When I read John Seddon's book Freedom from Command & Control: Rethinking Management for Lean Service, I was a fan. I thought, “Here is someone from the Dr. Deming lineage who has a good message about what's wrong with traditional management.”
Unfortunately, in the past few years, I've been increasingly disappointed with both the tenor and the content of his message. In his monthly email broadcasts, he frequently complains about “tool heads” and idiots and people who aren't the thinker he is. I have other criticisms of his message, but I have one particular beef about a podcast he created called “Rethinking Lean Service” (it's more a monologue, one that allows no opportunity for comments or questions, so I write here.).
In the podcast, he said, in part, the following (the entire podcast is no longer online):
“The tools people argue that Ohno said you must first standardize before you can improve. He never said that. Actually, it was Womack and Jones who said that. Indeed, in their 2007 edition of Machine That Changed The World, they said as follows…”
Seddon could not be more wrong on this point that Ohno never said that. His declarative statement is so incorrect, it makes you wonder if it's an intentionally self-serving lie (to tear down lean and Womack and Jones) or if he was just sloppy. Given his academic airs, you'd expect more precision. He has a habit of going after Womack and Jones and, yes, I'll defend them.
Update (3/1/11) — The direct quote seems to come from Ohno's student Masaaki Imai, see my comment and documentation here. But again, it was NOT made up by Womack and Jones.
Update (8/20/13) — The quote is also attributed directly to Ohno in the back of the book Taiichi Ohno's Workplace Management, which was updated and edited by people who worked directly with people who worked with Ohno.
“Where there is no standard, there can be no Kaizen.”
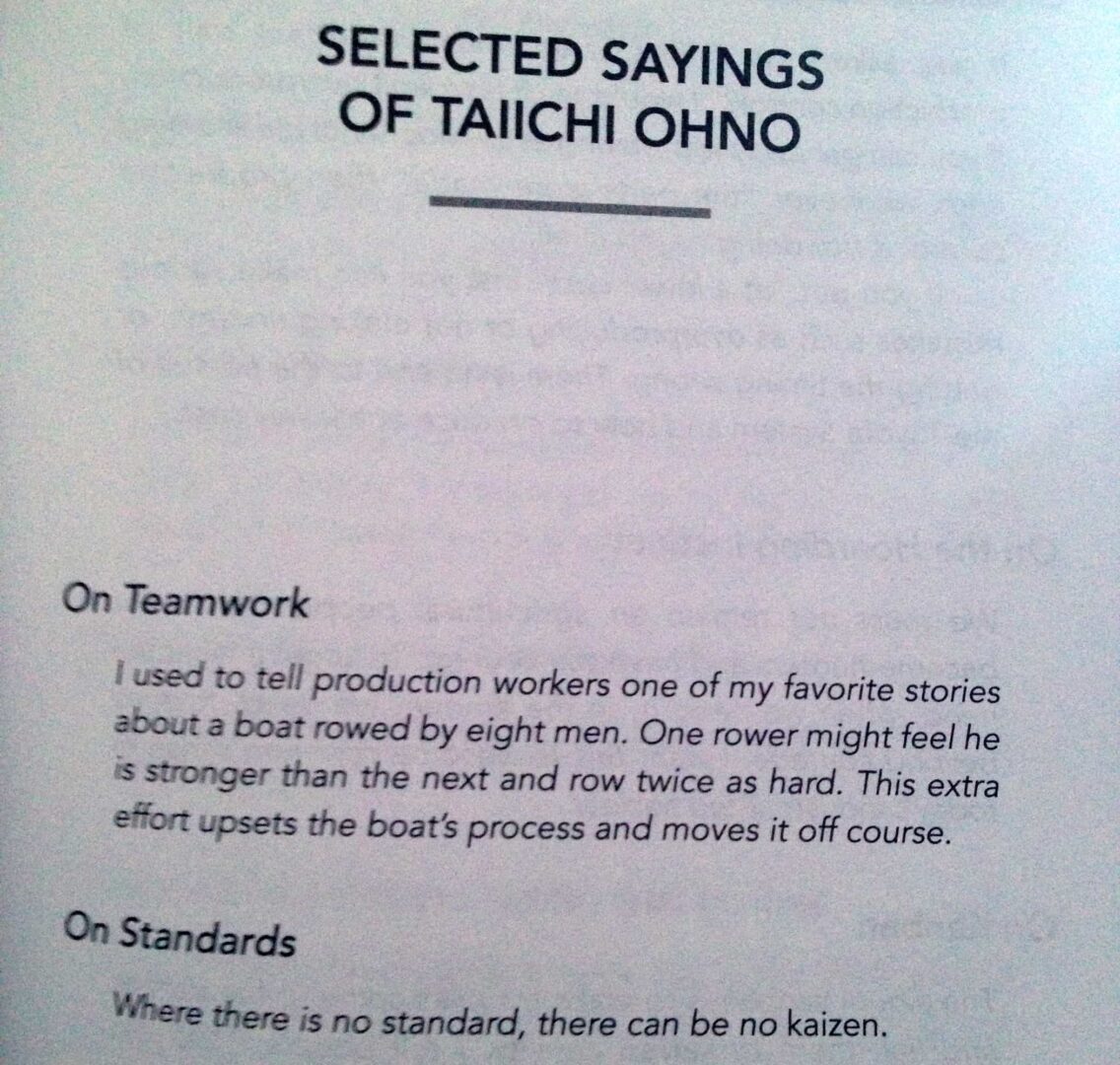
Note: if you are going to comment on this thread, please consider addressing my main point, that Seddon is misrepresenting both Ohno and Womack/Jones.
What he's apparently referring to is Womack and Jones writing: “As Taiichi Ohno noted, “Without standards there can be no kaizen.” (and the full text is below):
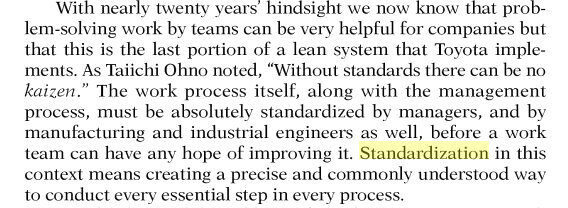
Now Womack and Jones don't footnote the exact Ohno quote (maybe they should have).
Ohno is quoted in The Birth of Lean as saying this: “My first move as the manager of the machine shop was to introduce standardized work.”
But if you look to Ohno's own book Taiichi Ohno's Workplace Management, Ohno writes things like these:
- “If you think of standards as the best you can do, it's all over. The standard is only the baseline for doing further kaizen.”
- “Standards are set arbitrarily by humans, so how can they not change?”
- “When creating standard work it will be difficult to establish a standard if you are trying to achieve “the best way”. This is a big mistake. Document exactly what you are doing now.”
- “Without some standard you can't say “We made it better” because there is nothing to compare it to, so you must create a standard for comparison.”
Ohno's work seems to state, in many different ways, that standardization is important as the first step to kaizen.
Seddon might want to nitpick and ask, “Where's the exact quote that Womack and Jones cite?” Fine, but it's hard to argue that Womack and Jones invented the quote as part of some top-down command-and-control evil plot to force standardization on people, especially in services. Seddon often quotes Taiichi Ohno as saying “do not codify” the Toyota method, but nobody can find that exact quote either.
Seddon is right (and I'm paraphrasing) to say it's harmful to over-standardize to the point where people aren't thinking or to where a process isn't flexible to meet customer needs. But many other Lean thinkers say that as well (a point that Seddon would probably deny).
Seddon rails generally against the use of “standardization” in services. He'd say that Ohno was building cars and service businesses are different so the same methods don't apply.
Well, in healthcare (a service), standardization (via Lean and Toyota methods and mindsets) is leading to many quality and patient safety improvements (like Dr. Richard Shannon's work that is literally saving lives), so it's disingenuous for Seddon or his followers to make his blanket statements like “Lean doesn't work in services.”
Here's my overall post on standardized work, if you want to read more. Standardization is a spectrum, not an absolute. In some settings, more standardization isn't helpful. In some situations, it is helpful but standardization shouldn't be taken to an unnecessary extreme. We shouldn't standardized for the sake of standardizing and “standardized” doesn't mean “mindlessly identical.”
Seddon and his crowd are fond of trotting out a failed Lean effort at the British tax office (HRMC) — an effort that I'd squarely put in the “L.A.M.E.” column (“Lean As Misguidedly Executed”). But Seddon takes examples like that and makes the blanket statements that all Lean is bad in services — it's not that people did it badly, there must be something inherently wrong with Lean if some people use it badly (I'm paraphrasing), but that's a specious argument at best.
Situations where “Lean” is used to tell people to tell office workers to take memorabilia off of their desks (as was done at HRMC) are clearly L.A.M.E. This is the sort of thing I've criticized and even mocked in a video.
But unlike Dr. Brent James, Seddon can't separate “lean done wrong” with “Lean” in general. Seddon paints with a broad brush that Lean is bad in a services settting — oh, and the solution is him, by the way. Seddon and his followers don't seem to want to accept there is any good thinking or that there are any good people in the Lean world — you have to follow them. They say Lean is bad, they are good. Black and White.
Now, to the second part of Seddon's audio clip. I *d0* would agree with him (strongly) that it appears the Womack and Jones take on standardization is not quite correct, that the “absolute standardization” of all work should be done by managers and engineers.
Updated: Looking at the whole of the chapter that Seddon is citing, Womack and Jones are giving a lot of credit to work teams driving improvement. They are reporting the fact that Toyota has managers and engineers set up a process (undoubtedly WITH the employees that will be working in the process) and THEN the employees play a major role in improvement. To portray this as “command-and-control” seems a bit misguided in an attempt to slam Womack and Jones. I think Seddon is selectively quoting Womack and Jones to try to make them look bad.
I've learned from Toyota people, and books like Toyota Talent: Developing Your People the Toyota Way, that standardization is a spectrum. You standardize the things that matter for quality or safety or service. And the “you” in that equation is the people doing the work (yes, this is what Taiichi Ohno taught). That's how I've taught and practiced Lean in hospitals and so do many others… but, again, Seddon wants to paint all “Lean” people as a bunch of command-and-control “toolheads.”
It's a shame that John Seddon lets his name calling and bad attitude toward others get in the way of some good points he has to make. Being flat out wrong and accusing Womack and Jones of inventing a bit of Lean history (Ohno's statement) is just one example of that unbecoming behavior. The bad attitude detracts from what might otherwise be some helpful ideas.
I've resisted writing about this whole “Lean v. Seddon” squabble, the fight that he's been picking, as I try to remind myself of a funny old Northwestern University Marching Band football cheer (this is back when the team was really bad): “Ignore them, ignore them, maybe they'll go away” (referring to the other team).
I've tried ignoring Seddon and his followers, but in this instance, I decided I would finally speak out.
Please scroll down (or click) to post a comment. Connect with me on LinkedIn.
Let’s work together to build a culture of continuous improvement and psychological safety. If you're a leader looking to create lasting change—not just projects—I help organizations:
- Engage people at all levels in sustainable improvement
- Shift from fear of mistakes to learning from them
- Apply Lean thinking in practical, people-centered ways
Interested in coaching or a keynote talk? Let’s start a conversation.
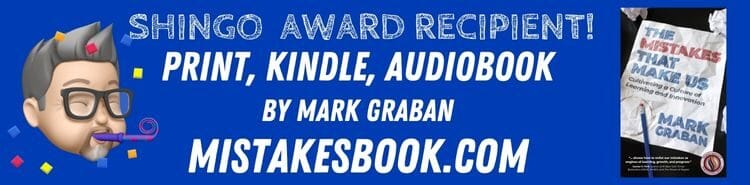
It just seems very unfortunate that as a community with common interests rooted in Deming’s work factions emerge to challenge each other like this. I’ve said before that lean and systems thinking are two quadrants of the same beachball. I use both in my work and both have merits – especially when combined. Johns a nice chap actually – just very focussed on his mission. The vanguard method he invented is powerful and has had great success in the UK public sector. I just find it peculiar that learned people resort to this kind of public derision. Seriously not cool! I hope we can get over this and have a productive discourse.
Lee – I’ve followed Seddon with some curiosity, but there’s nothing there but platitudes and puffery. Don’t blame Mark for not having productive discourse, Seddon spends more time attacking others than promoting anything positive, it seems. I’ve tuned out. We should just ignore Seddon and not waste the brain cycles thinking about it.
Lee, I know “they started it” is never much of a defense on my part, but I don’t think my countering his claims can be considered “derisive.”
I’ve said he might be lying, I didn’t accuse him of committing a felony.
It *is* unfortunate that there’s this discourse. I’ve tried taking the high road, but I’ve had my fill of the noise coming from Seddon’s world. If he’s “nice” it certainly doesn’t come across that way in his articles and newsletters.
I’m not saying systems thinking has no merit. I agree with you there.
Mark,
I also know John, and I really appreciate his work as he combines lean with systems thinking.
Systems thinking is pretty much based on how systems behave (which a company always is, remembering my own time at BMW, it was like being in a jungle with lots of different subgroups in their own environmont). The organization, John focuses on processes in the public institutions sphere (as there is probably the most muda and the essential leverage points for making the overall societal change happen).
In my personal view standardization only applies to the more “mechanic” processes within an organization. There will never be “the” standard as the system will constantly change (especially when people are involved;-)).
The focus on the attitude in which way the company is lead is relevant in the context of lean.
Where do you see the place for lean?
Cheers, Ralf
PS.: Jim and Dan clearly coined the expression “Lean Thinking” and sort of mainstreamed it, which on the one had was good. On the other one however consultants often “sell” something that they call it lean focusing on standardization (sometimes even their own approach). All the other different sounding approaches like system dynamics, systems thinking, group dynamics, which are essential in the context to make it happen, are banned by them very often (experienced that in some 20 interviews with “lean experts” in Germany personally .
Ralf – I think it comes back to the idea of “standard-IZATION” (not standard) and there being a spectrum. For very repeatable assembly line jobs, the standardized work is going to be more specific and more detailed. For other types of work, the standardized work will leave more room for judgment and every task isn’t specified to the second by any means. Standardized work in healthcare certainly doesn’t mean that people turn off their brain and quit thinking (this is true in manufacturing too).
You’re right that a lot of consultants (and companies) call all sorts of things “lean” when it’s not true to Toyota ideals. Where I’d differ from Seddon is that I’d call out the people misappropriating and misrepresenting Lean, while Seddon blames “Lean”. It’s hard to blame a concept or an entire movement. Seddon used to label his own work “lean,” as I’m sure you know.
Lean thinkers shouldn’t exclude other methods, I agree. If somebody does, is that “lean”‘s fault? I think not.
Mark – Thanks for your question on my last comment. If Lean Thinkers exclude other methods from the table, they crudely misunderstand and misuse the approach of lean. However they still “sell” the method and even large consulting companies are so accelerating the undervalue of lean principles. It is like a vicious cycle (as we say in System Dynamics), once these kinds of consultants are in a company, they will stick there and this will perpetuate the downgrading of lean.
Lean Thinking in my personal perception is a certain kind of process consultation that has been framed by EdgarSchein. I was happy to meet him in person last year on CapeCod. Even JohnShook and a couple of other lean folks attended the workshop that was called “Helping”.
Mark –
Thanks for your clarification. Yes it is not “the bad method” (per se) it is what we do with the “method” (in this case “lean”). Labeling a process with a specific word or expression can be so hugely misunderstood by others, or even not understood at all.
The challenge is to combine the wording and the doing so coming to the same/ similar way of understanding. Therefore I like it most not naming anything in the lean transformation I conduct without using specific wordings (either known to Japanese or Americans). It is the action that counts, which forces emotions to the people doing it. Emotions drive our behavior. The words alone won’t drive much change.
