There's a long-standing argument that I've been dragged into with a group that calls itself “new systems thinkers.” They loudly criticize Lean as being altogether awful (with the alternative, predictably, being their services). One of them wrote a blog post about why nurses should reject lean – you can likely find it via this Google search).
I agrees strongly that sometimes Lean is “done badly” — these are instances of what Bob Emiliani calls “fake lean” and what I've dubbed “L.A.M.E.” This anti-Lean crowd says the existence of anything that's done badly in a so-called “Lean implementation” proves that Lean itself is inherently bad. I think that's hogwash and this post will explain why.
I've written many times on this blog about instances of companies saying they are “doing Lean,” but it turns out they are doing any number of “L.A.M.E.” things including:
- Ignoring Toyota's “respect for people” principle
- Using Lean to drive layoffs or short-term cost cutting
- Not focusing on quality as a primary goal
- Not engaging front-line staff and managers
- Using Lean tools while ignoring the management system and culture
- Being top-down and coercive
L.A.M.E. things have happened in manufacturing companies, accounting firms, and sometimes hospitals. It's unfortunate when these things happen and it reflects badly on those leaders and organizations that are learning how to change their management system – those who are doing Lean the right way.
The real power of Lean is, of course, not the tools – instead it's the management system and culture, as described in great books like Creating a Lean Culture and Toyota Culture: The Heart and Soul of the Toyota Way. The mindsets, philosophies, and management methods in that book are transferable across different industries.
For example, Eric Ries talks about not blaming software developers and using PDCA improvement cycles in his “lean startup” movement. John Toussaint MD talks about the shift away from “naming, blaming, and shaming” as the old predominant culture in heathcare – and they are changing that culture at ThedaCare in Wisconsin (as told in On the Mend: Revolutionizing Healthcare to Save Lives and Transform the Industry).
The traditional organization is often top-down, coercive, and fear-based. This is, sadly, often true in hospitals (or it's worse than it might be in a typical modern Western factory). When top-down organizations try to force Lean tools at people, we can't expect much good to occur.
One could argue, with all of the great books and resources and consultants out there, that senior leaders need to be held accountable for not learning what Lean is really about (management system, philosophy, and culture change) or for not wanting to change.
So back to nursing — the best of the hospitals implementing Lean realize that it's about new ways of seeing work, being more customer (patient) focused, and engaging every employee in quality and process improvement.
Are there likely going to be L.A.M.E. cases where senior leaders continue to be top-down and coercive? Probably — not every leader wants to change (as John Toussaint and others have) and it's tempting to just throw new tools at people, expecting a quick fix that's not likely to happen. For Lean to work, leaders need to change so they can change the culture to something more constructive. Sometimes, that change takes time – people and organizations don't die overnight. Old habits die hard.
Some specific examples of what I'd consider to be “L.A.M.E.” in a hospital:
- Having dedicated process improvement people following nurses and doctors with stopwatches
- Giving medical professionals quotas for how fast they have to work, regardless of patient needs
- Getting rid of materials to have “just in time” inventory, but not having a properly working system that ensures supplies and meds are always available
- Telling medical professionals (or any staff) how to do their jobs (top-down standardized work)
- Laying off people after a Lean improvement effort
- Telling nurses how many pens they can keep at their desk (while patient care suffers)
Nurses should be opposed to all of that. I agree with the “new systems thinker” on that note. Nurses deserve a better workplace and they deserve to be respected and properly supported by doctors and administrators.
But the difference I draw from the Lean critics:
- They see L.A.M.E. and leap to the conclusion that Lean is inherently bad. They throw Lean under the bus and take the tone that these leaders are “idiots.”
- I see that Lean works well when leaders learn about and embrace the full management system. I work to try to educate healthcare leaders who are smart, but have a different viewpoint on management.
When it's really Lean, and not “L.A.M.E.”, nurses should be demanding more Lean. For example, the nurses union in New Brunswick, Canada, came out in strong support of Lean. That's because Lean was being done the right way – of course they wanted more of it.
Why would nurses WANT Lean? When organizations really embrace Lean:
- Nurses say, “Finally! Management is seeing the problems we face every day and we're going to work together on fixing things.” Instead of feeling neglected, they are being properly supported and involved in process improvement.
