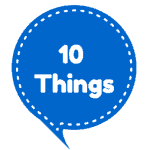
In the blog tradition of “Top 10″ lists (and “do not say” lists, like this one from Time or this workplace list from CNN), I'm going to take a stab at a list of things that I hope Lean practitioners will avoid saying in 2010. With apologies to David Letterman…
1. “Let's lean out that department.”
This phrase has long been the bane of a Lean Thinker's existence. To “lean out” a place implies a few incorrect notions.
First, it implies that Lean is a process that you can complete. It sounds like a cliche' at this point, but Lean is a journey, not a destination. Nobody ever has a waste-free process and Lean is an ongoing management philosophy, not a project to complete.
Secondly, the phrase implies that we can go “do Lean” for somebody. External forces, like a consultant (or, sigh, “sensei”) can play a role, such as teaching or coaching. To be most effective, the team members and leaders in that area must embrace and own the transition to Lean Thinking. It can't be done “to” them or “for” them, it must be done “with” them.
I'd accept “lean is a journey” as a nominee phrase to consider avoiding, but I'll probably keep seeing that one.
2. “We need to redeploy bodies.”
Redeploying people (or assigning them to another department or a new job) is definitely the preferred alternative to using Lean improvements to drive layoffs. “No layoffs due to Lean” policies are smart and admirable.
What I don't like is the use of “bodies” or “heads” to describe our most valuable asset, our people. At least calling people “heads” implies that you expect them to think. But still, I think we can just call people “people.” Even seasoned Lean leaders,
3. “We need to hire a ‘sensei.'”
It's better than saying “we need to hire some heads to help Lean out that department.” Let's just call a consultant a consultant. Or, better yet, a “coach” or “advisor.” Sensei furthers this whole mystique about Lean, that Lean is complicated and foreign, when it's really quite simple and should be accessible to all, not just senseis or “belts.”
Sensei is a Japanese word that doesn't always have positive connotations. Quoting Wikipedia (sorry to be doing that):
“Sometimes enthusiastic supporters and admirers use it fawningly, as when addressing or talking about charismatic business, political, and spiritual leaders. Japanese speakers are particularly sensitive to this usage when it concerns members of an in-group who spontaneously associate or identify sensei with a particular person – many if not most Japanese speakers readily see this usage as indicative of adherents speaking of a charismatic spiritual or cult leader. When talking about such situations, Japanese speakers will sometimes use the term sarcastically to ridicule overblown adulation…”
Yes, I realize Jim Womack used the phrase “lean sensei” in Lean Thinking. I think it's OK to question that at this point in our Lean progression. I mean no offense to the people who use this term, but I think it's a bit overdone in the Lean world. Do organizations benefit from having a consultant, a coach, or advisor? Yes, absolutely. I, for one, will never hang the term “sensei” on myself. I had the job title of “Lean Expert” once, and that was bad enough.
4. “Our goal is to do XX kaizen events this year.”
That's completely the wrong goal, the number of events. If this is pushed as the primary goal, it's possible that you'll get a certain number of easy events that don't deliver much value. This is, at best, a secondary goal – with the primary goal being improvements in safety, quality, time, cost, and morale. Or better yet, the primary goal can be learning, as it is at Toyota, per David Meier.
5. “Lean says we should ____________ …”
Or, a variation in the form of a question, “What would Lean say about __________?
Lean is not a person, it is a set of principles. It shouldn't even become a number of set-in-stone principles that are a replacement for thinking. We can learn from Lean principles, but we shouldn't blindly copy or implement a Lean principle without thinking. I worked for one company in the 90's that had gotten really excited about the supposed Lean principle of “Zero Inventories” (thanks, probably, due to book of the same title ). They cheerfully got rid of their finished goods inventory, only to find that their production lead times were too long and too highly variable for that to ever work. Blindly following a rule really hurt them and their customers.
“What would Lean say about our batch size?” Probably that it could be smaller than it is now, but we don't know that as an off-hand answer. Rather than falling back on a role principle or a rule of thumb, it's better to think through situations yourself or follow a number of Plan-Do-Check-Act cycles (or PDCA). There's a reason some Toyota leaders call TPS the “Thinking Production System.”
6. How do I get my ___________s to buy in?
This expression is often used with: managers, front-line employees, physicians, executives, nurses, etc. Far too often, “How do I get my employees to buy in?” is hidden code for “How do I get my people to fall in line and do what I say?”