It would be rather helpful if John Seddon would join in the conversation, as I think we all talk about the same thing, just from a very different perspective and experience. That would make some things probably much easier understood as they are a bit diffuse right now.
Cheers, Ralf
If Professor Seddon were to join “the conversation” my past experience finds him more likely to be denigrating instead of conversational. He paints with a very broad brush, which is disappointing.
… it may open the doors to new thinking about lean :-)
Let’s have it a try. What can we loose, other than gaining?
Ralf
The tone and spirit in which Seddon takes against other process improvement methodologies – especially Lean – is both disappointing and a huge waste of time. While he denigrates Lean and its practitioners, we are out there actually trying to help companies become better. He should step out of his ivory tower and get his hands dirty. As Ohno said, “Practice over Theory” – and that’s where pragmatism will be the judge.
I’ve got a slightly different take on the whole thing. Frankly, I’m having a difficult time seeing any sort of reason for arguing since, to me, both of you are in complete agreement with each other. I didn’t take John’s comments to be a blanket criticism of all lean, I took them to be precisely your point, Mark, that there are numerous examples of LAME out there and they are often actively harmful. And, because of differences in environments, we are likely to see more misapplications in service industries than in manufacturing industries. (That is, while the fundamental principles will remain the same, the practices may require more modification in service industries. Consequently, there’s a higher risk that “LAME” consultants will promote inappropriate methods by simply copying production optimized methods into service processes where they may not apply directly.)
When I listen to John’s podcast I hear a deep respect for Taiichi Ohno and a sadness for people who don’t understand and misapply what he created.
The standards and standardization bit is a great example. To me it was clear that John was criticizing mandated standardization done with little to no worker input. And we know that’s bad. He praised standards that are created by the people actually doing the work (and credited Ohno for that). And that seems to be the exact same point that you’re making, Mark. [As an aside, a few years ago I got to hear Ken Kreafle of TMMK speak at a conference. He was asked how Toyota ensured that different plants used “Best Practices” (i.e., common standard methods). His response was, “Why would we want to do that? Each plant has it’s own unique characteristics. Why would we think that something that worked one place would work in another?” To me that’s epitomized the point that you create standard work for the work you do which then becomes the basis for improvement, but you don’t mandate one single approach to doing things across an entire company since that essentially stifles improvement.]
Bottom line: In my opinion it appears that you’re in violent agreement with each other.
Steve – you’re right that there’s a lot of room for “violent agreement”, that command and control is bad, for example.
Some of the context isn’t here in this post, but Seddon has quite a habit of labeling people not in his fold as “tool heads” (including myself), denigrating Womack and Jones (who aren’t perfect, but have done a lot of good), and of making wild blanket statements like “lean doesn’t work in services.”
A lot of it seems self-serving, to say the least.
Their systems thinking journal guy is combative and claims that lean is inherently command and control (and again, Seddon’s approach is the only alternative). They can’t separate LAME from Lean. They claim any instances of LAME somehow proves that lean is a failed approach.
He’s a hyper-critical “smarter than thou” type and that’s part of the tenor that turns me off. Let’s say I disagreed with the Six Sigma approach (there’s a lot to it I don’t like actually) and I called all Six Sigma practitioners “DMAIC Clowns” or something – well that wouldn’t be very constructive. And that’s the approach Seddon takes.
Yes, he comes across as eerily calm in that podcast, but remember that’s a planned scripted thing, as opposed to the interaction I’ve seen him have with people online (and reports I’ve heard of his behavior toward “tool heads” in person).
Steve, We really all talk about the same thing, though with different wording and focus.
As an economist it is always miracle to me the “lean” is often minimized to production line activities. Cutting out all the necessary paper, administrative and software work in the “background”.
“Seeing the whole picture” is what ThomasJohnson focuses on in his well-known paper, “Lean Dilemma”, http://www.in2in.org/insights/TomJohnson-LeanDilemma.pdf. It shows neatly where the real power of “lean thinking” lays in front of us all.
What is it we, as “lean thinkers”, commit to when talking about “lean”?
womack and jone’s interpretation of ohno’s statement is probably what seddon was referring to
Perhaps the most amazing problem about this blog post is the deep lack of insight and understanding. Graban just doesn’t ‘get it’. He tries to relate everything back to Lean without understanding that Lean doesn’t have the equipment to make sense of the world. This isn’t Graban’s fault (not the people). Lean has defective genes.
Lean is ‘an old bitch gone in the teeth’ the signifier of a botched attempt at understanding.
Lean has become the chameleon of the quality world. Every time lean is identified as having a defect, it tries to sidestep culpability. The argument goes that what has been done is not ‘real lean’ or that it is ‘L.A.M.E’. So lean has gone on a strange journey and a series of mutations to become Lean Thinking. The only thing that it appears unable to jettison is its badge of Lean.
And yet the sobriquet Lean in front of thinking, acts to highlight the deficiencies in lean. The word Lean sabotages the thinking. Lean is now the ‘clog in the machine’.
Unfortunately those propounding Lean don’t know it. So this blog is yet another milestone in Leans inexorable decline.
X-rated (your comment got caught in my spam filer because of the pen name you chose). I notice you come from the UK. Funny, all of the screaming criticism is from the UK (except for Tripp), so maybe you are associated with John Seddon, as well?
If you’re going to rip me fine, just give us something specific instead of your empty vague criticisms. At least I can be VERY specific about what I don’t like about John Seddon or his message. I’m all for constructive criticism, but yours was not that.
A friend told me about Seddon a few years ago so I poked around his website a bit and subscribed to his newsletter. You mention the HMRC, he spent a few letters insulting some woman from the HMRC (the head?). Seddon was saying basically he would keep insulting her until she returned his calls. What? And this is an enlightened thinker who understands how systems work? He seemed more interested in getting attention than fixing the HMRC.
http://www.systemsthinking.co.uk/6-news-feb-10.asp#2
I also vote for “ignore him”.
Mr Graban,
Your post includes a number of innacuracies concerning my references to Ohno and Womack and Jones. Would you like me to ask my researcher to post the corrections?
John Seddon
Inaccuracies? I quoted you.
You are certainly welcome to respond.
Professor Seddon, you can’t respond for yourself to talk about your own words? How dreadfully disappointing.
Mark, et. al.,
The lean manufacturing dispute about what Toyota means by standardization and “standardized work” has been going on for 20 years. One side views standards as an attempt to impose control on workers and bypass their involvement (standards as fixed), while the other side views establishing standards as a basis for continuous improvement involving operators (standards as stair steps). How about this: What if both sides are wrong about what Toyota people mean when they say “standard”?!
Some words are so occupied in our brains that they are nearly useless for describing anything beyond what we already think. When Japanese Toyota persons use established English words like “problem solving,” “involvement” or “standards” to describe what they are thinking, it may well inhibit us from understanding what they mean.
The fact that this dispute has carried on for 20 years may say more about us – you, me and John Seddon included – than it does about the subject. It suggests we seek comfort in a predictable zone where our definitions and understanding are clear.
So let me put forth two hypotheses:
Hypothesis 1: Anytime you hear the word “standard,” if you substitute the words “target condition” the dispute will tend to dissolve.
Hypothesis 2: It is impossible to continuously improve a process without involving the process operators.
I invite any reader of this to refute these hypotheses experimentally.
Mike
Mike – I am currently reading your Toyota Kata book and really loving it (I am only on page 90 so far).
I think your book will help the Vangard people know Toyota (and Lean) is not about imposing standards to impose command and control. Your book (so far) clearly demonstrates Toyota thinks of the whole system and not point optimization. I also enjoyed the part that explains why Management By Objective is not a viable management method for modern times.
I hope your book will also help influence the L.A.M.E. consultants out there with a misunderstanding of Lean standardization.
I hope clients and potential clients read your book to help have the courage to deal with the political and cultural aspects of changing their management systems (not an easy or quick task). For their sake, I hope your book helps the recognize if they have a L.A.M.E. consultant.
I know I am dedicated to helping the organizations I work with make lasting improvements. I think all on this discussion share that same passion even if the terms/approach are different.
Mike – Thanks for your thoughtful questions putting into the conversation:-)
It seems that we all are often entrenched in our own mental models too fast (and stay there without letting go of our thinking).
In August I had an experience which touched the issue of language and what we “see” behind words we see or hear, http://leanthinkers.blogspot.com/2010/08/language-bottom-line-to-understand-each.html
Even worse the situation becomes when the wording is transfered from English into German ;-( Often there is no equivalent, and “einfach einfach machen” (just make it easier) (as done during the GDR times with not reliable material support) just seems too “easy” (and not lean;-)).
We still have a lot to learn, and except others’ views through going to the gemba (trying to understand the background and reasoning of the words).
Mark – Thanks for shaking up the conversation in the beginning. Sometimes this is necessary to bring the hidden mental models up to paper;-)
John – Thanks for stepping in yourself. Myself I am a strong believer in systems thinking and the direct connection to lean in the “Shingo / Ohno sense of lean”. Having experienced the “standard” way of implementing lean in a car OEM, I feel there still is a large gap towards the real power of lean.
Yet it is doable, and probably with less effort than we might think.
Mike Rother:
Thanks!! No attempt at refutation here. As Ralf points out, translation introduces all kinds of problems, so we need to *practice* these things and understand them, not just repeat words.
I heard Steve Spear say the following once, which supports and amplifies your notion of target condition as a useful interpretation of “standards”:
“…the tools and techniques of lean are things which are done to better define what is supposed to be happening, in a way that anyone can tell, and better compare what is actually happening with what should be happening…”
I teach it this way: A standard is not a straitjacket, but a reference point. How did we do this cycle?
I may be the only person that has attended Vanguard’s core curriculum and worked with the method and gone to LEI training. The focus of LEI training was the tools and in Womack’s second farewell address he states that a year ago LEI moved from tools to management affirming the focus. I don’t know the “new” lean approach that is being referred but the old was tool focused and the departing leader has affirmed this. If a tool focus is LAME as alluded to often than Womack started people down the wrong (tool) path either by design (easy to market) or ignorance. I suspect the former.
Many lean practitioners don’t know much about Deming until the recent interest where education seems to have risen. Red bead experiments and Deming quotes take me back to the Deming User group days. Where what Deming said was more important than advancing the learning, in part I believe this is why Deming User groups have died out.
Having just gone to the UK to take a deeper dive into the Vanguard Method, the depth of the approach is unmatched as new thinking provides breakthroughs. Heard of any new tools in lean? Are all problems the same? Do they need 5S, kaizens, etc? These are important questions.
There are important distinctions between lean and the Vanguard method, so those saying they are the same are just plain ignorant. They don’t know, and having seen both methods at work, I prefer the human change methods that accompany systems thinking not addressed by lean or six sigma
Deming offered us SOPK (system of profound knowledge) and psychology is an important last element of SoPK. Change is truly emergent using the Vanguard Method and tools approaches make changing thinking harder. They are rational and coercive ways to change where Vanguard takes a normative approach. This represents some of the rub between lean and systems thinking.
One distinction you left out was between what systems thinkers have found as differences between manufacturing and service. Making service like a manufacturing plant as Berwick and Toussaint advocate is a huge mistake. I believe they believe what they are doing is right, but before we get the whole country jumping off the bridge one might wish to heed the voices of dissent.
Tripp- Neither Dr. Berwick nor Dr. Toussaint are saying we should “make hospitals like a manufacturing plant.” If you think that’s what lean is all about, you’re really missing the point completely. What they do argue for us applying the best thinking and lessons from lean manufacturing (such as look at the whole system instead of department silos, engage everyone in improvement, and quit blaming individuals for mistakes).
I’ll assume you haven’t seen the data from ThedaCare, Allegheny General, and other hospitals that are dramatically improving quality, patient safety, and cost with lean methods, otherwise I don’t think you’d take the view that this is a “huge mistake.” I’ll give you the benefit of the doubt (maybe unearned) that you’re not “just plain ignorant” on that point.
The results from Allegheny are being repeated by Dr. Shannon at UPenn in Philly now. Yes, the whole country needs this. It’s not “jumping off a bridge.”
I wonder how Toyoda would react to this dialogue
Good morning everybody!
Amazed by the mass thoughtful comments. In the lean world the “chalk circle” is often referred to in order to find out what is really going on in a process.
Even though we are not standing in circle literally, our conversation reminds me strongly of it.
Slowly things evolve that have been not outspoken before. In the beginning we focused on the event (JohnSeddon’s quotes) with MikeRother’s hypothesis we have move a level deeper to the assumptions.
So we already reflect on what is driving our thinking. This, http://www.presencing.com/docs/thought/201006_Schein.pdf, short paper by EdgarSchein gives some good advice. It doesn’t name lean in any line, and yet when I read it lean springs into my mind right away. I remember well the workshop with EdgarSchein last summer on Cape Cod (on helping, actually its the title of his new book as well). Some folks of LEI, as JohnShook attended the workshop as well, so the change in focus and intention of the LEI that Tripp mentioned earlier is probably well under way.
What small action to make this conversation useful for the lean community can you contribute to?
Dear Bill S.,
Sorry to disappoint you but I am busy. So is my head of research. But if everyone is patient the corrections will be posted.
John
Ah, I see you were busy cranking out your latest nasty gram, Mr. Seddon, which includes the words tool-head, “faux academic,” dumb, loonies, and lunatics.
“Respect for people,” Mr. Seddon? Did you not learn that from Toyota?
Where did you earn your PhD, “Professor” Seddon? I’ll patient await your truth commission.
Hey, I like you.
I really like you.
Truly I love the boldness of Bill Ss comments as he remains hidden from view with no last name and a sea of Bills as a possibility. Pretty wimpy, Bill S. I’d be embarrassed too.
Wow, into conspiracy theories much, Tripp? Yes, “Tripp Babbitt” would be a far better fake name if I were using one. Wish I had thought of it first. You win. Maybe I’ll take “Trite Babble.” You OK with that?
“Professor” Seddon should have had the balls to call out the pseudo-academics he was referring to in his newsletter instead of dancing around the subject. Is he looking to remove me from his email list or something?
Bill S-
Couldn’t care less, if you stayed on the mailing list or not. Just like to know who your enemies are, a little more stand up and fight without the hiding seems more honorable.
B Allan-
I have to agree with you. I am tired of the Lean people saying LAME when success is not achieved, which is happening with greater frequency. Fads have short lives though.
I think that I understand why Seddon is so robust in his language. Niceties are great ways to creep around a problem. We spend half of our lives skirting around issues, whereas Seddon just says it. No BS. Direct. To the Point. Sure it makes lots of enemies. Yet if the wrong thing is the wrong thing, why bother dressing it up as something else?
I listened to the Podcast and I read Grabans blog.
I am inclining to Seddon’s way of thinking on standardization and service organizations.
For too long Lean has been dodging these bullets. You can’t keep on blaming LAME or saying that it isn’t real lean. The Lean method HAS evolved significantly but these are real challenges and it isn’t enough to keep dancing around the barrel.
The lean community (yeah, whatever that means) throws this sort of criticism at itself all the time. Seddon is saying the same type of thing – that something that doesn’t fit his view isn’t real Lean (isn’t Ohno Lean, I suppose). We’re all criticizing poor thinking (or lack of thinking or just using tools). John thinks the “lean community” has no right to do so. Seddon has the right to do so, I guess, because he’s disowned the term “lean” after the publication of his book titled “Freedom from Command and Control: Rethinking Management for Lean Service (The Toyota System for Service Organizations).” That was “real lean” he’d say?
Seddon, I think, is alienating people because of his “I’m smart, you’re not” attitude that comes across constantly. He knows best, just listen to Papa John.
You say he’s being direct, I say he’s rude and condescending. We can all have our own opinions on that.
