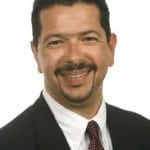
A returning guest for episode #132, we are joined by author and professor Bob Emiliani. Today, we are chatting about some videos he recently posted to his website… 10-year-old videos that document executives from Virginia Mason Medical Center, now considered a leader in Lean healthcare, visiting a Lean manufacturing company, Wiremold. You can view the videos on Bob's site or read some summaries via this blog post of mine.
In the podcast, Bob reflects on those videos and we talk about some of the lessons learned – what healthcare executives can learn about Lean leadership from manufacturing leaders.
For a link to this episode, refer people to www.leanblog.org/132.
For earlier episodes, visit the main Podcast page, which includes information on how to subscribe via RSS or via Apple Podcasts.
If you have feedback on the podcast, or any questions for me or my guests, you can email me at leanpodcast@gmail.com or you can call and leave a voicemail by calling the “Lean Line” at (817) 372-5682 or contact me via Skype id “
Full Transcript:
You can also now buy a book that contains some of my favorite podcast transcripts, via Amazon:
Mark Graban: My guest today is Bob Emiliani. We are going to be talking about some videos he posted on his website. They are 10 years old. They are some videos of a real pioneer in Lean health care; Virginia Mason Medical Center in Seattle, visiting a company in Connecticut called Wiremold, a manufacturing company.
Bob, in the course of doing research for a book 10 years ago, recorded a video.
He has unearthed that archive, digitalized it, put it on the web, for all of us to watch and learn from. It's interesting that of Lean healthcare industry, you can go and see those videos on his site or you can go to leanblog.org/virginiamason – Unfortunately, the videos are no longer online, but the link there has some of my notes about it.
Mark: I'm very happy to welcome back a good friend of mine and the blog in the podcast, Bob Emiliani, frequent guest in previous episodes. Thanks for joining us again, Bob.
Bob Emiliani: It's a pleasure to be here.
Mark: We're talking today where you posted a treasure trove of videos taken from ten years ago. I'll let you talk about the videos. Virginia Mason and Wiremold, great stuff that you shared online. I'll let you tell the listeners about these videos.
Bob: Sure, sure. In the 2001-2002 time frame, we were doing the research for the book Better Thinking, Better Results.
Around that time, a bunch of people from Virginia Mason Medical Center — close to 30 physicians, managers, department managers, executives, and so forth — made the trip to Wiremold. We thought this would be a wonderful thing to capture on film as part of the documentation for the research that we were doing for the book.
We shot the videos in 2001, it was November 2001, we shot the videos and got copies of them and put them away. I think I looked at them briefly but I put them away, used them a little bit for the book. We had extensive interviews with the executives that were transcribed. We worked mainly from that for the book.
Essentially put them on the shelf, and that's where they've been for about ten years.
Everybody forgot about the videos. I didn't because I looked at them everyday, and there they were. [laughs] Time passes and up comes the tenth anniversary. I'm thinking, “Let me have a look at these. See what's there.” I had a look. Having not seen the videos for such a long time I was impressed with what I saw.
It turns out that I have the only copy left. All the other copies were lost or destroyed, or whatever. I decided to digitize them and put them on the web for the tenth anniversary of the visit of the Virginia Mason medical center folks to the Wiremold facility in West Hartford.
I decided to post them. I was really interested in posting them for historical reasons, because it's such an interesting piece of Lean history. How Lean and health care get started. As well as extremely educational. I didn't want to sell the videos, I wanted to make this widely available so that people could learn from this. Hopefully apply what they learn.
They're also unedited. You can see it all as it was. I think in unedited form it really most useful for people in general and researchers, teachers, students, managers, politicians, and whoever is interested in learning about Lean. By not editing them, I wanted to make the point that I'm not cherry picking the best stuff out of the video to show. You're seeing it completely as it is.
It a wonderful lesson in Wiremold's senior management understanding of the, “application and continuous improvement of respect or people” principle. Ultimately, I hope people will see the videos as a wonderful companion to the Better Thinking, Better Results book as well.
Mark Graban: Yeah. For context for folks, Wiremold's Lean journey, if you will, started about what time frame?
Bob: It was 1991.
Mark: They were about 10 years in. Virginia Mason's at the their ten year point in their journey. I'm curious in terms the of the context of the set up, of how Virginia Mason got there, hospital in Seattle, visiting a manufacturing company in Connecticut? What was the connection that led them, to travel cross country, and go learn from Wiremold?