If we are expecting people to “buy” in, I'd argue that, as leaders, we must be “selling” Lean or other concepts. Lack of buy in means, at least, that people are engaged and thinking. If they have a reservation about Lean or a new process, take that concern seriously. It might not just be idle complaining.
I'm sure in my previous example, there was an employee or materials manager who thought “zero inventories” was a terrible idea. Was their concern viewed as “lack of buy in” to be mocked or ignored?
7. “If you can't measure it, you can't manage it.”
I don't believe that statement. I think this phrase should be avoided and it certainly shouldn't be attributed to Dr. W. Edwards Deming, as it often is mistakenly. Dr. Deming never said this and he, in fact, meant quite the opposite. Some of the most important factors in a system are very difficult, even impossible, to measure. That doesn't mean you can't try to manage them. John Hunter, friend and fellow blogger, has the definitive take definitive blog take on this here. Update: Bob Emiliani's definitive academic article (referenced in his comment to this post) is here: WGMGM.pdf.
8, 9, and 10: “Let's hansei about our yokoten over by the kamishibai board.”
I'm not opposed to all things or words of Japanese origin. Far from it. But I think the Lean movement has gotten a bit carried away in embracing Japanese words. Some of the most recent to enter the lexicon:
Hansei = reflection
Yokoten = horizontal spread of an idea in an organization, or “spread”
Kamishibai board = well, let's let our friend and fellow blogger Jon Miller describe it. I have seen a kamishibai board in use, yes. It's a great concept, just a mouthful to say.
Some Lean Japanese words are, as we say in Texas, “a cow that is already out of the barn.” I guess this means its too late to quit saying words like “kaizen” and “kanban” (although I've never understood why it's so hard to get the cow back in the proverbial barn).
How do we get the cow to “buy in” and get back into the barn? The stupid cow “hates change,” I guess. Well, except for the change of leaving the barn to begin with. That's another nominee phrase to avoid, “people hate change,” as I had written about here.
I try to write simply and directly. If we are working in an English-speaking environment, I think we should say:
“Let's reflect about how to spread Lean over by the visual management board.”
I'm about ready to start making up Japanese terms. We need a term for “sustainment,” as much as we talk about the concept.
I think I heard somewhere that its called “Jasunbai.” Coincidentally, it's pronounced just like the name of the Boston Red Sox New York Mets' left fielder, Jason Bay. Makes it easy to remember and say, don't you think? ;-) There's a new term to DEFINITELY avoid in 2010.
What do you think? Am I wrong? Are there phrases and terms that I shouldn't be so afraid of?? Are there terms you would put on your personal “stop saying” list to complement your “stop doing” list?
Please scroll down (or click) to post a comment. Connect with me on LinkedIn.
Let’s work together to build a culture of continuous improvement and psychological safety. If you're a leader looking to create lasting change—not just projects—I help organizations:
- Engage people at all levels in sustainable improvement
- Shift from fear of mistakes to learning from them
- Apply Lean thinking in practical, people-centered ways
Interested in coaching or a keynote talk? Let’s start a conversation.
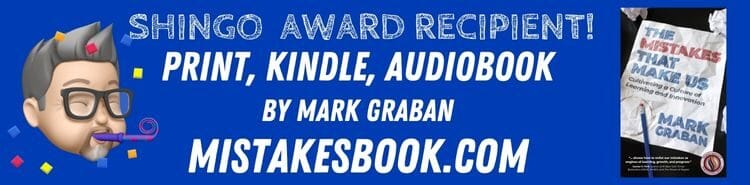
Good list. As I read the titled to the post, the first thing that came to mind was “lean out.” Too bad that’s prevalent enough that it made the top of your list too.
Good stuff. I would hope that many consulting practices out there that regularly use these phrases/words would seriously pause and reflect on them… Unfortunately, the Japanese words are slick and too many people who are new to lean are blinded by the razzle dazzle. I for one avoid them practically altogether anymore. I barely even use “gemba.” Now it’s “workplace.”
For me, personally, though, I don’t want to get too self-conscious in the connotation of my words/phrases. But, this post has inspired me to be more conscious of them. I’ll likely do a little check for understanding more frequently when I’m working with people to be sure my words are being perceived as intended.