This whole thread is almost getting out of control.
Alienating people? Is service improvement some befriending people competition?
Out of control?
Seddon appears to have highlighted serious methodological flaws that have seriously upset the lean community. I think that it is important that the lean community does something about the flaws.
Do not attack the person highlighting the flaws.
By “out of control” I meant some of the exchange between Bill and Tripp that was just personal between them.
It’s funny to me, the apparent hypocrisy that it’s OK to you that Seddon attacks but people can’t attack him for his exaggeration of the problems with lean or his tone.
Tripp, want to chime in and criticize BAllan for his anonymous username?
Seddon points out flaws in the methodology, as do I and as do many others. The difference is that Seddon makes the leap (as does Tripp) that “lean doesn’t work in services.” Tripp conveniently ignores data by claiming that lean is bad for healthcare. It’s ideology over data, that’s bad.
Why would I call out BAllan, when I am in agreement? Must be some type of lean logic.
Your attempt at explaining data in your recent blog post is laughable. You might want to spend some time in Knoxville with Dr. Wheeler and actually learn about what you are writing on.
Tripp – you criticized the other guy for not sharing his full name… you do understand the dictionary definition of the term “hypocrite?”
Thanks for the constructive criticism, why don’t you go to today’s post and share your insights with us instead of just taking potshots? Where do I have it wrong?
Boys, boys, boys.
It’s interesting how none of the John Seddon supporters (easy to tell who is in that camp) have taken on Mark’s concern that John is possibly intentionally misrepresenting Jim Womack and Dan Jones for his own benefit. There’s a lot of guru envy going on and none of it is attractive. Even John can’t be bothered to defend himself against the charge of taking the words out of context and misrepresenting Ohno’s words or intent. I see a lot of talk that’s apparently designed to deflect from and obfuscate the original point of this post – is John Seddon wrong, intentionally or not (we can’t gauge intent).
Please everyone get back to trying to help people improve.
Mark-
Do you understand the definition of moron?
Amanda-
I don’t believe Womack or Jones need help misrepresenting themselves. The Lean camp has its followers if you haven’t noticed.
Wow, that’s childish.
Amanda-
You mean its childish to defend your thinking? What do you have to offer, I am interested. What have you got?
If you were actually defending anything with logic, that would be one thing. Calling people “morons” and such is what’s childish.
Mark-
You call out John. He says he’ll respond. Womack never responds. You should be thrilled. One can assume Womack either can’t defend himself or has left the job to you, which is it?
The pettiness began long before this thread. I can be as ridiculous as you folks.
I would assume Jim chooses not to. I’m not acting on anyone’s direction here, this blog is my own property.
You calling yourself “ridiculous” is the first thing I agree with.
If i were seeking a consultant’s help and after reading the comments of Tripp Babbitt, I would never hire him as a consultant – his words are a reflection of his thinking, approach and treatment of people and, if I were a potential client, I’d be very concerned about how he would treat me.
Pete you might not hire him as a consultant but you badly need his help.
He would treat you like an adult & help you see the what & why of performance (no holds barred).
Given a consultant who is able to transform my business forever by being direct & helping change thinking or a community that is unable to face criticism … + gets upset when faced with penetrating academic insights?
Hmmmm let me think that one over a little?
John Seddon, Tripp where can we get hold of you?
H Clark (who runs Seddon’s “Systems Thinking Review”) –
We clearly have a different definition of “penetrating academic insights” here. And in terms of who is “unable to face criticism,” it’s clear which side here resorts to insults and name calling – John and Tripp. Good luck with that.
I’m still waiting for Tripp to show evidence he’s helped a single organization anywhere and that he’s not just empty (or nasty) words on his blog and otherwise.
I don’t recall name-calling or insulting. I do recall posting & linking to articles that are critical. I have been personally insulting.
In my view badging eveything that doesn’t work & claiming that it is LAME avoids lean ever taking responsibility.
It is like the invitation to step into the chalk circle (as though stepping into a lean circle) will suddenly reveal the hitherto hidden. What will be seen from inside the circle is merely a reflection of what is believed by the beholder.
Seddon will respond shortly. He has been attacked by many in the lean community, & before by CRM companies, ISO brigade for highlighting problems & impacts on service users. And yet the Lean community fails to answer his criticisms. And dodging is not answering.
On another point I do not damn & blast all altrnatives to systems thinking, but where one method is consistently causing damage it is right to highlight this.
I will continue to highlight & link & you will continue to huff & puff. And guess what? The world wil keep on turning.
H Clark – the insults flow freely from John Seddon (“loonies”) and Tripp. Tripp is clearly overmatched in this discussion, as he can’t rise above calling me a “moron” instead of discussing the issue.
The issue, by the way, is my post that says John Seddon has misrepresented “Ohno never said that” about standardization and kaizen – it was either an error on his part (which he can correct) or it was intention in his ongoing battle with Womack and Jones.
Jim Womack’s old LEI “e-letters” are just as much a one-way monologue as John Seddon’s newsletters. I’ve personally been pushing LEI to get more open, collaborative, and interactive.
I think you misunderstand my use of “L.A.M.E.” – it’s about the method not the results. If the method doesn’t square with TPS or Deming principles, people shouldn’t call it “lean” they should find their own name (or not give it a name).
If people say they are doing lean, but are just using a few tools and a top-down way, that’s not really Lean (that’s LAME). I think we’re in violent agreement on that. If people say they’re doing lean but they yell and scream at workers for quality problems, that’s not Lean (that’s LAME). I hardly claim “anything that doesn’t work” as LAME. Again, it’s about method and mindset.
I am trying to play a constructive part in correcting behavior like that or the misapplication of the Lean label (partly because it dishonors Ohno, Shingo, and Deming).
Lean is a pretty well defined set of principles. If people do bad things and are misguided in calling what they do “lean” that is not the fault of “lean.” Your blanket criticisms (on Twitter) that Lean is somehow inherently embedded with command-and-control thinking, for example, is a point I’d disagree strongly with. That’s your opinion, but that doesn’t make it “Academic” fact. You speak without data that Lean is almost always bad and, in using those words, it’s arguable that you are the one doing harm if you turn people away from a method that can certainly work and can have great benefit for patients, hospitals, and their employees.
I think that deep frustration flows freely from those who come across the wreckage caused by Lean in the UK.
It leads me to question your defense of Lean.
If the majority of people are doing it wrong, then the little island you claim as real lean that follows Toyota principles can hardly wag the dog can it?
There is something within Leans dark heart, that calls to a command and control instinct. From what I have read and seen to date, standardization and tools are two of the major issues linked with Lean. Certainly in the service environments standardization is corrosive to good service and inhibit systems from absorbing variety.
Additionally the tools traditionally associated with Lean, when used in service reinforce this dysfunction.
Macho talk sounds good in a detached-from-humans context such as this blog post and comment thread. But with real people, a vile tongue and a macho, tough-guy approach does not change hearts or minds.
As a father of 9 children (biological and adopted), I’ve learned that persuasion is only possible through gentleness, understanding, meekness, humility, and in the spirit of service, and with the other person in mind. What works in families and in familial relationship is also applicable to the world of business. Try name calling and brute force with struggling teenagers – go ahead; doing that only invites resistance and rebellion and, yes, their heart will change, but away from mom and dad, not towards.
As a lover of horses, calling horses names and acting with brute force does not change their hearts towards you. There are many life-principles we can learn from horses and equine psychology.
As a long-time practitioner of jujitsu and arnis, I’ve learned from my teachers and in my work with students, that having the student in mind and the student’s development foremost on my mind as I teach is what helps them develop, learn, and grow. Brute force and name calling, on the other hand, creates resistance and rebellion and ineffective learning.
As a former Toyota employee, it was always understood that the Toyota Production System is pragmatic at its core. Through experimentation, we learn what works and what doesn’t. Kanban is practiced because it’s the best we’ve got right now to instantiate the principle of pull. But, if something else comes along that manifests the principle of pull better than Kanban, then that will be adopted. It’s very pragmatic and uses the real world as feedback as to what works and what doesn’t.
Tripp Babbitt and John Seddon, on the other hand, border on fundamentalism as they defend their ideology. Fundamentalism breeds hate, anger, imbalance, war, and death.
My hunch is that Tripp Babbitt and John Seddon behave differently in their private and personal lives. Why? Because their approach on this thread and in their public discourse wouldn’t work in normal human relationships: it goes against the grain of how humans ought to be treated.
None of us on this thread has 100% claim to the truth; we can all learn from each other. It’s in that spirit that true Lean exists.
I’m happy to hear and learn from John Seddon, Tripp Babbitt, and anybody else. But, when the message is filled with insult and is communicated with a sharp tongue, your message will fall on deaf ears because at that point, your message is more about you than it is about the student or the hearer.
Yeah, me too.
I’m interested in learning something new.
Just like I did when I listened to an impassioned speech by a then-unknown executive named Jack Welch at the GE plant in South Burlington, VT about Six Sigma which caused me to give up on Ohmae/Deming/TQM and, later, giving up on Six Sigma and the silly Black Belts and Ninjas thing after attending a Womack Lean Love Fest and now, probably giving up Lean for…. something else.
Vanguard, maybe?
I see that I missed a great debate and a chance to interject Fred Taylor into the discussion.
I don’t know this guy Seddon, but I think I would like him a lot.
I am truly over-matched? Interesting conclusion, but you ARE judge and jury here.
Calling someone a liar is provocation in any field.
This is “respect for people” that lean folks keep flying in my face? Again interesting.
I’ll say it again, John says he will respond. You should be thrilled.
What I said is that Seddon is either lying or has his facts wrong. We’re clearly not inside his head to know intent.
Part of my intent with this post is to give back some of the behavior that’s come from the Seddon crowd – calling names and being provocative (to which, your favorite defense is that being provocative and argument fosters learning… so how that’s working for you here?). Actually, I think my tone here was pretty measured compared to the blanket non-fact-based criticisms of lean and yet the “new systems thinkers” are all up in arms.
It’s my blog, I can run the discussion how I want. I only deleted 2 or 3 comments that were truly a personal back and forth. In your online writing, you’ve previous screamed about how it’s your discussion and it was rude of me to not let you have the last word, so again, the word hypocrite comes to mind. And you’ll probably retort by calling me a moron.
The dog barks and the caravan passes.
Mark Graban’s article makes two major charges against John Seddon:
1) That he either lied or selectively misquoted Taiichi Ohno and Womack and Jones when he said:
“The tools people argue that Ohno said you must first standardize before you can improve. He [Ohno] never said that. Actually, it was Womack and Jones who said that.”
2) That there is no quote that backs up his statement ‘Ohno said do not codify the Toyota method’
To deal with the second point first – that there is no basis for Seddon’s claim that ‘Ohno said never codify method’ – please see this passage from the foreword to Ohno’s (1988) ‘Toyota Production System’:
‘While most companies focused on stimulating sales, Mr. Ohno believed just-in-time was a manufacturing advantage for Toyota. And for many years, he would not allow anything to be recorded about it. He claimed it was because improvement is never-ending – and by writing it down, the process would become crystallized.’
The first point is more serious and will take longer to deal with. As proof of Graban’s claims, he lists some of Ohno’s statements on standardisation. The most relevant is: ‘Without standards there can be no kaizen’ (in Womack, Jones and Roos 2007 p290) [we will label this Ohno quote number 1 to avoid confusion]. The various other Ohno quotes that were listed by Graban in the article do not contradict Seddon’s claim that Ohno did not require standardisation as the first step to improvement.
The Seddon podcast Graban refers to is based on an article ‘Rethinking Lean Service’, freely available from the Vanguard website (http://www.systemsthinking.co.uk/6-brendan-jul09.asp) and which will soon appear in an academically-edited operations management textbook. It is true that the podcast features a condensed version of the article and hence some of the supporting argument to Seddon’s statement has been omitted. It is therefore worthwhile referring back to the article itself to see the more nuanced position Seddon and his co-authors adopted:
[Beginning of the quotation] ‘While we have explored the genesis of standardisation in service management literature and practice and the fit with the lean tools movement, it is worth pausing to reflect on the lean-tools promoters’ arguments for starting any intervention with standardising the work. They often argue that Ohno said ‘first you must standardise before you can improve’. While this is essential in manufacturing, in a service organisation to standardise would diminish the system’s ability to absorb variety. Fitting with the top-down conventions this means, in practice, that standards are determined by the hierarchy and/or experts and imposed upon workers (a common feature of tools-based interventions). In contrast, Ohno placed importance on workers writing their standards themselves:
‘Standards should not be forced down from above but rather set by production workers themselves.’ (Ohno 1988 p98). [Let’s label this Ohno quote number 2]
It is a central feature of the TPS that improvements are made by workers adhering to a scientific method, an essential component in organisational learning (Spear and Bowen, 1999). Missing this essential emphasis, Womack, Jones and Roos (2007) placed the responsibility for standardisation with management:
‘The work process itself, along with the management process, must be absolutely standardized by managers, and by manufacturing and industrial engineers as well, before a work team can have any hope of improving it. Standardization in this context means creating a precise and commonly understood way to conduct every essential step in every process.'(Womack, Jones and Roos 2007 p290)
This merely reinforces the present style of management. In service organisations work typically has been standardised and industrialised from an internal, cost-focussed point of view. Managers dumb-down the first point of contact (or out-source it) to employ cheaper labour and fragment the flow of work (again, to reduce training time and lower labour costs). The consequences are more handovers; more handovers means more waste, and an increasing likelihood of failure demand (further waste). The more work is fragmented – sorted, batched, handed over and queued, the more errors creep in. Every time a file is opened, it has to be re-read (duplication). These problems are exacerbated as workers are working to activity targets.’ [End of quotation from Rethinking Lean Service]
Seddon’s argument is that the more important of the two Ohno statements here is [2] that the workers themselves must set their own standards, not have them set from above by managers distant from the work (rather than [1] Ohno’s point about standards being necessary for kaizen). This is because, where standards are to be applied, the locus of control must remain with the front-line workers so that they may deal with the variety of demands being placed upon them. Following Womack, Jones and Roos’ advice would not challenge any pre-existing command-and-control organisational mindset and it would lead to managers (not frontline workers) setting the work standards. The example of the British tax office (HMRC) shows exactly what happens when the tools of lean are super-imposed onto a command-and-control structure: demoralisation of the workers, poor customer service and many expensive errors.
Otherwise, the above section is self-explanatory and does not take anyone’s quotes out of context. On the contrary, the authors place Ohno’s words into the most relevant context for the subject of the paper: that of the management of services.
The accusation may therefore be levelled at Seddon that, in his podcast, he is guilty of omitting some contextual detail as he condensed down the content of the paper for the ease of the podcast listener. However, to accuse him of lying is both hyperbolic and well wide of the mark. It is also to miss the more important point he is making: in conventional service organisations, the lean movement’s emphasis on standardisation only serves to reinforce the management’s command-and-control thinking, leading to dysfunctional performance in the wider system.
Seddon’s work in services begins with going through what he calls ‘Check’, an essential series of steps which helps managers to understand the current performance of their organisation as a system. In taking the workers in the organisation through a normative learning loop, the dysfunctional behaviour of the system is exposed to workers, managers and leaders. At the same time, new measures are constructed around what really matters to the end user that show the way forward for any redesign of the system. In contrast, conventional lean (following Womack and Jones) and its advocated first step of standardisation misses the opportunity for learning by understanding the ‘what and why’ of current performance.
To argue that ‘lean done right is ok, it is only poor practitioners that are tarnishing the brand of lean’ is to throw up a red herring. It is to make (at least) two mistakes: a) to miss the fundamental flaws of conventional management as articulated by Deming (which conventional lean does not address) and b) to not differentiate between services and manufacturing (e.g. the treatment of all demand as work to be done and thus not recognising ‘Failure Demand'[Seddon 2003 p26]). Both of these points are explained in more detail in the paper ‘Rethinking Lean Service’.
