Listen:
Here is LeanBlog Podcast #40, an interview with a retired UAW/GM employee who wishes to remain anonymous, at this point. We have traded many emails over the past year, about Lean, and I'm impressed with this individual's true passion for Lean and Toyota Production System concepts.
We both agree that the “root cause” of many Lean struggles comes back to management's inability to create trust and to give up some control to the employees who actually do the work.
The intent here, from my perspective, is not “management bashing,” but rather to illustrate that there are some on the UAW side who “get it” and success is going to require true cooperation and sacrifices on both sides.
For earlier episodes, visit the main Podcast page, which includes information on how to subscribe via RSS or via Apple Podcasts.
LeanBlog Podcast #40 Key Points & Key Words
- “Quality Network” – GM and the UAW
- GM had been working with Lean methods since the early 1990s, but not associating it with “Lean” (Toyota) until this decade
- The need for trust and culture change — changing the “them vs. us” attitude
If you have feedback on the podcast, or any questions for my guests or me, you can email me at leanpodcast@gmail.com. Please give your location and your first name. Any comments (email or voicemail) might be used in follow-ups to the podcast.
Automated Transcript: Not Defect Free:
Announcer (2s):
Welcome to the Lean Blog podcast. Visit our website www.leanblog.org. Now here's your host, Mark Graban.
Mark Graban (13s):
Hi, this is Mark Graban. You are listening to episode number 40 of the Lean Blog Podcast for April 14th, 2008. We've got kind of a different episode today. Our guest is a retired United Auto Workers member who's choosing to remain anonymous because he's still involved with the union in retirement. And what we're gonna be talking about today might be somewhat surprising, surprisingly positive views about Lean and the Toyota Production System, the role that the union can play in, in helping advocate for Lean and Toyota Production System principles for the sake of employees and, and the auto industry and American manufacturing as as a whole.
Mark Graban (54s):
What, what are things that are interfering with that? How can we build trust between management and employees? Topics like that. So I hope you find it interesting. If you've got feedback or questions, I'd, I'd invite you to go to www.leanpodcast.org. Find the link to episode number 40 of the podcast and leave your questions or, or comments there. Alright, well, welcome to the podcast. It's nice to have you here with us today to talk about Lean.
Anonymous Guest (1m 25s):
Glad to be here. I appreciate it, Mark. Thanks for the opportunity.
Mark Graban (1m 28s):
Absolutely. I think we have a real interesting discussion ahead today. And, and I was wondering if you could start by talking about, you know, your background and, and personal experience with Lean As as UAW employee, you know, how it was first introduced and, and maybe what some of your first impressions were and, and how that evolved over time.
Anonymous Guest (1m 47s):
Yeah, I'd be happy to. I got about a 28-year term with General Motors. Started out as naturally a factory worker. My first opportunity to serve our union was as a scrap coordinator. Our plant was experiencing tremendous amount of scrap, costing us a lot of money, and they decided to put on a couple coordinators to try and pinpoint the problems. That was my first opportunity to serve, service our, our union membership. And after that I became a quality network suggestion program coordinator.
Anonymous Guest (2m 28s):
Really enjoyed doing that, really enjoyed serving the people. After that I had the opportunity, or our, along with that, I should say, my chairman came to me and asked me if I would represent our union as a UAW lean coordinator. Okay. I naturally jumped at the opportunity and had a few years to learn a little bit about Lane. What,
Mark Graban (2m 58s):
What, what, what was the timeframe for that? I'm just curious when that was that role just being created?
Anonymous Guest (3m 7s):
That role was just being created? Oh, about three years ago. Four years ago, maybe four years ago. Okay. And that's where I guess we start talking about how it was introduced to the plant. Technically it was introduced to our plant probably in the early nineties, but it wasn't introduced as a lean program.
Mark Graban (3m 39s):
Okay.
Anonymous Guest (3m 40s):
Introduced as a new operating system, a new manufacturing operating system. And it was diagnosed by our union workforce as just another program of the month, so to speak. So nobody really got excited about it. They just knew that management was gonna present this program and you know, we were gonna have to follow through with it and do what we do best. And that's make parts that went on for, I'd say probably to 2001, 2002 timeframe.