Regarding #7, the related phrase “what gets measured gets managed” bothered me enough when I worked in industry to later write a paper that was published in 2000 titled “The false promise of ‘what gets measured gets managed”’ (Management Decision, Vol. 38, No. 9, 2000, pp. 612-615). In it, I used mathematical logic to disprove this statement. Everyone believes in this phrase, yet it is so easy to disprove both empirically (if one simply observes) and using formal logic. The phrase is really bad because it encourages a proliferation of unnecessary metrics and causes people to lose focus. Often, Lean transformations muddle along because of too many metrics and the fact that the metrics are an awful (and confusing) mix of new Lean and legacy batch-and-queue metrics. And of course that which is not easily measured or cannot be shown on a spreadsheet is typically ignored, even though the information may be extremely important for management decision-making. One of the things we have to do better is teach Lean people to do is to comprehend and utilize non-quantitative information, because their legacy is to focus almost exclusively on quantitative data.
Agreed but please share strategies to get people to embrace the uncertain world of making decisions with little to no concrete data these days….it’s difficult. Funny idea however is that you used math to disprove the statement in the first place =) See, we are data driven – to believe what is writtenl…can’t we just do what we know is right based on what we see??
@Bob – with proliferation of metrics, they also become “unmanageable proliferation of metrics” because there are too many, requiring time and people to pull the data; it’s a slippery slope from here: leadership loses focus, rank-and-file loses focus and question their place, role, and value they add to the organization, often new software packages are required to satisfy the data-metrics monster, costing more money and time for implementation, etc.
I think it was Bill Waddell over at Evolving Excellence a few weeks ago that quoted Einstein. “Not everything that can be counted counts, and not everything that counts can be counted.”
Very succinctly put.
Terrific advice, with one caveat below! I hope this Top 10 list sticks!
Regarding #6, I respectfully disagree that lean leaders should be selling. Instead, leaders should be influencing, that is motivating people to work together, decide that the articulated goals and plans are worthwhile, and then take steps to fulfill them. For a helpful distinction between influence and persuasion (which totally avoids using the awful phrase “buy in”), check out: http://nicoledefalco.wordpress.com/2009/10/29/influence-vs-persuasion-a-critical-distinction-for-leaders/
Hi Mark, as you know, I have no problem using Japanese words… but I realize many people get their feathers ruffled by it so I try to be as sensitive as I can be depending on the folks involved.
But, as an example, you say hansei means reflection… when, in fact, I learned from my Japanese speaking lean pals it’s probably better translated as repentance. So I think “Westerners” like ourselves need to be careful when we think we understand what these “words” mean.
Finally, as a fun little experiment I searched your blog for a few Japanese words to see how often you’ve used them over the years.
Gemba = 20 pages of results
Kanban = 27 pages of results
Kaizen = 39 pages of results
I stopped there… but I think the point is you seem to have seen some value in these Japanese words, no?
I get what you mean by the new words that seemed to have popped up the last year or two… but to me all this means is people are learning more and more about the richness and power of this awesome methodology we call TPS and/or lean. Is that really such a bad thing?
p.s. Sorry about your Cats… I was pulling for them. Gutsy call at the end.
I was recently given an opportunity to Hansei (relfect) on my use of Japanese terms.
My simple minded comment in respect to others is that these terms are Mis-understood in part by the ignorance of those who use them and who truly do not know what they are meant to convey and the recipient who, if given in-correct guidance/teaching in use of terms will remain ignorant to their roots, meaning and use.
The word Jishuken showed up in an Industry Week article.
“Just Say Jishuken”
Another lean term from the Far East has landed on our shores.
By Jonathan Katz Oct. 1, 2007. Unknown to Mr. Katz it is my belief that the term was all ready here!
Yes, One must be cautious when presenting terms from the Eastern thinking world. Most are NOT directly translatable to English.
Most are conditions, ambiguous, far reaching, and if you are not aware of interpretations you may be causing more harm than good.
Respectfully,
Todd McCann
Mark,
I humbly submit #11: “Rolling out Lean” (or “rolling out” anything). There are at least two problems with roll-outs: first, the focus is on the program/tool you are rolling out rather than the people. Second, what feels like a rollout to me may feel to others like being rolled over.
Alternative: engaging people or, if we want to stick to the original root, enrolling people.
Exception to this rule: if the threat of being rolled over gets the cow back into the barn
Lots of great comments today.
@Amiel — exactly, people are far too often “rolled over” by lean. Rather than rolling out the tool, think of solving the problems.
