“Progress isn't made by early risers. It's made by lazy men trying to find easier ways to do something.” – Robert Heinlein, American science fiction writer (July 7, 1907 – May 8, 1988)
With “kaizen,” the Japanese word meaning “change for the better” (and an improvement methodology), it often seems like a fine line between “lazy” and “efficient.”
The word “lazy,” has negative connotations, while “efficient” is positive. But one of the primary directions in the kaizen approach is to make improvements that make your own work easier.
In healthcare, making ones work easier might translate into rearranging supplies to reduce the amount of walking required. This frees up more time for patient care, which leads to better quality outcomes and shorter hospital stays – meaning a cost savings. So is “laziness” really that bad if applied in a good way?
My wife and I used to frequent a wine bar in the Fort Worth area (when we lived there before moving to San Antonio about a year ago). The staff who worked there were great and we enjoyed their weekly wine tastings, where five different wines were poured in succession, usually into the same glass (as opposed to a “flight,” where a wine bar might bring five different glasses at once).
As the waitstaff came through, part of their job was to remember which customer was having which tasting, #1 or #2. The staff might get tired of always having to ask customers “which tasting number are you having again?”
One of the staff members, Brandi, implemented her own improvement. She put a small number on the base of each glass with a washable marker, as pictured at the top of the post. This way, she didn't have to stop and ask anybody and she didn't have to be embarrassed by not remembering. She avoided the waste of pouring the wrong wine to the wrong customer (although, as a customer, this was a bit of a benefit, as you got an extra tasting).
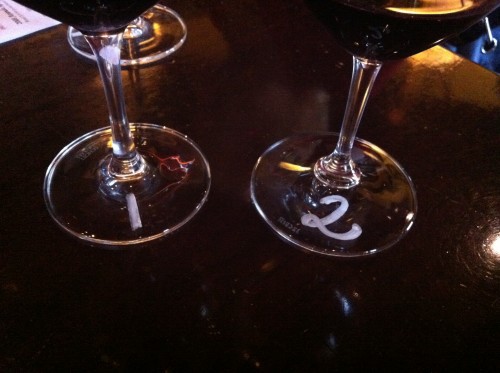
Brandi's improvement is a form of what we might call error proofing or mistake proofing, in the Lean management methodology, as it helps prevent errors. It reduces the risk of error, but it doesn't completely prevent her from pouring the wrong wine in the wrong glass. Still, it's better than the alternative of NOT marking the glasses. It worked for her.
When I talked to Brandi about her improvement, her response was a modest one, saying:
“Oh, that's just me being lazy.”
The wine bar didn't have a formal kaizen program, far from it. To me, this counts as “kaizen,” in terms of being a small continuous improvement, a change for the better, as we write about in our book Healthcare Kaizen: Engaging Front-Line Staff in Sustainable Continuous Improvements. This is also an example of the type of improvement that hospital staff might manage and share through KaiNexus, a software startup I am working with, although the system can help manage more complex improvements, as well.
In a more formal kaizen program, improvement involves a discussion between an employee and their supervisor. Especially in healthcare workplaces, kaizen is not a “just do it” system, where everybody just implements changes on their own. The discussion with the supervisor is an important part of the process, as the supervisor can discuss the idea to help ensure that there aren't any foreseeable side effects upstream or downstream or in other areas. The supervisor discussion isn't meant to be onerous and supervisors are supposed to work with employees to make sure most every idea (or some iteration of it) gets implemented and evaluated through a PDSA, or Plan-Do-Study-Adjust, methodology.
In the wine bar, this is an example of an individual kaizen where Brandi's improvement didn't have a negative impact on anybody else. They used an automated dishwasher, so the numbers didn't create more work for somebody else downstream (they are easily washed off by the dishwasher cycle). The numbering wasn't permanent, so it didn't increase the number of glasses they needed on hand. If there were permanently marked glasses, with the numbers etched into the base, they'd have to hold more inventory of glasses in case, for example, the #1 tasting was really popular one week.
Brandi didn't talk to her manager to get permission for this kaizen improvement – she just did it. One downside of not talking with the manager is that the idea wasn't necessarily shared with the other waitstaff, although they might have seen what she was doing and asked about it.
When there's a good kaizen idea, it helps to have a way of documenting and sharing that idea (via bulletin boards or web-based systems), to give recognition and to let her co-workers copy the idea if they want. There's no shame in “stealing shamelessly” when it comes to workplace improvements.
Brandi made her change, she tested it in use, and she confirmed that she made her work easier – for the benefit of her customers, herself, and the bar. That's PDSA and kaizen in action.
She might call it “lazy,” but I think it's smart.
You can also read comments from LinkedIn readers from March 2013 when I posted this there.
Please scroll down (or click) to post a comment. Connect with me on LinkedIn.
Let’s work together to build a culture of continuous improvement and psychological safety. If you're a leader looking to create lasting change—not just projects—I help organizations:
- Engage people at all levels in sustainable improvement
- Shift from fear of mistakes to learning from them
- Apply Lean thinking in practical, people-centered ways
Interested in coaching or a keynote talk? Let’s start a conversation.
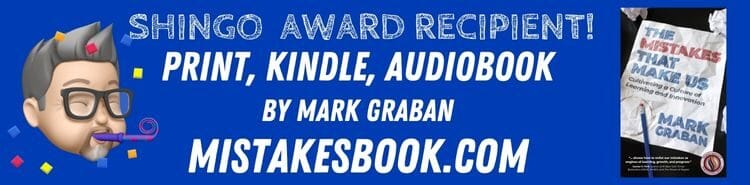
good post
Question from Twitter:
“Doesn’t the white marker impact the fine dining experience?”
No, honestly I didn’t notice the number the first time Brandi was doing that. One time, I did see it and I asked her if she just started doing that. She had been doing it for a while and I hadn’t noticed.
It’s a fairly subtle marking. It’s no worse than a wine bar that serves flights on paper labeled 1 through 5 or something.
I wonder if other customers feel the same way?
I like Brandi taking the improvement into her own hands. Small but effective. I like it. Creativity over capital.
Funny how Kaizen can make someone think they are being lazy.
It reminds me how I often tell my wife that I am not procrastinating, I am doing it Just In Time (then she reminds me of her “right time” verus my “right time”). :)
Good post.
I suggest a different attitude it is not being lazy rather it is working smarter instead of harder.
We may forget, but just about every innovation was created to make something easier. The only why people can actually do more is if you first make their existing work easier, and faster to complete.
Yes, I don’t think what Brandi did was lazy at all.
A big focus of kaizen is making your work easier, rather than a cost cutting focus. With kaizen, cost reduction is an end result, not a primary goal like some suggestion systems would be.
[…] also told a non-hospital story of Kaizen in a wine bar and the lack of kaizen at our county tax […]
Isn’t necessity the mother of invention? Where there is a need (in this case, for uninterrupted wine tasting) Brandi created a way to ensure her privacy.
Fun article!
[…] a few years ago, Mark Graban, author of Lean Blog, wrote about a wine bar server who developed an informal way to keep track of which wines were being …. This helped the server to reduce errors and be more efficient. The server called her method a […]