- The culture changes to fix routine “Every Day” problems – instead of jumping through hoops and constantly fighting the same fires, they get to focus more time on patient care.
- Lean helps support save care – proven documented examples include reduced patient falls, fewer infections, and fewer cases of V.A.P. — nurses want the best for their patients.
- With Lean, the space is designed and sized to match the processes for nursing care, instead of nurses being forced into spaces that don't have enough bed/equipment storage space, for example.
- They get to design their own standardized work and can improve it through daily huddles and kaizen boards.
- The nurses get to work as part of a team (such as ThedaCare's Collaborative Care model, where the RN helps direct doctors and pharmacists.
- Nurses work less overtime because they have more time during the day to do proper charting instead of batching it at the end of the day.
To those of you with nursing backgrounds, what would you add?
The culture and management system have been clearly defined in the Lean literature – the abundance of books from Jeff Liker, for example, and others. I humbly submit that my book tries to cover these same themes (and has been endorsed by Liker, David Mann, and others I consider experts on Lean management).
Please scroll down (or click) to post a comment. Connect with me on LinkedIn.
Let’s work together to build a culture of continuous improvement and psychological safety. If you're a leader looking to create lasting change—not just projects—I help organizations:
- Engage people at all levels in sustainable improvement
- Shift from fear of mistakes to learning from them
- Apply Lean thinking in practical, people-centered ways
Interested in coaching or a keynote talk? Let’s start a conversation.
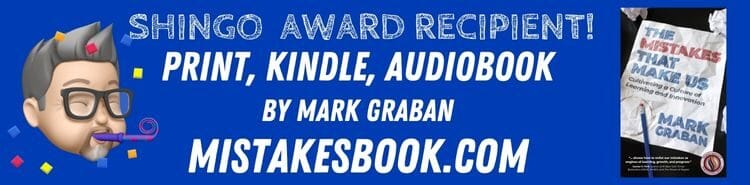
Mark – I find that many of the systems thinkers are simply re-stating the 100-year old arguments against progressive management commonly put forth by workers and others (e.g. “standardization is bad because our work is highly varied”). As you note, it is in their interest to do so, whether they believe in the old arguments or not. Nurses won’t demand Lean management until they clearly understand the differences between REAL Lean (CI+RP) and Fake Lean / L.A.M.E. – something the Lean community has utterly failed to do over the last 30 years, and hence has given a large opening to many other different management ideas and practices (most of which are zero-sum).
The criticisms and arguments against Lean are a natural consequence of two things: not knowing the difference between zero-sum (win-lose) and non-zero-sum (win-win) management practice, and competition among similar ideas (e.g. Lean vs. system thinking) or ideas that appear to be similar (e.g. LeanSixSigma). If Lean expects to win the competition, then we need a massive effort by all in the Lean community to persistently knock down each of the 100-year old arguments against progressive management and make totally clear the differences between REAL Lean and Fake Lean / L.A.M.E.
For going on 15 years now, REAL Lean has been the focus of all of my books and nearly all of my papers. Your vigorous efforts to promote REAL Lean, both in-person and on LeanBlog, are laudable. But you and I, and a few others, can’t do it alone; we need a lot more help.
I would imagine that your reference to labor versus progressives would include the infamous ‘Watertown Hearings’ which used the forum of a congressional hearing to rail against Frederick Taylor’s Scientific Management methods.
One interesting snippet from Taylor’s own testimony:
“Scientific Management is not any efficiency device, not a device of any kind for securing efficiency; nor is it any bunch or group of efficicncy devices…..
…It’s goal is a mental change in managers and workers with the substitution of hearty brotherly cooperation for contention and strife; of both pulling hard on the same direction instead of pulling apart…”
Post-Victorian style aside, those were lofty goals for those in business in 1912 and they still seem viable 98 years later.
Mark- great post.
That is indeed a modern-sounding quote from Taylor. Bob Emiliani shared another article recently with me where Taylor sounded quite modern and quite “lean.” I’ll blog about it soon.
Great topic. Excellent post.
Too many thinkers, not enough doers.
