First off, I'm not trying to dredge up a “Lean vs. Six Sigma” battle here. I'm not “anti-Six Sigma.” I'm not a huge proponent of the methodology and I don't practice Six Sigma personally, but I see a place for a structured statistical quality improvement methodology to help solve certain complex problems.
What I *do* take issue with is the “Lean Six Sigma” community consistently misrepresenting Lean. I wish this would stop.
The “Lean Six Sigma” crowd seems to consist of a lot of Six Sigma “black belts” who have also adopted Lean. As an aside, you rarely see Lean practitioners rushing to add Six Sigma to their approach. There can be multiple interpretations of that, depending on your perspective. Now, organizationally, many hospitals use Lean first and then layer Six Sigma on top of that to help solve particularly sticky problems. That approach is reasonable, but what I mean is that fewer “Lean professionals” add Six Sigma to their personal repertoire than vice versa.
I believe that Lean and Six Sigma are two similar, but different, yet complementary things. I don't consider “Lean Sigma” or “Lean Six Sigma” to be a single comprehensive methodology. And I think that's more than just nitpicking over semantics.
“Lean Six Sigma” often gets explained like this (a direct quote from one communication I received recently):
- Lean is about Process Speed, Efficiency, and Agility, Improving the flow of goods and services with a standard and visible workplace
- Six Sigma is About Process Quality, Reducing Defects, and Variation, Improving the process to meet customer requirements
It's always a split of “lean is about speed and six sigma is about quality.”
This is factually incorrect, this notion that Lean is just about speed. It's incorrect to say that Lean doesn't address quality, both directly (through methods like error proofing and root cause problem solving) and indirectly (the improvements in quality that tend to come with better flow).
Look at the core, basic, fundamental roots of Lean, the Toyota Production System.
Illustrated as the “Toyota House,” it has two pillars:
- just-in-time (flow)
- jidoka (quality at the source)
With the rich history of Toyota/Lean methods for quality, such as poke yoke (mistake proofing) and the history of the pre-automotive era Toyota weaving loom that automatically stopped when the thread broke (read the history of jidoka on the Toyota website), you can't deny that Lean is about quality AND flow. They go hand in hand. Improving quality leads to better flow, better flow (through less batching) leads to better quality.
As one of the original Six Sigma gurus, Thomas Pyzdek, said on Twitter:
Quality is a result. Lean and Six Sigma are about identifying the critical drivers and root causes of quality results. It's not either/or, it's and.
Agreed, it's not “either or,” and when Lean Six Sigma people say Lean isn't about quality, they look silly and they do their followers no favors.
Does Six Sigma help improve quality? Well sure. Does Toyota use Six Sigma? No. Toyota uses the 7 Basic Q.C. Tools, which are:
- The cause-and-effect or Ishikawa diagram (fishbone)
- The check sheet
- The control chart
- The histogram
- The Pareto chart
- The scatter diagram
- Stratification (alternately flow chart or run chart)
Many of these tools and methods pre-date Six Sigma. They are included in even the most basic Green Belt education. Yet, they can be used without the formal Six Sigma methodology, as Toyota and many leading “Lean Hospitals” would practice.
I've read a book that was published earlier this year titled, Lean Six Sigma for Hospitals: Simple Steps to Fast, Affordable, and Flawless Healthcare. Sadly, the introduction to the book mentions nothing about Lean as a quality improvement method, nor does it talk about Lean as a management system. It's all tools and projects.
The most disturbing passage comes in the discussion of the “types of waste” — a concept that comes from the Lean methodology. The book seems to again imply that Six Sigma is what's needed for quality, as the first six types of waste (including overproduction, waiting, etc.) are the only things Lean addresses:
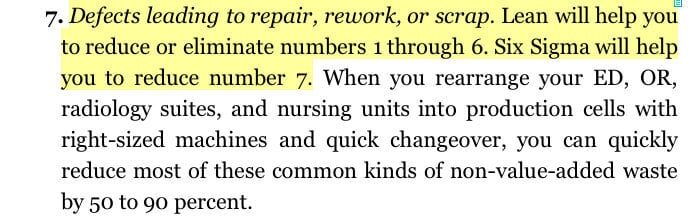
If the author doesn't mean to say that Lean doesn't impact quality, the section is poorly written and confusing.
