Lean gamble has paid off for United Southern Industries
I hate to criticize anyone who's been really successful with Lean.
The worst thing I can say about United Southern is to ask, “What made you think Lean was such a gamble and such a risk?”
The company was really struggling, before Lean:
Custom injection molder United Southern Industries was in a financial crisis a few years ago, as were many small and medium-size injection molders due to intense competition from abroad. In 2005, the Forest City, N.C., manufacturer of products such as automobile bumper components and child safety seats lost business, forcing layoffs. In truth, meeting monthly payroll sometimes challenged them.
So did USI run to China? No, they adopted Lean. And here's the important thing… not just a half-hearted attempt at using Lean tools. They adopted a Lean Management System for the entire enterprise.
Did they win prizes for implementing 5S? No! They got business results:
United Southern's total immersion into lean enterprise, including adoption of a lean management system that permeates the entire company – not just the manufacturing floor – changed everything. Its results prove those changes work. In the third quarter of the company's 2007 fiscal year, USI's pre-tax profit soared to almost double the custom injection molding industry gold standard. It winnowed down its scrap from 5.7 percent to 3.8 percent and continue to reduce scrap. In one facility, it reduced scrap an average of $25,000 per month for eight consecutive months while revenues and volume increased. USI recently became a tier two supplier for Mercedes, BMW and Lexus.
How is it that a $30 million company with 250 employees can make the Lean transformation, while huge companies often can't? Oh, wait. It's probably because a small company can be nimble and change its culture much faster than a behemoth. What has a better turning radius, a ski boat or a battleship? Certain battleships would rather wait for government loans and bailouts because “they're too big to fail,” ala the huge financial institutions.
USI implemented the management method of “zone control” (and you can read more in the article):
“The entire process, including employee training, cost about $125,000 over a year. The resulting efficiencies will save more than $600,000 in 2008,” said Bennett.
Embracing lean methods at the senior enterprise level for almost two years now, United Southern operates in small groups using “zone control.” A little-understood and stringent lean stability management tool, it incorporates daily report-outs and the dedication of everyone, including top management. Every management employee learns to run a molding zone before teaching.
This sounds like such a great story. The leaders are learning, and they're turning into teachers. A great Lean leader is a coach and a teacher, that's such a common theme in so many of these Lean transformations, regardless of the industry.
“Sam's bold and strongly believes that senior leaders need to lead by example,” said Bennett. “He challenged my commitment and told me to be the driver. He told me that he would be a teacher-leader and I would teach and lead my organization. He said to lead our transformation from upfront and not rely on external consultants or staff-level change agents. So now it's an everyday commitment.
The article also talks about their implementation of Hoshin Planning, aka Policy Deployment.
United Southern Industries president Todd Bennett and North Carolina State University lean practitioner Sam McPherson will present a case study on lean and zone control at USI during Reliable Plant magazine's “Lean Manufacturing 2008: Lean Tools for Maintenance and Reliability conference”, October 6-8 in Chicago.
Click on this link for books on hoshin planning (via Amazon).
Please scroll down (or click) to post a comment. Connect with me on LinkedIn.
Let’s work together to build a culture of continuous improvement and psychological safety. If you're a leader looking to create lasting change—not just projects—I help organizations:
- Engage people at all levels in sustainable improvement
- Shift from fear of mistakes to learning from them
- Apply Lean thinking in practical, people-centered ways
Interested in coaching or a keynote talk? Let’s start a conversation.
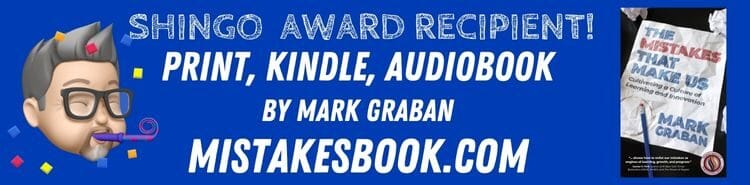