@Ron — thanks for the bowl game condolences. You’re right, I don’t avoid all Japanese words. There are simple words (like “gemba”) and the complicated/hard to say (“heijunka”) and the outright intimidating (“genchi genbutsu”). I don’t say ban all Japanese terms, by any means. And for certain settings, the Japanese terms are more easily embraced.
Thanks for everyone for their comments and tweets.
This has to be one of the most classic series of caveats re: Lean I have had the pleasure to read recently. That it hammers home the need to be inclusive and collaborative, and supports flexible thinking re: Lean vs dogma is refreshing and “right-on”.
Thanks, Bill! To my readers, I’ll share that I had the pleasure of meeting Bill last month, a former hospital COO who knows a lot about Lean.
His new organization and their lean management model is something I’ll be learning more about:
http://www.dfw-r.com/LeanCulture.html
Maybe Bill will be a future podcast guest.
Great article. I had no idea that Japanese words like sensei had become popular terms. I agree with you that it seems a bit out of place.
Do we believe the statement that “Where there is no standard there can be no improvement” as Taiichi Ohno said?
If we do believe it, how can we have a standard without measurement?
If we don’t believe it, are we saying that we can have true management without improvement?
I think the definition of “manage” is far too vague and disagree with the thrust of Mark’s argument regarding 7. “If you can’t measure it, you can’t manage it.”
One can “manage” anything poorly, without measures, without standards, without intelligence, but “barely coping” is different than “progressive management” which requires measurement.
Not everything that is measured gets managed, but what doesn’t get measured gets managed only by chance.
Jon – I agree with Ohno’s statement.
I also think you can indeed have a standard without measurement. Not everything that’s important has a simple measure. I think measures are important, we should strive to measure our results, not just hope that patient safety or length of stay improves, for example. Data is good.
But, sometimes the Deming misquote leads people to treasure measures for the sake of measures, as if their measurement automatically leads to improvement. As Dr. Deming would say, by what method? I agree with you that we need good management.
Mark, great post! As a former English teacher, I recognize the need that some writers and speakers have to dazzle their audiences with needlessly complex words and phrases. The introduction of Japanese buzzwords gives mere mortals (those folks we’re trying to get to “buy in,” remember?) the heebie-jeebies, puts them off, makes the speaker sound like a know-it-all. Respect and dignity? Bless my Strunk & White!
Nice post Mark. I certainly agree with most of your improvement suggestions however I disagree with avoiding the Japanese words in lean. Like most everyone, it is a personal bias to use or not use them. With the English language made up of mainly foreign words, what’s a few more? I posted in more detail my point of view. http://tinyurl.com/yhemqtd
Keep up the thought provoking posts!
[…] agree with this from the 10 Things I Wish Lean Practitioners Wouldn’t Say in 2010 (via the Lean Blog): 7. “If you can’t measure it, you can’t manage […]
[…] by a post on the Lean Blog, Pat reminds us that you can’t measure everything effectively. Having written my […]
Hi Mark,
Justa wanted to show this small presentation I’ve made about Lean SW Development “Lean in 4 minutes”. (http://www.youtube.com/watch?v=gBLIJKHS2tc)
I’d appreciate your feedback.
Bye!
@Mike W. — thanks for sharing the link, your post is provocative right back at me! Appreciate it.
Mark Rosenthal’s (The Lean Thinker blog) comments wouldn’t fit here, so he wrote a whole post of his own as a response:
http://theleanthinker.com/2010/01/06/leanblog-org-10-lean-things-not-to-say/
Hey Mark,
This list is good Hansei. Communication is important in any lean transformation, and how words and phrases are used can help or hurt the effort. A few comments:
Japanese words can be effective, but in most companies should be limited. We try to use only a couple, like kanban, because we haven’t thought of good English equivalents.
Regarding #6, it’s easy for people to fall back on the idea that “people hate change”. In reality, people don’t like being told they have to change. Most people will change if they are engaged in the transformation process and understand the reasons for the change.
In an effort to contribute a little more to this thread, on my new blog I’ve added “10 things Lean Consultants Should Stop Doing”.
http://leanbuilt.blogspot.com/2010/01/10-things-lean-consultants-should-stop.html
I’ve found two references to the idea that people hate being changed, from two management greats:
People don’t resist change, they resist being changed. -Peter Scholtes
Peter Drucker also said it is a myth that people hate change, they hate being changed.
http://books.google.com/books?id=R6Jg8m1e4koC&pg=PA174&dq=drucker+%22hate+change%22&hl=en&ei=z-bXTf3rJuXl0QGmpLD8Aw&sa=X&oi=book_result&ct=result&resnum=1&ved=0CCoQ6AEwAA#v=onepage&q=drucker%20%22hate%20change%22&f=false
Sometime ago I learned about what the majority of individuals in the world would refer to as “resistance to change” from Peter Senge. Senge has a different point of view on this topic. Senge states and teaches that what you are seeing is not resistance but more along the lines of balancing actions to a desired outcome in the social system. Limits to Growth / Success / Improvement. The Beer Game is a prime example and exercise that fully demonstrates limits to growth. Go See and play the Beer game.
