The Winnipeg Free Press has an article about their local St. Boniface Hospital, a member of the LEI/ThedaCare network I'm involved with called the Healthcare Value Network. About 40 of us from different Network member organizations visited last Thursday and Friday for what we call a “gemba meeting” — going and seeing, first hand, what a network member is doing well with Lean and what their lessons are.
Dr. John Toussaint blogged about the visit and I'll comment here on the news article (“Turning St. B into a lean machine: Standard Aero serves as example to help hospital improve care“).
From the article:
St. Boniface Hospital president, Dr. Michel Tetreault [pictured below], said bottlenecks have long occurred in the health care system because hospitals “give great people broken processes and expect them to do good work.”
That's such a common theme, including in the Dennis Quaid “Chasing Zero” documentary – the problem in healthcare is “bad systems” not ‘bad people.”
We saw many examples of front-line staff being engaged in (and enjoying!) process and quality improvement. They showed us a new Lean-inspired practice that was also shown in the Quaid program:
For example, a pair of nurses who gave a demonstration of the new bedside shift report, whereby a departing nurse updates her replacement at the patient's bedside, rather than dictating into a tape recorder in a back room, said this and other lean initiatives help reduce errors, such as when patients receive their medication or how much.
This seemingly simple practice flies in the face of “how we've always done it.” Doing report (shift handover) at the bedside involves the patient and improves nurse communication in a way that leads to better quality and fewer errors. I've seen nurses at other hospitals talk into a tape recorder – the tape is listened to by the next nurse and they have no opportunity to ask questions or get clarifications. You can imagine the types of miscommunications that happen if the new nurse hears a number wrong or a medication name wrong. That's what St. Boniface is trying to prevent with having the nurses TOGETHER, talking face-to-face with the patient, including the patient in the discussion.
More about nursing and comments from Toussaint:
One of the lean success stories at St. Boniface has been time-saving practices for nurses. After tracking nurses on the job, hospital staff found they spent an average of 45 minutes per shift “looking for equipment and other stuff.” Using a lean principle, supplies were moved to a specific area, complete with labels and regular restocking from another employee in the supply area, and the amount of wasted time was reduced to 15 seconds per shift.
“The improvement has been put back to patient care. There's more time at the bedside,” Toussaint said.
“These are all manufacturing principles, they've been applied to health care and they work. Patients are more satisfied, they don't wait as long, they spend more time with their nurses and the quality (of service) is better.”
Here's a great example of a Lean method like 5S having great benefit when applied with the right purpose. 5S isn't about being neat and tidy – it's about nurse effectiveness and freeing up time for patient care. More time for patient care correlates incredibly well to improved patient outcomes (quality, safety) and shorter length of stay.
The article also has a sidebar that talks about their improvements in “door to balloon time,” which means patients with chest pain get their diagnosis faster and, when required, get their heart blockage opened up much more quickly.
I love this quote too, from manufacturing company that's inspired and helped St. Boniface:
Internal processes aren't improved by external experts, according to Brian Lanoway, a former Standard Aero executive who provided lean consulting services to St. Boniface for two years. Instead, they're improved by the people involved with them every day, such as nurses, orderlies, clerical staff and patients.
External experts can help, but it's ultimately about the involvement and ownership by hospital staff and physicians. I saw many examples in different departments of hospital staff owning their own improvement work. That's how changes are truly sustainable.
As Toussaint mentioned in his post, after two+ years of Lean, St. Boniface has improved quality and reduced costs the right way. It really seems like they are on the right path. They have very strong C-level leadership, but that leadership team doesn't have all the answers (as the picture might indicate). They are leading in a way that allows people to take initiative and thrive.
As with many of these articles, there are some misguided reader comments that show much education we still need to do. This is where Toussaint's upcoming book On the Mend may help.
One reader criticized St. Boniface for learning from Americans. What's wrong with that? At an operational level, at the point of care, things are amazingly similar even though we have different payment systems. St. Boniface is learning from ThedaCare and ThedaCare is learning from St. Boniface. This is good for everybody.
Another reader said:
Hey, if you feel patient care can be compared to assembly lines more power to you. I however, want my care directed as humanely as possible!!!
Unfortunately, that misses the point. We're not making the Lean hospital a cold, uncaring “assembly line.” Look at the Dutch example of “loving care.” When we free up nurses from running around searching for supplies and equipment, that gives them time to be more humane and caring. When a patient gets the proper diagnosis faster, what's more humane than that?
Efficiency and productivity in healthcare, the Lean way, leads to better quality and a more humane environment. It's a shame that so many assume quality and cost are tradoffs or that efficiency and humaneness are tradeoffs. Lean lets you have it all – better safety, quality, access, cost, and staff morale. ThedaCare and St. Boniface are both proving that.
Please scroll down (or click) to post a comment. Connect with me on LinkedIn.
Let’s work together to build a culture of continuous improvement and psychological safety. If you're a leader looking to create lasting change—not just projects—I help organizations:
- Engage people at all levels in sustainable improvement
- Shift from fear of mistakes to learning from them
- Apply Lean thinking in practical, people-centered ways
Interested in coaching or a keynote talk? Let’s start a conversation.
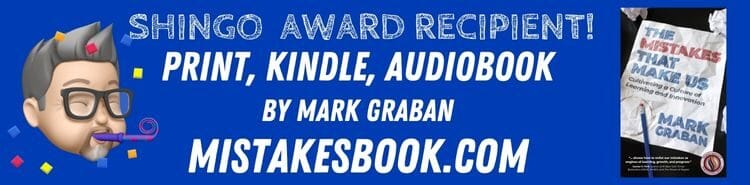
Mark – thanks for this blog about Boniface. It just so happened that soon after I read it we were giving a presentation on 5S. So I referenced the example to drive home the point of the objective and value of 5S
Keep up the good work
Hi Mark-thank you for your blog on St. Boniface and it was a great experience to meet the participants in the Gemba from Healthcare Value Leaders Network. I also noticed the comment from the person who criticized that we were “learning from the Americans”. As a care provider who has worked in both Canada and United States I can say first hand that both countries have huge room for improvement, isn’t that what brings us to the common ground of using lean to do so? Personally I am grateful that we are in this journey together!
Jonathan and Genevieve – thanks for the comments. Glad to have met each of you in the past few weeks. Genevieve, I agree that there’s a lot to learn across national borders, that’s part of the great opportunity with the lean healthcare movement.
Here’s a nice summary of our Healthcare Value Leaders Network visit from Mike Stoecklein:
http://gembawalkabout.tumblr.com/post/545508346/lean-thinking-at-a-canadian-hospital
[…] Helen Zak, the President and COO of the Network, hosted a session for IHI attendees to learn about our efforts. After her overview presentation, we had two presenters from our Network member organizations: Barb Bouche from Seattle Children’s Hospital and Dr. Bruce Roe from St. Boniface General Hospital in Winnipeg (see this earlier blog post about visiting his hospital: “Learning and Sharing Lean Healthcare in Winnipeg“). […]
[…] Check out their website about their Transformation work and this 2010 article from the Winnipeg paper (and my blog post about it). […]