I hope this has clarified matters somewhat.
Brendan O’Donovan, Head of Research at Vanguard
Thanks for your response, Brendan. I appreciate your tone and attitude and your lengthy response. There is a lot to respond to, but I start with the last point:
“conventional lean does not address” — This is where speaking in generalities sheds no light on anything. To take just two examples, in my book “Lean Hospitals” in Dr. John Toussaint’s “On the Mend,” we both talk in depth about the problems with traditional management including blaming people, not looking at systems, and forcing things on people in a top-down way. For you and Professor Seddon to try to carve that out as your exclusive domain paints with too broad of a brush and misrepresents what people are talking about and doing in the lean world.
Secondly, the idea of “failure demand” is not a uniquely Seddon concept. The idea of preventing service errors (defects) that lead to rework (such as re-labeling lab specimens or re-admitting patients) is also covered in our books and other “conventional lean” books and sources.
I will respond to the rest later, but I believe you are throwing out your own red herrings and straw man arguments.
For example, you are leaving out the nearby sections of “Machine” where Womack, Jones, & Roos talk about employee involvement in continuous improvement and how they possibly so emphasized that in the first printing of “Machine” that they ignored the role of managers and supervisors. I interpret what they wrote as meaning that managers, engineers, and production associates (or any front-line staff) work together in designing a process and employees play a major role in kaizen. By quoting only part of one page in the book, I think you’re again shading their words to fit your narrative that they are top-down command-and-control tool heads.
Additional response to Brendan’s comment:
Part of my issue is that Seddon often very directly quotes Ohno as saying “do not codify”. You might say “codify” and “crystalize” are the same thing, but why not quote directly and accurately?
I can share details later, but Norman Bodek (who met both Ohno and Shingo) claims that the “do not crystalize” argument from Ohno was really a public smoke screen for not wanting to share this with outsiders. I have to take Norman at face value, as he has no dog in this fight.
When Seddon makes statements like to “standardise would diminish the system’s ability to absorb variety” I think we are working off of different definitions of “standardize” (not just different spellings). If you mean “standardize” to mean un-thinking and identical (with no flexibility), then of course that is going to hurt your ability to absorb variety. But Toyota (see “Toyota Talent”) doesn’t say standardized means identical and unthinking even in a factory setting.
In a services or healthcare setting, “standardized” can be guidelines for how and what to do things in “normal” circumstances, leaving flexibility and judgment and reaction and thinking. I would agree with Seddon that a call center with strict scripts that must be read is far worse than one where people get to have leeway to solve customer problems (like Zappos). To be identical and unthinking isn’t the definition of “standardized” used universally by the Lean world. By some sure, but don’t paint with such a broad brush that standardization always causes problems. In healthcare, standardization (again, not identical and unthinking) leads to lower infection rates, etc. in many instances (research Dr. Rick Shannon and those who have implemented “checklists,” a form of standardization with room for thinking and judgment).
As to the Womack quote about managers and engineers doing it all, I’ll stand by my claim that you’re cutting and pasting in a way that tells YOUR narrative, not the whole story that Womack wrote about involving everybody in the process.
You say:
To me, that sounds like a pitch perfect definition of TRADITIONAL management, not lean (dumbing down the work, small silos, more batching. Work being standardized from an internal, cost-focused view is TRADITIONAL MBA thnking, not Lean thinking. Lean gives people MORE scope of work (more cross training and breaking down silos to improve quality and flow, not having a “cost-cutting” focus. You’re misrepresenting lean to suit your narrative.
You say:
This is only true where it is true. It’s hardly universal. Again, painting with a ridiculously broad brush.
You say:
Does he give Brian J. Joiner credit for that (from his book “Fourth Generation Management”)???
I don’t think you’ve clarified anything other than the overly broad generalizations and poor assumptions made by Seddon and his associates.
you might be interested in our new addition to the English Language which is a collective term “an ARGUMENT of Conceptual Territories”, the proof for the existence of this new term is on this blog and at http://ping.fm/2h2BK
Oh BTW real name….
I think we really have to consider the clients here.
While some consultants are part of the problem Seddon referrs to by using a tool based approach and mislabling it as Lean (either on purpose or via a misunderstanding of what Lean is), some organizations do dont have the cultural or political readiness to instantly change their behaviors or thinking.
A consultant can work with leadership to change how they manage to support the Lean improvements, but a client can choose to ignore the advice. Just because an organization does not take a consultant’s advice doesn’t always means it is a problem with their skill (although that could be a factor).
A key element of Lean is being a learning organization. If leadership contines in a command and control fashion despite advice to the contrary, the water level will be lowered and the problems will be visible. Lean work is iterative and not “instant pudding”. I have faith that leadership will begin to see how old leadership styles will get in the way of true systemic change and performance.
In my experience, using literature or acedemics is not reason enough to get leadership to change. Clients usually believe they are different and/or can find conflicting management philosphies to counter the argument. We are working against years of conditioning that management by objective and that leadership is the smartest entity to solve problems. We have to meet clients where they are (command and control worts and all) and help them transform away from that. Culture change does not turn on a dime.
In other words, it is not Lean that fails an organization. It could be bad consultants. It could be clients that don’t take good consulting advice. It also could be clients that are still on a learning journey and defeat is called too early.
Been sitting in the sidelines, but I must speak my piece now.
For those of you not familiar with Seddon/Vanguard (and I suspect that will be the vast majority of you frankly – his opinion of himself is quite dangerously inflated), keep in mind that the self proclaimed “academic” John Seddon has a for-profit consultancy (Vanguard). He has people aligned to his financial interests in a very direct way (including Tripp and others).
They have a proprietary closed model that’s doing battle with an open, diverse lean movement with many voices. Criticism of their approach threatens their paycheck, hence their violent reaction in a very direct way.
Has “the Vanguard method” been fully published for anyone to look at with an objective eye? All we hear is Seddon and his scarily like-minded followers crowing about how it’s the best thing ever, like any salesperson would say about any product.
The Lean movement has taken arrows in the back and criticism for 30 years. Lean isn’t going anywhere. Bob Emiliani writes about this a lot – the criticism has been and always will be there. Lean isn’t a closed proprietary or even consistently practiced term/methodology. Lean is such a broad blanket term with so many variations and applications, it’s almost a meaningless term. So there’s this big vague airy villain for Seddon and his followers to attack and obfuscate.
I’ll take an open and adaptable system (lean is arguably “open source”) while Seddon’s movement will crash and burn from its inbred thinking. Lean is Google, Vanguard is Microsoft, we know who is winning that battle.
So, to the lean people I’d say this: chill about the noise from Seddon/Vanguard. They will be ignored like the bunch of loons that they are. Relax and do your work and keep your nose to the grindstone.
Keep calm and carry on.
You have to characterize systems thinkers as loonies in this way or you would have to explain to your clients why you have pushed standardization and tools on them. You obviously give your services for free as one of the many lean philanthropic consultancies of course.
Dreamon – I guess you didn’t catch that the first reference to “loonies” on this page was your man Professor Seddon throwing that at the lean folks (in his newsletter). Some example he sets huh?
Keep your nose to the grindstone?
Sounds like an admonition from Frederick Taylor to Schmidt.
You all lose me in the dialogue when you throw out a label like “loonies” (I’m from Canada,… a “loonie” is a coin in my pocket).
This is so great!
Watching all of the consultants vying for the title of Doge of whichever particular flavor of process improvement being marketed on this particular day gives me a chuckle when I most need a chuckle.
I am in a minority here since I am one of the few people passing though these hallowed columns of Lean Land- not often and for good reason- who actually owns businesses (ugly industrial stuff) in need of improving.
I can honestly say that after reading all this, I doubt that I would hire any of you folks on the simple basis that you all seem to live in some shared fantasyland of talmudic proportion hissing and swatting at one another over one’s use, or misuse, of some arcane term or concept.
Of course, we live in an age driven by consultant’s conceit: a conceit that promotes the ‘idea’ as being more important than the implementation of the idea so this behavior is probably inevitable.
In my world, the lowest, tactical granular worry of any given day has to do with the cost of hydraulic fluid, diesel fuel, keeping good employees employed, the cost of raw steel and things of that nature, and not so much with worrying about which interpretation of a word is the ‘right’ one. (That is a talmudic argument.)
As a military vet, I hear the word ‘standard’ and I think more of the standard as that flag hoisted high around which we gathered to do battle- a point of focus as one poster above wrote, a place to rally and commit to a collective effort.
I do not presume to know Taichi Ohno’s thoughts or his inner perspectives, but given the state of his nation in general and Toyota, in particular, after the war, I can imagine his version of standardized work had more to do with a call to action to save his country, his company and his countrymen around that standard and less to do with the trivial pursuit of term definition that has rent morons, idiot and liars into an otherwise interesting discussion.
Ha! Best post of the entire thread!
Synfluent…you said you were in VT to listen to a previous messiah speak at GE years ago…can I buy you a beer and we can share best practices? You deserve one after this post…I’m in Essex by day and St. Albans by night.
Bryan Lund
Frankly I think that the tradition of Systems Thinking goes back to seminal work by a number of great thinkers working together to look for common systemic structures across multiple discpilines.
I gather from my own studies that this included engineers, psychologists, anthropologists, operational researchers, biologists and many others. From what I can gather there are quite a number of different lively and genuinely insightful strands in contemporary Systems Thinking which are quite open to investigation (EG SODA, Viable Systems Model, Critical System Heuristics and Soft Systems Methodology just to mention a few). Against this background it seems rather unfortunate that what should be a synergistic interchange is characterised by such partisan views. I have to observe though that I’ve always tended to take a rather poor view of denigrating potential clients by name and on a public forum. It would most certainly make me question the ability of the author to maintain any degree of discretion.
Most important though is surely that readers should be aware of the fact that there are wide ranging and rich open resources on the web dealing with multiple expressions of the Systrems Thinking tradition.
They won’t cost you a fiver a shot either.
@Mike- Unfortunately, there are even factions in the “systems thinking” world (a legacy that includes great thinkers like Dr. Deming, Peter Senge, Brian Joiner, Chris Argyris, and many more).
This John Seddon crowd not only stomps on “lean” but they have to further elevate themselves by describing their work as “New Systems Thinking.”
Well from what Vanguard openly divulge there’s nothing very new about it as far as I can see. Though no doubt saying this will risk having opprobrium heaped on my head. I guess it’s a question of “new to who?”
It seems to me (having studied lean to some extent during my MBA) that TPS embodied a rather similar eclectic and synthetic spirit as ST (or for that matter many areas of study aimed at illuminating and enlightening practice).
My reeason for joining this debate is really to point out that I don’t think the blustering opinionated stuff I’ve seen here should be taken as typical of all those engaged in ST approaches.
As someone with a great deal of interest in ST both theoretical and applied I don’t think what I’ve seen here is doing the wider ST community any favours at all.
Yes, agreed. +1
Name even one of those systems ‘thinkers’ if you may.
I started reading this with interest but it soon faded.
There are several points I’d like to make as a person who worked in Toyota for 15 years. The first being that I am sick and tired of academics that ‘don’t get it’. If Lean was born of an academic study of TPS then why does Lean miss the point and this while system v tools argument exist?
The simple fact is they are inseparable! The tools are the answers to situations and problems that are highlighted through a systematic approach. You cannot have one without the other! Implementing tools because they simply exist is the work of a madman!
Why do you think Toyota call it a production system? Is it because they have tools or is it because they apply them systematically?
Academics of TPS take note. Knowing some of it does not make you experts. That applies to both sets of followers here! To pick up the point of who sets the standards, then the answer is simple. It is a translation of the drawings that is documented by the engineers. Who creates the Standardised Work to achieve these torque and other standards. Well that is the operators themselves. They decide the method.
One other point. Problem solving is not Kaizen. Kaizen is Improving on an achieved standard, problem solving (properly titled “Iji” translated as maintenance) is returning to a standard not being achieved. In both cases a standard is required, be it one set by an engineer or an operator as both should achieve a common end. THAT is what Ohno-san was referring to.
I work for a Lean consultancy now, although I refuse to call myself a consultant. By definition, a consultant is somebody at the top of the profession they are being consulted on. How long did it take Toyota to be a Lean organisation? Answer: they are still trying
Have they achieved anything by reading a book or by getting dirt under their finger nails. I read a book about 747s the other week, am I now a top pilot?
Think about it.
Alan – thanks for your thoughts. It sounds, then, that Womack, Jones & Roos properly described what Toyota does (engineers develop standardized work with operators). Mike Rother in “Toyota Kata” writes that production operators at Toyota don’t have time to do kaizen, that it would be “disrespectful” to ask more of them than they have time for. Interesting.
I work in the healthcare realm where there are no process engineers. The starting point for improvement is chaos and basically “no system” so the best people to design and improve a new system (and we give them time away from their regular job to do this) is the front-line staff – nurses, techs, pharmacists, etc. — not the managers.
The ‘best people’?
The utterly clueless or just the mostly clueless? My folks are mostly of the former type as opposed to the latter type.
At any rate, it sounds like a wonderful well font from which to draw and fill the vessel of Lean success.
Synfluent – I didn’t think you were a part of the misanthropic “everybody is stupid” camp. Come on, man…
I am of the camp of those who really ‘do’ something and really make ‘payroll’.
Remind me, again: what do consultants really do besides pontificate?
Actually Mark, you have managed to miss my point massively. No, engineers do NOT work with operators to develop standardised work. They set the standard of the end product to be achieved. What the operators do is design the method of achieving it. Two very different things!
Your post suggests that Toyota has process engineers. Do they, really? I’ve never met one!
I now also cover healthcare. The model Toyota uses very much applies. No Nurses, etc. cannot dictate what is “good” medical care. They have standards to achieve. But by applying the thinking and process of achieving these standards in the same way that Toyota operators do still applies. I have successfully applied this in Hospitals (pathology labs, wards, operating theatres included), office environments, call centres and manufacturing environments many times!
My point is, that both “sides” of the arguement above are wrong! Lean (typically, from what I have experienced of many consultants) and “systems thinking” (like thats an invention!!!) are both misinterpretation of what was being studied! Academics on both sides have clearly missed the point!
@Alan – I wasn’t trying to refer specifically to Toyota. I was referring to process engineers at the different manufacturing companies I worked for.
Maybe engineers *should* work with production people to draw on their experience.
Mark,
there is a thinking way in Toyota that nobody knows the job better than the person who does it every day. It’s a fundamental in TPS. If an engineer walks down to the assembly line and tells an operator how to do their job, they wouldn’t make it back to the office! The standardised work they have created is based on a huge amount of knowledge and experience. Quite different to the knowledge and experience of a good engineer. That is why an Operator will never tell an engineer how to do their job in Toyota! They have that mutual trust and respect that is often written about but little understood!
This is not difficult. I do not get the point of the opening post. Was it to highlight a fundamental problem in Consultancy or was it to take a snipe at a particular segment of it? In either case, my earlier point stands.
Both are wrong!
The point of the post, for what it’s worth (and it’s not much) is that the John Seddon crowd is trying to make a career out of straw man arguments and blanket attacks against lean and, in particular, Womack and Jones.
And my point is that both Seddon, Womack, Jones, [insert academic here], etc. do not understand the ethos of what they have studied. They have got the methods written but not the thoughts of the people applying them and what motivated them to do so.
They think they get it and that it was about numbers and standards. Because thats what exists on paper. What they missed was the mindset and the thought process that exists in somebody that problem solves every day. They are so far up their academic backsides that they must be right. Sadly, they missed it. By a country mile!