Peter prescribes the use of archetypes in the systems thinking world. The archetypes are used to expose sometimes hidden Limits to Growth. So when anyone states we have encountered resistance my approach is to ask the question: What is/are the balancing effects present in the system(s) causing the real or perceived limits to growth > slowing and or delaying moving forward?
Most might say that this statement is only one of semantics, yet when you apply the thinking of Limits to Growth archetype, other hidden forces come forward from passionate people who don’t have an agenda. W. Lareau and I had many discussions regarding such a phenomenon. The limits to growth is a naturally occurring system, ergo it continuously happens in nature all of the time. Think of a forest it does not grow wildly out of control there are balancing forces in nature to curb the growth, natural checks and balances, so why should it not apply to social systems?, ie. specifically those undertaking a journey of Continuous Improvement in their establishments.
Respectfully
Todd McCann
The Beer Game is a great exercise… but I think it teaches different (and also important) lessons about supply chain design and execution.
Senge is brilliant, but the language and terminology isn’t exactly the most accessible to most people. Talk of archetypes, etc. requires some translation to really be well understood, I think.
It is accessible to all people. Through SoL The Society for Organizational Learning and Pegasus Communications.
http://www.pegasuscom.com/
The genesis of the Beer Game.
Forrester, J.W. (1961) Industrial Dynamics. Cambridge, MA: MIT Press. Contains a description of an early version of the Beer Distribution Game.
If one takes the time to understand the thinking and techniques of systems thinking and systems dynamics, they will create positive outcomes. Systems thinking has been applied by many of the Fortune companies to create breakthrough thinking to get un-stuck.
The game’s intention is to expose underlying structures of complexity in a system. The thinking and new learning can be applied to every naturally occuring system in existance. The presence of the lack of positive Feedback loops causes the system to breakdown, aka “re-enforcing loops”. I had the opportunity to Go See Peter last year and participated in a 3 day workshop. Foundations for Leadership.
He spoke of Deming, Juran, Ohno, Shingo, TPS and Lean thinking. He is a supporter of the Lean Thinking in the US as well as everywhere.
He is referenced in Lean Thinking books as well.
Respectfully,
Todd McCann
I’m glad to hear Dr. Senge speak highly of Lean and other systems thinking approaches.
Yes, there are broader lessons from the Beer Game – including the impact of time delays on our ability (or inability) to draw correct assumptions about cause and effect, etc.
My point was that some of the language used by Dr. Senge is very academic and, at times, overly complex, making the amazing insights in books like The Fifth Discipline less accessible (meaning “understandable”) than they could be. The man is a genius, don’t get me wrong.
Todd,
I have plenty of respect for Peter Senge. I taught systems theory for four years in Seattle University’s MA Organization Systems Renewal program, assigning Senge, Wheatly, Maturana, and others for readings. We also brought Peter Senge, Fritjof Capra, Linda Booth Sweeney, and other systems theorists to Seattle as guest lecturers, so I know these people as friends and colleagues.
Now, I had already been a lean consultant for fourteen years before being a systems professor. What I did not see in all the wonderful work of the systems folks was actual corporate or organizational transformation from systems thinking or systems dynamics. I’ve seen it with lean methods and philosophy — at Boeing, Toyota, Virginia Mason Medical Center, Seattle Children’s, Boldt Construction, and Herrero Construction, and lots of Japanese manufacturers and suppliers (visited Boldt and Herrero again last week).
You assert that “Systems thinking has been applied by many of the Fortune companies to create breakthrough thinking to get un-stuck.” That’s not the same accomplishment as Lean being the method and approach for changing the way an organization makes their product and serves their customers. That’s what lean has done both with and without a lot of systems theory.