Anonymous Guest (4m 20s):
And then all of a sudden this word kaizens popped up. It was an all employee meaning, and we were informed that we were going to do kaizen work. We were going to become Kaizen this, Kaizen that. And that's really was the first time we've ever associated our manufacturing production system with Lean. And that's when I was asked to become a UAW leading coordinator. My first problem was, well, where's my book? You know, how, how do I learn this? So I didn't know nothing about it.
Anonymous Guest (5m 1s):
And I went to management, didn't get no books for management. I went to the union, didn't get no books from the union. So I ended up on the internet. Right.
I basically educated myself through the internet, through your Lean Blog, through the book. I bought the book The Toyota Way.
That's basically how I educated myself so that when I went into a workshop, I could represent my people fairly, right? Yeah. As everyone knows, it is Union against Management. And I was there to make sure management didn't run over our union people. And basically because I was new at it, naturally I wasn't that good.
Anonymous Guest (5m 45s):
But as time went on and I became more educated, I really developed a passion for lean and a hundred percent believement that this is what we have to do to protect this plant and to protect our jobs. So when I stood up in front of our workforce, you know, what I preached or what I taught came from the heart. It wasn't something that just came from a book. It was something that I believed really had to take place in order to save these jobs here in America. So that's basically how it got introduced into the plant I was at.
Anonymous Guest (6m 25s):
People will ask, well how, how was it received? You know, how did the workforce accept it? Well, they didn't accept it too well.
Mark Graban (6m 33s):
Okay. Why? Why is that?
Anonymous Guest (6m 36s):
Well, number one, we had a bunch of people that had a lot of years of service that you ever, you've probably heard the old cliche, you, you can't teach an old dog new tricks. Well, the old dog didn't wanna learn no new tricks, let's put it that way. Yeah. So we had a bunch of people in the workforce that just didn't wanna change management, did not take the time to change the culture, didn't even attempt to change the culture. They didn't attempt to help 'em understand the culture that developed this process. And to me that was a, a cardinal sin. I mean, you can't put the cart before the horse.
Anonymous Guest (7m 18s):
And that's what we were trying to do. Right.
Mark Graban (7m 21s):
I mean, as, as you read The Toyota Way and educated yourself about lean, I mean, what, what were the things that stood out to you that would, would have to change about the culture, the things that were different between the culture in your plant and what was being described as a, a lean or, or Toyota culture?
Anonymous Guest (7m 38s):
I guess the biggest thing that, that I see that had to change was trust.
And we have to trust each other. We have to have a, a joint atmosphere where when management says something, the union believes it, and it is a truthful statement.
It does, it does have some validity. And that's what was lacking. I mean, it was them against us atmosphere. And every time they wanted to do something that they say improved the process, our people believed it just made us work harder. And that was things that we had to overcome.
Mark Graban (8m 13s):
Right. And there's a, a long history and unfortunately a long track record of lack of trust between the parties, right?
Anonymous Guest (8m 24s):
Oh, definitely. Yeah. It's just, you know, if we could establish a scenario where a true scenario where, especially in lean, where when you improve a process, the nut guy next to you is not gonna get laid off. You know? And I did, I had, I had some training sessions to do for new hires, and one of the people raised their hand and they asked me, they said, well, what are you gonna do when, when we go out there on the floor and we improve this process that takes six people, we get it down to four people, what's gonna happen to the other two? And I says to the individual, I said, well, why do you ask that question?
Anonymous Guest (9m 8s):
Well, she says, because I just came from a plant and the last job I had was we had to lean out our, our process and we leaned out our process and we had eight people on it, and we leaned it down to six and I'm one of the two that got laid off Now. So, you know, that's not good. Right. That's, that's not a good conclusion to what should be a happy event. Right. So I spent a few minutes telling her what my beliefs were, what would happen in a scenario such as that. And that is that you would be put into a bank where you would do further kaizen events or you would do training or you would fill in for absenteeism.
Anonymous Guest (9m 52s):
That to me is the perfect world. Having said that, I'll say this, some of our manufacturing facilities are so fat that, you know, you might have to have a layoff for there.
Mark Graban (10m 9s):
And what was, was there anything presented to, to try to, you know, try to build some cooperation around, you know, how how lean would be good for the customers or, or how lane might also be good for employees? It sounds like that maybe wasn't the case.
