Tomorrow's blog post today… not that anyone will be reading anything non-Michael Jackson related. RIP. A modern tidbit… I learned about the news via a friend's Facebook status update. The new, new media, I suppose.
Communications Woes Show at Boeing – WSJ.com:
Non-aviation folks (and healthcare readers)… stick with me, this isn't strictly a post about making airplanes.
Isn't it a fairly common dysfunction of organizations that bad news doesn't flow up? This happens in manufacturing… an old boss at unnamed company (not GM) once typified this by saying (bragging really) that “my job is make my boss look good.” That “goal” certainly wasn't accomplished by sharing any bad news. I was sickened. I wanted to focus on making things better, not just creating the fake impression of better. Bad news never flowed up.
In other organizations (and this was a GM dynamic) bad news didn't flow upward. Why? Mainly fear. Fear of being yelled at. Fear of being embarrassed in front of others and ridiculed. That fear led to team leaders faking the hourly production numbers (the shift total was correct, but the hourly numbers were smoothed out to eliminate the peaks and valleys… the valleys got you yelled at).
“…Boeing had said at the Paris Air Show just days ago that the plane was ready to fly.”
I'm not an aviation expert, but I know the annual air show (in France or the U.K.) is THE wheeling and dealing show of the year. Many planes are sold here, right?
Then, Boeing announced after the show that the test flight will be delayed.
So what gives?
I often have a bit of a philosophical debate with my wife when a company screws up — are they dishonest or are they incompetent? Sometimes you can't tell. We have a little debate about which is worse — competent but dishonest (at least they're competent) or honest and incompetent?
You might think the Boeing executives were lying in Paris. But they'd have to be smarter than that, to think that the lie would eventually catch up to them.
I don't think Boeing's executives (or GM's) are stupid.
Did they HONESTLY think the test flight was on time?
“‘During the last two years…some investors described optimistic statements by management as misleading,' wrote Doug Harned, aerospace analyst at Bernstein Research, in a note to investors Tuesday. ‘On the contrary, we saw the answers as honest, which is the heart of the problem. Management appears to have been operating without adequate visibility into the details of program performance in the 787 organization and at suppliers.'”
Honest, but a clueless sort of honest. Why did the information not get to the Boeing execs? They must be pretty embarrassed (they didn't comment for yesterday's WSJ story).
The above quote blames the suppliers, in a way. Blame — there's another dysfunction of broken organizations. Is it really the suppliers' fault? Do you “blame” those who chose the suppliers? Those who manage the suppliers? Does it matter?
The structural flaw that has grounded Boeing's 787 Dreamliner originates with Boeing's engineering and will likely add months of delay to the new jet program, an executive with key partner Mitsubishi Heavy Industries said Wednesday.
Trying to piece this together… it's probably not too much of a stretch to assume that people in Boeing KNEW that there were problems or likely delays.
Oh, the WSJ reports that people in Boeing DID know… in May, when the Air Show was in June. D'oh!
This week, however, Boeing said its engineers and senior executives alike had known since May of the structural problem that will keep the jet grounded, possibly for months.
Why did this news not get to Boeing execs? At what point in the communication chain did things break down? Who was afraid to share the bad news?
The same type of dysfunction exists in hospitals… bad news not filtering up to VPs or the CEO. Do you have examples to share (anonymously) about bad news not flowing up? What caused that? Was it fear, as Dr. Deming would have said??
There's a story in my book,
Lean Hospitals, about how the CEO in a leading lean hospital was helping create an environment where people could be honest without fear of retribution. A nurse told him bad news — that she wasn't entering information about medication errors into the computer system because it took too long. He thanked her for telling him this and worked to get the problem fixed as a “servant leader.”
Please check out my main blog page at
www.leanblog.org
The RSS feed content you are reading is copyrighted by the author, Mark Graban.
, , , on the author's copyright.
What do you think? Please scroll down (or click) to post a comment. Or please share the post with your thoughts on LinkedIn – and follow me or connect with me there.
Did you like this post? Make sure you don't miss a post or podcast — Subscribe to get notified about posts via email daily or weekly.
Check out my latest book, The Mistakes That Make Us: Cultivating a Culture of Learning and Innovation:
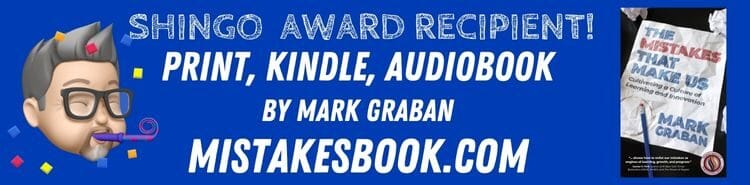
Here is an example I learned about a couple of months after the fact.
A local business unit leader issued a new edict to “force” the correction of a long standing problem. He stated, "there will be no more 'stealing' of items from kits to make up for kits sent in from the supplier with missing, defective, or incorrect items." (I am sure similar things occur in hospitals.)
The supervisors “fixed” the problem by no longer reporting incidences of missing or wrong kit items while they continued to break into kits to retrieve the parts they needed.
The policy had changed nothing for the better – it only made matters worse – the bad news (quality info about the kit problem) was no longer filtering up to those at the top.
I don’t blame the supervisors. They had seen this kind of thing before and figured the issue would go unresolved. They just decided to keep things moving. I don’t see anything wrong with the unit leader “putting his foot down” and demanding action either. He was relatively new and was just trying to get a handle on things.
The problem was the absence of a process for:
– taking on the new edict as a problem solving project
– playing “catchball” to get common understanding and agreement on a plan of action
– assigning resources and adjusting the project schedule to merge the new effort with work already underway
Without these key process ingredients present, the policy was unlikely to succeed right from the start.
While this episode exposes internal communication issues in Boeing, it appears that the root causes for these delays are elsewhere and much deep rooted.
Major flaw I notice in this case with Boeing, a company touted as a lean leader in North America, is the efficacy of Lean Engineering practices on the ground.
Apparently Boeing’s quest for technology innovation (example: use of light weight composite technologies in unproven areas of aircraft manufacturing) without adequate ‘front loading’ of the system is one of the main reasons for this issue. Fundamentally, the technology innovation has been adopted in the product even before the technology is matured for that application. There seems to be no alternate design solutions Boeing has thought of to counter the risks associated with their innovation. This is fundamental requirement of ‘Set Based Concurrent Engineering’ in lean engineering.
Of course, the subsequent product performance issues and lack of communication flow are all consequences of this basic issue.
I don’t think even companies like Boeing have realized the importance of engineering function (especially ‘front loading’ of multiple concepts) that determines the fate of their product and in turn the growth prospects of the company.
Constant ‘undue’ pressure on engineering schedule and cost targets leads to such costly ‘reworks’…