Nor is it the UN Security Council where any one member gets a veto.
In my mind, PDSA is about TESTING ideas. What works in practice? We should be driven by data and results where we can, not opinions. That's what concerns me about workplace voting… on what basis are people voting?
If we have a proposed new method, we should be able to determine if it's working better than the old way (including giving “seven days' grace” as I recently blogged about). Sometimes, the manager might have to make a decision about what's best, but doing so after getting input from employees and then explaining WHY things have to be done (and not because “I said so”).
But, I think organizations, including health systems, would be better off by following those rules and building upon them. What Kaizen rules would you add? Please leave a comment.
What do you think? Please scroll down (or click) to post a comment. Or please share the post with your thoughts on LinkedIn – and follow me or connect with me there.
Did you like this post? Make sure you don't miss a post or podcast — Subscribe to get notified about posts via email daily or weekly.
Check out my latest book, The Mistakes That Make Us: Cultivating a Culture of Learning and Innovation:
I think that maybe the “Each member has an equal vote” could be something like: “Each member’s ideas should be heard and respected” or “Everyone is responsible for improvement efforts”
Not much to add though.
Yeah, as it says, “involve everyone.”
I agree that “everyone has a voice” or the way you stated it, about being heard and respected, is a better way to say it than “vote.”
Toyota and lean manufacturing, they have such a close relation. A reason I presume Toyota has a stable production schedule in contrast to the other companies like GM or Chrysler.