As a LinkedIn “Influencer,” I was invited to contribute a story to the “My Best Mistake” series. I wrote about something I, at first, thought was a mistake… taking my first job out of college at General Motors.
In the piece, I write about why I wasn't interested in a job at General Motors, but why I took a job there anyway (one plant's supposed dedication to the “Deming Philosophy” of W. Edwards Deming). Alas, I learned the “Livonia Philosophy” was (ironically) just a poster and slogan on the wall.
My Best Mistake: Working at General Motors
But, it turned out to be a great learning experience… but, sadly, the Livonia Engine Plant was closed as a result of GM's bankruptcy, even with the great improvements they had made after we got a new plant manager who was one of the first GM people to learn from the GM/Toyota NUMMI joint venture (as you can hear about here).
A photo of the closed plant:
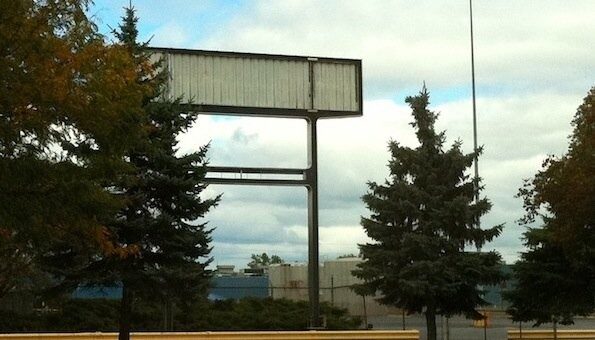
The full article:
My best mistake was one of my earliest career decisions – taking my first real job at General Motors. From all of the darkness and frustration came some amazing mentors and some learning opportunities that have helped me throughout my career.
When I was graduating from undergrad in 1995, I was a weird bird in that I had read, and become a huge fan of, the work of the quality guru and author W. Edwards Deming (1900-1993). My dad, as a GM employee, took his famed four-day seminar while I was in high school, which led to my interest in Deming. I read his seminal book Out of Crisis for fun over one holiday break. Yeah, weird.
As I was looking for my first full-time job out of college, I was originally pretty dead set against working for GM. From what I knew, GM was a traditional “command and control” style company that Dr. Deming railed against. I was idealistic, so I wanted to work in an organization that thought systemically, was customer and quality focused, and engaged all employees in continual improvement.
Through the job search process, I thought I had actually found one of the exceptions to the usual GM culture in the Livonia Engine Plant, located in my home town, just over a mile from where I grew up. During the interviewing process, they sold me on their “Livonia Philosophy,” which was basically a re-writing of the Deming Philosophy and approach to management and quality. It sounded like a great opportunity, so I took the job.
Oops.
Within the first week, I realized that the Livonia Philosophy might have been actively followed back in 1990… but the philosophy seemed to have sadly died along with Dr. Deming in 1993. The philosophy was really just a poster and slogans on the wall (the irony of this will be clear to others who have studied Deming).
In the plant, “leaders” ruled by fear and screaming. That was the GM way. They blamed UAW workers for poor quality when it was the managers who wouldn't let the workers stop the line to do proper quality checks. It was the traditional GM culture – quantity over quality. It was, ironically, everything Deming was opposed to. All of the plant's problems were attributed to either a “lack of urgency” or a “lack of intensity,” said our plant superintendent (second in command) nearly every day. Ugh.
Our plant had low productivity, poor quality, and very low morale. It was like a personal dark cloud was issued when you came in the door each morning, following you around all day. It didn't feel particularly safe. A few times, I slipped and fell on the greasy floor and I routined breathed air that hung heavy with the mist created by cutting fluid in the engine block machining stations that I was the industrial engineer for.
The only bright spot in this disaster was a group of salaried employees who had been hired from Toyota suppliers, Nissan, and other companies that did things more along the lines of what Dr. Deming taught, using Lean and the Toyota Production System. They were sent by GM Powertrain headquarters to help, but local management wanted nothing to do with them. They were literally exiled to a mezzanine-level office, as far away from the plant manager as possible.
Thankfully for me, there was a combination of bored “lean thinkers,” an eager student (me), and a plant full of waste to examine. Since the old-guard managers weren't really interested in different thinking (their only solution was the UAW workers working harder), the lean thinkers could really just talk to me about how things could be different. They explained how managers behaved in their old workplaces and why it worked better. They were happy to have a student and I was happy to learn.
After a few major quality problems with our Cadillac engines (which were, of course, blamed on the workers, when it was really a problem with the management system), the plant manager was promoted to a role at headquarters. Only GM could be so good at rewarding failure (but he was close to retirement, so maybe it was humane).
We got a new plant manager who had been one of the first GM people to work with Toyota at the famed NUMMI joint venture plant in California (he was interviewed for the This American Life episode about the factory). This was the style of leader I wanted to work for. He started engaging the lean thinkers to actually start working with people on improvement. He stood up in front of the UAW workers and salaried staff and told them the problem wasn't the workers – the problem was the management system. And that system started to change, thanks to his leadership.
After my first six months at GM, and before this new plant manager was brought in, I thought I had made the biggest mistake of my life. I wished I had gotten a job at Honda or Toyota. Looking back at it, those two years of experience include lessons I still draw on when working in hospitals (which are often managed today more like the old GM of 1995). As painful as it was at times, the experience of starting to fix a really broken organization has actually served me very well. That's not really the type of experience I would have gotten at Toyota. It turns out that starting my career at GM was the best mistake I ever made.
I left after two years at GM – one really bad year and one that was pretty encouraging. It was hard to pass up the chance to go to MIT for grad school (a great opportunity that came up thanks to the mentoring of an MIT alum I worked with and another great mentor at GM).
Sadly, the plant is now closed – a victim of the GM bankruptcy. I took the photo of the closed plant with its now-empty sign back in 2011 when I was back home.
What do you think? Please scroll down (or click) to post a comment. Or please share the post with your thoughts on LinkedIn – and follow me or connect with me there.
Did you like this post? Make sure you don't miss a post or podcast — Subscribe to get notified about posts via email daily or weekly.
Check out my latest book, The Mistakes That Make Us: Cultivating a Culture of Learning and Innovation:
As bad as it was for the employees, it was just as bad for the suppliers.
Back in the early 90’s, I was fortunate to have had an internship with a company called Amtex, a supplier of automotive carpets to the NUMMI facility in Fremont, California. It was quite a learning experience and I certainly saw firsthand the clear and evident commitment on the part of the company to its employees. Toyota, even in Japan and contrary to popular myth, does not guarantee lifetime employment. No employer can credibly make such a guarantee. What an employer can do and what Toyota does is state that the last thing the company wants to do is lay off employees. Only as a last resort will it turn to reducing the work force. Through such a policy, real trust can develop between the company and employees, along with the motivation for employees to accept responsibility and take ownership. At NUMMI, this policy was called “mutual trust.” However, the plant since closed back in 2010, and the facility is now the new TESLA plant.
Thanks, David. It’s sad that something as simple as “mutual trust” is missing from so many organizations.
I wonder how things are, culture wise, at the plant now that it’s Tesla.
[…] When I worked at GM from 1995 to 1997, it was VERY male driven. The only female manager I can remember in my plant was the head of quality. The plant manager, everybody at the level below him, and all of the managers and supervisors I worked with were men. There were many women in the engineering ranks and on the assembly line. But leadership (or what passed for it there) still seemed to be a very male domain. […]