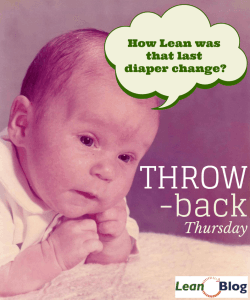
Last weekend, at a patient safety conference, I heard a physician talk about “robust process improvement” and this, thankfully, included an endorsement of Lean methods.
That's the good news.
The bad news was that the physician who was presenting trotted out what appeared to be a tired and incorrect framing of Lean and Six Sigma, as shown in the picture below (this conference used the widest widescreen slide format I've ever seen, by the way):
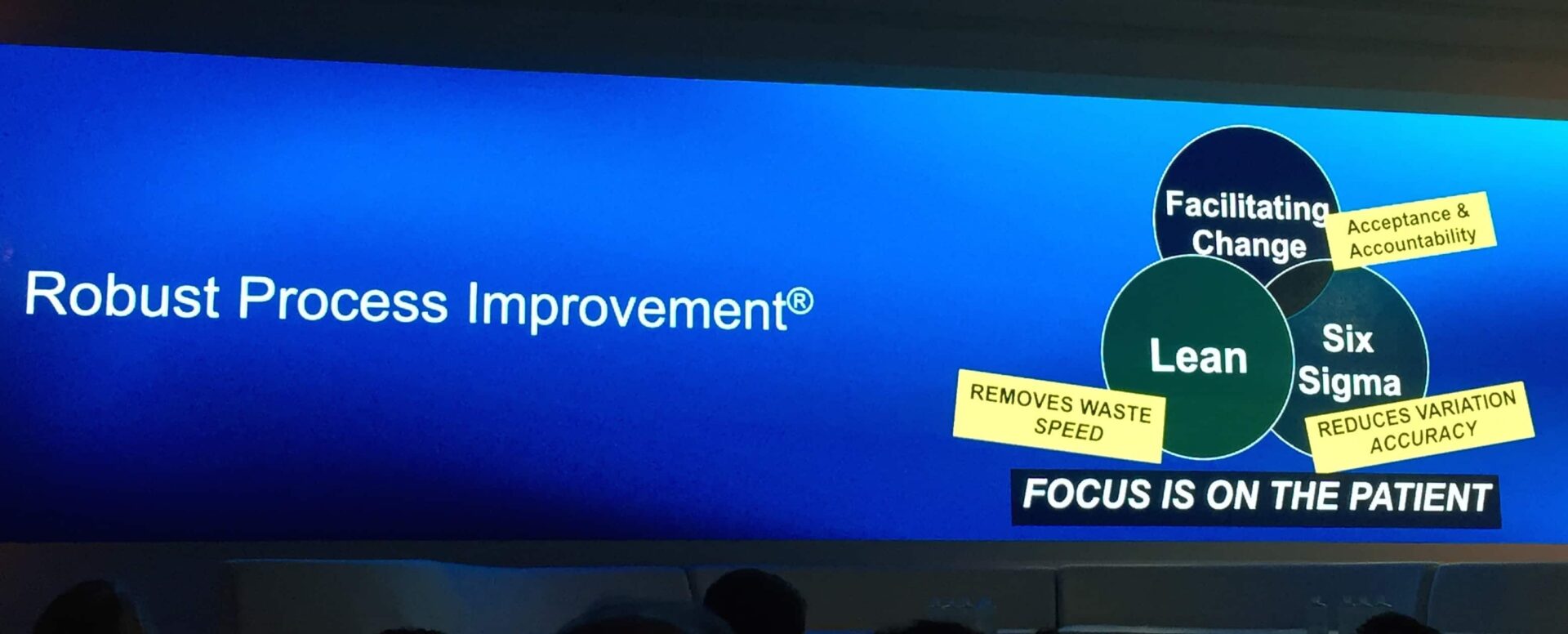
It's an example of Lean As Mistakenly Explained (or a form of L.A.M.E.), where Lean is “about waste and speed” and “you need Six Sigma for quality.”
Ugh.
Listen to Mark read this post and the original (learn more and subscribe):
So that brings me to a post I wrote in 2011, today's Throwback Thursday. I wrote the post in 2011 and I don't need to write it all again. That post was titled:
“Dear “Lean Six Sigma” Crowd – Lean is About Quality, Too“
Lean is not about “making bad stuff faster” if Six Sigma is not involved. Remember this video I posted last year?
It's ironic that the speaker talks about “confusion.” He's horribly confused. He probably still is.
I'm going to politely and respectfully reach out to the Joint Commission presenter and try to convince her that Lean is about both quality and flow… just ask Toyota.
Also check out this good piece by Nicolas Ruhmann on LinkedIn: “Lean Six Sigma Could Blind You.”
We'll have to keep working to clear up these misunderstandings.
What do you think? Please scroll down (or click) to post a comment. Or please share the post with your thoughts on LinkedIn – and follow me or connect with me there.
Did you like this post? Make sure you don't miss a post or podcast — Subscribe to get notified about posts via email daily or weekly.
Check out my latest book, The Mistakes That Make Us: Cultivating a Culture of Learning and Innovation:
Thanks, Mark. We get asked this all the time. Our client base (lawyers) likes definitions. Given the type of work our clients do, we rely more heavily on Lean than Six Sigma (just try talking to lawyers about statistics). It’s just a better fit. BUT we always stress the quality aspects of both Lean and Six Sigma approaches. If you remove waste (defects and rework) from a process, you’ll be delivering a better product and meeting client needs more effectively. Lawyers have to deliver a quality product. It would be completely useless for them to produce anything but quality advice for their clients. We use Lean tools to help them discover how they can deliver even better quality at less cost to them and their clients and reduced pressure on themselves. As Karen Martin put it recently, easier and more profitable are not mutually exclusive!
Hi Mark – As a teacher, I dislike it when people who are taught how to go get the facts (do research) do not bother to go get the facts. A little research on the early writings about TPS would take the Lean Six Sigma people to the work of Yasuhiro Monden, who was the first to write about TPS at length, including conversations with Taichi Ohno to clarify key points about TPS.
Professor Monden said in his book, Toyota Production System (first edition, 1983, page 2 – see http://www.bobemiliani.com/yasuhiro-monden/):
“…although cost-reduction is the system’s most important goal, it must achieve three other sub-goals in order to achieve its primary objective. They include:
1. Quantity control, which enables the system to adapt to daily and monthly fluctuations in demand in terms of quantities and variety;
2. Quality assurance, which assures that each process will supply only good units to subsequent processes;
3. Respect-for-humanity, which must be cultivated while the system utilizes the human resources to obtain its cost objectives.
It should be emphasized here that these three goals cannot exist independently or be achieved independently without influencing each other or the primary goal of cost reduction. It is a special feature of the Toyota production system that the primary goal cannot be achieved without realization of the subgoals and vice versa. All goals are outputs of the same system; with productivity as the ultimate purpose and guiding concept, the Toyota production system strives to realize each of the goals for which it has been designed.”
Lean Six Sigma is like saying “TPS Quality” or “Lean Quality.” It does not make sense. Most people don;t do Lean right. Adding six sigma complicates matters and causes confusion, and thus creates waste.
Also, note that “Respect for Humanity” was identified as a required sub-goal, for which the Lean community began paying serious attention to only recently (ca 2007).
Hi Bob, I agree with your concern that often “people who are taught how to go get the facts (do research) do not bother to go get the facts”.
Two quick thoughts on this:
1) Are people _really_ taught to do research (to get the facts and critically analyse what they read)?
2) You rightly suggest that people should read a high quality book to learn about a topic of interest. But how can we keep these books relevant in an age when some people think they are experts on a topic after five minutes on google?
If people think “they are experts on a topic after five minutes on google” or “experts after some Yellow Belt class,” then that’s not the fault of books…
Those who say, “Lean…. oh right, that stuff’s easy” are they ones with the least knowledge or experience with Lean.
