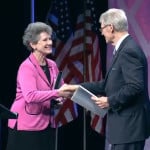
Last week, I posted a podcast with Mike George, founder of Strong America Now, an organization that is promoting Lean and Six Sigma methods to our political leaders and government. Much of the discussion, maybe unfortunately, was focused on Mr. George and his approach (“Lean Six Sigma”) rather than the potential for using Lean to improve the public sector.
Here, I want to share an excellent video of Karen Rago, a nurse and executive director with the UCSF Medical Center. She gives a 15-minute presentation on the use of Lean thinking to improve healthcare. This video appears on the Strong America Now website and I will embed it here.
At the risk of flaring up the Lean vs. Six Sigma debate, I found it interesting that Karen's intro said that one of the necessary factors were “Six Sigma skills,” when everything she presented and talked about was really just Lean, Lean, and more Lean.
That said, the work she presented was solid and was spot on in terms of Lean mindsets, including not using Lean to drive layoffs. The presentation was focused on improvement projects, as opposed to the ongoing management system of Lean, but it was good stuff.
The video, in two parts, followed by my notes.
Karen started by emphasizing that their “first obligation is to do no harm.” She talks, thankfully, about improving quality AND reducing costs.
Case study #1 – Stanford Hospital CABG surgery
- For Coronary Artery Bypass Graft surgery, the problem statement was that cost and mortality were too high
- They were breaking down silos to work together, from surgeons to housekeeping.
- Ideas brainstormed by front-line staff. Generated 130 ideas. Implemented 75%.
- Mortality fell 48%
- Cost per case down 40% over 3 years
- All 6 surgeons worked together in a room on standardizing the surgical pack (each had their own separate pack previously)
- Went though every single thing in that pack and got things to a single standard pack for CABG and a standard for valve surgery.
- Switching to less expensive but equally effective antibiotic
- Reduced unnecessary heard catheter usage by 25%, reduced risk and cost
She then talked about the Lean types of waste and explained what was necessary – a new way of thinking and getting EVERYONE involved.
Case study #2 – UCSF – Sterile Processing
- Problem – carts were inaccurate 28% of the time (surgical delays)
- Improved efficiency by 17%, reducing staff by 14 (redeployed, no layoffs). Quality of the process improved.
- Savings $1M in a vyear
Case study #3 – heart failure readmission reduction
- Medicare will stop paying for 30-day readmissions
- At the start, the rate was 22.6% rate, initial goal to reduce to 16%
- They worked on improved communication and collaboration across multidisciplinary team
- Rate fell to 11.6% in 2011, expect to get
I didn't see any mention or reference to anything I'd call a Six Sigma method. Lean is very powerful, especially when we have such gross waste in healthcare. Fixing things requires more teamwork than statistical analysis.
I'm glad that Mike George is putting time, effort, and money into spreading this message. The more our political class knows about Lean, the better.
Here is another lean healthcare case study that Karen wrote from UCSF.
Please scroll down (or click) to post a comment. Connect with me on LinkedIn.
Let’s work together to build a culture of continuous improvement and psychological safety. If you're a leader looking to create lasting change—not just projects—I help organizations:
- Engage people at all levels in sustainable improvement
- Shift from fear of mistakes to learning from them
- Apply Lean thinking in practical, people-centered ways
Interested in coaching or a keynote talk? Let’s start a conversation.
[…] ————————————— Source: via StrongAmericaNow.com Organization: UCSF Medical […]