Reminds me of the common reference – “I’m seeking job/career satisfaction”. What a great way to describe “Retired in the job”.
I know of no right minded, high performance pro who is ever satisfied. To be satisfied is to eliminate the yearning, hunger, and thirst for achieving seemingly unattainable goals (the best).
I realize this mindset is not baked into the culture at most companies. Perhaps it’s fried at others. Point is, we’ve just scratched the surface of the potential of lean, not only inside companies but inside us.
Instead of “new systems thinkers”, best starts working on new job design schemes that fit better with lean methods and practices.
jim
OK, you have nursing leaders with hundreds of barely functional and many disfunctional processes that affect patient safety every single day and how is lean going to help them? Nursing leaders were trained to survive in such an environment by putting band-aides and another educational module on the really severe failures and sweeping the rest under the rug. A key for the lean facilitator is to stay engaged with nursing leaders long enough and “fix” enough problems that they can see that they don’t have to live in environment that accepts patient harm as the cost of providing care.
To Anonymous – you’re right, that lean facilitators (and the hospital leaders) need to be engaged so they can actually change the culture. If lean is “just one more thing” for the nursing leaders, then it’s not likely to go very far. If lean is a method and a culture to help eliminate causes of harm and a way to free up time from managers not having to fire fight as much, maybe then lean will be seen as a positive.
Mark –
If a Health Care organization is seeking outside help with Lean how do they distinguish between L.A.M.E. and “real lean” services? What kind of questions should be asked to uncover L.A.M.E.?
This leads me to another questions. Does L.A.M.E. happen because of bad advice or because Leaders are not willing to change their thinking? In other words, is L.A.M.E. based on customer demand? Interested in your thoughts.
Thanks,
Holly
Holly:
Your first question is an important and difficult one. Setting it in a classic lean frame, I’d ask: What is the standard for REAL lean? How do we measure against it? And most challenging, how can a leader just setting out and trying to select teachers/consultants/mentors be qualified to make that assessment?
I agree with Mark Graban and Bob Emiliani that reading is important, and Bob sets out some good screening questions, but I don’t think that’s enough (I’m sure they won’t disagree). What else to do? You can read John Toussaint’s book, but you also have to do what he did: go experience lean. To really grasp the standard, to understand what they are getting into, and to make better decisions earlier in the process, leaders have to go see what other organizations are doing. Hook up with a network of lean thinkers (any industry – snowblowers did it for ThedaCare!); participate in a lean healthcare summit; tour organizations that have begun to change (the further along, the better). The experience of a REAL Lean organization is palpably different, and if the path a teacher or consultant is offering doesn’t appear to lead in that direction, then keep looking.
And don’t marry the consultant! If it isn’t working, keep studying, networking and teaching while looking for new teachers. Always checking against the standard and adjusting the plan as we go. Knowing that there was something real out there (based on our reading, study, and networking) has been vital to me leading our journey as we coped with and recovered from mistakes and misdirection.
And to your second question, I’d say that L.A.M.E. is often a response to customer demand. There will always be demand for easy answers. To paraphrase Dr. Deming: Success is optional!
Holly – These are excellent questions. You would have to closely examine the offerings of the trainer or consultant to see if they present Lean as a bunch of tools (Fake Lean / L.A.M.E.), or do they present it as a non-zero-sum principle-based management system – “Continuous Improvement” and “Respect for People” – focused on creating value for end-use customers and eliminating waste, unevenness, and unreasonableness using the scientific method (REAL Lean).
How does the trainer or consultant understand and present the “Respect for People” principle? Is people just employees, or is it all five key stakeholders: employees, suppliers, patients (customers), investors (payers, etc.), and communities. Is it zero-sum (win-lose) or non-zero-sum (win win). Do they understand the relationship between “Continuous Improvement” and “Respect for People?” (see http://www.bobemiliani.com/oddsnends/cirp_matrix.pdf). Do they strongly promote the three signature characteristics of Lean: application of the “Respect for People” principle to all five business stakeholders; qualified job guarantee (i.e. no layoffs due to kaizen), and quarterly profit sharing?