I'm not sure where the “Lean Six Sigma” crowd got off the rails on their description of Lean. Saying or implying that Lean isn't a quality improvement methodology is L.A.M.E. — Lean As Misguidedly Explained. It's necessary to speak out, as too many are spreading the wrong message about Lean.
What do you think? Please scroll down (or click) to post a comment. Or please share the post with your thoughts on LinkedIn – and follow me or connect with me there.
Did you like this post? Make sure you don't miss a post or podcast ā Subscribe to get notified about posts via email daily or weekly.
Check out my latest book, The Mistakes That Make Us: Cultivating a Culture of Learning and Innovation:
I took a “Lean Six Sigma” course for Green Belts that was taught by a Six Sigma MBB (started with GE). He was quite brilliant and drilled into our heads that Six Sigma was about problem-solving, not reduction in variance. I had a whole new outlook on Six Sigma after the course.
Unfortunately, he completely misrepresented Lean and told the class that in a nutshell, it was all about VA vs. NVA. And that Lean lacked essential components like DMAIC (?). While he said Lean was “good”, his attitude toward Lean was almost condescending.
As a student of both Lean and Six Sigma, I often see instructors misrepresent or downplay the other school which is sad.
My Six Sigma instructor also downplayed Lean, but I imagine it was because he hadn’t been exposed to it in its full glory. I learned about Lean first, through visits to a Toyota supplier and Kaizen training while at Ford in the 1990s. Lean/Kaizen struck me as being the entire culture and way of thinking of the Toyota supplier. When I took a Six Sigma course in 2007, I felt it was less about culture and more about “black belts” coming to the rescue. I do think there is a place for Six Sigma where more complex analytical tools are required to solve a specific problem; however, I believe establishment of a Lean culture in an organization is the place to start.
Completely agree.. I tend to favor the lean side of the equation as a business leader. Mostly because of speed. Six Sigma tend to be long drawn out problem solving initiatives, but when trying to affect change rapidly kaizen and workshops (80/20) tend to bring more impact.
Re: Halden Zimmermann LSS graphic on the same…
https://rattlesnaketime.wordpress.com/2014/12/04/halden-zimmermann-lss-processes/
Also.. this is interesting.. different angle
http://thehaldenzimmermann.com/continuousimprovementcompanies/
Thanks, Thomas. I like how your diagram shows that “Lean Six Sigma” (altogether) can address quality and speed. Either Lean alone or Six Sigma alone should focus on things that matter to the customers and the business (not just cost) and the same should be true when the methodologies are combined.
An “authority” in my own organization recently contrasted Lean and SS by saying that Lean doesn’t have a focus on the customer.
I am continually amazed at Lean non-practitioners expounding on what Lean is or isn’t.
To say Lean is not customer focused is professional malpractice by that “authority.” That’s a version of L.A.M.E. I haven’t heard yet.
Great piece Mark! What I think may be partly behind all the misconceptions about Lean out there is that many people heard a very early sound bite about Lean (reduce waste, improve flow) and that’s where their learning stopped.
We in the Lean community share in this problem. Some of the earliest and most highly respected Lean books didn’t cover the full spectrum of Lean principles. For example, with PDCA not front and center, DMAIC filled a perceived gap that never actually existed. Same with root cause analysis and the other analytical tools that predate Lean but were always an active component. To this day, I can’t name a Lean book that has covered RCA adequately. Yet data collection and analysis is a critical component of the Lean work we do.
It almost seems like we need a “Lean Redux” book that takes a broad but more complete view of what Lean truly is. We need to do something to help people who are behind in their understanding catch up to where Lean is today.
That’s what we can do. Now here’s what the Six Sigma community can do. I see two fundamental and consistent flaws in LSS program curricula. First, the time allotted for Lean content is nearly always around 25%. So it’s no wonder many GBs and BBs don’t really “get” Lean. Five days of Lean does not an expert make. Not even close.
