Thanks to Dean Bliss for sending an article to me about some of the great Lean healthcare work taking place in Iowa. I've visited Iowa a number of times to give talks and visit hospitals and I know many of the leaders from their involvement in the Healthcare Value Network. There have been many people who moved over from the best Iowa lean manufacturing companies to help improve Iowa Healthcare (including Dean). New Shingo Award winner John Toussaint, MD even went to medical school in Iowa. What's in the water there? :-)
Before getting into all of the good stuff, there are two things that bothered me a bit:
- The headline about “squeezing costs”
- The line about “speeding up” processes.
The subtitle is a better reflection of the work taking place. The headline and sub read:
Squeezing health-care costs
A majority of Iowa hospitals are using lean techniques to increase efficiency, improve care
I don't think of “squeezing” as being a word with positive connotations. Growing up around the Big Three and starting my career at GM, “squeezing” was a pejorative, meaning that an automaker was just bullying the supplier into providing lower prices. In comparison, Toyota was known for partnering up with suppliers to reduce waste and do things that would actually reduce costs, allowing Toyota to share in some of the savings. Chrysler was, for example, shifting to that more collaborative style, but then Daimler bought them, and they went back to the old way of just demanding a price reduction each year.
The U.S. federal government (Medicare and Medicaid) seems to take the lead in “squeezing” hospitals and doctors. The argument in favor of just arbitrarily slashing prices (because you can) is that it “forces” the supplier (the hospital or the doctor) to get more efficient to keep their margins in line. But, squeezing leads to many dysfunctions — it often bankrupted some auto suppliers and it might lead to quality suffering if the supplier is just slashing costs instead of really reducing waste (as Toyota would teach them to do). There are some cases of private insurers working with healthcare suppliers to partner up on reducing waste and sharing the savings… that's more of the Lean model.
It is not the fault of the Iowa healthcare folks that the headline and this other line from the story made me cringe. Ala Toyota senseis…. we can talk about the problems first, then get to the good stuff.
I left this comment on the news story site, if they publish it:
Thanks for a great article that highlights the important improvements that are taking place in Iowa healthcare.
This one sentence prompts my comment:
“Lean techniques focus on speeding up processes and reducing waste by identifying and eliminating steps or activities that don't add value.”
When talking about Lean, to say we “speed up” processes really means that we are minimizing delays and waiting time and we're eliminating non-value adding steps, as you say.
Unfortunately, hearing “speed up” makes people think the focus is on doing the real value added work faster, which isn't the focus of Lean. Speeding up the work makes us think of the Lucy and Ethel chocolate factory scene from I Love Lucy, which is a stressful workplace that put out bad quality.
Lean healthcare is about reducing waste so that healthcare professionals aren't stressed, which allows them to provide the best patient care possible, as IHS and Mercy are demonstrating.
OK, now to the good stuff…
About Iowa Health System, from the article:
In 2009, Iowa Health hired its first lean specialist, Valerie Boelman, an industrial engineer who had formerly worked at two Iowa manufacturing companies, as its process improvement coordinator.
“We had a lot of good people internally who knew quality and health care, but we didn't really have the expertise in process and inventory and those kinds of things that we needed,” Nessa said. “So rather than try to train internally, we made a purposeful decision to go out and hire that expertise, and we've continued to do that. We're now using some of these people to infuse these skills into other areas of the organization.”
Read more: http://bit.ly/zv5iys
It's great to see a hospital being open to bringing in people from other industries, as it's the combination of experiences and skill sets (inside and outside eyes) that leads to great improvements.
And their results from the use of Lean and Six Sigma:
“We're touching really every part of the institution right now, from clinical to non-clinical areas,” Nessa said. Since 2009, her team has led 25 quality improvement projects and contributed to more than 100 additional projects. Last year, the team generated more than $1.7 million in savings for Iowa Health – Des Moines.
And about Mercy Medical Center and their hybrid “Lean/Six Sigma” approach:
“This team is really focused on improving processes to improve quality, patient safety and service to our patients; those things always come first,” he said. “But we've also been able to eliminate waste and reduce costs.”
In the past eight years, Mercy's process improvement team has completed more than 300 projects, Varnum said. Last year, the hospital saved more than $3.3 million through improvements put in place through the team's work.
That's yet another example of an organization that shows Lean isn't about “cost cutting.” If you do the right things for the patients and for the staff, cost and financial impact will follow.
And Mercy also realizes that Lean is not about layoffs:
As one example of a cost-saving project, Mercy eliminated approximately $500,000 in annual labor costs by streamlining the movement of soiled linens, equipment needing sterilization and trash handled by its reprocessing department. With the more efficient processes, fewer people are needed to do the work. “And we accomplished this with no layoffs of staff,” Varnum said. “We actually transitioned these people into other areas of the organization. It's just a great example of how it's supposed to work.”
And they realize that Lean has to involve everybody:
Every project involves front-line staff from the department that's involved “so they're part of the process work being done,” Varnum said.
Congrats to these organizations… you can read more and see more data and examples of their results in the article.
Please scroll down (or click) to post a comment. Connect with me on LinkedIn.
Let’s work together to build a culture of continuous improvement and psychological safety. If you're a leader looking to create lasting change—not just projects—I help organizations:
- Engage people at all levels in sustainable improvement
- Shift from fear of mistakes to learning from them
- Apply Lean thinking in practical, people-centered ways
Interested in coaching or a keynote talk? Let’s start a conversation.
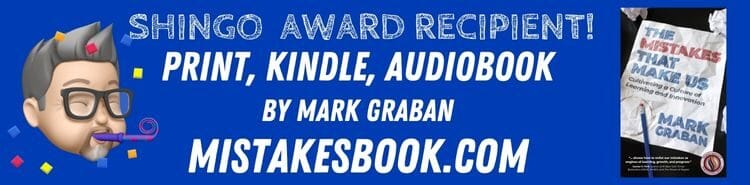
Thanks for posting, Mark. We are proud of our work in Iowa, but we realize we have a long way to go.
Mark as you point out there is a difference between squeezing costs & speeding up the process and elminating waste, reducing the leadtime & cashing the resultant savings.
One difference is in the language we use which needs to be about engaging and being respectful of people. Another is in being choiceful about how we cash in the savings. The benifits don’t have to be just financial but certainly could be in quality of patient care and speed of service to patients.