As I've talked to and worked with hospitals and their leaders about Kaizen, or continuous improvement, the concepts, mindsets, and methods make sense to people. They understand how Kaizen is different than the outdated and ineffective suggestion box method.
A common response is “Mark, that makes sense… but we just don't have time….”
I'd like to make the case that “lack of time” should not be an excuse that shuts down the possibility for Kaizen, but rather it's the first problem statement to which we can apply our Kaizen thinking…
“Lack of time” can't be the end of the story. Healthcare is too important, for patients and our staff, for us to accept “lack of time” as an excuse. Leaders should ask “what can we do to free up time for Kaizen?” If improving is a priority (a necessity, really), we have to make time for it.
A number of hospitals in the Lean Healthcare movement have instituted a practice of having a two-hour “no meeting zone” at the start of each day. No, this doesn't create more time for catching up on email. The no-meeting zone time is used for going to the “gemba,” or the place where the work is done. Leaders participate in team huddles and participate in Kaizen during that time.
Speaking of email, there have got to be ways to encourage people to use email more intelligently, so it isn't such a time sink for everybody. Can everybody hold to, for example, a “three sentences” policy? Can we reduce the number of unnecessary CCs and BCCs? I don't know what the answers are for your organization… but that's another area that could be addressed to free up time.
You can look into your own work, as a manager or leader, to identify time or activities that are the most wasteful. Are there meetings that you can send a delegate to? Or maybe some meetings should be replaced with a short email status update.
We explore this theme a bit in our book, Healthcare Kaizen.
Either way, my challenge to you is to use “Lack of Time” as a problem statement for the PDSA process. Or create an “A3” about how to free up time for Kaizen. What are the root causes of “lack of time?” What would you propose as countermeasures?
Please scroll down (or click) to post a comment. Connect with me on LinkedIn.
Let’s work together to build a culture of continuous improvement and psychological safety. If you're a leader looking to create lasting change—not just projects—I help organizations:
- Engage people at all levels in sustainable improvement
- Shift from fear of mistakes to learning from them
- Apply Lean thinking in practical, people-centered ways
Interested in coaching or a keynote talk? Let’s start a conversation.
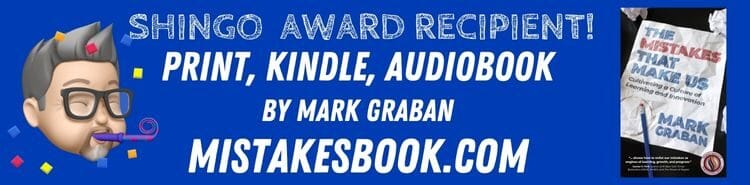
Mark…Ha!…I laughed when I saw your post this morning because I hear this statement used as an excuse all the time! NO TIME IS NO EXCUSE! Kaizen should not be done in addition to your work, but rather as part of the work itself. Kaizen is a mindset change about how we spend our work time. A few ways to help this process could be to actually budget kaizen time into each day, make it part of each employees job description, offer extra tim or paid over time to work on kaizen, and finally…apply kaizen BEFORE it becomes an emergency…be proactive rather than reactive!
Thanks for being (I think) a first-time commenter, Patrick. I hope you’ll come back to read and participate in the discussion.
I completely agree with both of you on the “no time is no excuse”… and I have frequently stated to groups that “doing your job” and “improving your job” are the same job. The last couple of lean projects I have been involved in recently have struggled to find the time for employees to participate. A sure way to create some cynicism towards lean is by management not supporting staff to make the time to participate.
This is unfortunately very common. Management is fine by doing “LEAN”. But as soon as people require time to think about continuous improvement, all believe in LEAN by management is gone. As a result, doing continuous improvement is just another monkey on their shoulders and the are expected to just “wing it”.
There’s an old quote from Lao Tsu that says, “Time is a created thing. Saying ‘I don’t have time’ is like saying ‘I don’t want to.’
Now that we’ve defined the problem, it’s time to do an A3!
Mark, great article. I have heard some saying that “because we do not have kaizens yet (which means no standards work and related standard audit piece”, we cannot use the no-meeting zone between 0800-1000 productively. My response to them would be to use that time and “with purpose” go to the gemba. That should lead to lots of kaizens. Kaizens then lead to standard work and standard work audit, which will lead to creation of “leader standard work.” At that point, we may hear that “the 0800-1000 no meeting zone” is not even enough any more to spend time on: 1) doing gemba walk, and 2) doing standard work audit. Gemba walk with purpose between those hours may be the 1st thing these folks want to do.
Ah, Mark: as you know, this is a subject near and dear to my own heart.
There’s no such thing as “lack of time.” If your child were sick and needed to be taken to the hospital, you’d find time. It’s just a matter of priorities — and in most organizations, kaizen just isn’t a priority on the order of, say, preparing for a Joint Commission visit.
The no meeting time blocks are a good start towards freeing up time, but I think that it’s a pretty clumsy tool. It’s far better to start looking for root cause — *why* do we have so many damned emails and so many meetings? — before applying a countermeasure like a no meeting time block, or limiting emails to 3 sentences. In my experience, poor communication protocols and a reliance on information “push” rather than “pull” lead to metastasizing email and meeting burden.
I’d love to talk more about this issue!
In my experience you also need to shut down ‘competing’ business improvement approaches.
One thing that struck me on a visit to another government bureaucracy that DOES do Lean well, is that the managers understand that the 1 hour standup meeting at the Obeya and their Gemba walk IS the actual meeting to discuss improving the business.
Not the token meeting they are going to have in front of the staff before disappearing into a meeting room to talk about essentially similar issues in a traditional management meeting format.
This is the curse of my organization. Convincing them Lean is an alternative to traditional management by firefighting or worrying around a boardroom table, not an add-on to, which of course is difficult to find time for.
Our local tribal health administration is building a huge new administrative office building (97,000 square feet), their second since I started working at a sister organization. Their current philosophy seems to be to add new employees to make apologies for all of the inefficiencies that exist. An aggressive schedule of Kaizen could free up a lot of administrative capacity to dedicate to health care.
I’ve seen negatives to kaizen when they were set up as bigger events which are expensive and also generate the expectation of some quick gains (often painful to implement) that will much more than offset the expense.
But if we commit to kaizen as a short daily routine that reviews yesterday’s issues and generates small continuous improvements that often may just be tweaking of procedures. Over time we just notice that we’re getting better.
[…] really good ones) hold you back from looking to find a way to make a difference. As Mark Graban suggested recently, let the identified barriers become your first problem […]
[…] performance through direct technical intervention nor motivation of people, and certainly not both. Lack of time for kaizen is not an excuse, but rather a problem to be studied and countered through effective root cause corrective action. […]
Leaders are starting to take note. It is really us the coaches, the practitioners to guide them all the way to deploying good emails and meeting etiquette. This week I called a meeting on 5S with a colleague. They accepted and turned up. In the course of the meeting he highlighted that his department has implemented a meeting free Wednesday and that I should really call this encounter a meeting. I was devastated: if I new the policy was in place I would have reschedule to comply. This is clearly a good practice that is not widely known in my organisation. Next step is for me to have all leaders communicate their no meeting zones in the week
Thanks for sharing your story. At least the manager didn’t try to get around the “no meeting zone” by saying, “Let’s call this meeting an ‘encounter’.”