Second, I’ve yet to see LSS content outlines address the two core pillars of Lean – respect for people and continuous improvement – in any more depth than a mention, which explains why the Six Sigma portion of LSS is falling out of favor in many organizations. Without these two pillars in place, Six Sigma is nothing more than a traditional way to “force” an organization to change and we all know how that’s turned out.
I agree JM. It happens a lot. In software with Agile, Scrum, RUD, Kanban, EP, etc. The TOC people saying that they provide the focus for Lean and Six Sigma.
Joking, but some truth to this: “You expand/rely on what you are good at. My methodology is always the umbrella and it is what makes the others work. Also, consultants that sell culture get paid more than the ones that sell tools.”
I think all of us in Lean and Six Sigma must recognize this and accept the fact that we must be driven by what fits the customer’s culture and not be driven by our preferred method. We typically attract people that think similar to us anyway, so it seldom will be a loss of business.
Good topic, and very well put Mark. I enjoyed reading it. Thanks.
This is very true Joseph.
The book on Lean Software to which everyone refers suffers from exactly the same problem that Mark has identified – it’s Lean as viewed by a newly arrived practitioner from the Agile community, and seeing everything through an Agile lens. Lean is validated as being good because follows Agile practise.
Now that’s not a bad perspective for someone moving Leanward from Agile to have, and at their best, they have a lot in common (respect for people being a major one), but it really comes across as demonstrating limited understanding – it’s the “written from Cliff’s Notes” version. Lean Software is often now described as “Lean and Agile Software”, conflating two different but related methodologies just much as LSS does.
It’s a good start, but it needs an equivalent work bridging from Lean destination to balance it and disentangle the two.
Ron Pereira had a post like this a few days ago. Can somebody at HBS or Sloan write a book about all the different, entirely compatible and complementary continuous improvement methodologies in the world and please coin a new flashing name to call them by?
I tire easily of “true believers” who seem to think that their particular tool set is the only path to excellence.
What appeals to me about lean is the tendency to embrace a broad variety of tools from many sources within the underlying philosophy. What I dislike about lean is the tendency to insist on Japanese terms and origins for methods purely to gain cache’.
Anne Mulcahey, when she was CEO of Xerox, said in an interview in Financial Times: “Lean is an important nuance [to Six Sigma].” The misunderstandings run wide and deep.
Mark:
I think much of the misunderstanding about the central place of quality in lean arises because so many people latch onto it as a “cost cutting” methodology rather than gaining a deeper understanding of the whole picture: a comprehensive management system for improvement and organizational development, whatever challenges you face. I’m not sure six sigma ever aspires to be that. I’m not trying to start an argument, I really don’t know! Comments?
An observation you can find in the writing of some of the Toyota veterans out there is that “American Lean” has often missed out on “quality at the source” (or one of the many ways of interpreting jidoka). As you observe, it was always (since before they started making cars, even) central to Toyota’s approach.
You note that flow leads to better quality. It’s worth reflecting on how that happens: it makes defects easier to see, when they are coming at you one piece at a time, and easier to stop them before they go any further. That’s the beauty of the approach – all the tools and techniques of lean are about making deviation from standard more obvious to everyone. So all those “sigmas” are easier to see… no matter what methodology is used to root them out in the end.
So an alternative post title could have been:
Dear Some of You in the American Lean Crowd – Lean is About Quality, Too
I can understand how frustrated some of you feel. Lean has been minimized by the Six Sigma community as somehow being inferior for not making use of all the many non value added and infrequently required Six Sigma tools.
Likewise, the Six Sigma community would argue that they too are all about continuous improve, the customers (internal and external, and thereby are indirectly showing “Respect”).
I, personally, am method agnostic. Like a doctor who treats a patient at the right time, in the right setting, with the right method, I will use the best method, at the best time, to best solve the problem.
Can’t we all just call ourselves Demingites?
By the way, if you where to read “Increasing production, decreasing costs” by Charles Underwood Carpenter published in 1920. He talks extensively about reducing waste, improving quality, respect for people and ect. I often wonder if Deming didn’t get many of his ideas (beyond control charts) from Charles.
Hi Mark,
Good article. In my view there is more than enough waste / variation / defects in business, government and charities to keep all sides of the quality professionals occupied & employed for a long time….
Correction – a friend reminds me that, since 2009, Toyota Financial Services has had six sigma.
But it’s still correct, I believe, that Toyota does not use Six Sigma in their factories.
What’s the difference between using A3 & Statistical Process Control and using Six Sigma?
(For the sake of argument).
-Andy
I think, for one, a Six Sigma program is defined by the formal training and certification of improvement experts: green belts, black belts, master black belts, etc.
That’s a primary defining characteristic to me, in practice and attitude.
You can use SPC and A3 (and pareto charts and DOE) without it being a Six Sigma environment.
Hi Mark,
What is interesting for me is anecdotally Lean seems to really catch on where the work is more physical or visably based (e.g. manufacturing, distribution centres, hospitals, armed forces).
Six Sigma appears to be more heavily used in transactional or places where there is a strong data presence (e.g. Financial Services, Contact Centres, Telecoms).
I fully accept this is a generalisation – but I do wonder if this indicates where one methodology perhaps works better than the other.
Hi again Mark
I take your point – honestly I do – about the belt fetish and the cumbersome and unfriendly approach from Six Sigma.
It would be good if the absence of formal statistical training in many fields were acknowledged. It can be a daily battle to get people to understand concepts like normality, common causes, loosely correlated variables and trends, statistical significance and so on.
If I can wheel a person into a meeting with a colourful belt and a wizard’s cloak and say “This man is a Six Sigma guru and can tell you all about your data” it carries a lot more weight than your poor old Lean prac with his process maps and injunctions to respect people and so on.
It would have been good if the original Lean senseis had talked more about the contribution of statistics to quality – but being in a manufacturing, engineering environment I think they overlooked it as it was assumed.
In service industries, even in hospitals, you can’t assume it. As I said in my previous post, the number of doctors, even as high school graduates with applied mathematics, who don’t understand even basic statistics has to be seen to be believed. They assume epidemilogy is an obscure branch of medicine and they will learn the techniques if they ever need them.
Hi Richard,
This reminds me of something I concluded when learning my greenbelt. Our school systems did a good job in teaching us some really useful techniques (Pareto, Histograms, Scatter Charts etc). It takes about a week in work to forget the usefulness of them…..
This article in the FT today on statistics in the wider world maybe of interest to some readers!
http://www.ft.com/cms/s/0/dfe55458-ccb6-11e0-b923-00144feabdc0.html#axzz1VvwWmv3P
As humans we like to create convenient definitions to describe our range of skillsets. I use Lean Six Sigma in the same phrase not because I think one diminishes the importance of the other. Needless to say I have heard practitioners and consultants being equally dismissive of the other approach and arbitrarily deciding what comes first or what is more logical to use. The way I see it, they are synergistic approaches with Six Sigma adding more emphasis on statistics and Lean adding more emphasis on classical industrial engineering tools. I am a Master Black Belt but I bristle at being called a Lean Expert or a Six Sigma Guru- seems short-sighted to label yourself as a product that consultants have arbitrarily packaged over the past 30 years. In essence they are both elements of ‘Structured Problem Solving for Process Improvement’. Perhaps we should come up with a new acronym…’SPS’ anyone?
Yes, you and me on the same page. Michael Balle wrote ‘there is no expertise in Lean only experience’ and I think that’s partly where Mark is getting lost – don’t worry about the belts as such, but the expertise aka experience the person has.
Six Sigma tools do have so much to add to Lean when appropriate, the culture of ‘experts’ less so.