Hi Mark, from reading your blog it is obvious that you are operating with a broad definition of Lean (can’t recall any other lean-specific blogs with a reference to quality control charts). What I have seen a lot of is Lean being branded as an alternative where quantitative skills are not really needed; this of course gets compounded over time because it attracts individuals without the robust quantitative skills that sometimes _are_ needed. Might this be the reason that quality is seen as something separate to Lean (as often practiced)?
I think you mentioned it on another page, that walking into Toyota we would not see much in terms of quantitative tools being used. That of course does not preclude their knowledge of such tools, however, it can lead an external observer to make erroneous assumptions. How much do you think this difference, between what is visible and what is not, adds to the misconceptions?
Hi – I’m not sure I’d call a control chart “part of Lean” per se, but it is a method that Toyota uses in the plants. I’m not sure if it matters to say control charts are part of Lean or complementary to Lean. Either way, they are useful (powerful, even).
Control charts pre-date TQM even. Even my GM plant, circa 1995, used control charts (sometimes badly) before they embraced Lean.
At the Toyota plant here in San Antonio, they make it clear (when asked) that they don’t do “Six Sigma.” They don’t train belts and don’t have a formal program.
They teach every employee the “7 basic QI tools” – including control charts. They use statistical methods, when helpful, and of course have some employees with deeper, more specialized statistical training (this was true at other automakers, of course).
Many visitors to Toyota make “erroneous assumptions” and that’s been happening for decades.
“They use statistical methods, when helpful”
Perhaps that “when helpful” is the sticking point then. Common practice seems quite polarised between “always” and “never”.
In your experience, why do you think that is?
* The sense of certainty (“when helpful” is a bit ambiguous)?
* The aptitudes of those involved?
* How people were taught?
* All of the above?
* Any other reasons?
I don’t know. I can’t speak for others really. I think many people are intimidated or uncomfortable with statistics or they’re not exposed to those quantitative or statistical QI methods. It’s easier and more comfortable to fall back on less quantitative methods like 5 Whys or Fishbone Diagrams?
Lean shouldn’t be a measurement-free or data-free zone. Nor should numbers drive everything we do. I guess that real world balance is the hard thing to figure out. People want easy answers.
Why do you think there’s an underuse or lack of appreciation for these methods?
As far as underuse and lack of appreciation go, I think it’s exactly as you say, many people are uncomfortable with statistics; they subsequently opt-out of being exposed to the methods.
Conversely, I have read of many cases in six sigma land where there is an overuse and excessive faith in quantitative methods, resulting in analysis paralysis or GIGO (Garbage In Gospel Out).
As you pointed out, getting the “real world balance” right is the challenge and it’s not as easy as just packaging Lean and Six Sigma together.
In my opinion,Lean 6Sigma may not be a routinely used problem solving technique in Lean Healthcare or in any other Lean Process Improvement environments as much as we use Ishikova Diagram or a 5 Why Technique.
However,wehen we are tackling very complex problems with innumarable number of minute inputs causing uneffordable output errors such as wrong site surgeries,surgical site infections or reduction of mortality rates in Healthcare,we may have to resort to high level statistical techniques.
I have also come across usage of Taguchi Techniquses to solve certain complex design problems which are expensive while implementing lean solutions in some design and Manufacturing setups
Hi – Your comment is confusing. Are you saying that “Six Sigma may not be a routinely used problem solving technique?” It’s very confusing to say that “Lean 6Sigma” is a part of Lean.
Lean and Six Sigma are two different methodologies, with some overlap.
I agree that Six Sigma statistical methods can be helpful in solving certain types of complex problems or those that are particularly difficult to solve.
I fully agree with Mark that 6 Sigma and Lean are two different methodologies.
My intention was to mention that 6 Sigma may not be a routinely used methodology to solve day to day problems in Lean Healthcare or in other areas when trying to find Lean Solutions.
I am doubtful weather 6Sigma existed at the time Toyota was developing TPS using simple problem solving techniques to solve their day to day Production problems with a core philosophy of Continuous Improvement,which was later termed as Lean Manufacturing.
Correct, Six Sigma did not exist “back in the day” when Toyota was developing TPS. But, Toyota is a company than continues to evolve in many ways and they certainly could choose to embrace formal Six Sigma… but they have not.