Bob: They had read the vignette in the book, Lean Thinking by Jim Womack and Dan Jones. They read the Wiremold's vignette in there. Gary Kaplan was the new President, and “CEO” of Virginia Mason, he'd been in the job about a year, he realized that health care had to change, and among the things they did early on, was to make this visit to Wiremold.
I remember vividly one day, a bus pulling up to Wiremold, 25 or 30 executives, department managers, and physicians, getting off this bus, and filing into the conference room, to hear the presentation. They had lots of shop floor visits, seeing how things were going in the shops, and in the office at Wiremold. One of the things that, I was impressed about seeing, especially again, when you go back and see the video 10 years later, it really hits me even more.
The Virginia Mason team was, a team that was highly motivated to learn new things, and they weren't put off at all, by seeing the application of “Lean” in manufacturing. They were able to translate it to health care, and of course Art Byrne, Orry Fiume, Kevin Fahey, and the others, they also helped make this translation. The Virginia Mason folks were able to help that along, and I think this was a very important step along the way.
You know Mark, that some people would say, “Oh, no this is a manufacturing thing, we're health care, and we're different,” and they didn't fall into that trap. They seemed to be very motivated, they asked great questions, and they had done their homework. Gary must have done a good job, by preparing the team for the visit, they had read things and so forth, they were extremely receptive. Their story is told in a book that came out last year called “Transforming Health Care.”
Mark: Right.
Bob: Which is an excellent book, and I hope other people have a look at that.
Mark: Yeah, that is a great book, Charles Kenney is a very good author, who worked with the team at Virginia Mason, to help compile and share that story, because now you have a lot of organizations, that go travel sometimes across the country, and the other direction to go and visit Virginia Mason, and to see what they're doing.
Bob: Mm-hmm.
Mark: Now you have Dr. Kaplan and others, in that role, giving the talks, and Art, Orry and the other leaders from Wiremold are doing.
Bob: That's right, and it's also nice to see, this student/teacher relationship. A chain of teacher and student, teacher and student. For Virginia Mason, “Wiremold's” the teacher, Virginia Mason is the student. Now Virginia Mason is the teacher teaching other students, and so forth, it's just nice to see that.
Mark: Was there an on going relationship, over time that you're aware of, between “Wiremold” and Virginia Mason? Some of the leaders have moved on, or retired from Wiremold, did they continue to play a role in, helping coach or mentor Virginia Mason?
Bob: Absolutely they did, Art has been a close colleague, and friend of Gary Kaplan for some time now, better then 10 years now, and yeah, there's been an on going relationship there.
Mark: What were some of the things in your review, and recollections of the videos, some of the common themes, that senior leaders were talking about? Senior leader to senior leader I know you said, “That they were people from all sorts of levels, visiting from Virginia Mason.” What were some of the things, that were set out, as being transferable, in terms of the lessons learned, or just the “Lean” principles that they were sharing.
Bob: I think it's just interesting the way, Art was able to tell they story, make it resonate to people, in a completely different line of work. He's drawing analogies, between what they do in the shop, and what goes on in healthcare. We've all had some experience in healthcare whether it's a doctor's office or some sort of operation.
With our knowledge of Lean we can kind of relate to how things could be improved in healthcare. The first part of the series of videos is a 10 or 11 minute opening statement that Art gives to Virginia Mason where he provides these kinds of analogies and so forth. Art comes across as he is, which is a very regular guy and he's just telling a story, and very fact-based and so forth, and very sensible and logical.
The feedback I get from the video is that people say, “Wow I can't believe a CEO talks like that. My CEO doesn't talk anything like that. My CEO doesn't know any of that sort of stuff. In fact, my CEO says stuff that's opposite to that.” It's just so interesting to see this interaction between Wiremold and Virginia Mason.
From the Wiremold perspective, the videos show the result of a senior management team that immersed itself in Lean for many years. They, through hands-on experience with Lean, not telling people, “this is important for you to do, go do it”, but for themselves actually getting involved and practicing it on a daily basis themselves that they learned these nuances and details of Lean, which is very rare for senior managers to know.
They're able to explain this to the Virginia Mason folks, which I think is part of the reason it helped, with it being a receptive message for the Virginia Mason folks. It really emphasizes what you see in the Wiremold executives is “Here's what happens when leaders at the top are engaged in actual daily Lean practice; hands-on doing and hands-on thinking.”