Fake Lean / L.A.M.E. happens both because of bad advice from trainers and consultants, and leaders who are unwilling to change their beliefs, behaviors, and competencies. To a great extent, Fake Lean / L.A.M.E. is based on customer demand; demand for rapid improvement that delivers quick cost cuts – which shows a fundamental misunderstanding of Lean, whose purpose is to grown and improve to better satisfy customers, not cut. Historically, managers have cherry-picked Lean tools to achieve their cost-cutting goals, and thus rarely move beyond Fake Lean / L.A.M.E.
Healthcare organizations, and anyone else, should be extremely discriminating in seeking outside help. On the other hand, they can do a lot on their own and perhaps avoid those who present Lean as nothing more than a bunch of tools to cut costs. Please consider reading my books and published papers on this topic, the latter are posted online and can be downloaded for free (http://www.bobemiliani.com/publications.html). This knowledge will enable you to better judge the offerings of trainers and consultants, and also help you improve your own practice of Lean management.
Please add Rother’s TOYOTA KATA to the list of books that have a good definition of a Lean culture and management system.
For Holly’s question, sometimes the answer is “in-between”.
As a consultant, I hope I am giving good advice but my clients in leadership are not always ready to change. So there is sometimes a dance where some good lean stuff is done on the floor but there isn’t Lean management to support it yet. While it is currently L.A.M.E., leadership is learning and I am consulting to help them get to “real lean”. I don’t think we should call L.A.M.E. defeat too early while the leaders are still learning.
Lean tells us to use long-term thinking. Don’t throw in the towel if you aren’t at “real lean” in the short term!
I really enjoy this discussion and I am very happy to find people facing the same challenge.
Explaining leaders the difference between fake lean / L.A.M.E and real lean I figured out that the scientific definition of success might help to explain the real idea of lean.
By definition success means “efficient effectiveness”. Every Leader want to be successful.
The efficient component of lean is easy to explain and to understand “continuous improvement” (with kaizens).
The effective component of lean is “respect for people”, at least in my opinion. Understanding value in the eye of your customers. Defining your value stream. If necessary do Kaikaku and turn the whole company into a better direction. Even give your employees a vision that is alive even if you overtook already your competition – perfection.
I tried to express this in a picture at my lean-interim.com blog (most stuff in German, sorry, use google translate): What is Lean?.
I really like what Peter F. Drucker said ones: -žThere is surely nothing quite so useless as doing with great efficiency what should not be done at all.”
But in real world it seems that doing things right is easier than understanding and doing the right thing.
Thanks for all the great responses. Lots of good ideas and insight. Especially appreciate the “go see” advice Andrew posted.
Speaking of Andrew’s post, I’m intrigued by one of his questions, “What is the standard for REAL lean?” There are many opinions of what real lean is, but is it possible to create a standard? Or does each organization starting their lean journey create their own standard?
Each organization or leader sets their own standard, I think. A standard isn’t something absolute, in the sense that I’m using it here, but best current understanding in local context. It develops with your study, training, and practice. It should change over time as your understanding deepens and you raise the bar.
There are, of course, things like the Shingo Prize Model, but they shouldn’t be taken as absolutes, in my opinion, just more information. Every application is unique. While it plagues us at times that there isn’t a single, trademarked, reference point for “lean”, it’s really a good thing, I think.
All of that said, there are some pretty explicit hallmarks. As Bob Emiliani remarked above, a framework for continuous improvement and respect for people represent a strong consensus view but this is so general as to be difficult to apply and frustrating to someone wanting help starting out. You could build up all the detail from those foundations, but they are both deep, rich subjects. In any event, the details of the original post, the specific L.A.M.E. experiences in healthcare that Mark outlined, do not test well against this simple framework.
[…] [1] All quotes attributed to “Mark” are from this post, used with permission: https://www.leanblog.org/2010/11/why-nurses-should-reject-lame-and-demand-lean/?utm_source=feedburner… […]
Thanks to everyone for the thought provoking comments.
