Once again, the WSJ has written about Lean at Starbucks (see my last post “Controversy over New Standardized Work at Some Starbucks Stores“) in Wednesday's paper.
The newest article is called “At Starbucks, Baristas Told No More Than Two Drinks“, which you should be able to read for free even if you're not a subscriber.
Yesterday's article leaves me to wonder, once again, if Starbucks is getting wrong or if WSJ writer Julie Jargon is writing about a partial picture based on her interpretation of internal company documents.
Taken on the surface, you have to ask if we're reading about Lean or a top-down, inflexible approach that's really more like Taylorist industrial engineering or what I would call “L.A.M.E.” For a more creative approach to this subject, click here.
Again, I'm writing based on what I am reading in the WSJ, not on any first-hand experience with Starbucks as anything but a frequent customer.
From the article:
“Amid customer complaints that the Seattle-based coffee chain has reduced the fine art of coffee making to a mechanized process with all the romance of an assembly line,”
Are these really the customer complaints? I'm personally not looking for rudeness from my barista, but I also don't want what they called a “single serving friend” in the movie “Fight Club.” I'm a “get my coffee quickly with a smile and go” type of customer, myself.
Me thinks the writer might be overromanticizing beverage making and taking an unnecessary slap at assembly lines. Not all assembly lines are necessarily a Charlie Chaplain movie come to life. A factory where workers are fully participating in the continuous improvement of their own work might be a more enlightened workplace than a Coffee Gallery where baristas are told precisely what to do.
Late in the article, the writer mentions Lean:
“Over the last few years, Starbucks has been applying to the coffee counter the kind of “lean” manufacturing techniques car makers have long used as a way to streamline production, eliminate wasteful activity and speed up service. The company has deployed a “lean team” to study every move its baristas make in order to shave seconds off each order.”
“That team discovered that many stores kept beans below the counter, leading baristas to waste time bending over to scoop beans, so those stores ended up storing the beans in bins on the top of the counter.”
What is a “lean team”? Is that a group of experts from Seattle who are standing over workers like a “time study man” like Frederick Taylor standing over Schmidt, the pig-iron shoveler?
To me, a “lean team” has always been hospital staff members (like nurses or laboratory technologists who are taught how to analyze and improve their own work). The idea of a specialized “lean team” sounds very traditional and top down (the WSJ paragraph reads just as well if you search for “lean” and replace it with “industrial engineering.” If it were top-down, Seattle-driven, you might make the case that it's more McDonalds-ism than it is Lean.
The article continues:
“Starbucks baristas are being told to stop making multiple drinks at the same time and focus instead on no more than two drinks at a time “starting a second one while finishing the first, according to company documents reviewed recently by The Wall Street Journal.”
On the surface, this seems overly directive and inflexible. Yes, there is an industrial engineering effort that can be done to balance simultaneous work operations, much like a complex and flexible manufacturing “cell.”
Are employees being taught why this new method is better? Are they given a chance to give input and feedback? Better yet, is Starbucks teaching the store managers and baristas Lean methods that they can use to improve their OWN stores together?
Again from the article:
“Baristas are also supposed to steam milk for each drink rather than steaming an entire pitcher to be used for several beverages.”
The language of “being told to” and “are also supposed to” again sounds very top-down and directive. I understand the argument that if you steam a whole pitcher full of milk, it's going to get colder than is ideal for beverages after the first. It sounds Lean to reduce batch sizes and to do “single piece flow” drinks.
But sometimes, a batch size > 1 is appropriate for the customer demand and the flow of the operation. If you are making breakfast for your family, would you make toast one piece at a time when you have a four-slice toaster, because that's “lean”? No, you'd make one batch of toast if you had people ready to eat four slices.
If it's a slow time of day, maybe it's appropriate to do “single milk steam” flow, but during a really busy time if you are making two drinks at essentially the same time, maybe it's appropriate to steam two drinks worth of milk at once.
But who am I to say? I'm just some blogger.
I'd want the baristas and managers to think about these challenges and figure out what works.
Should the company have some standards? Of course — Toyota workers don't get to decide how many tires go on a car (so much for the “fine art” of manufacturing things). Some standards should be set consistently (such as the number of espresso shots in a regular grande latte), but I think the Lean approach would give baristas flexibility to participate in developing their own standardized work and to possibly have different standardized work for different times of the day (based on store volume).
There's so much variation in Starbucks stores and their physical layout; how can you be so sure that a single method is best for all stores, anyway? I'm sure Starbucks must understand the need for flexibility.
Again from the article:
“The new methods have “doubled the amount of time it takes to make drinks in some cases,” according to Erik Forman, a Starbucks barista in Bloomington, Minn., who says his store began making drinks under the new guidelines last week. Longer lines have resulted, says Mr. Forman, who is a member of the IWW Starbucks Workers Union.”