When I visit clients and tell them about this stuff, I get challenged with “yeah but Toyota are Japanese and they have a different culture!”, my reply “yeah but my factory was in Derby in the heart of the UK and matched the culture of every Japanese plant”. So! Considering all this, whats left unanswered! Seddon got it wrong? sorted. Womack and Jones got it wrong? Sorted.
What questions are left unanswered?
@ Alan – I think John Shook will bring his practical Toyota experience into the fold at LEI in his new role as CEO, would you agree?
Synfluent,
see that tarred brush in your hand, could you put it away please!?
I don’t know Mark. I left Toyota 5 years ago and have never met him.
But after a year in Japan out of my fifteen with Toyota and working with folk from the Toyota world, my expectations are yes he will. There is a simplified and westernised version of a Toyota principle that is commonly known as “Go and See”. The real Toyota princple is “You do not think and you do not speak until you have experinced it for yourself”. I apply that all the time. Even to your question below!
I am sharing, with permission, some comments from somebody who only wants to be identified as “an ex-Toyota employee from Japan.”
On this topic, he writes:
“Not sure why anyone would call Jim or Dan the “Tools people”. If anything they started to move lean beyond the “tools” of kaizen events and at least in the direction of “flow” and “system”. Lean Production in 1990 I have not re-read in many years but I’m sure there are quotes in there about the system (and they went beyond just manufacturing). That is pretty easy to establish.
There is no quote that can be attributed to Ohno in Japanese about what to do first standardization or otherwise…his only comment regarding implementation was to “Depart from needs”. His main comment about standardized work was that you have to do it yourself to learn what it is.
He put a special group together that became known as the Operations Management Consulting Division around 1970 to start explaining TPS to tier one suppliers. Fujio Cho and Kikuo Suzumura were the two most famous in that group. One of them or both started telling various parties that there is no continuous improvement without standards.
The did not mean “standardized work” however. Standards in Japanese literally just means a “baseline for comparison”. Numerous people after that have used the “no improvement without standards” statement inside of Toyota. So I suspect that Jim and Dan picked it up there from their numerous visits to Toyota.
My friend Isao Kato wrote the current Toyota Standardized Work course back in 1968. He has or had slides in the text in Japanese that stated there can be no improvement without standardization. Not sure who said it first.”
So his take is that there’s not a quote that can be directly tied to Taiichi Ohno, but it seems clear that the expression was used by many people in Toyota and was NOT made up by Womack and Jones, as Professor Seddon charged in his podcast.
[…] no room or need for “process improvement turf battles” as we’ve seen here on the blog recently (and often the very ugly side of it). By “any approach,” I mean THEIR approach – […]
Hello Mark and all other contributors to the thread!
Due to the voices in between which had not much to do with a lean attitude at all, I sidestepped for a while.
Scanning through the comments from top to bottom now, I have the sense that we are talking about something that seems relevant to most of us. Otherwise we would not share a minute posting something, would we?
Working as a non-engineer (economist) in a purely driven engineer culture at BMW for about five years in Leipzig, I can tell that what you get with lean can be so different as mice in different areas of the globe.
Seeing lean always through “economists goggles” there is much more in the process than the production line on the shop-floor. The biggest potential -that is mostly still under the surface- lays everywhere in the process of creating value but not in the production! Especially taking other wording than the typical “lean” words you are quickly an outsider and alien, even though the problem pattern and way of solving are more than similar to the classical lean approach.
Wording or language in general can be so fast be a “killer” of good intentions and we should be aware when our own mental models are taking over our rational thinking! Some short thoughts on that around a small event lately (cup of coffee with lots of milk – what does that exactly mean?) http://leanthinkers.blogspot.com/2010/08/language-bottom-line-to-understand-each.html
If we focus on production we miss the larger overhead and pre- and after part with all its administrative processes, and especially the institutions that set the setting for companies to operate, should be in our all focus. (At least if we really mean lean in the “pure sense”, which means creating true value with the least amount of hassle (whether it may be stress, physical resources, and the seven wastes of muda in general – I would like to add a No. 8 “putting people on the wrong position”)).
What JohnSeddon, in my eyes wants us and the lean community, wants to make aware is that boiling lean down to the scientifically solved standard processes will inevitably lead back to the problems we had in the beginning. Using some not so nice wordings -even though they sound harsh- are sometimes necessary.
To my knowledge to all the literature that is around (and I have read a lot in the last 10 years) in print or the web, TaiichiOhno (and not just him) were not talking in nice words to the managers and workers in the factories of Toyota when he found something not working. So we shouldn’t throw stones on JohnSeddon, rather should understand, what is the underlying problem that we together could solve.
Due to the length of the blog entry most of us perhaps don’t remember MikeRother’s entry early on. I liked it very much:-) Worthwhile rechecking once in a while!
I’m wondering how many hats fell off when those points flew over their heads!
I’d kindly invite readers to view my comment on Evolving Excellence:
http://www.evolvingexcellence.com/blog/2010/02/thanks-craig.html?cid=6a00d834521be169e2013488050ec2970c#comment-6a00d834521be169e2013488050ec2970c
Where it appears that, in the video linked to there, that John Seddon is taking credit for the work of Brian Joiner.
Video:
http://www.evolvingexcellence.com/blog/2010/02/thanks-craig.html
I have to tell you this leanblog has more drama than TV. Conspiracy theories, fake Toyota employees and the anonymous “linker” that posts 8 months later on a separate website with a video that doesn’t work.
Get a grip.
The truth behind the name “New Systems Thinking” has nothing to do with arrogance or high treason or any other paranoid scenario Mark can muster. It has to do with the fact that the name was the only one available when I reserved the website.
What were we talking about again?
Tripp – the video works, I just clicked on it. It’s probably not Commodore 64 compatible, is all. If I were truly into conspiracies, I’d think you were saying that to get people to not click on it.
Sigh, you can think things are conspiracies if you want. My blog post has drawn some people out of the woodwork who have all sorts of stories and I guess one of those people shared the video. Seddon has more detractors than me and I’m hearing stuff of the “you can’t make this up!” category. I assume you think the email I posted must certainly be fake while the ex-Toyota guy (which we can’t verify) who agrees with you is real.
That was the ONLY website name available? Really? TrippsBizarroLand.com was taken? At least you differentiate yourselves from Peter Senge, etc. and the original systems thinkers. I was using what I thought was the proper name for your movement, “new systems thinkers.” That wasn’t a slam. Sheesh.
Were one to distill the advice of Edwards Deming to its essence, it would be “don’t tweak.” Respond to noise in a non disciplined fashion, and all you do is exacerbate what you meant to improve. Hence, Statistical Process Control (SPC) to distinguish real problems (process drift) from normal fluctuations in repeatable processes and Shewhart cycle (PDCA) to impose the rigor of the scientific method on change.
Of course, Deming was not the first to arrive at this view that discipline in design is a precursor to discipline in change.
Even the most rudimentary high school lab demands that an experiment be written before it is tried, that the equipment be cleaned to ensure the outcome is the result of the design, not the arbitrariness of dirt and other perturbations injected into the process.
Do you know if a recipe worked? Only if you followed it.
So too with Toyota’s commitment to specification as a precursor to improvement. Without defining what you expect to do and what you expect to happen, you cannot meaningfully determine if what is happening is a bona fide problem or merely the result of work done out of control.
Hence, all the famous tools of TPS carried over into the lean world, and the many others not so popularized, all do double duty (when used as at Toyota–a very strong qualifier): They help specify what is predicted/expected of a process design and make clear when reality departs from that prediction.
— Heijunka? Make clear expected output and make departures (ahead or behind) visible.
— Cells, flows, and the like? Make clear expected work sequence and responsibility and make departures from those expectations visible.
— JIT/Pull/Kanban: Make clear what has been requested and make visible that a request hasn’t had the appropriate response.
— Standard work and 4S (with poke yoke and jidoka): Make clear what approach is expected to lead to each person’s successful outcome and make visible when work is progressing contrary to those expectations.
Two anecdotes on which to end.
One: When I was doing my research with Toyota (and still to this day), I couldn’t visit a site without first predicting what I expected to see and what I expected to learn. If I didn’t, how could I legitimately be surprised that I had seen anything new?
Two: I was on the phone with the head of a major retailer and along time Toyota veteran. After the retailer went on and on and on about hsi firm’s commitment to kaizen, the kaizen spirit, and continuous change, the Toyota vet finally commented:
“You just don’t get it, do you?”
“What do you mean?” was the response?
“You think we’re all about change this change that. But you have no idea how hard we work to first standardize and stabilize before we make changes.”
“What do you mean?”
“Well, what we do is really really complicated. If we did what you describe, we would never get better by learning day in day out. We would just be churning fruitlessly.”
In short: design work so learning is an inevitable consequence. If you don’t make that investment, life is lived on nothing but a chattering plateau.
Respectfully,
Steve Spear
http://www.TheHighVelocityEdge.com
Twitter: @StevenJSpear
Excellent observations and additions to the discussion.
Thanks.
“- Heijunka? Make clear expected output and make departures (ahead or behind) visible.”
Ehhh… I think ur confusing the hour by hour board with the heijunka box Mr Spear. Visual management of progress has nothing to do with heijunka which is scheduling by “level volume and mix”. Time to stop making speeches and go see for urself Mr Spear.
A couple of observations (and I have no skin in this game). John Seddon is free to call anyone anything he wants, we are (within reason) a free country so he can “have at it”.
That said, one of my former employers once told me “it does not matter how smart, or how right you are if no one will listen” and I find that JS to be a annoyingly smug in public and in his writing and I don’t think calling anybody an “idiot” or “loon” is going to engage them in the process of examining how they work but if that works for him, so be it.
That said I do not think that JS has the market cornered in being controversial, at least on of LEI’s consultants has publicly advocated the use of no consultants unless they can trace their professional pedigree back to Ohno him self and he does not believe that consultants more than 2 degrees of separation from Ohno should be used.
Thanks for chiming in Andrew. Look out, you’ll get criticized for not having a surname ;-)
This is a friendly nitpick, but LEI doesn’t have consultants and LEI isn’t a consultancy… I think the person you’re speaking of is an independent consultant (he has his own business) who has books published through LEI. There’s no strict LEI orthodoxy that must be followed as there is in the Vanguard pyramid.
I think his opinion about the pedigree is wrong, but that’s his opinion and not LEI orthodoxy.
I accept your distinction about LEI but I’m not sure that when individuals that have an association with them (specifically the UK version) that this separation is made clear and that the fact that it is not LEI orthodoxy is made clear.
At a number of events that you and I have both attended people associated with LEI have presented work done in organisations (or imagined work or not even started work in one particular case (n.b. it was the first time I’ve ever seen someone new in post talk about what they would do in the future in a plenary session but leaving that aside (they got that session soley because they let LEI in their organisation)) and one would be hard pressed to see any difference between their presentations and those done by any consultancy you could care to mention.
I have to be honest and say their are individuals (consultants) that I like to listen to and who I think have something to offer. They are generally facilitative, inclusive and interesting to listen to and they include Mike Rother, John Shook and S Spear. In fact I found Womac to be quite amusing, though I’m not sure whether it was intentional or not.
There are others who I could literally pass out from boredom listening to and who I will not name (these are not dangerous but simply boring) but there is a third group who I have a visceral dislike of because they come across as sanctimonious and pious and seem to hold their audience in complete contempt. This group is the one that does “lean”, “consultancy”, “coaching” etc a huge dis-service as they switch people off and to be honest, no matter how smart or bright they as individuals might be, we’d be better off without their contributions as they do more harm than good.
To try to further clarify the sometimes unnecessarily-muddled waters, Dan Jones and the Lean Enterprise Academy (UK) do consulting work as do some of the other organizations that are affiliated with the US-based Lean Enterprise Institute. http://www.leanglobal.org gives a list of those orgs. The LEI is a 501(c)3 non-profit educational institute by legal structure.
Dear Mark et al,
Mike Rother, started an interesting discussion which seems to have been “caught in the cross fire”. It very much deserves investigation. What is the value of defending a term (i.e. lean) anyways? Why should we bother redefining it or separating real lean from fake lean (as my friend Bob Emiliani did – although I respect his thinking).
1. I think Mike’s hypothesis deserve a lot of attention. Lets have a separate blog post on that. Lets continue the discussion.
2. Lets tone it down guys (especially Bill ‘no-surname’). But also yourself Mark. Not very common in scientific circles to throw words such as ‘liar’. John Seddon is actually very down to earth at a personal level; you just have to get pass the public speaker facade (which he might think is necessary in conveying tough messages). He is within his rights to insult public servants who waste our money in the UK. It’s called freedom of speech! When you assume a position in politics or public sector, you are expected to “live with” harsh comments. Especially if you are as incompetent as the ones we have in the UK. But in scientific circles, such as this one, lets tone it down…
Cheers,
Keivan
Keivan-
This is worse than partisan politics where one side attacks the actions of someone in the other party and then looks right past the same behavior in their own party.
I was being intentionally provocactive in saying that Seddon might be lying to A) get his attention and B) throw some of his same behavior right back at him. He has been runnnig around impuning the reputations of Womack and Jones – saying they basically invented an Ohno-ism and they are just doing this to make money (his comments that Womack sells his consulting services to anyone who wants them, when Jim is not a consultant).
On the “let’s tone it down and be scientific” front, Seddon continually calls people names in his newsletter, Tripp calls me a “moron” and calls me “sick”, let I’m singled out to tone it down and be scientific. Seddon thinks anyone who has a different view is a “loonie” or a “nutter”. Not very scientific.
I’m not defending a “term” here. I’m defending ad hominem attacks, straw man arguments against lean, and overly broad blanket statements. Howard, the editor of the pseudo-academic systems thinking review journal that’s been created says things like “lean is inherenty command and control” – that’s not very scientific of him to throw around opinions as pseudo-academic fact. Seddon and his crowd conveniently define lean in a way that’s misleading and allows them to attack it (and he accuses Womack of being greedy and self-serving).
As to “freedom of speech,” that is an American concept, thank you very much. I would defend Seddon’s right to say whatever he wants, but with that comes a right to A) criticize his behavior and B) criticize his words in return. Seddon is quite right to criticize the regime of targets, especially the dysfunctions in the NHS (like the 8-minute ambulance target). I can understand his frustration with the British government.
A number of people have come out of the woodwork to tell me John Seddon stories or about how people have been “traumatized” by his approach. Since England doesn’t have the same freedom of speech that we have here in the U.S., they are afraid to speak out for fear of being bullied or for fear of legal action.
As to the link posted yesterday, it’s not very “academic” for Seddon to say clearly “I developed” this “check” business when it’s obviously written about in Brian Joiner’s book from the early 90s. Academics are supposed to give credit to others for their work.
So, yes, let’s “tone it down.”
Mark, You bring up an interesting point: when are people consultants? I would say LEI and any other lean practioner is an expert (because his/her knowledge is not mainstream knowledge in the workplace).
A consultant (in the sense I and EdgarSchein see it) is someone who tries to help the client to see and understand his/her own processes and support him/her to improve the processes in question through their own knowledge. More in a 1990 MIT Sloan Management Review article by EdgarSchein: http://hevra.haifa.ac.il/~soc/lecturers/samuel/files/651256216654.pdf
Are we helping or just giving advice?
Mark, Steve, et al,
Let me present you with a real life example (recent too!).
