Thanks to my friend Matt May (check out his new book The Laws of Subtraction) for hosting “5 Questions” about my latest book Healthcare Kaizen. Matt asked some great questions and I hope you enjoy the discussion.
Healthcare Kaizen: 5 Questions With Mark Graban
What are the most significant differences between Lean Hospitals and Healthcare Kaizen?
In Lean Hospitals, my goal was to simply and succinctly define core “lean” (aka “Toyota Production System”) concepts, philosophies, and methods in a healthcare context. The book provides examples without having a prescriptive, multiyear implementation path for an organization, since I believe there's no single cookbook approach to “going lean.”
Healthcare Kaizen is different in that it provides a bit more of a how-to path for an organization, starting with how to use kaizen principles in a single department and progressing to how to establish a broader program and a “kaizen promotion office” (KPO) in an organization.
Lean Hospitals incorporated a balanced set of examples from different healthcare organizations around the world, while Healthcare Kaizen draws heavily on the experiences of my co-author (Joe Swartz) over the past seven years at his employer, the Franciscan St. Francis Health System in Indianapolis. About two-thirds of the book's examples come from his organization, and many of its lessons on leadership and its KPO are the core of the book, while I contributed other methods and examples from organizations I've worked with or know. We have more than 120 examples of real kaizen improvements, both large and small, in the book (with full color photos), as we think healthcare professionals are used to learning a method from case examples–the point is to learn the kaizen process rather than copying all of those individual improvements.
In the Foreword, Masaaki Imai (author of Gemba Kaizen) states that he's disappointed in the speed at which Kaizen is being embraced and adopted in the West. What's your take?
When I worked in manufacturing, I found it incredibly sad that so many workers are not listened to, being told (often literally) to “check their brains at the door.” This was a major part of the problem at General Motors when I worked there during the mid-1990s, as it was harder for the company's leadership (at all levels) to embrace kaizen and other new leadership principles than it was to adopt isolated lean tools like 5S or value stream maps.
When I moved into healthcare in 2005, I was sadly disappointed to see that nurses, laboratory technologists, and other hospital frontline staff members had similar complaints–that nobody ever asked what they thought about anything, and that they were not engaged in kaizen or any meaningful form of continuous quality improvement. Even though everybody was better educated, the dynamics between frontline staff and managers, and with their senior leaders, were shockingly familiar.
During the past 10 years, healthcare organizations have increasingly embraced lean methods. However, many still rely too much on formally scheduled, weeklong projects, and they rely too much on lean specialists rather than engaging everybody in real continuous improvement. Kaizen and continuous improvement leads to higher staff engagement, which correlates well in healthcare journal studies with higher patient satisfaction and, more important, better patient outcomes. This is really important improvement work, and we need more of it. Now. Lives are at stake.
So, yes, I share Mr. Imai's disappointment. The famed healthcare quality advocate Dr. Don Berwick wrote about kaizen in The New England Journal of Medicine, in 1989, citing Imai's work and the related leadership teachings of W. Edwards Deming. A few leading organizations, like ThedaCare (Wisconsin), Virginia Mason Medical Center (Washington), and the University of Michigan Health System are working toward their stated goal of “everybody being a problem-solver every day.” And, again, my co-author's organization is doing a fantastic job.
We are constantly trying to make Kaizen “quick and easy.” Why do we do that? It seems to be the antithesis of the principle and practice. Is speed and difficulty the major obstacles (see Question 2) in the minds of Western managers? If not, what is?
I disagree with the premise that “quick and easy” is the antithesis of rigorous process improvement. “Quick and easy” is the best way to get started from my experience, and it's our best shot of turning a goal of a “culture of continuous improvement” into reality.
I think Imai and an American, Norman Bodek, in their books about kaizen, share great wisdom about starting with “quick and easy” kaizen ideas (as Bodek calls it). That doesn't mean every kaizen improvement can always be implemented quickly, or that we only do small things. A hospital department might have a broken chair–so a quick-and-easy kaizen is to get it fixed or replaced before somebody gets hurt. If chairs are being broken frequently, then the team might use a more rigorous problem-solving approach, like an “A3” format for the plan-do-study-act (PDSA) cycle. An emergency department might work on moving the location of a crash cart (a simple fix) while also applying the kaizen process to the improvement of clinical protocols and resident training. We have opportunities for improvement of all sizes and levels of complexity in healthcare.
