Below is a Toyota expression that I love… and this is a statement that could apply in any type of organization, don't you think? When people ask me, “How can this Toyota stuff apply to a hospital?”, I think this statement covers the foundation of it pretty well:
“Every Toyota team member is empowered with the ability to improve their work environment. This includes everything from quality and safety to the environment and productivity. Improvements and suggestions by team members are the cornerstone of Toyota's success.”
It works just as well for a mythical Keller Community Hospital (a hospital that doesn't exist, but I'm starting to use it as an example of the hospital that I would want in my community):
“Every Keller Community Hospital team member is empowered with the ability to improve their work environment. This includes everything from quality and safety to the environment and productivity. Improvements and suggestions by team members are the cornerstone of Keller Community Hospital's success.”
I had such a good afternoon yesterday, visiting a real client of mine (a hospital laboratory) that has really embraced the above principle better than any I've ever worked with. They've expanded “Lean Management System” concepts (from my book and David Mann's Creating a Lean Culture: Tools to Sustain Lean Conversions) throughout the different areas of the lab — clinical lab, blood bank, microbiology, and anatomic pathology. Employees are engaged in submitting and implementing their ideas, improvements are celebrated and posted visually, and performance measures are tracked, posted, and discussed daily in short team huddles.
I saw suggestions implemented that impacted employee safety, productivity, quality, and getting test results to patients and physicians more quickly. Every employee has the opportunity to participate in improvement. It's such a great thing to see, watching people explain what changes they've made and seeing the pride on their faces.
Now, to spread that throughout the hospital… and the rest of healthcare.
Please scroll down (or click) to post a comment. Connect with me on LinkedIn.
Let’s work together to build a culture of continuous improvement and psychological safety. If you're a leader looking to create lasting change—not just projects—I help organizations:
- Engage people at all levels in sustainable improvement
- Shift from fear of mistakes to learning from them
- Apply Lean thinking in practical, people-centered ways
Interested in coaching or a keynote talk? Let’s start a conversation.
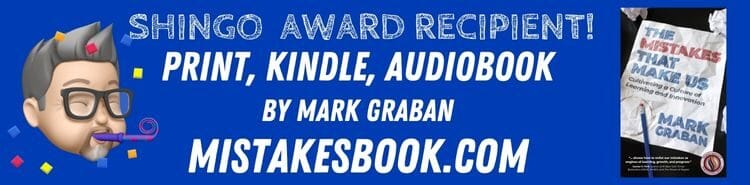
You wrote: “It works just as well for a mythical Keller Community Hospital.”
And not only that, it works just as well for almost anyone. I simply cannot recall now how many times I have heard similar comments from senior corporate leaders around the globe. “We’re not Toyota, how could this work for us?” is a common refrain.
No, of course you’re not Toyota. But a rigorous foundation of principles and practices whether in mathematics, physics or Toyota Production/Management System is applicable and transferable across cultures, industries and companies. I’m on a mission to communicate that message. Adam Zak
I couldn’t agree more. Companies and hospitals alike are looking for the “recipe” for Lean. The recipe is not just the tools, not just what Toyota did, not just what Thedacare did. It’s leading your organization in a different way. It’s engaging employees at every level. It’s understanding your customer and your strategic direction. And it’s understanding yourself, which may be the most challenging of all.
I agree to Dean Bliss on this, its about involving and accessing it yourself.
Mark;
I love the comment, “Every employee has the opportunity to participate in improvement.” This goes well with Dean’s comments on engaging and understanding. These activities present an opportunity for a culture to be changed into one of continuous improvement, while maintaining a certain degree of sutainability. Certainly this is the goal in hospitals, manufacturing or service industries. Great post!
I met a silvered hair Mr. Toyoda at the Textile Show in Greenville, SC in 1978 or 1979…..
He was a little on the chubby side but he was so present. I remember asking him about the water jets which drove the fill……..
Sheesh…I was questioning Mr.Toyoda….
Power to the People
LEAN is about giving your people the insight and authority to make a positive difference in their workplace.
NOT statistics, analysis and numbers – those are just tools on the journey to giving knowledge and Power to the People.
My two cents,
By the way, the hospital on post at my alma mater, West Point, is Keller Army Hospital. I hope they read your blog, Mark!
I agree with the statement.A team cannot be called as a team if there's no members.The main key here is how every team member is important,their opinion,skills,ability and health that contributes on the quality of their work.