Mark,
I like Drucker’s phrasing better, and have been quoting him lately when talking about the importance of employee involvement and education. A simple phrase, like “People don’t hate change; they just don’t like being changed”, is easy to communicate and explain, and can have a big impact. Just ask the Vice President how she would react when she enters her office on Monday after the lean experts came in over the weekend and redesigned her space to make her safer, more productive and cost effective. Would simply showing her the kaizen results (while wearing your kaizen t-shirt) convince her that she and the company are better off by eliminating her chair, raising her desk and putting her stapler and pens on a shadow board? Would a kaizen coffee mug and a few words of support form the President make her feel better? What’s the likelihood her office will remain “improved” for very long?
@Brian – thanks for sharing that post. I agree completely on point 6, I’ve always said “people don’t like to be told what to do.” People typically love change if they are initiating it or at least have some input. “People hate a change” is a sorry excuse for people to fall back on when THEIR change is not readily accepted by others.
Great post Mark. I agree with everything except for the part about Japanese words. I think it is OK to keep the cow out of the barn as long as the use is handled responsibly.
If trying to impress someone with your Japanese vocabulary – don’t use it.
If teaching lean thinking is getting held up because of the words – don’t use them right away and share another time.
I think the use of Japanese language should not be a either/or proposition. I think both English AND Japanese can co-exist provided the speaker/writer evaluates if the audience responds as desired.
As to point number 6, if a leader or consultant has to “sell” lean, then they are seeking compliance and not commitment. I like how you tie “buy-in” as a metaphor for being sold to.
@Brian – Great points. I agree it shouldn’t be all or nothing with Japanese words. In all things, balance.
I agree on your comment on Point 6.
Mark, I like much of what you articulate here. I have hardly used any Japanese terms in 20 years of lean consulting (really did study Nagoya engine plant in 1990, creak). The only term for which I never quite found a synonym was hoshin kanri, although “management by method” was an accurate if mystifying translation.
Regarding setting goals for a number of kaizen events, I agree with you in principle. But in practice, IF kaizen events/Rapid Process Improvements are going to be a primary method of engaging many employees in serious process improvements early in an organization’s lean journey, then setting aggressive quantitative targets will work IF you have a method, and probably IF it’s a major hoshin for the organization for two to four years. I think both Virginia Mason and Seattle Children’s have proven this, and probably Boeing. AND those kaizen events/RPIs would not have been, or were not, as successful without strategically thinking through where to conduct those numerous events.
Another “Top 10” list — this time a list of resolutions from Pat Wardwell at the GMBP:
http://leanjourneytruenorth.blogspot.com/2010/01/ten-new-years-resolutions-for-lean.html
Ron Pereira chimed in with his take on this issue:
http://lssacademy.com/2010/01/06/kanji-and-humility/
[…] Now, I’ve seen a job posting for a hospital in Montana who wants a “Lean Sensi.” Argh.The proper term, when used, is “sensei.” This term, taken from Japanese, of course, is often used to describe a Lean change agent or coach, even in an American setting. It’s a term that I would prefer people not use, as I wrote about here in “10 Things I Wish Lean Practitioners Wouldn’t Say in 2010“). […]
Loving this post, added to our twitter page – i think you could rename the post to 10 things Lean consultants always say! – this reminds of a game called buzzword bingo where you tick of the the things you KNOW the consultant will say!
[…] 10 Things I Wish Lean Practitioners Wouldn’t Say in 2010 (leanblog.org) […]
Good list.
I first learned of and studied TPS in 1980. Since that time I have lost count of how many companies / individuals I have worked with in a proces of continuous improvement, i.e., the continuous improvement of the constraint limiting the attainment of our (their) goal.
I have 2 belt colors; one is brown and the other is black. They match my shoes.
Frankly, I have little to no use for “lean” practitioners who are focused on the tool set and have no appreciation of what it takes to run a business. Leadership is the ability to create a vision of the future and cause people in the organization to create their own solutions to get where they need to be. If they use “lean” tools, good for them….. but do not confuse “lean” with strategy or vision.
As I said, good article.
Erik Hager, a lean “Sensei” was taught by another “Sensei” Hajime Ohba at Toyota. Erik doesn’t use that term for himself but he recognizes the value of being mentored by “one who has gone before” and passed the knowledge on to another. “Sensei” does have value in spite of the fact that it is now an over-used, hackneyed term. Just because it has lost some of it’s original power, does not mean we should not restore it to it’s original place and meaning. Erik is busy helping companies without worrying about titles or certification because the real value is in what you accomplish. He is a “Sensei” because he is seeking to mentor others in the TPS thinking. I’m sorry if it sounds like there is a difference between what Erik knows and your garden variety lean consultant, but the reality is, there is a difference.