Mark: Ten years later that's one of the things that is striking when others go and visit Virginia Mason or when Gary Kaplan talks about his role as a CEO, going to the Gemba. Going and asking questions and having both the involvement and the style of leadership is something that you can see…You see similar things when you go and visit ThedaCare. I've only had the pleasure to spend… I was able to spend half a day once at Virginia Mason. I've spent more time at ThedaCare. But I think both organizations, as well as some others, are doing a great job of trying to pass those lessons along to others in healthcare.
Bob: Yeah. I think this is part of the way it is with people who understand Lean well, is that they recognize they have a responsibility to teach what they had learned from others. What you see Art and Orry and so forth doing is that they're teaching Virginia Mason the things that they've learned themselves on the job and the things that they've learned from some of their teachers and some of the consultants and so forth over the years.
You've got to say, too, that with Virginia Mason's visit there the Wiremold folks are learning stuff too from Virginia Mason, right? It's always a bilateral sort of thing.
Mark: I'm curious to maybe delve into that a little bit more, from your experiences or maybe what you knew directly from Wiremold, the idea of learning by hosting a site visit or having others come in and ask questions. I guess it kind of falls back to the old idea of learning through teaching, having to reflect on your ideas.
Bob: Oh, absolutely. To be able to explain something requires a lot of baseline knowledge of it. But then, as these audiences change because they're in different lines of business, or different industries, or different companies, or from different countries or what have you, that always challenges your ability to explain things.
In doing so, you learn things. You learn where there are good connections between what you know and what's going on in some other industry or where there are disconnects, minor or major, that you need to think about to improve your explanation or that you need to learn more about in order to provide a better explanation.
I also think it's just a part of the mindset of a Lean leader. While their job title might be “Manager”, they always see themselves as teachers. In a conventionally managed business, the managers there never consider themselves as teachers.
Mark: Well they're supposed to have all the answers.
Bob: Have all the answers and tell people what to do. Whereas in “Lean world” the manager is a teacher as well. You see this tradition carry on from the people who trained and taught the Wiremold executives, training and teaching the Virginia Mason executives, and so forth on down the line.
Mark: Hopefully, I think we're seeing more and more of that in healthcare. Virginia Mason is teaching and hosting people. ThedaCare, through their involvement with the Lean Enterprise Institute, the Healthcare Value Network, we're seeing more and more hospitals teaching each other, they're going and visiting manufacturing.
I should go and ask somebody at Virginia Mason if they're at a point where they have manufacturing companies that are early in their Lean journey coming to visit Virginia Mason. I mean there's no reason why these lessons can't go back and forth across these different boundaries. Are you seeing anything like that going on out there?
Bob: No I'm not. I think that's a really good thing to ask. I don't know that it is happening. But that would be very interesting.
Mark: Maybe a last question to ask you of your own reflection: anything new? You've certainly lived through this and you've seen the videos a bunch. Were there any “aha” moments or light bulbs going off in your last viewing of these?
Bob Emiliani: I just think it's, generally, just really interesting. You've got practical examples of actual executives who know Lean very well, know all these nuances and details, and the videos inform you of how they think, and how they talk, and what they know, and it provides a basis for comparison to others in terms of a model for leadership or a direction on which they need to go to learn things.
The feedback has been very positive upon releasing these videos. I've got to say a couple other things too. I did post as well, an editable PDF form, in which people can type in and extract their leadership lessons.
There's a page that people can write in. What are their leadership lessons from listening to Art Byrne? What's my practical action to take? What's my expected outcome? What's my actual outcome?
The learning lessons here are very practical and people can pick up on those and apply those. There's a form for each one of the videos that they see. In addition, I'm in the process of getting some videos made.
One of Art Byrne reflecting on this visit ten years ago. I hope to have that posted on the website later in December, towards the end. Virginia Mason folks are also putting together a five or seven minute reflections video from Gary Kaplan from this visit. Those two videos will be posted on my website towards the end of the year or very early next year.
Mark: That's great.
Bob: Stay tuned for that. Yeah, I'm looking forward to that.
Mark: That's great that they're doing that and I'll certainly post about that on the blog. For people that are listening, if you want to keep an eye out for that, go to Bob's website, bobmiliani.com. He's got a great newsletter that's sent out. That would be another way to learn about all this great stuff that's coming out from Bob.
Thanks for sharing that and it's always good talking to you about it.
Bob: Likewise. You're welcome.
What do you think? Please scroll down (or click) to post a comment. Or please share the post with your thoughts on LinkedIn – and follow me or connect with me there.
Did you like this post? Make sure you don't miss a post or podcast — Subscribe to get notified about posts via email daily or weekly.
Check out my latest book, The Mistakes That Make Us: Cultivating a Culture of Learning and Innovation: