Will the Real Lean Production Please Stand Up? | Labor Notes
Yesterday, I blogged about how a nurses' union in Canada was supporting the province's lean healthcare activities for improving patient care.
Going back a few weeks, I blogged about a union website's criticism of what they described as “Lean” in some hotels. I put “Lean” in quotes because much of what the union wrote about sounded more like “L.A.M.E.” (Lean As Misguidedly Executed, as I coined it a few years back)., not real Lean.
Unfortunately, nothing stops any company or organization from practicing whatĀ Jim Womack has called “stupid meanness” in the name of what they label incorrectly as “Lean.” Managers could say they are implementing “systems thinking” while doing bad things that would make that crowd squirm and cringe. Bad management is bad management.
True “Lean,” based on the Toyota Production System, starts with the customer and includes the ideal of “respect for people” (meaning their employees, among others). If hotels use Lean as a mindless “speed up” program where employees are pressured to work faster, or if more people are getting hurt, or if employees aren't included in the process, that's L.A.M.E.
So in the light of that original union criticism, I tried to defend Lean to try to help clarify that not all Lean efforts are equal. Just because some people do bad things in the name of Lean, that doesn't mean Lean should be discounted completely as a methodology.
The union wrote back with a second post, linked at the top of this post andĀ also here. They made fun of our use of the term “lean community” but, hey, the union folks call each other “brothers and sisters,” so there's no monopoly on curious-sounding terms. My point isn't to get into a tit-for-tat with the union… so back to the topic at hand.
The union writer, Chris Kutalik, gives our “community” some credit for being “high-minded” in defending what's really Lean vs. L.A.M.E. It's fair to say that many (or most) of us reading my blog regularly do show respect for people and don't want people getting hurt.
Kutalik says that Lean, ideally, is about eliminating waste. He forgets (or doesn't know) the “respect for people” principle. Does Toyota live up to that ideal perfectly? No, they are human. But at least Toyota sets the bar high, unlike many companies who practice the “to hell with people” principle.
He writes:
“In theory, a more efficiently-organized workplace would be a safer, happier workplace.”
Yes, that's absolutely true when Real Lean is being practiced. It's not just “theory.”
They trot out a study or two that supposedly proves (extrapolating) that all Lean efforts make workers miserable and hurt people. That's not true, their criticism is overgeneralizing by far. I have helped teach Lean methods and thinking to professional staff members and managers in many hospitals where morale improved dramatically (in measurable ways, based on survey data). Lean done right creates a happier, more engaged, and fulfilled workforce. L.A.M.E. creates frustration and cynicism (so does bad management under any label).
Even if we disagree on the extent of how commonplace “L.A.M.E.” is, I'll give them credit for coining a new “L.A.M.E.” acronym: “Lean As Mainly Experienced.” I'm going to add that to my repertoire.
“[Lean] has frequently meant fewer workers doing more work in jobs they control less and less.”
Real Lean is about giving MORE control to people doing the real work. Lean leaders give up their old command-and-control mindsets and allow people to practice “kaizen,” making their work easier and helping them do a better job of serving the customer's needs.
We're on common ground with Chris. I appreciate it when people speak up to criticize L.A.M.E. when we see it — and taking control away from people is certainly L.A.M.E., not Lean.
I think we need to do more to unite and speak up to defend the ideals of what Lean is supposed to represent. When other groups unfairly criticize Lean as being “just a bunch of tools,” we need to speak up and remind people that Lean is a philosophy and management system. When consultants promise “fast Lean” or simple prescriptions that can be blindly followed, we need to speak up and say, “No, Lean is hard, and it requires you to think, not copy.”
A friend suggested we need a support group to deal with this sort of unfair, overly broad criticism. Maybe this blog is that support group. If you see articles representing “L.A.M.E.” of any form, share them with me. As the union suggests, the “Real Lean Production” does indeed need to stand up… and speak up. I've registered the domain “LAMEnotLean.com” — what should we do with as a “community”?
Thanks to Labor Notes and Kutalik for spurring us to action.
Please scroll down (or click) to post a comment. Connect with me on LinkedIn.
Letās work together to build a culture of continuous improvement and psychological safety. If you're a leader looking to create lasting changeānot just projectsāI help organizations:
- Engage people at all levels in sustainable improvement
- Shift from fear of mistakes to learning from them
- Apply Lean thinking in practical, people-centered ways
Interested in coaching or a keynote talk? Letās start a conversation.
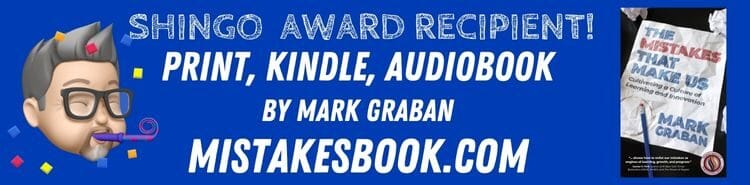
Thanks for summarizing this thread of conversations and blog posts Mark.
I read the Labor Notes response but see one flaw as it applies to how people are "mainly" experiencing lean. When does a union hear from its membership about a management program? When it's going poorly. Do they get lots of input when it's going well? Certainly not. Do they hear about it from those locations that are not unionized? Not unless they are in an organizing effort.
That's flawed data. The fact is that if you go broadly there are many, many, many examples of success where lean has helped both the company and the employees.
A lot of our clients will claim it is harder to apply lean in a union environment. I agree that it's different. But a union environment more than anything just establishes a set of rules. You may or may not agree with the rules, but they are the rules. If you are honest, play by the rules, and communicate with the union, I see no reason for lean in a union environment to be difficult.
It has been in cases. I have seen union officials run out of their position by their peers because they supported the lean efforts. That doesn't make unions bad, just that particular one bad.