While researching our book, I found the work of a UCLA professor and psychologist, Robert Maurer. It's too easy for leaders to pooh-pooh the idea that people are afraid of change, by basically telling people to just tough it out, à la Who Moved My Cheese?, (J. P. Putnam's Sons, 1998), a book I really dislike. Maurer writes about the brain science and evolutionary traits that literally make us afraid of large change. When faced with a large change (even an overwhelmingly positive one), the “fight or flight” instinct of our reptile brain kicks in, and our creativity ceases. Maurer teaches, as does Imai, that the best way to create a culture of innovation (a buzzword so beloved in this day and age) is to get the ball rolling with small changes that don't create fear. Maurer says to ask employees, “What's the smallest possible improvement we could make?” Instead of just asking people to not be scared, we need to reduce the level of fear, by starting small.
As we discuss in the book, once people participate in small changes, they gain enthusiasm and build problem-solving skills. Then, they are more likely to find or stumble across larger changes. I think the major obstacle to improvement is the Western obsession with “million-dollar ideas.” Asking for these rare, million-dollar ideas is the surest way to kick in the fight-or-flight response. Through small ideas, my co-author's hospital is saving millions of dollars a year. It's better to have lots of relatively small improvements (more than 4,000 in 2011) that add up, instead of a small number of huge projects.
What surprising insights or learnings did you realize in writing this book? Why were they so powerful?
I was really surprised to stumble across a book written by a TV host, model, and actress, Maria Menounos, called The EveryGirl's Guide to Life (It Books, 2011). This is not the type of book I normally read! OK, I didn't read the whole thing, but I thought it was fascinating that she wrote, in part, about kaizen, which she defined as a “Japanese philosophy that focuses on continuous improvement in all aspects of life.” She added, “When something in life is good or works well, remain open and challenge yourself as to how it could be improved.” It was surprising to see a celebrity touting this approach for improving one's life.
Maurer also uses the kaizen approach to help his patients get started with, say, an exercise program. Instead of saying “start exercising 60 minutes a day,” Maurer's approach is to ask the patient to start with one minute of exercise a day, as that's less scary… then new habits form and people can increase their exercise gradually (yet pretty quickly) with a higher success rate than those who are scared into inaction by a big goal.
Partly inspired by this, we included an entire chapter of “home kaizen” examples that had been submitted by staff members at my co-author's organization, proving that kaizen really is a philosophy and a way of thinking… it's hard to turn off this way of thinking once you start practicing kaizen. It really does become hardwired as a new way of thinking, as Maurer would say in his books.
What is the one thing you want readers to take away from Healthcare Kaizen?
Improvement cannot be limited to experts and improvement specialists–whether those experts work in the domains of lean, Six Sigma, or other approaches. We have so many problems to fix in healthcare that the only way to engage people in fixing the really big, systemic problems is to first engage them on all of the little nagging things that interfere with them providing the best patient care. As Imai says, “Kaizen is for everybody!” and kaizen is something that can (and must) be practiced every day (or at least every week).
Please scroll down (or click) to post a comment. Connect with me on LinkedIn.
Let’s work together to build a culture of continuous improvement and psychological safety. If you're a leader looking to create lasting change—not just projects—I help organizations:
- Engage people at all levels in sustainable improvement
- Shift from fear of mistakes to learning from them
- Apply Lean thinking in practical, people-centered ways
Interested in coaching or a keynote talk? Let’s start a conversation.
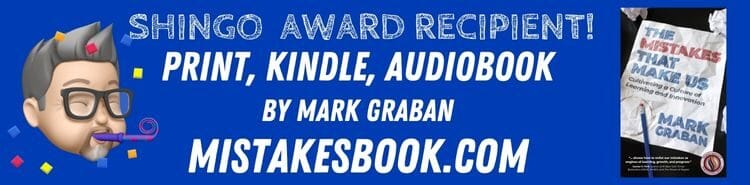
Nice article, Mark.