I was at the HQ of a multinational. Fairly new on their lean journey. Yet the person in charge of lean is very critical of Jim, Dan, LERC, and pretty much everyone else. This gentleman is basically creating loads of standards, procedures, lean methods, etc. He asked me a lot about various lean techniques; kept asking about how to use them and what they are. At some point he asked me what a certain tool is. I even thought he is testing me! I politely answered I don’t know enough about it. Also asked why he wants to know about such diverse array of techniques. His answer was (I quote) “how could you help us improve if you don’t know about lean tool”. Interestingly the techniques he was asking about were not diagnostic tools or systems analysis methods either. They were “solutions”. I couldn’t believe that a very successful organisation with good reputation, has people who jump to solution without understanding the problem (or even having those problems). A lean office which is creating work for itself by generating standards and work methods, instead of designing the lean office out (which is presumably the ultimate goal of any lean practitioner). I listened to Mike Rother recently and he was telling a similar story – not all that different from a European retailer. Mike is reading this hopefully will correct me if I have misunderstood / misquoted him.
This is an example why I think, the “lean movement” has contributed to the “problem”. The problem is that we have too many “toolheads” (to quote Seddon) behind the wheel. Standards, in the sense that Steve says are OK (and necessary too). In Steve’s comment above, the standard is a temporary condition. Means to an end; not an end in itself.
Frankly, I think the western management culture (especially American) has not really got the point about Ohno and Toyota (right tone?!). My point is that, TPS is rooted in a certain paradigm and certain thinking which is alien to conventional (or modern) management. There are traces of obsession and evidence of “self sacrifice” in TPS which cannot be easily replicated outside the paradigm out of which TPS appeared. Maybe we should change our thinking first, then worry about lean tools.
Kind regards,
Keivan
Keivan, thanks for the thoughtful reply.
I agree with tools and solutions without first understand your current situation is a problem. Going back to my J&J days, our consulting methodology with clients spent a great deal of time with hospital staff and managers observing and understanding their current state. This didn’t mean just doing a value stream map (often, we didn’t even do that) – but it meant talking to customers, standing in the ole’ “Ohno Circle” for hours on end and making sure we understood workload (demand), the current process (or lack there of), the waste, and the staff frustrations.
You can’t just go in and plow ahead with tools.
I’m down with that.
So to your story, I’m not sure I quite follow the narrative. These folks were trying to use tools and they were critical of Jim and Dan. Why were they upset? Because Jim and Dan only talk about tools? I know more about what Jim says and he’s not a “toolhead.” He never worked at Toyota, but he’s not a thoughtless toolhead. So if you could explain why they were upset, that would help.
I think this is a chicken and egg problem. Yes, there are many toolhead consultants. But, there is also a huge market for Western managers who want “quick fixes.” As Dr. Deming said decades ago, “there is no instant pudding.”
I would turn down business from somebody who just wanted quick fix tools and I’d especially turn down business from somebody who just wanted cost cutting and/or layoffs. Life is too short to work with clients like that.
But not every consultant shares that philosophy, they want/need to put food on the table, or they’re opportunistic and happy to take money from a client for giving the client what they want (even if it’s not what the client needs).
To standards, I’ve always taught standardized work and kaizen go hand in hand. You have to first understand your current condition and how things are done today — but then improve!! Not static. Not top-down. Not “rolled out” (people being rolled over).
I don’t understand the rancor thrown at me by the John Seddon crowd because we’re in sync on 90% of things, it seems (from what I can tell of the Vanguard Method). I feel like I’m attacked because I’m not part of their little club, which is strange… and I clearly do not want to be in their club (because of their behavior and attitude).
They attack me when I think that rancor should be pointed in other directions.
But what do I know, I’m a moron, so says Tripp.
Thanks Keivan. Your last statement echoed my thoughs.
I’m very early in my consulting career (I focus more on workload management and its effect on individual and team performance), transitioning from 18 years of clinical and leadership work within healthcare, but, despite my novice status I’ve already frequently come across the manager/leader that “just does not get it”. Healthcare management is historically a culture of command and control with only pockets of exceptions (e.g., Mayo clinic, Cleveland clinic, etc.). I’m a small part of an enormous “tranformation” project that will only be successful if managers not just see that they will have to manage differently, but, more importantly actually start behaving and thinking differently.
Regards,
Ron
Related blog post:
http://sysparatem.co/blog/?p=47#comment-419
In a comment, Ben (@antlerboy) wrote this, in part:
It’s obvious that somebody in the Seddon camp set up a brand new twitter account, @LocalGovIT, with the sole purpose of lumping abuse on @antlerboy, who had the nerve to criticize Seddon on that other blog. That account uses the exact same phrases as “BAllan” who posted comments here.
Tripp – it’s clear that you and the Seddon crowd complaint of “dirty tricks” because that’s your game and you know it well.
The longer you play these games, the more you expose the way you operate.
Anyone ever come across any Shakespeare scholars? There are quite a few and you can make a pretty good living at it. They spend a lot of time advancing different theories about Shakespeare. A very small number of them are actually quite interesting but of the others the poet Alexander Pope commented that “they appear clever in the same way that a fly caught in amber appears beautiful”.
No relevance to this discussion of course!
:o)
[…] a follower of Mark Graban’s Lean Blog, you will definitely want to read his post entitled The One Where John Seddon Might Be Lying.Mark Graban critiques John Seddon, Systems Thinking, Systems Thinking in the Public Sector, and […]
It is about time that the Lean community engaged in constructive debate.
I am Director of the MS program in Lean Operations at Lean Enterprise Research Centre (LERC), Cardiff University. LERC was started by Dan Jones, and we appointed John Seddon as visiting professor for a three year term almost three years ago. Our MS students are all practicing managers engaged in Lean implementation. Age range 28-55. Dan Jones has recently spoken to our current MS class; John Seddon is due to speak shortly, and has been most thought-provoking to previous groups.
Virtually all our students love both Dan Jones and John Seddon. Our students don’t necessarily agree with all that Dan and John say. But that is the point. Both of them have many valuable points to make, but not necessarily in the same area.
I was first exposed to what is now called Lean with Toyota South Africa in 1982. 1982. I am still learning. And I realise that we all have a great deal still to learn. Hence take note of Steve Spear and Mike Rother (both of whom have spoken at Cardiff). Anyone, but anyone, who claims to have all the answers is deluded. There are elements of TPS that work pretty much everywhere, but certainly not all of TPS works in all environments, as some would have us believe. John Seddon says he does not know about manufacturing. I believe Dan Jones has limited exposure to local authorities and service. Obviously many things have changed since Deming and Ohno, not least employee attitudes and education and the internet including web 2. (But, by the way, I am surprised that TWI JI Job Breakdown has not entered the discussion about standard work.)
Vanguard (Seddon) methodology and cases have been quite rigorously examined by at least two independent British academic groups in a longitudinal way. By the way, I don’t know of any similar studies of Lean implementations, at least since ‘The Machine’. (The Shingo Prize is not a rigorous longitudinal study in the same sort of way. It is an evaluation framework, useful for that purpose. I was a Shingo examiner.) The results showed some remarkable achievements but also some shortcomings. John Seddon has made some remarkable contributions, not only on awareness of failure demand, but also on engagement, ‘roll in’ and measures. I have experience of John Seddon being most conciliatory and helpful. (Maybe, unlike some of his disciples.)
And so too with Dan Jones, and some of his disciples. But both have ‘stood on the shoulders of giants’. We at LERC recognise both.
In Lean and in Systems everyone borrows. It’s the way to make progress. That, and humility. As with religion, the most ardent devotees are often the newly converted. We all need to make an effort to remove the filters that work against seeing the other person’s viewpoint. I have them also.
Rather than nit-picking about who said what and whether quotations are correct, look for the amazing opportunities that exist for both Lean, Systems and of course Lean-Systems Thinking. To mention a few: Web 2, Agile software, Design Thinking, Viable Systems Model, Churchman’s long-forgotten inquiring systems, Brain research, Learning, thoughts on Value, accounting for Lean, Factory physics, followership…… We need Dan Jones, John Seddon, and many others. And, as Lord Keynes said ‘When the facts change, I change my mind’. It’s PDSA.
The point is we all need to learn from failures. Whilst a certain number of success stories do show that a methodology can work, the greatest learnings come from honest reflection of failures. Of course, people – especially consultants and authors – are notoriously reluctant to admit failures. I look forward to the Lean and Systems Failures conference. What tends to work and what does not work, where and why.
I must say I think Mark Graban seems to be increasingly polemical and digging a hole for himself. He started an excellent discussion, but this now seems to be degenerating into a slanging match.
Thanks for your thoughts, John, and for being upfront about your working relationship with Professor Seddon.
Those who regularly read my blog know I’m not a polemic or a verbal bombthrower. I certainly recognize and honor those who I have learned from (and I’ve spoken positively about Seddon’s book on my blog). I never claim to have all of the answers and I admit Lean isn’t perfectly executed and that all Lean tools aren’t perfectly applicable (but the high level management system and culture is applicable and arguably MORE important in healthcare, services, and the public sector).
I’m not trying to say “lean is good” and “Seddon is bad.” I’m not setting up that construct or fight here. Seddon and his followers very often say the opposite in their attacks on Lean, and Jim and Dan. Their method is perfect, everyone else is incurably flawed. They imply Jim and Dan are greedy and trying to just make a buck with selling Lean to toolhead command-and-control people. That’s outrageous and unfounded.
What I’ve attempted to criticize is not the Vanguard Method, but rather Seddon’s rude, personal, inflammatory attacks on others (see his monthly newsletter) and his misleading blanket statements about “lean is a wicked disease,” for example. This does incalculable harm to society if people are turned off from even exploring and learning about Lean as a result of Seddon’s rancor and noise.
Maybe Seddon is a sweet, thoughtful person. His online persona is actually quite the opposite. What I’ve learned with internet bullies is that they back off once you punch back (I guess this is like the schoolyard). I don’t spend my life looking for people to verbally punch… I feel like I’m defending myself (and lean) against bullying behavior that Seddon and company have demonstrated for years.
My post here was intentionally polemic – my attempts at parodying John’s behavior aren’t recognized as parody except by regular readers. But again, I’m criticizing behavior and tactics, then out come the insults and personal attacks from the Seddonistas, such as I’m a “moron” (Tripp regularly reaches new lows in lashing out with insults instead of reasoned argument).
So, as I’ve suggested to others, Mr. Bicheno, it’s hypocritical for you to tsk tsk me for behavior that’s commonplace from Seddon and company. There is an obvious double standard, as has been shown by other commenters here (all who have some direct financial tie to John Seddon, you’ll notice).
I will recognize (and I do) that John Seddon is teaching many powerful ideas (from Deming, Ohno, Brian Joiner — oops he doesn’t acknowledge that). I believe in these ideas strongly. I’d suggest you recognize Seddon’s harmful, bullying behavior. He’s the polemic.
One unintended consequence from my post is the outpouring of contact from all of the enemies that Seddon has apparently created in the last 10 years. They have been bullied into not speaking out in public. It’s not my intent to hear all of their grievances or to pass them along, but their experiences confirm my impression that Seddon is not just an internet bully in his approach with people.
Seddon works for you, I don’t blame you for trying to defend him and your university’s reputation.
I’d guess in the several years that this blog has been in place that there’s not been a post that has generated this response.
I’ve received JS’s newsletters in the past and they are pretty denigrating to anyone that is not drinking his own particular brand of koolaid, which I find to be as annoying as many of the publications that have come out of LEI. (specifically fictional stories about automotive execs running hospitals, a crime against publishing if there ever were one)
There may be some irony in that John Bicheno, the author of the “Lean Toolbox” is defending JS who routinely refers to “lean” practitioners as “Lean Tool Fools”. (I happen to own all JB’s books and use them as reference tools and they are very comprehensive in their scope)
I will say though, that this thread has caused me to return to JS’s newsletters and whats more interesting than this debate in some ways is that JS likes to make the argument that his work is founded in part in the work of Ohno and that he has kept to “chosen path” but others such as Jim Womac (just one example) have lost their way by becoming “Tool Heads”, so I suppose what we could take from that is that JS is “true lean” and the rest of the world is well………….not.
This argument is simply never going to be won. I find JS condescending and annoying but there are plenty of others that I feel that way about in the “lean” world, so I’m not losing to much sleep over it.
The publication I believe you are referring to comes from the Lean Enterprise Academy (Dan Jones’ organization). It’s affiliated with Lean Enterprise Institute, but they are not one and the same. LEI does not sell their publication at lean.org.
Correction, it’s not listed on the Healthcare page at lean.org’s bookstore.
I think you might find they do :)
http://www.lean.org/Bookstore/ProductDetails.cfm?SelectedProductId=260
though perhaps they should not…………..I just can not imagine giving this to any of the CEO’s / Exec’s that I know and saying, here’s a fictional story about how you can change your organisation around its premise is a failing organisation that hires a new CEO from an automotive tier 1……..
They would think I was barking mad……..
Talking about persons only, such as JohnSeddon, MarkGraban, and all the others, dismisses the power of lean thinking: focusing on the process!
What would the process look like taking JohnSeddon and MarkGraban out of the equation of discussion (I don’t call it a conversation or even a dialogue at this time)? What is the underlying structure that is not obvious to us to see?
Ralf, anytime we expect these gurus to be a hero, we’re bound to be disappointed.
I think the reaction to John Seddon would be different if he didn’t speak with such cocksure pomposity. He could have said “Jim Womack and Dan Jones say that Ohno said first you must standardize… but I disagree with that interpretation of Ohno’s writing… and here’s why.”
There’s a difference between speaking the hard truth with no B.S. and being a prat.
Seddon loves to drop “Ohno taught me…” as if he was a protege’ at the machine shop in Japan. Such pomposity. You read his freaking books like the rest of us, John, or did Ohno guest lecture in your psychology classes?
Now John Seddon has no monopoly on pompous windbaggery – have you read Jim Womack’s emails? Seddon attacks people rudely. Womack atttacks us by not having an editor and by droning on and on. But those are done. I’ll expect more from John Shook until he proves disappointing.
None of these guys are worth hero worship.
Keep calm, carry on. Do your job and work hard, don’t worry about the nattering nabobs of negativity and guru-ishness.
And, yes, I’m being a prat too, I suppose.
What is really bothering us in context of this conversation? What has triggered our very personal “hot buttons”?
Stepping down the ladder of inference to get to the raw data and understanding the dynamics (isn’t that the real notion of lean thinking that Ohno and Shingo have promoted for decades? I hope so, that we are collectively capable of doing so, otherwise the lean community probably will go down as have the great societies of the Romans, Aegytians and others – this would really equal a massive waste or MUDA as we say).
http://blog.pegasuscom.com/Leverage-Points-Blog/?Tag=ladder+of+inference
Glad if some of you are interested to explore more. Setting up a Skype conference call/ chat, I would be happy to do so (if requested).
Cheers, Ralf
I think a better analogy would be the splintering and the factions of the Scientific Management movement, which has been highlighted and written about by Bob Emiliani.
From his book, see: Real Lean Vol. 2 – Ch. 1, 2, 3, 4, 10 and Real Lean Vol. 3 – Ch 1, 7
As a UK practitioner who has fallen foul of Seddon in the past, like you I have big problems with him and his approach. The basic problems are (1) he tries to be polemicist, academic and consultant all at the same time and confuses what is needed in relation to each role (2) he slags (i.e criticises, as we say this side of the pond ) the approach of his competitors in public – not in my view an ethical business practice – he should just get on and do what he does (often very well) and let it speak for itself. I would guess that for every two people he turns on, he turns one off. It’s self-defeating for him.
With a final comment on this blog, all one has to remember is that John Seddons original site was lean-service.com.
Seddon, at that point in time, was in a market that was becoming saturated with “lean” so the two possible outcomes were to “ante up” or to “fold”. Seddon “folded” and at some point changed his companies domain and distanced his self from “Lean”.
The problem he has is that his site was “lean-service”, clearly he has since had a “crossing the rubicon” “moment”, or subsequent “epiphany”, but let no one here forget for one moment when posting that his original site was “LEAN-service.com”.