A good article otherwise.
Paul – thanks for your comment. I’ve met Erik and I know he’s not a hack. As you state, as the term “sensei” gets used more often, it becomes meaningless. As the term is self-appointed, it becomes meaningless.
I value real sensei. I cringe when suddenly everyone is a sensei. Am I a sensei? No.
How do you “restore” the term once the meaning is degraded. You can’t tell people to stop using the term (my blog post is a “wish” not a “command”).
[…] know the title of the video says “Lean Sensei” and regular readers know I don’t like the profligate use of that term. I’ve met Erik and he’s the real deal (as explained in this blog […]
[…] Neither is even close. Fortunately, most good continuous improvement, lean, six sigma, and similar practitioners and trainers understand this and build in soft skills to projects. […]
[…] 10 Things I Wish Lean Practitioners Wouldn’t Say in 2010 – Lean Blog- 5. “Lean says we should __________ …”6. How do I get my ___________s to buy in? […]
Lean suffers from what all anti-cultural movements suffer – hard to build its own prominence and respect within the wider community if it is pulling apart the very same accretions of culture and meaning from others.
For example, if you go into a hospital and educate the staff that layers and layers of history, culture and status that have built up over decades are just ‘waste’ and that the customers don’t want to pay for it…and that staff should just focus on value…then you are unable to impose any layer of culture of your own, whether it be Japanese terminology, a cult of masters and contrary thinking about issues.
Even Six Sigma, to its credit, at least has its own culture that demands respect – even if it is built on an arcane basis of statistics and has use adopted the martial arts gradings to reinforce it.
Lean seeks not to be like these – to be about plain thinking, grass roots respect and personal development, but as such will not leave much of a footprint, and therefore not much of a legacy.
Mark has posted before against mass mobilisation in the workplace using posters, which is fair because they are a poor tool and do not communicate respect for staff…but the consequence of this is that Lean will remain only in the hearts of those that know it.
re Japanese language – I do detect an undercurrent of racism about this. I do not see much recoil about lawyers using Latin or Norman French in their day-to-day business, nor about doctors making up new Greek words for machines or drugs they invent. Music students and Opera fans must know Italian.
I do not see much resistence to German being used by car enthusiasts, so much so that Volkswagen, Audi and BMW now market in English-speaking countries in German. They know German = reliable and there’s no reason why we should be afraid of Japanese = disciplined, respectful, thoughful as a cultural branding.
The Anglosphere is in decline and the day will come when we will all need to know more Chinese language (which suits me as I do already). The kanji you have already learned, like Toyota’s Shin-To-Tai I saw at their local plant, will certainly place you in the lead as advance towards the next paradigm.
Deceptive goals or buzzwords like “zero inventories” show how people will grab on to a shorthand word (does something like “lean” come to mind?) without reading the book or talking to the author. While I think Doc Hall would approach his Zero Inventories book differently now after 30 years, it does a remarkable job of hitting nearly all the principles we know as lean and not oversimplifying matters. In part, it was the failure of production management folks to grasp what he was trying to convey, particularly in regard to pull vs. push systems, that drove him and a few like-minded folks to defect from APICS and its death grip on MRP to found the Association for Manufacturing Excellence. Maybe it would be a good 2011 goal for people to go back and read a few of the mid-80s books on Japanese manufacturing to see how far we’ve come.
Good post. I first learned of and studied TPS in 1980. Since that time I have lost count of how many companies / individuals I have worked with in a process of continuous improvement, i.e., the continuous improvement of the constraint limiting the attainment of their goal.
[…] hur viktigt det är att öka effektiviteten. De sätter igÃ¥ng projekt med metoder som lean och six sigma. MÃ¥let med dessa metoder är att ta bort allt spill frÃ¥n organisationens processer. […]
Karen
I found Doc Hall refreshing when he spoke here last year. Hat and accent but otherwise not your average Texan!
Mark,
The definition of the word Sensei is a simple minded one.
A teacher, instructor.
They are respectful, humble and disciplined.
Disciplined in many forms.
Exceptional Instructors Challenge their students constantly.
They do not give away the answer.
During my youth I practiced martial arts, my Sensei was a great instructor. He brought to life new ideas and thoughts of my person, my confidence, self esteem, all positives.
Personally, I don’t see the word Sensei being overused but mis-used.