A former mentor of mine was the UAW VP who helped set the vision for the GM Saturn – UAW partnership. Not everyone saw that as a good thing, but it was a revolutionary agreement. He said "Union reflects management." What he meant was that if you had a bad, argumentative, uncooperative union, it was likely just a counter-force to having an overbearing and inconsistent management.
Yes, the rules are different in a union environment. You do have to change your approach. But that doesn't mean you cannot succeed.
Jamie Flinchbaugh
http://www.jamieflinchbaugh.com
De-skilling, speeding-up, etc., are persistent, long-standing criticisms of Lean from workers – union-represented or not. These criticisms go back to antecedents to Lean such as 1880s Scientific Management. Mr. Kutalik is reflecting a reality which should force us to recognize how spectacularly unsuccessful the leaders of progressive management, as well as progressive management practitioners, have been over many decades at addressing these basic worker concerns. That they linger on after more than 100 years should tell us that we remain deficient in our approach to advancing Lean management (and thus practitioners' approach to applying Lean management)- which as I have pointed out in one of my books, is largely the same today as it was 100 years ago. We're doing the same thing but expecting a different result, which does not seem likely to happen.
I like the idea of a web page devoted to clarifying the difference between Lean and LAME. I'm not sure what kind of web page would be most effective, but I could envision a wiki format that allows Lean advocates to build a common knowledge base that can be edited, refined, and continuously improved. This knowledge base could be split into two main branches: 1) information explaining what Lean really is, and 2) information dispelling myths about Lean and explaining what LAME is. Whatever you come up with, it will be much appreciated by the Lean community, I'm sure.
One minor note about the domain name, LAMEnotLean. It kind of sounds like a rally cry choosing LAME over Lean. Kind of like "love not war." To clarify, you could reverse the order to "Lean not LAME" or go with something like "LAME aint Lean." Just a thought.
Good point, Mike. I wondered about that. Domain names are cheap!
Thanks also to Jamie and Bob for their comments. Anyone who is a new reader of the blog should check out Jamie's book (Hitchhiker's Guide to Lean) and Bob's many books in the "Real Lean" series (I linked to him above in the "Respect for People" phrase).
While it would take years, I think the entire Lean community should make a concerted effort to move away from the word "lean," simply because the word is too often misconstrued and misused. I frequently hear "they run a lean operation" which has nothing to do with true Lean.
I don't know the answer, but there has to be a better word or acronym, something that better represents the values and philosophy of TPS and Lean.
On Twitter, @shawnevandeusen wrote:
Worth reading in spite of the title – "Leanies"? RT @flinchbaugh @leanblog: New Post: Leanies of the World, Unite! http://u.mavrev.com/08dlm
Fair enough. I hate the term "leanies" and normally don't use it (and I cringe when I hear it). But I wanted a parallel to "workers". Could have also gone with "Lean thinkers of the world, Unite!"
Yeah, "leanies" is not a good word. The whole Lean lexicon is a bit difficult to use. There's a lot of jargon (which I know is a pet peeve of Jamie Flinchbaugh), and the word 'lean' itself is just not marketable. It just doesn't invoke the positive thoughts that you'd like to have associated with such a wonderful methodology. I know it's just a superficial issue, but for some reason, lots of people just can't get past the negative connotations associated with the word 'lean.'
I still like Scott McDuffee's Fruit Salad Production System :)
Mark;
As with Jamie, I've experienced great success in union environments with continuous improvement methodology. It wasn't really hard but certainly different. In many cases, the union environment has set rules, which establish the boundaries in which to operate. I'm finding more and more that the word "lean" has a tendency to hinder and set automatic boundaries to the purpose of continuous improvement. We're going with a CI or continuous improvement wordage because we simply want to consistently improve on what we're doing today. Excellent comments by all.
Let's face it – most "lean" deployments or transformations are not ultimately driven by a vision of "long-term mutual prosperity" as at Toyota. Even if the operations people and some others higher up get the significance of this as a foundation of success, if the sole purposes of enterprise remain maximizing return to shareholders and maintaining management in the lifestyle to which they have become accustomed, then it is pretty likely that there will be an atmosphere (and a reality) of taking advantage of front-line workers. I'll echo (and paraphrase) Bob Emiliani's comment – if you don't change the way you think, why would you expect different results?
This is one of the core problems with transformations that start at the middle. It's not just about "getting the execs on board" with change (they are generally pretty enthusiastic when the bottom line starts improving). There is a culture of division between management and labor that our correspondents at "Labor Notes" are well justified in recognizing and calling out.
I saw W. E. Deming in a video conference in the early 90's (the year, and his age, I think!) when he delivered one of his great lines (paraphrasing): "Think win-win? What other option is there? There is no such thing a win-lose because that always turns into lose-lose."
As we explore "Lean not LAME" or whatever it ends up, let's catalog some North American examples of "long-term mutual prosperity" resulting from a business following the Toyota way.
-ALB
What I find most interesting about the Labor Notes page is that there is no alternative offered. Only criticism. Armchair quarterbacking from any position, other than the genba itself, is quite easy. I find it amusing that in the side bar of the Labor Notes page, there are many links to a cleverly branded "Troublemaker's Blog" and shopping cart links to purchase "Troublemaker Gear".
Whether union or non-union, we have to ask critics if they are going to continue to be part of the problem using antagonism or try to improve their situation with a non-zero-sum paradigm.
Bryan,
It's really easy for the union to just sit there and take pot shots. It's a political position – union leadership gets elected. So they pander to their voters the same way a congressman would. Tell 'em what they want to hear and put on a show, then you keep your power.
[…] Notes has often lashed out about Lean, as I blogged about hereĀ (see more posts). They are usually either just complaining about management (if Lean is an idea […]