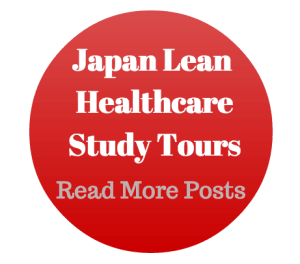
Last week, I wrote a post (part 1) looking back at our visit to the Toyota Tsutsumi factory that was part of our Japan tour that took place two months ago now. See previous posts in this series. I'm going to try to do one post a week on this topic. If you're in San Francisco, I'm giving a talk on Wednesday night about Lean, Japan, and ideas traveling back and forth across the Pacific.
The Importance of Breaks
Healthcare professionals know that nurses and other hospital employees don't get enough breaks during the day, yet alone time to eat a proper meal. Fatigue leads to bad service and, even worse, mistakes and errors that harm patients.
Toyota's production associates get a 10-minute break every two hours in the first half of their shift, then a lunch break. The break areas are conveniently located close to the line to minimize the time spent not resting. During our tour, a break occurred, and it got nearly silent in the plant, with equipment being shut down to save energy, I presume.
Granted, it's easier for Toyota to choose to stop producing for a period of time than it is for a hospital. Patients are still there and need care. That said, I think hospitals can figure out how to schedule staff to allow some to take breaks while others maintain patient care.
After lunch, Toyota gives team members a 10-minute break every 90 minutes, more frequently than before lunch. Why? Because they know that people get more fatigued toward the end of the shift. The healthcare visitors were impressed with the care and attention placed on preventing fatigue and defects or other problems. It's respectful to provide appropriate breaks and it's smart business, as it leads to better safety and quality, among other benefits.
Listen to Mark read this post (learn more and subscribe via iTunes):
Andon Cords and Buttons
As with the San Antonio tours, the visitors were impressed with the support provided to employees through the “andon” system. Our guide described that when the team members were falling behind or had any problem, it “should be identified immediately” by activating the andon system. Read my post from the 2012 tour about andon pulls and corporate culture.
As we saw during our visit, a Team Leader comes immediately after the chimes sound and the “andon board” indicates where the problem is and who needs help. The team leaders and team members wear baseball caps in the plant (compared to hard hats in San Antonio).
As I wrote about last year, Toyota is switching from the traditional “andon cord” to yellow push buttons. Here, at this plant, they had buttons that rolled along with the team members on their parts cart. The button seems like a very convenient mechanism for the team member to call for help. In the final inspection area, they had traditional andon cords since there are no parts carts there. The key principles are to allow people to ask for help, then respond immediately with support, trouble shooting, and problem solving, as needed.
See this short video:
Yes, there is a final inspection area in Toyota plants. What? I thought they built in quality? Well, that's their goal, but they realize that, today, having final inspection is better than NOT having inspection. The ideal is built in quality, but today's goal requires doing everything possible to protect customers from defects (customer first).
How can healthcare apply these principles? Check out what Virginia Mason has done with their Patient Safety Alert system.
4S and Workplace Organization
Is that a typo? 4S?? That's what you might be thinking as you read this.
In the Lean community, people often debate or argue about using the term “5s” (the more common term, which I've preferred) or “6S,” which adds “Safety” as an S. I'm all in favor of safety of course… but I think safety should be the foundation for everything we do. The Tsutsumi plant, like the San Antonio plant, has a green safety arch that everybody walks through when entering the plant. It's symbolic, but it says something like “safety is the door through which all work enters” or something like that. Safety isn't an “S” to tack on.
Toyota was calling it 4S:
- Sort
- Set
- Shine
- Standardize
Our guide was asked about the 5th S, “Sustain,” and she said something to the effect that it's assumed it will be sustain. I think that probably really means that the leaders, at all levels, work to ensure that sustainment.
I know the healthcare leaders, nurses, and physicians in our group realized there were many lessons to take away from a visit to Toyota. The same has been true here in San Antonio.
What do you think? Please scroll down (or click) to post a comment. Or please share the post with your thoughts on LinkedIn – and follow me or connect with me there.
Did you like this post? Make sure you don't miss a post or podcast — Subscribe to get notified about posts via email daily or weekly.
Check out my latest book, The Mistakes That Make Us: Cultivating a Culture of Learning and Innovation: