Mark's note: I'm happy to have a new guest blogger, Dr. Wiljeana Glover, from MIT, and a fellow member of the Society for Health Systems. The plan is that Wiljeana will be a regular guest blogger here.
Greetings to the leanblog.org community. Â My name is Dr. Wiljeana Glover and I am currently a Postdoctoral Research Associate at the MIT Lean Advancement Initiative. My current research interests include healthcare systems, improvement sustainability, and management innovation. I look forward to sharing some of my research topics with the community from time to time and getting your invaluable feedback. Â I'd like to especially thank Mark for giving me this fantastic opportunity to share with you.
With the increased use of lean work system practices in recent years, many organizations are using various improvement approaches, including Kaizen events, to rapidly introduce change and to create a culture of continual improvement (or kaizen). Unfortunately, as many of the readers of this blog know, improvement approaches are often used ad-hoc, as opposed to systematically.
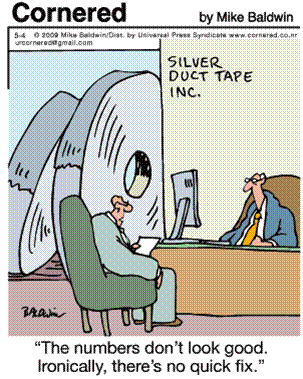
Solely using Kaizen events in an ad-hoc fashion = working at Silver Duct Tape, Inc.; A lack of Planning, Sustaining, and Supporting.
The ad-hoc use of Kaizen events may yield a varied implementation approach as well as varied outcomes and attitudes toward improvement (e.g., “This is just the flavor of the month”). And while it may seem intuitive that designing and implementing a Kaizen event program may promote more systematic use, there are many challenges to creating a Kaizen event program. For example, despite the focus on improvement systems in the lean and continuous improvement resources, most Kaizen event publications emphasize individual event success. Â Thus, organizations tend to lack adequate guidance for integrating multiple events over time in a systematic fashion, i.e., within a Kaizen event program.
Having a framework that systematically organizes practices, combined with a consistent and structured assessment approach, allows those involved with coordinating improvement programs to better design, execute, and refine these programs. Â The work of Dr. Eileen Van Aken and colleagues (including me) describes one such cyclical framework with four stages, A. Plan, B. Implement, C. Sustain, and D. Support (Figure 2).
The first process area, A. Plan, occurs at the strategic level of the Kaizen event program and is intended to provide the organization with a sound approach for identifying potential Kaizen event candidates, defining a portfolio of Kaizen events sequenced within a work area or synchronized across different work areas, and developing the initial scope and project charter for each selected event.
B. Implement includes the implementation of the Kaizen event program, as well as the detailed planning and implementation activities for each individual Kaizen event and focuses primarily on effectively completing a specific event and its follow-up activities.
C. Sustain focuses on the use of different mechanisms intended to increase the probability that changes enacted and improvements realized from an event will be sustained and shared over the long-term.
Finally, D. Support processes are intended to create an organizational infrastructure to promote and support the Kaizen event program.
This framework, whose structure is supported by the PDSA cycle and the CMMI, was originally developed  within the Belgium Armed Forces, but it would be generalizable to the healthcare industry.  And although this framework is focused on Kaizen events, it could be extended to other types of improvement programs.  A more extensive description of the framework is available at the International Journal of Productivity and Performance Management.
I hope that this framework is helpful for your organization. Â And whether you use this framework or another program approach, I'd like to ask [in the context of healthcare systems]: Â What are your major difficulties with creating a systematic approach to Kaizen events? Â What are some of your success stories in making your own “framework” successful? Add a comment, below.
Please scroll down (or click) to post a comment. Connect with me on LinkedIn.
Let’s work together to build a culture of continuous improvement and psychological safety. If you're a leader looking to create lasting change—not just projects—I help organizations:
- Engage people at all levels in sustainable improvement
- Shift from fear of mistakes to learning from them
- Apply Lean thinking in practical, people-centered ways
Interested in coaching or a keynote talk? Let’s start a conversation.
Hi Dr. Glover,
Your post rings true. We must distinguish between tool-driven, system-driven and principle-driven kaizen. Tool-driven is essentially “ad hoc,” as described above, while system-driven is typically directed by value stream improvement plans and the like. Principle-driven kaizen represents the gold standard of kaizen and is characterized by system-driven kaizen PLUS daily kaizen as conducted by an engaged and empowered workforce.
Thanks for your comments, Mark! I especially like your description of principle-based kaizen.I feel as though Kaizen events get an especially “bad rap” because of this issue.
As an aside from some of my recent observations, it appears as though improvement efforts in hospitals are almost divorced from the hospital operations, such that the managment/improvement engineers are not a part of the overall strategy and operations, but this group that gets called to fire-fight when something is “broken.” I think better understanding of how lean/improvement efforts are implemented to achieve principle-based kaizen within the context of the organizational strategy, operations, etc. is needed.
Great job and I agree in theory. Flow charts always look good on paper. Implementation requires tact, charisma and true leadership. Resistance is similar to pain in the body, its needed to alert you of possible problems. Too often we implement these programs in a cult like fashion promising the cure to all problems. Anyone not in total agreement is a rebel. Let the people have a part in forming the vision. Align their tactical vision (ideals) with your strategic (vision) and that will create true synergy. Let people know the system is never perfect that is the reason for the term continuous improvement. This will lesson the frustration in change management.