Lean had a couple of defects when it escaped from Toyota – fundamentally because it was not intended to be used outside Toyota:
a) its name was poor, non-descriptive and without clear boundaries
b) statistical tool base as standard (none of the muda, muri, mura, 5S content is statistical)
c) assumption about the way companies would hear/receive the message.
c) is very reflective of the insular culture. The story about Toyota’s brake problems with floor mats being a fundamental misunderstanding by the Japanese of the Americans’ desire to put mats in cars; this is similar to the fundamental misunderstanding of how the Lean message would be received in American/other companies.
I heard a former consultant out of Toyota recently say that he went to Ford from Toyota. He’d never heard of Lean because Toyota was his first job, he didn’t know other firms didn’t do things the way Toyota did. If TPS is all you’ve ever known, it would seem odd that the lessons of Lean are novel in other places, strange and possibly against the grain in other firms.
Richard – arguably, the thing that Toyota didn’t anticipate was that American drivers would stack multiple floor mats on top of each other – a fairly stupid and lazy thing to do. It wasn’t just “a floor mat.”
To their credit, Toyota has criticized themselves for not anticipating that drivers would do that.
As for getting off track, I don’t care about belts – it’s the six sigma organizations that often get very sidetracked on counting the number of belts they are training instead of looking at improvement. Or, they literally tell people that improvement doesn’t count unless it was part of a formally-chartered six sigma project. That’s an excess that should be avoided – the expert-driven improvement snobbery – whether it’s black belts, kaizen events, or whatever you would call it.
My connection with the “improvement movement” was via Lean rather than Six Sigma; however for me there seems to be a very critical distinction between the two approaches that goes beyond just any sort of allegiance to what I first came across.
Anyone looking at understanding my quick summary below in more detail than I am going to raise here might look at Marvin Weisbord’s superb Organisational Development text that he updated in 2004 and renamed “Productive Workplaces Revisited”. He looks at the history of consulting support offered to organisations and discerns too broad approaches. The one he calls “learning to do things to / for others” and is rooted in Frederick Taylors Scientific Management. The other is “learning to do things with others” and draws from and develops on the work of Kurt Lewin and Action Research. He traces this latter lineage through the work of OD and Organisational Transformation theorists and practitioners like Bion, Lippett, McGregor, Trist and Emery etc. The former is predicated on the expert telling the system the answer and ultimately limiting and even undermining the whole systems ability to learn. The latter is more about process facilitation – in so far as there is any expertise it is around facilitating questions rather than providing content answers. It is about whole systems learning where the essential orientation is developing the expertise of everyone rather than a few. There is a very critical issue here from an OD / OT perspective – namely “ownership”. And this connects to another important distinction very well articulated by Carney and Getz in their book “Freedom Inc.” – where they distinguish between organisations with employees that are self directed and those that at best are highly motivated.
My perspective on Lean and Six Sigma is that the latter’s DNA is very much of the expert / telling / learning to do for or to others. Lean on the other hand is about facilitating the whole systems learning rather than being predicated on a few experts (black belts and master black belts) telling people what they need to do – setting targets and the like.
If we are looking to build sustainable organisations that produced quality products and services that customers value in our fast passed and ever evolving environment we need to build organisations that Gary Hamel says “need to be as agile as change itself”. Organisations organise themselves around a distinction between thinking and doing – the expert who thinks and the others who do is not going to help us build these sorts of organisations. Six Sigma may help build short term returns for shareholders but in my view because it’s inherent DNA is about “learning to do things to / for others” rather than “learning to do things with others” it will not help us build the sort of organisations we need – and it seems to me as a process to ignore all the excellent evidence that exits around whole systems thinking and improving a systems performance.
And directly related to this – Six Sigma stories are often replete with stories of job losses and redundancies. The Lean stories are not – and if they are the lean community is very quick to tell them that they have misunderstood the fundamentals of lean. Lean requires a deep change of mindset amongst managers first and foremost – what H Thomas Johnson describes as moving from “Management by Results” to “Management by Means” in his book Profit Beyond Measure. I think Six Sigma is so readily taken up by traditional management because it does not require any fundamental shift in their basic assumptions (ala Edgar Schein) – which will consigns us to creating organisations that few people want to work in (see any number of employee engagement metrics – notwithstanding cohorts of managers working very hard to change) and which despite considerable effort managers seem very unsuccessful at changing (John Kotters, 1996 research and McKinsey & Co’s 2008 research).
