Hello from the frozen tundra of North Texas. I wish the Packer fans hadn't brought Green Bay weather with them. It's not nearly as green as that picture of “Jerry World” (aka Cowboys Stadium) looks.
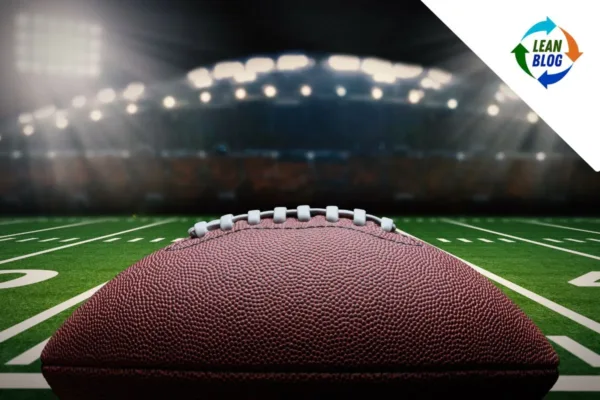
Back in 2008, I blogged about how NFL footballs, including those specially made for the Super Bowl, are made in America – the Wilson football factory in Ada, Ohio. I wrote how I hope the production doesn't get outsourced to China… well, as of 2011, it has not. And I hope it stays that way. ESPN has a new feature (including a video) by Paul Lukas from the “Uniwatch” Blog.
One reason the production hasn't been sent offshore is that the Super Bowl footballs are produced right after the teams are determined – that's well under a two-week lead time. I guess footballs could be sent via air the way iPads and iPhones are – but I think it's great to see what work being done in Ohio.
From the ESPN piece, about the quick-response manufacturing:
“Wow,” I said to Molly Wallace, the Wilson publicist who was explaining all of this to me, “so I guess your football factory must be hopping on the Monday after those games.
“Oh, they don't wait until Monday,” she said. “A work crew shows up at the factory during halftime of the second game on Sunday. They have some pizza and soda on hand and make a little TV party out of it. Then, when that game is over and we know who'll be playing in the Super Bowl, they start making footballs.”
“Wait a second,” I said, checking the playoff schedule and doing some quick math, “that game won't be finished until about 10 p.m.”
“That's right,” Wallace said. “They work all night, until five or six in the morning. Then a new crew comes in to take over for them.”
Now, is this a “lean” factory? There's no evidence that they use Lean methods at all. We could nitpick and point out inventory and inspection and maybe some manual work that's not great from an ergonomic standpoint. If you want to draw a value stream map, have at it :-)
What stood out to me in the article and the video:
- The longevity of the employees. 29 years for the Plant Manager, 30 and 40+ years for many employees.
- The pride that people have in their job, their purpose, and their role in the games.
- I'm surprised the footballs are turned right-side out by hand, as Paul Lukas was!
- Old equipment, “but it works” as one employee said in the story. There's a real tradition in many Lean factories of making your own equipment to meet your own specific needs and uses. If you maintain the equipment, you can keep it in working shape for a long time.
Paul Lukas also shares some additional photos on his blog post about his visit.
What struck you about the factory?
Please scroll down (or click) to post a comment. Connect with me on LinkedIn.
Let’s work together to build a culture of continuous improvement and psychological safety. If you're a leader looking to create lasting change—not just projects—I help organizations:
- Engage people at all levels in sustainable improvement
- Shift from fear of mistakes to learning from them
- Apply Lean thinking in practical, people-centered ways
Interested in coaching or a keynote talk? Let’s start a conversation.
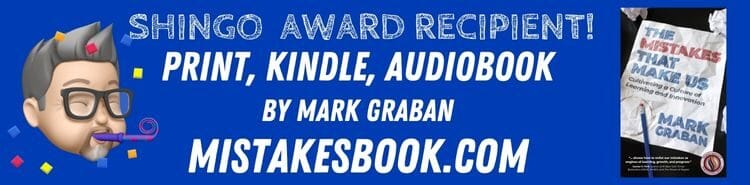
[…] This post was mentioned on Twitter by Garments Engineer, Lean News Feeds. Lean News Feeds said: From LeanBlog Super Bowl Footballs – Made in America (Ohio!): Hello from the frozen tundra of North Texas…. http://bit.ly/dZ8m7A #lean […]
I had seen a similar, but different video just a couple weeks ago:
http://twitter.com/#!/scottsorheim/status/25973855633801216
and what stood out to me was similar: some unbelievable years of service–employees must enjoy working there, and “Emmitt” in the video I saw was turning the balls inside out for 20-some years. His forearms were like Popeye’s! As you mentioned, a possible ergonomic problem.
It’s interesting to see two different videos about the same plant and how many of the employees in each of the videos have employed so long there.
Thanks for sharing that video. I see lots of batching and what looks like functional process islands. Nothing close to cellular production, eh?
Yeah, it’s hard to get the whole picture from the video, but there’s not an immediately obvious reason why every operation seems to be isolated.
I agree with the comments re batch and isolated operations. They really should look at a team concept and run single-piece flow which would get rid of all the non-value-adding handling (significant in these labor-intensive operations) and also thereby introduce the concept of staff doing then multiple jobs for less repetition and better ergonomics, and in my experience, greater job satisfaction. There is also available electronic leather-cutting equipment versus the manual clickers being employed. Basically an individual marks off bad spots in the leather, the hide is scanned electronically and those spots recorded in a digital image of the hide, and the leather then is cut automatically (avoiding the bad spots), while the staff preps the next hide for loading. It takes a tedious physical job and makes it a brain-based task (worth more) better for the individual while also using leather better (the major cost) and cutting at lower cost — so everyone wins. This eliminates the need for metal dies as well. One such machine is even made in the US in CT, an added win. And there are better ways to set up the manual turning job (one approach being to just set the turner horizontally versus vertically so you can use your legs and full body on the turn versus just your arms and shoulders which is very taxing and not good safety-wise), including use of some pneumatics to assist the effort. Their approach to stamping balls is good with the indexing rotary table with no doubt multiple stamping heads (not shown) so there is one load, one unload.
I have worked on baseball glove projects (tougher than footballs) in process improvement where we have run single-piece flow in small teams doing everything after cutting-stamping which has to be centralized because of high investment in the best equipment (clickers you can put right in the team but stamping would be expensive to decentralize). But they then could sew, turn, install the bladder, inflate and test, check 100%, and pack in one continuos flow by multiple small teams. And teams then really get involved in taking that process to ever better levels as in a small group effort, individuals can really have input and effect. And productivity is typically improved by 50% so the same group can do more and win ever more market share.
You always worry when a company is doing batch work in a less than effective process that it is setting itself up eventually to lose those good-paying U.S. jobs to offshore, driven by the management’s or its customers desire for lower costs. We can compete here but we need great lean processes, continuous improvement, and employee involvement in making things better and better. With air shipping today even on quick turns we are not immune from overseas. I like the idea of these balls still being made in America and not even in Latin America where you can make and ship today as quickly as from Ada, OH.
Len