Anonymous Guest (10m 24s):
Well they were, they were always telling us that we, you know, we gotta do this because if we wanna get Toyota business, we gotta use a similar Toyota operating system. And then ours operating system wasn't called ts, but we had to, you know, show a version of it that would be acceptable to a Toyota if they ever wanted to come in and do business with us. Right. That was what we were being told, you know, we gotta do this, we gotta do this to compete with our neighbors down the road and we gotta do this if we ever wanted to do work for Toyota.
Mark Graban (10m 58s):
I'm curious also that we, you said that the operating system, you know, that sounds like maybe it was lean without being called Lean was put in place in the nineties. The, the difference between that and when it started being called Kaizen and Lean, was it, was it merely a difference in name or was there some change to the approach?
Anonymous Guest (11m 19s):
There was big change. Okay. There was a big push. There was tremendous amount of involvement. A lot of workshops started popping. Our biggest problem at that point was getting workers to participate in the workshops. There again, no culture change, but yeah, there was a huge amount of activity that all started after that initial Kaizen event started. The ball started rolling and people started changing, you know, the way they did jobs. Some of it was kind of force fed. Some of it was kind of willingly done because they knew it was better.
Anonymous Guest (12m 3s):
But still, during all of this, you still had this huge cloud hanging over your head of, what's the word I want? Denial. Maybe it maybe be a good word. The worker thing that all they're trying to do is get more out of me. You know, no belief in the fact that this is gonna help keep my plan alive. This is gonna give my grandkids a job. None of that was, you know, to the forefront. It was all about what are they trying to do, you know, work me in the ground. Yeah.
Mark Graban (12m 34s):
So it sounds like trying to help coordinate and convince people that that wasn't the case. I'm, I'm, I'm sure it was a challenging role to be in.
Anonymous Guest (12m 42s):
Well, it was a tremendous challenge. I took it, like I said, personally, and I went to my people and I told 'em, you know,
I'd rather have you mad at me today and have a job 20 years from now.
And that's kind of what got me through it was because my job was to keep that plan open and keep as many people working as I could. Right. I believed, and I truly believe, and I still believe that lean is the way to do that. Yeah.
Mark Graban (13m 12s):
And I, I I know you're, you're very passionate about, you know, lean being potentially positive force for the automakers and for manufacturing. So I was wondering if you could share a little bit some of your thoughts on, you know, what, what you think the, the role of Lean could be and, and, and maybe what positive role that the UAW and, and other unions could have in help helping spread lean.
Anonymous Guest (13m 38s):
Well, I think as positive I, as I think about it, I do believe in it 110%. I, I, I referenced the comments made by Jeffrey Liker numerous times on your Lean Blog when, when he tells us that 95% of American companies say they do lean, but only 2% are less than 2% are successful. That to me is an issue that to me has to be addressed. And whether it be the union address it or whoever, but somebody needs to step up to the plate and say, Hey, this is what we gotta be doing and we gotta ensure that we're doing it.
Anonymous Guest (14m 18s):
We can't just stand in front of the microphones and tell corporate America say, yeah, this is what we're doing. This is, this is lean and we're practicing it. The bottom line is, is that part coming off that assembly line at tact time? And if it's not, then we got an issue, we got a problem, and if we continue to ignore it, you know, these jobs are gonna continue to disappear.
Mark Graban (14m 48s):
And so do you think, you know, with within the plants or you know, what, what, what would, what would you hope to see in, in, in the future as far as trying to help gain acceptance for lean, not just with within the workforce, but also trying to help encourage and, and educate management on, on the types of changes that need to happen?
Anonymous Guest (15m 15s):
Well boy, that's about an hour-long answer.
Mark Graban (15m 19s):
Yeah. I'm sorry. It's not an easy question to answer.
Anonymous Guest (15m 23s):
Oh. But you know, I, I have to revert back to the culture. Yeah. Management has, I shouldn't say has to drive it, but you know, management is supposed to be driving it. Right.
To me, management has to turn the triangle upside down. They have to be on the bottom. Customer and employee has to be on top. They have to support that triangle.
And they do that through financial supporting of the issues that come up in the lean process. They do that by making sound decisions to support the worker. They have to stand down there like Hercules and hold this triangle up.
Anonymous Guest (16m 3s):
That's, that's their role. And until they accept that role and develop that culture change, our lean attempts are gonna continue to fail. Cuz what I see happening is in manufacturing somebody that says, I'm gonna do lean, they go in there and I always, I always use Lean as a, an example of Lean as a cherry tree pull of cherries and manufacturer management goes in there to that cherry tree with all the different elements of lean, and they start picking these elements off the low hanging branches, and they start to profit from that and they show profit from it, they save a job, or they eliminate a job here, they eliminate a job there and they, they show their executive board or their profit shareholders that they just saved $80,000 a year because of that.