Lean is more than a set of tools and it is that that distinguishes it for me from Six Sigma – and that distinction I think is one of fundamental importance – provide one thinks about workplace improvement beyond the simply transactional – i.e. improving shareholder value – to its wider stakeholder value and ultimately contributing to a better world than the one we currently have.
It is entirely possible that the tools of TOC and Six Sigma make a very important contribution to this – but if the system into which these tools are placed does not change we ought not to be surprised that any change effected is unlikely to be sustainable beyond the continued presence of overbearing leaders and will fail to tap into the full human potential our organisations are replete with.
Here is my 2 cents on the subject. MIT open courseware has a great free course on Lean. It is taught by experts in the aircraft manufacturing industry and the lecturer give the following contrast between Lean and Six Sigma.
Objective
Lean – deliver value to the customer
Six Sigma – deliver value to the customer
Theory
Lean – eliminate waste in the process
Six Sigma – eliminate variability in the process
Assumptions
Lean – waste removal will improve performance
– many small improvements are better than system analysis
Six Sigma – a problem exists
– figures and numbers are valued
– system output improves if variability in process decreases
Focus
Lean – flow
Six Sigma – a problem
I hope this helps.
Six Sigma in Medicine
3.8 Sigma = 99% correct
= 5000 incorrect surgeries per week in the USA
= 200,000 wrong prescriptions a year in USA
6 Sigma = 99.9997% correct (3 erros in a million tries)
= 1.7 incorrect surgeries per week
= 68 wrong prescriptions a year
Using 6 sigma to measure and track errors in my hospital is impractical. Take central line blood stream infections for instance. We have a very low rate of CLBSI. Only one infection in the last 2 or 3 years. We are a 180 bed hospital and have at most an averge of 7 to 9 people with central lines on any given day. Lets assume 9 people. That is 3285 patient days a year. To reach Six Sigma significance we would need roughly 304 years and expect 3 infections in that amount of time. Not a very practical measure for this and similar condition so we have concentrated on eliminating waste our processes and reacing to each unexpected failure.
Tom – I think the data shows, for one, how far most hospitals are from six sigma quality levels and, secondly, how “zero defect” through error proofing and other approaches should be the goal rather than any sort of “acceptable quality level” type rationalization.
The other problem with the six sigma calculation is the definition of an “opportunity.” “Defects per million opportunities” sounds as vague as “infections per 100 line-days.”
I’d nitpick with that MIT course comparison. Lean is hardly a numbers-free zone. Lean can be just as data driven as anything, but without the complicated statistics of Six Sigma.
I think Lean also addresses variation – maybe in different ways than six sigma. A big part of standardized work is the assumption that lower variation = better quality.
“Lean is hardly a numbers-free zone. Lean can be just as data driven as anything, but without the complicated statistics of Six Sigma.”
Mark, maybe you could have some content on your blog eg a podcast of someone who can give some examples of Lean with stats but without Six Sigma. I’ve never seen it.
I open my Womack and Jones or other texts I see very little on statistical measures of quality. If anything, it’s something I remember more from TQM, Deming and co.
Do the docs in your hospitals understand statistics? Would they be able to interpret changes in MRSA or surgical misadventure or ER waiting times correctly, concepts of statistical significance or random variation?
If you had 2 docs making different decisions about the same condition, put them into a 2×2 table and you told them the chi-squared and p values would they look at you like a madman?
I think we’re talking about two different things.
I’m talking about using numbers and being data driven in making decisions (such as how many emergency rooms to build and how many to staff each day) and using data to measure performance.
Yes, I’ve seen many hospitals using control charts to manage performance data to avoid reacting to common cause variation, etc. I’ve taught some hospitals how to do this. This is covered a bit in my book “Lean Hospitals,” for example.
You can be “data driven” without using chi-squared tests or complicated statistics.