A WSJ reader commented about the irony of a union member (from the “Wobblies“) complaining about management's efforts to slow them down. That certainly is the polar opposite of the usual “speed up” complaints that unions have typically made.
The article continues:
“Tyler Swain, a barista in Omaha, Neb., who is also a member of the union, worries how he will keep up with volume if he can only complete one drink at a time. “While I'm blending a frappuccino, it doesn't make sense to stand there and wait for the blender to finish running, because I could be making an iced tea at the same time,” he says. His store has yet to adopt the changes.”
Tyler sounds completely rational about this — you shouldn't stand there and watch a piece of automation (a frappuccino blender) — that's a solid Lean principle (“man/machine separation” – sorry for the gender-specific phrase).
But the WSJ interviewed someone who hasn't been part of this new process yet!!!! What I read about earlier in the article was the process for running the espresso machine/bar, not the frappucinos.
I can't believe that Starbucks standardized work would say something like “stand and watch the blender run” regardless of whether this was top-down Taylorism or an employee-driven Lean process.
I would love to see Starbucks employees involved in what Norman Bodek calls “The Idea Generator: Quick and Easy Kaizen” or what FastCap and VIBCO have their front-line employees doing — improving their own work to make things easier for themselves and better for their customers. Engineering and redesigning a system (such as the overall store layout and the technology of the espresso machines) is important, but employee/partner/barista engagement would be powerful and rewarding to all involved (and it passes the “is it good for the company?” test of Office Space's Initech).
The only Starbucks comment is from a spokesperson who may or may not know anything about Lean. They didn't quote or cite the Starbucks lean leaders mentioned in other articles.
Starbucks said:
“As with any new behavior, it will take time for baristas to become comfortable with the new method,” said Starbucks spokeswoman Trina Smith.
You're not helping the case, Starbucks spokeswoman, that this isn't top-down Taylorism. Schmidt eventually became comfortable with Taylor's new pig-iron shoveling methods, too, I'm sure.
I really wish these articles were about how the BARISTAS are improving their own work. I wish I knew if Starbucks was getting it wrong or if the WSJ reporter was making assumptions and writing inaccurate stories…
Also, see the Business Insider summary of the story with some local NYC reporting that implies Starbucks workers are being watched with cameras to make sure they follow their standard process (who knows if that is true?).
Also, check out my slightly-more-creative post titled “The Article I *Wish* I Had Read about Starbucks in Yesterday's WSJ.”
Please scroll down (or click) to post a comment. Connect with me on LinkedIn.
Let’s work together to build a culture of continuous improvement and psychological safety. If you're a leader looking to create lasting change—not just projects—I help organizations:
- Engage people at all levels in sustainable improvement
- Shift from fear of mistakes to learning from them
- Apply Lean thinking in practical, people-centered ways
Interested in coaching or a keynote talk? Let’s start a conversation.
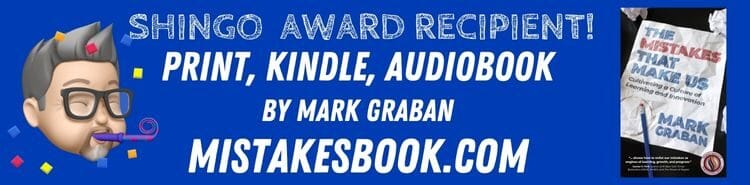
[…] For a more traditional approach to this topic, check out this alternative post, “Real Lean at Starbucks or Tayloristic Industrial Engineering?“. […]
When anybody can shovel 90 lb pigs, I want to be the first to shake that man’s hand.
Carefully, albeit.
Mark, you still can not bring yourself to admit that Lean is little more than Taylorism warmed over, can you?
synfluent – don’t think mark will reply as lean and taylorism are quite different. can you show me exactly where the respect for people tenet intersects w/ Taylorism?
nope didn;t think so…
Fake top-down lean is nothing more than warmed over Taylorism, that’s the problem.
I am amazed at the comment above. Taylorism warmed over??? Seriously???
Me i’m too bleary eyed at my morning espresso to even notice the person serving let alone camera’s watching them. Whats intresting about this is from the PR perspective and the ‘negative’ press created. Who’s heading Starbucks ‘comms team on this one?
When it gets to the stage that you have to write a fictional lean success story the game is up. This is the reality of Lean no matter the protests that this isn’t Real Lean.
Joe – so why are you hanging out on a blog about a method you despise so much, Mr. Anonymous UK Commenter? Not keeping busy enough with your variety of so-called “systems thinking?”
There are plenty of real lean success stories including a growing number of hospitals. I just wish Starbucks was that type of success story.
Interesting you turn legitimate criticism into an attack on other people. I am a manager for Starbucks UK and we are dreading lean control being applied to our us. I know of lean because I was a team leader in an office where they applied lean and it was a disaster. Workers threatened to go on strike when they started mapping what movements we made to do our job.