Anonymous Guest (17m 3s):
Yeah. That's a low-hanging fruit. That low-hanging opportunities that they grab easily because it's there. The rest of those cherries are those elements of lean hanging on, on the treating rot. They just go to waste because they never get there. My my theory of lean is it has to go from the front door to the back door, and every, everywhere in between. You don't do that. You're kidding yourself. Yeah. You know, you're, you're, you're gonna have areas of waste. You're not gonna realize the, the profitability that you could or the efficiencies that you could if you picked all that fruit. Right. Did that answer your question?
Mark Graban (17m 43s):
Yeah, no, I mean, I, I think that's a good diagnosis of, of what happens a lot of the time. You know, we're people are tempted to look for a quick fix, you know, or, or find the, you know, the, the lean tool that fits into their culture. You, anybody can force people to implement 5S or kanban. Right? And, and you could say, look, we're, we're doing lean, but to, to step back and look in the mirror and, and try to look at, at the culture and the way people interact with each other, that that's definitely a lot harder to do. And, and, and that it takes a special kinda leader to step stand up and, and recognize and, and say, we need the change.
Mark Graban (18m 25s):
You know, when, when I was at GM, we had a, a new point manager who came in, he had experience at the new me facility in California with the Toyota people, and he stood up in front of everybody, UAW salaried, everybody, and he said, we need to change the management system. It's not a problem with the workers. We need, we're going to change the way we manage and that's what's gonna make us all successful. And, you know, that, that was a very powerful message. And, you know, I don't think there's too many leaders, you know, that are willing to stand up and, and take that kind of responsibility. Unfortunately,
Anonymous Guest (18m 59s):
I think you're right.
Management has to be susceptible to change. They gotta accept the fact that the worker knows something.
Mark Graban (19m 10s):
Yes.
Anonymous Guest (19m 11s):
Not just a robot punching the time clock every day to come to work. He's done that machine 10, 12, 16 hours a day in some cases. He knows that machine in a lot of cases better than the process engineer can tell you when that machine isn't running right. Just by the sound of it. And the, they have a, an enormous tool out there for profitability, quality issues, safety issues, and they just refuse to use it because they don't wanna relinquish that power.
Mark Graban (19m 41s):
That said, I think there's still, I I think you and I would agree, there's still hope for the manufacturing world that you know, that the, the message will start syncing in and, and that some, some change can happen. And I, I certainly hope we get a chance to have some more discussions about that. I'd certainly invite anybody listening if you have questions, you know, for, for a future discussion on this topic, you can email me or, or leave a message on the blog and, you know, we, hopefully we can explore this more.
Anonymous Guest (20m 10s):
Well, thanks again, Mark. I appreciate the opportunity and yeah, we, we can get together again and share some more views and hopefully, you know, the right people are here and lean will go forward and American commerce will prosper.
Mark Graban (20m 26s):
Okay, well hope so. So thanks again. I appreciate your time.
Anonymous Guest (20m 29s):
Thank you, Mark.
Announcer (20m 30s):
Thanks for listening. This has been the Lean Blog podcast. For lean news and commentary updated daily, visit www.leanblog.org. If you have any questions or comments about this podcast, email Mark leanpodcast@gmail.com.
Please scroll down (or click) to post a comment. Connect with me on LinkedIn.
Let’s work together to build a culture of continuous improvement and psychological safety. If you're a leader looking to create lasting change—not just projects—I help organizations:
- Engage people at all levels in sustainable improvement
- Shift from fear of mistakes to learning from them
- Apply Lean thinking in practical, people-centered ways
Interested in coaching or a keynote talk? Let’s start a conversation.
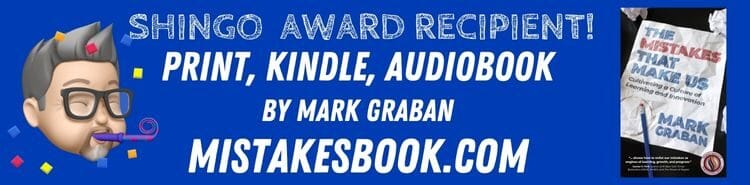