So much of what we’re improving in healthcare is “low hanging fruit” that doesn’t require a ton of statistical analysis. But data and numbers are critical. We’re not just winging it.
Mark
I have to agree – particularly with the belt-focus. I see it in my own employer (and given that I’m about to join the LSS Deployment Team, I’m slightly playing with fire here), which runs a Lean Certification Scheme that’s entirely belt-based and linked to titles up to Lean Master.
Me, I’m happy with the title that aligns to their bottom level: Lean Change Agent. When I formally move over to the new role at the end of September, that’s what I’ll have on my LinkedIn profile. I’m happy to be a Senpai, not a Sensei.
I also see it in the thinking and the methodology. It feels very heavyweight, based on a series of structured workshops, with thorough data analysis in between. For some of the changes it sponsors (particularly the more radical changes), this is appropriate, but where are high volume of small changes with rapid feedback cycles of coaching that helps people actually splice Lean into their DNA?
Hi,
I have a slightly different view on the concept of belts & practioner levels.
For individuals personally I believe there is a motiviational benefit in recognising the accomplishment in sucessfully completing one of the training.
Another benefit is if you are recruiting a potential employee this helps (in the initial stages at least) frame what the potential employee should be capable of. There is a good analogy I use with accounting. If a candidate has passed certain exams this sets certain standards. You clearly need to ask further to see how their experience and application fits your needs.
I accept there is a flaw in the recruitment situation in that the quality of training (either six sigma or lean practitioner) varies by company and provider. I do not believe this helps methodology in general.
I have not experienced the “train X by Y” culture, but I could see how this is likely to be counter productive. Although this seems to be a management rather than anything related to the methodology problem.
Sick Sigmer, I mean Six Sigma, is all about one thing — cutting heads!!!
Mark:
Let’s come back to your original intent: not trying to start a Six Sigma vs. Lean vortex to be sucked into (again) but to observe that lean addresses quality concerns, whatever some people might say.
The core lesson of Toyota is to create an organization that drives improvement and solves problems. Some of the easily applied, reliable methods they use don’t require advanced statistics or statistical hypothesis testing, but clearly lead to improved quality of product and service delivered to the customer without them.
The thing I love about lean is that the same efforts that improved quality in our business were associated with ergonomics improvements, shorter lead times and reduced costs. It’s NOT either/or, speed vs. quality. Its “easier, better, faster, cheaper” (Shigeo Shingo).
For some consultants, Six Sigma is merely a set of quality management tools, statistical methodology and a form of employee certification that supposedly guarantees mastery of implementing Six Sigma principles. Though it is often the case that there is only really a rudimentary understanding of the tools and techniques involved that by itself, would be insufficient to drive real change. Even worse some consultants will try to train and certify your entire company, when only relatively few team-members ever really need to be to gain the best results. While most companies have attempted to implement some form of Six Sigma strategy, the actual bottom-line results in many cases have been disappointing.
Any tool is only useful when you know when, why and how to apply it.
Be it 6 Sigma or Lean, a hammer or a screwdriver, no one is better than the other, just more appropriate depending on what you would like to achieve.
I disagree that Lean is a “tool” to be used tactically and as needed. It’s really a philosophy and a way of thinking. Is Six Sigma the same? I’m not sure…
[…] That’s a good start realizing, correctly, that Lean is about both efficiency AND quality. […]
The power of lean tools drive the most impact when used in commercial facing processes. Typically lean is only thought of in mfg environments and few leaders pick up that the same tools are even more powerful in driving revenue and profit instead of cost out situations. Very few companies look at lean this way and are missing a huge opportunity.
Ref the guide below written a while back for the LEAN BUILDING BLOCKS (or roadmaps), it may be harder to see…. but at the bottom basics are roadmaps around mfg, at the very top, where the most impact is are the customer facing ones. Of course if you cant do the basics like 5s and Policy Deployment those may be a challenge to start with but you can see customer is a major part of a lean framework.
Re: halden zimmermann continuous improvement white papers attached:
https://rattlesnaketime.wordpress.com/2014/12/08/halden-zimmermann-building-blocks/