For all those acolytes, if you’d been paying attention your “chosen one” was as bought in to “lean” as Dan Jones, Jim Womac or the the next consultant. It simply turns out that at some point post 05/06 he felt that “systems thinking” would more clearly reflect his personal offering. A cynic, on the other hand, might think that it was needs must, and that you’d exit a saturated market, change the offering, and disparage a methodology that works (to whatever extent) for some organisations.
Whilst I’m at it, I forgot the link for the acolytes in case “they” forgot their “chosen ones” particular history……..
http://www.lean-service.com
Type it in your browser, if it does not work, happy to send a screen capture showing
Lean-service.com – vanguard home page
Alternatively, you can always go to the web archive and find this, for example:
http://web.archive.org/web/20080602210550rn_1/www.lean-service.com/home.asp
A personal highlight in the early part of 2008, when apparently “Lean” was not a problem for JS:
http://web.archive.org/web/20080214053011rn_1/www.lean-service.com/home.asp
My personal highlights from April 2008 were:
Vanguard Senseis (this was in bold)
Hear the Vanguard Senseis Speak about systems thinking, applying the method and their experiences in intervention
Watch the video clips
DVD – An Introduction to Lean (in bold)
“Are you ready to change the way you think?”
What is this thing called “Lean”?
What really happened in Toyota?
How is service different to manufacturing?
How can you apply the principles behind the Toyota Production System to improve service, dramatically reduce costs and improve morale?
Why should you watch out for the ‘tool heads’?
You could not make this up…………first lean (a DVD and JS had Senseis and was promoting them), then systems thinking and lean is for “tool fools”, it appears that for some time Mr Seddon was a “tool fool” and apparently fine with it, perhaps he simply found his true calling sometime after 08……………or perhaps he realised he was a little fish in a big pond, who knows?
All of these links display pages which talk about systems thinking.
I may break a lance with JS on tactless attacks but as anonymous you can’t expect to be trusted if the links don’t do what you say….
Mike-
The links Andrew posted work… they are titled “systems thinking” but have the content that Andrew stated…
Here is a general link to explore the old “lean-service.com” pages from different years:
http://web.archive.org/web/*/http://lean-service.com
I’m not that anonymous but the links do exactly what I stated they do. John Seddons previous site domain name was “LEAN-service”. Apparently he did not have problem with the term right up until the moment he did have a problem with it, but everyones entitled to change their mind.
The pages I posted offered “Lean” training and Vanguards “Sensei’s”. I’m not sure how much more clearly they could have articulated their own Lean offerings. So, again, my point stands, he either saw the light and has moved on from what he now views as the flat earth society to a more sophisticated model OR he simply realised that the market was being saturated with consultancies and that the easiest thing he could do, was to state from his “academic” ivory tower that lean was for fools and the way forwards was “systems thinking”.
Andrew;
actually yes you’re right. I was misled by the odd concatenation of the terms Systems Thinking and Lean.
It does as you point out, look rather like opportunism. I think Lean probably fits as a very relevant discipline in operational areas but mny understanding (not definitive by any means) of the wide ranging frameworks and discourses within Systems Thinking make the conflation of lean and ST at these references look like an attempt to add 6 inches of chrome exhaust to an existing vehicle and rename it.
Andrew, I think my favorite is the page where Seddon promotes:
http://web.archive.org/web/20040203093717/www.lean-service.com/home.asp
“Lean Fundamentals
What are the benefits of going lean?”
and
” LEAN TACTICS
Practical tools for action”
Lean this, lean that. Tools, tools, tools. In John Seddon’s own words, was he a “tool head” or a “fool with tools”????
Mark, I think the actual highlight in this section is this archived page:
Lean Fundamentals
A three-day, in-house programme where participants assess for themselves the value of lean concepts for their organisation.
This programme is only available from Vanguard, leaders in the translation of lean concepts for service organisations.
Download a brochure now…
AND in the Lean Tactics (I’ve pointed out a few of my favourites)
Improving processes means thinking, measuring and working end-to-end, starting and finishing with your customers. These tactics provide frameworks and tools for improving process performance.
Contents
Process improvement – an overview
**********Mapping a process************
Things to question about your processes
*********A better way to ‘fight fires’********* (that strikes me as rigorous systems thinking
**********Improving a fix**********
********Process improvement by comparing processes********
*******When to standardise work********* (I thought I recently read that standardisation limits the ability of service sector organisations to cope with the demand)
Barriers to expect
The dangers of process myopia
It is not about LEAN per se, it is about the “bad” METHOD.
Over 120 comment express quite some concern, that something is going wrong. Lean is not just lean, reading the books by JeffreyLiker, MatthewMay, ShigeoShingo, TaichiiOhno and others brings to light that SystemsThinking, SystemDynamics, TheoryU, Zen are the fields that are also connected and part of it.
Whoever is trying to sell just one version of it, mostly his/her very own blended one puts all others “outside the circle” and so diminishes the power of LEAN.
A pity, but seen everywhere where money is the only motivation to do LEAN in the first place. Remember well my first interview at a “lean consultant” in Hannover, Germany, whom I admired until this evening. There I got the message, “We do it our specific standardized way that has been proven!”
Time is changing, production is not any more as important as it used to be (in Germany only 20% of the workforce is active there), service fields are springing up (lean not yet an issue there, even though Agile and Scrum are promoted here and there – with not much impact, as they often don’t connect to the broader lean view).
Instead of lamenting against what “evil actions” JohnSeddon is doing, we should ask ourselves, “How can his action help us to bring forward what we are passionate about: LEAN THINKING?”
[…] here.In what follows are a few top-notch management improvement articles from the last month.The One Where John Seddon Might Be Lying (Mark Graban): Mark Graban critiques John Seddon, Systems Thinking, Systems Thinking in the Public […]
http://www.thesystemsthinkingreview.co.uk/index.php?pg=18&backto=1&utwkstoryid=257
… some more thoughts on what is really going in management and institutions.
What is going on BTW?
Why does it take about a week to get an event to the German version of http://unleashingideas.org (http://gruenderwoche.de)
My very personal view is that Europe, and Germany especially, will fail similar to the Romans about 2000 years or other great societies, within 10 years when changes are not nurtured and command & control are still in action despite the exponentially changing world. See link.
Best regards and my recent cents (not just he two that normally come in)
Ralf
My research has apparently caught Seddon in his lie, or at least in changing his story.
Seddon’s own newsletter from July 2004:
http://www.systemsthinking.co.uk/6-news-jul-04.asp#1
Seddon wrote:
“Ohno said you cannot improve without first standardising work. That is undoubtedly true in manufacturing; but is not true in service. In fact if you start with standardisation in service you can make things worse.”
But now Seddon is saying “Ohno never said that”? Busted.
Read further in the comment, it’s clear that Seddon is emotional about not being accepted by the lean community. Boo hoo.
“The sad thing is they talked about me, not to me. I hope once they are over the emotional reaction we can have a dialogue, I am sure there is a lot we can learn from each other.”
Mark, what is the point of all this ranting, nit-picking against Seddon? Is this insecurity on your part? Are you not willing to learn from others outside the TPS confines?
Yes, Seddon has probably shifted somewhat on standard work. So what! That is a great sign for me! But his basic thesis remains – the need to be able to ABSORB variety in service.
In the meantime there are some wonderful things happening that EVERYONE in the Lean movement could learn from. Please see:
http://www.managementexchange.com/blog/m-prize/announcing-m-prize-winners-audacity-imagination-experimentation
Why not try a dialog as Seddon suggests?
PS: I know both John Seddon and Dan Jones well – both have been professors at Lean Enterprise Research Centre, where I work. I respect both.
John B. – the original point of my post was not to criticize Seddon’s method, but rather his behavior. This has nothing to do with insecurity. If I was insecure, I’d keep my mouth shut.
I’ve had nothing but positive things to say about his work including his book “Freedom from Command and Control.” However, Seddon’s increasingly ad hominem attacks against Lean as a whole are harmful to the Lean, process improvement, and systems thinking communities.
As SeddonWatch has pointed out, it seems that it’s not Seddon’s *view* or opinion on standard work that’s changed or evolved, it’s his use of Ohno that has changed.
Seddon quotes a highly-respected man, Ohno, who is deceased and can’t speak up one way or another. Seddon used to say Ohno said this, now Seddon says Ohno never said that. It seems disingenuous and self-serving to use Ohno as a way of gaining credibility.
If Seddon merely said “I don’t think standardization is the first place to start” and if that view evolved, then I wouldn’t have an issue with that. But his constant reliance on “Ohno told me this” and the fact that it’s changing is troubling. If Seddon merely disagreed with Womack and Jones, he could make his case in a calm, reasoned way as an academic might. Instead, he resorts to name calling and ad hominem attacks. That’s worth calling out and highlighting.
Seddon doesn’t seem like a “dialog” kind of guy, frankly. He’s right, the world is wrong – that seems to be his view.
You might call it nitpicking, but that’s your right. I’ve had a disturbingly high number of people contact me offline who say I’m on the right track about his attitude and approach. It’s my right to criticize it.
Seddon seems a pretty intelligent guy, so the right question is to start with why he using these “communication tactics”? (And then continue asking why…)
What is his goal doing that, that way?
Demoralize people?
If he is smart, there should be more than ego, should be more than economic interest, what if maybe he is working around a bug in human brain? (He maybe know something about psychology that we don’t)
We all want to conform, we all want to belong to a group, we all want to be seen as smart, not as dumb, we all want to right, and we don’t want risk, and all would buy a magic pilule to solve our most pressing problem if someone sold it.
If current Lean interpretation by the people who is in charge of the structural decisions on service organizations is detrimental to the bottom line, and if Lean is the defacto standard for improvement, doing more of “Lean” will make service organizations worse unless someone creates a counter measure for that effect.
The only problem with this strategy is that existing members of old group will react, that’s colateral damage, and caused by their personalities are bounded to the tool, method, practice, brand that joined them, which is a bad thing as this things are volatile, and we should be free to change tools easily than what defines my being.
Do you define yourself as a “Lean Consultant”?
Then his strategy may hurt your fellings.
Do you define yourself as someone that wants to improve how service organizations are managed and at the same time improve people’s lives?
Then his strategy can be something you learn from.
I used to have the same behavior in a “war” I established with brazilian IT processes, projects and quality status quo. This was RUP (IBM), PMI and CMMI guys, most of the academic world and the goverment program Softex for software excelence.
I was pushing an Agile approach to improve software development industry, every body told me I was crazy and that it never would work on their organization. You can’t imagine how hard is to fight with status quo, how easy your voice is not heard, how easy your message get’s thrown out of the window, how dogmatism reign sovereign.
I tried some strategies, but the one that worked was to talk to the 4 year old mind, to demonize, to polarize, and of course they had good ideas, but for a moment I needed to make joke of their methods, to introduce something that could not be tough by the current paradigm, to take the system from that state, I had to destabilize it, I had to polarize it, I had to move people’s emotions, I had to have an enemy, I was pushing for something that was substitute of something else, and the system (industry) reacted.
Just to understand, one yahoo group on CMM (quality model for software) with 2600 people in Brasil was closed by their founders because most conversations I joined became polarized as this one became, I was called names by some old model proponents, a lot of them later I trained on the new stuff, no bad fellings as I know that their reaction was the only thing they could do at the moment.
Lean, not what Toyota does, is becoming status quo, the defacto way, and managers are going to ask for Lean, not for improvements, are going to judge tool “implementations” and not improvements, reports will be about # of people trained in Lean tool X. More “Lean” will not be more improvement, but more tools “implanted”, there are a lot of implementations like that, and that’s basically what will grow, as less people understand what could not be read or written about Lean.
Maybe a little fragmentation is good to the market. A single trademark “Lean” can easily comoditize the market and bad consultants can became invisible to the customer, and all the good consultants suffer from this.
Another more interesting way of defining who we are would be for what is our purpose and not what are our tools, this way all would be talking at what we did to improve something in some context and what were the results of this experiment.
Hope that this trows a little more light into this thread, or feel free to call me names, I’m fine with that.
Juan.
Here’s an interesting post by Tom Johnson at The Lean Edge: http://theleanedge.org/?p=462. Seems to correspond with what Vanguard is about.
Sorry to dredge this back up, but I have new facts.
Seddon says “Ohno never said that” (the quote of without standards there can be no improvement).
I was re-reading a classic book “Gemba Kaizen” by Masaaki Imai. Imai studied directly with Taiichi Ohno.
Imai wrote:
https://kindle.amazon.com/post/GBA0QH2MAOFP
I hope that settles it. It’s NOT a quote that Womack and Jones made up or invented. Seems like the quote is simply often misattributed to Ohno, when it was really Imai.
Hi
can anyone please help me with some books names which talks about, implementing lean in call centres.
am doing my dissertation on implementing lean in call centres. and iam very much confused if lean can be implemented in call centres, since it talks more only about the manufacturing industries. I was not able to find any books talking about lean in call centres. But only one which supports call centres i found was, “systems thinking” after reading this now iam again confused if Systems Thinking is lean or not.
I love this!
Thanks for showing that you folk are all human to! I respect each of you for your academic work and I am glad to now that you through paper balls at each other in the class room just like any others. I will make sure to show this to fellow students, that think of you as Gods.
Even the good Uncle Ohno had his mistakes, I am sure. So does JS and the rest of you. Thank the Lord for that.
[…] something of a war going on between John Seddon and the Lean community (see comments on this post in Mark Graban’s Lean blog), but I credit Seddon with defining the concept of failure […]
You haven’t closed the forum so I will make one comment:
Seddon sounds like he is directing his invective at a UK audience of bureaucrats and consultants, but others, including Mark, getting caught in the crossfire.
We had this in Australia once. A UK dermatologist spoke at a UK conference on how sun cream was a con and perpetuated by manufacturers of the stuff.
He was quoted in Australia and this was treated as outrage. When he was interviewed, he said that he was only talking to a UK audience about the couple of days of sunlight they get each year, and the industry’s desire to have people put cream on each day, regardless of weather.
Australia has the highest rates of skin cancer in the world, and he acknowledged his advice was foolish in our context. He hadn’t thought his remarks would be picked up here.
Seddon is unlikely to sell to US buyers -there is no market for the cynical, hard-bitten civil servant talk that sells well in the UK. I suspect he doesn’t care for that reason – what is hurting his reputation in the US has no effect in the UK, and may even boost it.
roughly 140 comments on a question about standardization. There comes in standardization every time a lean initiative is started. Standards are set. Workers seduced to take these (best thought) standards set be experts often (internal and external). Only to run into major major difficulties not so far in the future.
Despite the fact that John has a very peculiar way of bringing the message over, the objective fact is rather that the worker has be become the expert of his process and learn how his action connect with actions after his/her workstation.
The intention to create an environment where genuine learning amongst individuals and teams can take place will be the only way to cope with the accelerating changes we see and feel in the world around us. That not everybody hits the “suitable” tone is not a sign that he or she doesn’t want to improve the system. We all have to be sensitive (can’t put myself out of this) to inquire into what drives the other one’s behavior – that is what Ohno and Shingo would have called true “lean thinking” (even though the expression did not exist in their time).
So long, a lean thinker for over three decades (most of it just doing it, not calling it lean, six sigma, or anything, I just removed the obstacles in the process ;-))
@RalfLippold
I have been following this thread for a while, and I am wondering: why do so many people get annoyed over the ‘style’ of John Seddon? I mean I have seen quite some video’s and read quite some papers by him, and while I do get his ideas (they sound quite sensible and matter of fact, and I find them really interesting) I don’t understand the antagonism he raises. I am from The Netherlands, we have a reputation for being blunt, perhaps that’s why I don’t get where all the sensitivity comes from? John Seddon’s ideas seem quite straightforward and worth an experiment or two. Nothing lost, right, by experimenting, doing a ‘check’ on value and failure demand? I mean it is not even expensive. Anyway, I just ask you this question because you seem to appreciate what Seddon is about and also say that “John has a very peculiar way of bringing the message over”. What do you think is so peculiar? I hope you will answer me because I really am in the dark here… Hope you can help and explain this to me!