To Holly’s question – I think a lot of this has already been answered well, but “L.A.M.E.” consultants might do things like:
1) Emphasize cost savings through headcount reduction
2) Emphasize anything “fast” and “easy”
3) Not teaching people (breeding dependence on the consultants)
4) Have a “cookbook” approach to lean that’s not flexible or adaptable
5) Have a dismissive attitude toward employee input
6) Not teach anything about culture and management system (tools only)
Great post, Mark (and great comments on the “new systems thinking” blog post as well).
One of their earlier posts mentioned that, “How did Taiichi Ohno (the man who created the TPS) teach people? Did he give them tools to solve problems they thought they had (as the lean tool-heads do?). No, he taught managers to study their work as a system, his favourite work was ‘understanding’. That’s what Systems Thinking does, it starts with studying.”
With this point, it seems as though the author is stating that “understanding” or “studying” are common across both approaches, which appears to support, not oppose, the relationship between lean and “systems thinking.”
In any case, it is easy for organizations to have unsuccessful lean implementations and anecdotally place the blame on lean instead of identifying a root cause (e.g., lack of CI+RFP), thus giving lean healthcare a bad name…proponents of lean may be able to counteract this by not only stating how successful they are now, but also regularly describing how they’ve experienced challenges along their lean journey (e.g., due to a lack of CI) and how they overcame those difficulties.
Without respect for people you are not practicing lean. Unfortunately many things calling themselves lean are not (this is the same as things calling themselves TQM, quality, six sigma…). Adopting the name of a management system and not much else shouldn’t tarnish the management concept but it does for many people.
Respect for people makes an organization more effective. It also is something I personally care about. Those are 2 different things. It happens to be nice for me that what I believe in, also has shown to be a good strategy. I don’t know what I would do if it turned out a good strategy to manage was to eliminate joy in work. Luckily I don’t have to make that decision.
The power of lean and Deming’s ideas to provide people better lives i what makes me care so passionately about helping encourage adoptions of these principles (the real principles not just saying “Lean”). http://management.curiouscatblog.net/2010/10/14/positivity-and-joy-in-work/
Here’s an unfortunately example of, I’m sorry to say it like this, some blatant idiocy on the ‘new system thinker’ blog.
I’ll link to them since a comment link doesn’t help their SEO:
http://blog.newsystemsthinking.com/why-nurses-should-reject-lean-in-hospitals/comment-page-1/#comment-871
Asked about the use of “quick changeover” in healthcare, I responded about how it helped prevent delays and improve O.R. utilization (something that doesn’t harm patients in the least) and they say:
That was the comment even after being provided with information about the practice related to O.R.s. This group is blinded by a narrow view that lean is inherently bad.
Mark – couldn’t help checking out that guy’s blog site – and I have one word: scary!. Not sure exactly what his motive is or what brand this guy is selling, but what I am sure of is, he sure has no idea what he’s talking about…
Can anyone advise what to do when the Lean culture of single small steps of continuous improvement is what you want, but you walk in as a lean professional and see a process that is just about pure waste, producing very little of any real value to anyone?
Do we set them on the journey of continuous improvement, or shut them down and let the cards fall where they may?
Lean activity can be wasteful if you know for sure the larger activity being improved is simply a waste of everyone’s time and money,
Richard – you’re right that sometimes an outside voice needs to ask challenging questions and help pressure an organization to reinvent instead of just tweaking what might be a fundamentally bad process – see my post about not taking waste out of a workaround process:
https://www.leanblog.org/2010/11/dont-speed-up-or-improve-a-workaround-process-fix-the-system/
Outside eyes and outside voices are important, but you should avoid dictating solutions. You might be right as the outside voice, but it’s a complex matter to get others to see things the same way and to buy in to your possibly radical ideas…
Mark,
I’m not sure I understand your criticism of the stopwatch. It seems to me that a stopwatch can provide data as to whether one layout is better/faster/easier than another, just like a spaghetti diagram does. As a tool to provide information, it seems valuable. As a tool to hector people into working faster, it’s dangerous.
Or perhaps your issue is with the stopwatch being held by process consultants, rather than the workers themselves?
Can you explain your thinking a bit more?
The problem isn’t the stopwatch but rather how it is used.
Used by the stereotypical Tayloristic I.E., it is bad. Now peers timing their own colleagues work isn’t as bad, IF that study doesn’t lead to a quota or an inflexible time standard.