The teaching I received was difficult, challenging and enduring over time. In addition I was taught to take my new knowledge and share unconditionally for the beneift of others. Plain and simple.
Call it a code.
Respectfully,
Todd McCann
I find it interesting that the concepts originated in America or from Americans (Ford, Deming, et al.), was taken to Japan, used there and not being transfered back in Japanese terms.
Steve – I’m not opposed to Japanese terms, but the risk comes when people take it too far. If the Japanese words are intimidating or creating barriers to learning or action, then we need to be careful about that.
I think organizations can do just fine with Lean without kamishibai boards and yokoten.
Can only reiterate my point from other Lean blog posts – I walk into a room full of doctors (as I’m sure Mark does) and end up speaking Greek to them.
They can use terms like nosocomial or iatrogenic or whatever that have perfectly plain, English equivalents but they would rather use Greek. So I wouldn’t worry about using Japanese terms, within the craft.
Two wrongs don’t make a right, in terms of using jargon or confusing terms, whether it’s from the medical professionals or lean professionals.
I think the Leanest language is the simplest language that communicates the most effectively (based on the eyes of the listener or receiver of the communication).
No one is saying a doctor should say to his patient “You’ve got an infection acquired nosocomially and iatrogenically” when he stuck a used syringe in a patient at a hospital. But if that is the most direct way to say it to another doctor, then let it be.
It speaks more to the issue of what a profession means:
-Doctors use Greek
-Lawyers use Latin and Mediaeval French
-Chefs use French (and the word itself is)
-Couturiers and Sommeliers and Vignerons also do their craft in French
-Religions use dead languages like Sanskrit, Latin, Ancient Greek and classical Arabic, and revive languages like Hebrew.
All of these would class themselves as professions. Strong professional codes and cultures.
If Lean becomes a profession then it will use its language. What is probably more the point is do we want to be a profession, or merely an assistance to people to think.
Arguably, that’s what doctors and lawyers once were. Assistants to ordinary folk to manage their own health and their own affairs. But over time they took over the management of these matters and ordinary people delegated/abrogated their own responsibility for them. You no longer went to a hospital bed to recuperate and consult a doctor. You went there for them to do things to you. And the things they did attracted labels that were very precise.
In process improvement we can’t afford to do this – Lean should never become an ‘overhead’ like paying your legal bills or healthcare bulls. That’s a reason I object to “Quality” departments when I see them.
That said, the quickest way to explain to another lean practitioner that you had a kaizen event or went to the gemba is to use those words.
I once heard Toyota had an objective to survive 1000 years. If it does, I’d like to imagine in 1000 years all those Japanese terms enshrined the way all the mediaeval French and Latin has become embedded in our Legal language. English is so much richer, and arguably one of the richest languages, because of 2000 years of borrowing from the languages of the world, which is why words like liberty and freedom aren’t perfectly interchangeable.
[…] To the contrary, I’m a big believer in the “no layoffs due to Lean” policy and I’m always the one teaching methods that hospital staffers can use to improve their own work. I agree the word “consultant” has baggage, which is why I’d prefer “coach” or “advisor” (but not necessarily “sensei”). […]
Hi Mr. Graban,
This list as usual is absolutely consistent, however the difficulty of selling it to the laity and especially CEOs is too big.
When hiring a Sensei, they think have gotten rid of all unpleasant decisions and that they may seem sympathetic to their employees eyes, no one will do their services, only lead them to inevitable conclusions.
They expect have done hiring of a booklet with instructions, rules and performance indicators ready to be used, like if every company did not have their own quirks and covet reducing the staff like if it were the primary way of earning. Otherwise normally working on waste in areas like safety, quality, cost, time and inventories makes possible to overcome the expected goals.
It is easier and keeps the collective moral high when you can just use the non-replenishment of the natural turnover and only replace the inflexible persons, after listen to them carefully and exemption and deeply examine the reasons of discordia. We have much to learn from them.
We can, if it is imperative for the manager, use the names in fashion, but the solution is in simple things like the A3, Kaizen, PDCA, JIT etc., The secret is to engage people and motivate them to think of simple and different ways to do the same . The Sensei must be able to detect the correct proposals, group them, sell them to the managers and give the credit to those who have them.
hugs,
[…] My friend, and fellow Texas lean blogger / Big Ten college football fanatic, Mark Graban wrote an article earlier this week summarizing ten things he wished lean practitioners wouldn’t say in 2010. […]