Joe, if you are indeed a Starbucks manager who is new to this forum or this discussion, you used language in your first comment that sounded (coincidentally?) EXACTLY like those in the UK whose primary interest is attacking Lean with a broad brush, instead of recognizing that there are organizations that apply Lean thinking and principles the right way and those that just apply tools in a dysfunctional way. Lean isn’t inherently bad.
Unfortunately if the only experience with Lean thinking is what Starbucks does, he’s going to have a negative perspective on it. Until I did some research, I thought it was crap, too.
James – thanks for being open-minded and for taking the time to learn more about Lean… as I’ve written about here, Lean is sometimes done in a “crap” way but that doesn’t mean Lean itself is a crap idea.
No problem. To be uninformed is to be a shitty organizer. To be honest, the Lean you talk about on here shares a lot philosophically with what the IWW aligns with philosophically, stuff like worker self-management and autonomy, with a focus on collaborative, bottom-up structures. Which is, by the way, the exact inverse of what Starbucks is doing of late.
I do have one question, though: what’s reference behind Taylorism? It sounds familiar but I can’t quite place it…
James – Frederick Winslow Taylor is one of the fathers of Industrial Engineering:
He was a contemporary of James Connolly, the labor leader.
He’s the one who really cemented the idea of separating thinking (managers and engineers) and working. That’s the predominant management model today still, unfortunately.
Toyota and Dr. W. Edwards Deming helped turn that on its ear. In a lean environment, leaders say “the people who do the work are the ones who improve the work” (and they mean it).
The idea of an expert standing over you with a stopwatch and clipboard telling you what to do better – that’s Taylorism. Lean should really respect the input of those doing the work – such as the baristas.
And the lean I talk about here… this isn’t the only place nor am I the only one who talks about lean that way (Check out http://www.bobemiliani.com for some other good research and content from somebody else who really emphasizes the Toyota “respect for people” principle in his writing.
Interesting comments from Starbucks employees, many pro and many con, over on the Starbucks Gossip blog.
Many baristas say the new system works better, once you get used to it. Many say that the system should allow room for judgment and flexibility (I’d agree with that). Many criticize Julie Jargon for a poorly researched, crappy article.
As someone who is both a member of the Starbucks Workers Union and has had to deal with the new repeatable routine, the description of it is pretty spot on in the article. Julie left a couple of things ambiguous, but the implementation is a top-down thing, without a doubt. It owes way more to McDonalds than Kaizen or Six Sigma, and leaves no real room for adaptation to various store layouts or personal abilities. As far as people saying the new method made them faster, I would point out that the company spokesperson ‘didn’t have that level of detail’ is pretty damning as to it actually speeding things up universally.
Have to say this is the first time I’ve seen your blog, but I’m adding it to my bookmarks because it’s good stuff.
Oh, by the way, Erik talking about getting customers out the door faster is somewhat ironic to be sure, but we union baristas like our regulars just as much as nonunion baristas, and unlike the people running the show in Seattle, we know what our customers actually want, particularly in the morning. Anything that gets in the way of that ultimately causes us problems through either diminished tips or customer complaints, neither of which is good for us.
Here is a great blog post from Patrick Anderson about how lean in his healthcare organization does NOT mean “one size fits all” at each site:
http://leaninalaska.wordpress.com/2010/10/15/customizing-vs-one-size-fits-all/
“We prefer Customizing our solutions, using our employees, who focused on our customers.”
I wish the Starbucks story was portraying that.
Patrick is very much a student of Dr. Deming and not a top-down command-and-control guy.
It’s worth reposting, John Shook’s LEI column from last year about Lean at Starbucks:
http://www.lean.org/shook/ColumnArchive.cfm?y=2009#Col1085
In part:
Whether it’s top down or Lean, all that matters to me is that I get my frappuccino quickly and double blended. : )
Here is some advance customer communication going out at UNC:
http://news.unchealthcare.org/som-vital-signs/2010/oct28/starbucksservice
Interesting – Tim Horton’s (in Canada) is also using lean in a very similar business…
http://www.wowjobs.ca/job/Senior+Lean+Process+Leader-tim+hortons-oakville+on-9185113
Comments from CEO Howard Shultz on lean in today’s WSJ:
WSJ: Some of the changes at Starbucks have been intended to make things more efficient behind the counter, but there’s been some criticism that streamlining the coffee-making process could actually take some of the romance out of the experience and slow down service. What kind of feedback have you gotten from customers?
Mr. Schultz: Through lean practices we’ve been able to comprehensively bring about a significant change in the effectiveness of making an espresso drink and serving our customers. The interesting thing about today versus three years ago is that the qualitative scores of the Starbucks brand, speed of service, cleanliness of store, trust in the brand and overall satisfaction are at record levels going back a decade.
http://online.wsj.com/article/SB10001424052748704076804576180313111969984.html?mod=ITP_marketplace_3