All the best,
Muriel
Muriel – I can only speak for myself, but when Seddon engages in name calling and personal attacks against other Lean authors (like Womack and Jones), then that is what I take issue with. At least to this American, that is rude and unprofessional.
Muriel, Thanks for your thoughts. As a European and global citizen (done home exchange for several years) I also see John as another inspiring promoter of lean and systems thinking (the underlying understanding of processes).
I can understand Mark on his thoughts as well, as John talked “bad” about the LEI (Lean Enterprise Institute) which its founder he is. Nevertheless lean thinking in the purest sense (as would John, Jim, Dan, and the other “gurus” like Taichii, and Shigeo would see it) is about questioning and inquiring the status-quo and ask “Why?” to find out the underlying root cause for behavior.
Perhaps it is John’s talking different from what one would expect from an engineer with the English accent. Anyway I am always interested to see different views on lean and I am not yet convinced that we as a lean community have reached a major point on the improvement ladder.
Just lately from a well-known lean institute I got the feedback by one of its consultants, that social media doesn’t play any role in the field of lean.
I wonder whether the narrow focus on tangible work and supporting tools is still mainstream.
Just my own very personal view on the issue.
Cheers from Dresden, a truly lean-free zone (even though all employees in the local companies with experience from GDR times are true lean thinkers and doers (pretty much similar to where Toyota once came from, being crap and looking for better ways, without buying in expensive consulting or investments)
Ralf
Muriel-
The US has become more politically correct or PC as it is known. Looking good over truth and substance has been winning the day. Even this post has changed names from calling Seddon a liar to unfair criticism.
We have a nation of “gurus” that have never “done” anything. Some are former speech writers or academics that became more reporters than gurus. The truth has been defined by popularity not knowledge.
The word of caution is that anyone reading anything look for what actually works through experimentation with method . . . not copying, shortcuts or belts. Principles over rules, inspection, technology and scripts.
Dissonance offers a way for seekers to question and move forward. The Vanguard Method brings to the table something different, but will require Americans to challenge their current thinking. Something, that we have become very uncomfortable with as the world’s largest economy. Status quo is ruining us.
In the name of actual truth, the title of this post used to say Seddon “might be lying” because I can’t be inside his brain to know his intent when speaking his untruth about Womack and Jones making things up. I did not call Seddon a liar. I just stated it was a possibility he was lying. Now that it has been documented that Womack and Jones didn’t “make it up,” will Seddon be correcting the record from his side?
As I said higher up – there is an Atlantic Ocean between the British way of public discourse and the American one. Divided by a common language, as they say.
Seddon is preaching to a local audience; fully aware of the infamous failures of institutions like the NHS, the Yes Minister culture and so on.
The US does not carry this baggage and it is hard to see why Seddon is preaching so negatively to what is essentially his own target market, the UK.
Mark-
To be perfectly honest I could care less what Womack or Jones think. I do care that our country is stuck in a quagmire of political ideology over knowledge and gurus in empty suits (or brains). Discern for yourself who those might be.
Richard-
The US and UK face the same plight (i.e., they both carry the baggage of a dysfunctional government). Billions go in and little comes out, lots of waste. Telling folks they are doing the right thing (being positive) does not promote improvement. A cold smack shower of water is sometimes useful.
I am not interested in personalities I am interested in methods that work. The vanguard method is ruthless in exposing waste in systems and also combines intervention theory with a change model that leads to change based on knowledge and also addresses management thinking (the biggest lever for change). I am a fan of Seddon because he has introduced me to a method that works. I am more than happy to listen to other change practitioners but you must show me results.
I am interested in personalities because if Seddon claims to be sensitive to understanding where people are at, interesting them and stimulating their desire for improvement – then being rude to them is hardly the best way to go about it.
I’ve met the man, I think he’s very intelligent and I use some of his terminology and thinking in my work (I hope he doesn’t sue me for this).
But it’s a struggle for me to understand in a job where Lean means really respecting people, their history and insight with processes, to work out why this guy is demeaning all sorts of potential allies, unless it is to push his proprietary model of process improvement.
And from one Lean ‘cultist’ to you Vanguard fanboys – you do look like a cult.
And Muriel, if I can be blunt, Dutch people aren’t the people I would go to for diplomacy training, and see, being Dutch you will be able to take this, apparently.
If you can’t, then it suggests to me your statement about not understanding what Seddon is doing wrong doesn’t ring true.
John Seddon makes an important point using a style of delivery that creates a strong reaction in the recipient. This approach works, as evidenced by blogs such as this.
In the UK public sector, there is a prevailing culture of management speak and wooly communication. Passionate, blunt and charismatic delivery are not a common quality amongst public sector leaders. It is for this reason that John Seddon gets noticed in the UK public sector. Many employees of public service organisations appreciate the fact that he calls out leaders for actions which most know are destroying service.
As a manager in local government, I have seen lean applied and have also personally applied method recommended by John Seddon. My experience is that the lean projects failed to deliver any sustainable change in culture or thinking. Seddon’s techniques produce change in a more emergent manner and appear to create a longer term culture change. It is the learning element of his method that makes this difference. I can only go on experience here.
I suspect Seddon can be too abrasive for some but hey, so was Steve Jobs!
As someone who actually works within an organisation as an employee, I would be more interested to hear evidence based debates about the merit of different approaches rather than a personality clash between their proponents.
Thanks for your thoughts, John.
My post was never about whether his methods work or not… it was a commentary about his habit of rubbishing competing Lean gurus. He’s been doing much less of that recently, so I presume he’s focusing on his work and his clients and that’s good for all, I suppose.
From a hospital in Japan:
“Kaizen cannot be promoted without standard.”
https://twitter.com/MarkGraban/status/303227526287859713/photo/1
Sorry to rehash this… John Seddon said “Ohno never said that” about the quote “Without standards, there can be no kaizen.”
The editors of the book “Taiichi Ohno’s Workplace Management” directly attribute this quote to Ohno.
I’ve added a photo of the page from the book in the blog post if anybody would like to revisit this. I think this really proves that Seddon owes Womack and Jones an apology.
OK, good luck with that apology.
I believe we are still missing the point – three years on.
Here is the list of things to move forward and discuss:
(1) Differences between manufacturing and service.
(2) Blind use of tools intended to solve a different problem than the one it was designed for.
Mark: If we can agree that Deming laid the foundation for Ohno and TPS (which we have in the past), then these issues:
(3) Dr. Perry Gluckman wrote a book in 1989 (Everyday Heroes) that references some of the things that are now called “Lean.” His thinking came from Deming (student at NYU under Deming).
(4) Deming’s Profound Changes (Delavigne and Robertson) can give us a clue on the American Perspective of why management manages the way it does. Taylorism and Neo-Taylorism still influence our perspective. There needs to be a discussion and knowledge from “Deming” Lean to Taylor “Lean.” LAME as you call it needs to be discussed in greater specificity around these transformation and thinking components. This shift in thinking is a move from Newtonian Determinism/Scientific Management to the discoveries of last century by relativity theory (Einstein), uncertainty principle (Heisenberg), chaotic processes (Poincare), theory of knowledge (CI Lewis), and statistics (Shewhart) that discount this determinism.
(5) Discussion on the social sciences and psychology. Bennis, Benne and Chin, Argyris, Lewin, Quinn and I am speaking to some new thinkers that have written papers on intervention theory for individuals, groups, organizations and society.
(6) I still don’t believe that Seddon copied Joiner, by starting with check. Regardless, I believe that Vanguard’s Check or understanding your organization as a system is something separate from the PDCA. The difference is rooted in the theories of the 20th century thinkers. The unknown, but knowable (check) vs. the unknown and unknowable (Shewhart’s PDCA and/or Shewhart’s PDSA).
This is not an exhaustive list, but is a decent start.
As for Seddon, we must credit him for advancing the thinking or at least giving us a new perspective whether we like him or not.
Our challenge needs to be to advance the thinking. My belief is that a barrier is the tools element in this (the lean) community.
Three years down the road, can we move forward now?
I know the apology won’t happen.
I think it would be good for Seddon to “move forward.” I have noticed he is spending less time on ad hominem attacks against Lean and people like Womack and Jones. He still has a tendency to launch vicious personal attacks against individuals, as I witnessed earlier this year.
So, I won’t give him too much credit for anything.
I appreciate, also, that you’re launching fewer blanket attacks against Lean, Tripp. It’s not a “wicked disease,” as Seddon said. We can have a mature discussion about your points, and others, through our various blogs and publications over time. Our views are actually more similar than different.
Also, see page 102 of “Freedom from Command and Control” and you’ll see Seddon is quite clearly saying to start the Plan-Do-Check-Act cycle with “Check.” That context and reference is pretty clear and the history also shows Joiner wrote about this first. A citation would have been cool.
Yes, I know. Only Seddon can speak for what he read or didn’t.
I do think it is important to know that Seddon uses check as more of a unlearn/learn loop or re-educative piece. Joiner seems to come from a more pragmatic/systems view. The overlap might be the systems piece. I don’t see any traces of intervention theory in Fifth Generation Management.
Again, I see Vanguard’s check as something that precedes the PDCA cycle. PDCA for the unknown and unknowable. Just my view.
Correction: I should have said Lloyd S. Nelson for unknown and unknowable. Deming credits him.
agree with the part about standardisation – i see this as simplification, in IT its logical to cookie cutter some offerings to different sets of clients as the pull model will break you in trying to achieve it given the rate of change. I understand both sides of the argument, i don’t see one size fits all as the customer is always right….
Wow. A few personal parts being measured here.
I suggest a few need to put the books down and instead invest their time in learning by doing. Make the mistakes and enjoy them if you do want to emulate Ohno.
I’ll tell you what, you can have this one and thank me later. Achieve this and you’ll do ok.
Learn like you don’t have to,
Try without fear of failure,
and Improve when no one is looking…
Job done.
Good point Lee.
Here in little old New Zealand some organisations have been applying the ‘Check’ first method.
It’s been enlightening. I’ve seen teams find that often we’re applying a ‘one size fits all’ approach. People realise that what we want is:
– consistency when needed
– variation when needed.
The variation speaks to both customers and people in the work. Understand how your people want to learn, and meet it. Equally, understand what customers want and meet it.
Teams that I’ve worked with have done crazy things like:
– remove every target they could find – and replaced with XMR charts. Customers now get what they want sooner. And, rework rates have dropped. It took time, but eventually people in the work realised they unconsciously ‘gamed’ the targets. Anxious to process requests (Target = 95 per cent within ten days) people would find an error, stop the clock, and pass the work back to the customer, thereby causing rework. Managers were oblivious to this.
– varying response to customers – the teams now treat customers differently. We try to meet what customers want. Also, we look for the customers who most often get things wrong. We work with them to redesign things like forms. This has reduced rework for all.
I’m not associated with Vanguard, but I have read Seddon’s book. Also, I am woefully ignorant of Lean methods. (I’ve just not had the opportunity to see this method (or its variants) in action).
I do appreciate what I read from OP’s point – bashing people is rude.
It’s also very off putting.
However, I can also appreciate how frustrating it is to influence other people. Case in point for us was trying to change how people think about targets. Leaders just would not let us remove them. We only made head way – from the results of a pilot study. Finally the manager said ‘I’m surprised that worked!’. And, voilla, target gone and improvement realised!
Thanks for your comment. I also appreciated Seddon’s book, as I’ve said here before.
Before I got introduced to Lean, my education was in Deming methods.
It frustrates me currently that many “lean daily management” practices in healthcare, while there are some good things about it, are recreating the mistakes made by others in the past with:
1) arbitrary targets
2) reaction to simplistic “red = bad” and “green = good” thinking
I also suggest X and MR charts and do my best to teach about this in different ways.
But people think targets are fine.
They don’t understand the dysfunction that’s created. Or how it’s a waste of time to come up with an explanation for every point of common cause variation.
We can do better.
Toyota was influenced heavily by Deming.
It’s time for the modern “Lean Healthcare” community to be similarly influenced.
Mark,
Fascinating discussion. I am a student and am sincerely looking for clarification.
I am one of those Seddon readers that came across FCC.
It absolutely transformed my thinking.
Funny I always thought of Seddons work as systems-thinking for Lean service?
I find Seddons premise that transferring lean manufacturing to service with caution wholly convincing.
I also accept having read your comments on the idea of shades of standardisation.
My thinking is grounded in Seddons exposition of the Tagucci loss function and the gap from the nominal demand.
But I’d like to take it a step further.
In manufacturing a product once manufactured cannot be easily changed and therefore represents almost a static / historic demand profile or representation of ‘VD’. And it can no longer flex to changing demand profiles.
As such it almost shifts from what the manufacturer thinks its customer wanted to a product lead approach as it shelfs life increases and demand profiles shift.
The Tagucci loss function applied to service is therefore all the more fascinating. there are multiple nominal demands in play and multiple VDs and they are shifting. Then I agree with Seddons case that it is all about designing in the variety of demand into the service.
However, let’s take an example of McDonalds. This is a classic case where the consumer is almost wanting a standardised service experience or is it? Here a standardised service experience maybe valid and VSM applicable?
I welcome your feedback and comments because I am looking for a ‘truth’.
Hi Moses –
On McDonald’s… does the consumer want a “standard” service experience (including the food) or has that been thrust upon them by McDonald’s? I’m not really a McDonald’s customer anymore, but it seems like McDonald’s is trying to add more variety and options in their food. Can they handle that operationally? That always seems to be the question (how are we doing the work?).
“Here a standardised service experience maybe valid and VSM applicable?”
Not sure what you mean by “VSM applicable?”
Mark
Thanks. Interesting.
I am half torn between a customer almost wanting the reassurance with a case like McDonalds that it has a standardised service irresepective of world-wide location and the introduction of lets say local variety.
So agreed there is a shift in its product offerings.
Litmus test: However ask one of their checkout staff for something as simple as a cup of water and see what they say?
The reponse I got was hilarious. ‘Gee that sounds healthy! erm…… conference………..Ha!
What are your thoughts on the Tagucci loss function?
With VSM I am trying to understand whether it should be applied to a service where demand varies?
We don’t want a standard service response like, ‘I’m sorry but we can’t do that because…..?’
This is Seddons contention. i amlooking for more insight here as I am not sure?
Value stream mapping as I undestand it, is looking for a standardised approach. Isn’t this contrary to a flexible service design?
welcome your thoughts.
McDonald’s has country-specific foods to appeal to their local markets… but I also heard a story the other day about a business traveler in Thailand who was allergic to shellfish. He wasn’t eating much, but was SO happy to see the Golden Arches in a smaller city and a Big Mac there tasted like a Big Mac anywhere. He really appreciated that standardization.
The Taguchi Loss Function is brilliant. There’s no arguing with that, I think.
I think there’s a misunderstanding about VSM (maybe spread by Seddon, I don’t know). All a VSM does is have people document and better understand the current state of the system — in particular, information flows and material flows… and customer demand and other data. A “future state” VSM is drawn to help envision a better future and move toward it.
There’s nothing in the VSM process that implies things must be TOO standardized or that you wouldn’t account for demand variation. We take that into account in healthcare value stream maps all the time.
I was reminded of this old discussion… I’m in Japan and literally just heard a recently-retired Toyota executive (who was in charge of the Toyota TQM program) say: