I had a great opportunity a few weeks back, seeing former Speaker of the House Newt Gingrich give a talk at the Ontario Hospital Association annual event in Toronto. I had a chance to meet him briefly and had a quick exchange about lean in healthcare, something for which Newt has long been a loud proponent.
He seemed genuinely interested when he asked about my talk the day before about lean.
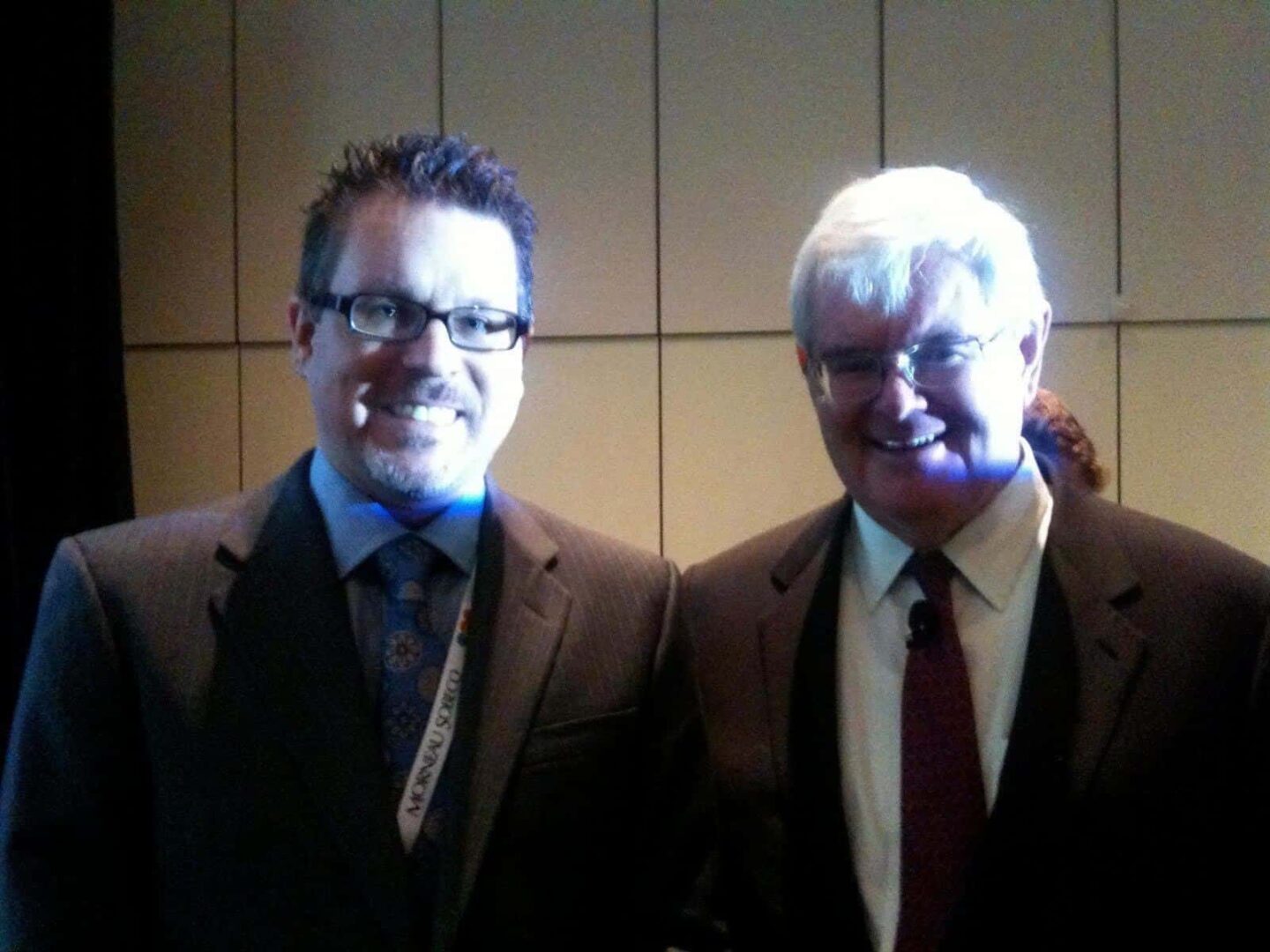
One of Newt's projects is the Center for Healthcare Transformation. He gave an endorsement for the back cover of Naida Grunden's excellent book The Pittsburgh Way to Efficient Healthcare: Improving Patient Care Using Toyota Based Methods:
Every person who cares about modernizing health in America should read this book. If we could understand the Toyota system in health, we would save thousands of lives and billions of dollars.
In his talk, the topic was “e-Health,” covering electronic medical records and the like. Very much a Lean Thinker, Newt encouraged the crowd to not look at technology as a silver bullet — they also have to work on process improvement, using methods including Lean. Newt spent much more time talking about process innovation than he talked about technology, which I really appreciated.
On the one hand, Newt said there is a moral case for Electronic Health Records and the positive impact on quality. On the other hand, technology alone is not enough. He said we have to combine continuous improvement and the Toyota model with technology to be successful. Newt said we have to get the silos working together, through better processes, to improve quality and safety.
Some points he made on the power of electronic systems:
- “Paper Kills” — EHR can improve safety and the patient must be a co-owner of that information.
- The cell phone is the future of medicine in public health — everybody has them.
- Imagine sending a video of your grandmother at 2 am to your doctor and the impact that could have on care.
- Expected efficiency improvements from not duplicating care and tests and using outcomes data to determine the best care.
- We can help “track down cheats and crooks” to detect and eliminate fraud (costing CMS between $70 and $120 Billion a year – news link).
Newt, being a historian (that's his PhD), gave an amazingly detailed history of Dr. Deming's influence on Toyota and the impact of lean on the auto industry.
Here's an audio clip:
He raised an excellent point that lean change is difficult since you're trying to change the culture. Lean geeks will know he didn't get every detail right (NUMMI is in Northern California), but Newt certainly has a deeper and more detailed understand of Deming, Toyota, and quality improvement than any other major political figure.
He raises a provocative question — how can we get every employee in the hospital engaged in making suggestions and improving processes? This is part of the coming “fundamental change in how we deliver healthcare — you're going to see a lot of Henry Ford-type moments.” I agree with his statement that we need “a workforce and people that are working together.”
In keeping with Dr. Deming's teachings and lean principles, Newt said this gem:
“Cost control is a bureaucratic term that never works.”
Ironically, focusing on costs often leads costs to go up. Improving processes and improving quality inevitably leads to true cost reduction. Newt understands that and we need his voice and those ideas in the healthcare debate.
He also understands the challenges of change management and leadership, saying:
“If you brute force a large enough change, you guarantee it will implode.”
That's something to keep in mind in our lean work and systems implementation. Are hospitals “brute forcing” the use of electronic systems by doctors? Are people truly working together or are hospital senior leaders just pushing new things on people?
Newt weaved in some other historical tales contrasting the Wright Brothers and the federal government in their development of the first airplanes. He pointed out how the Wright Flyer wasn't given to the Smithsonian for many decades due to a long-running feud and rivalry, where the Smithsonian refused to believe or credit the Wrights as the first to fly (see this news story).
The Wrights followed an iterative PDCA process, something that reminded me of Steven Spear's writing in Chasing the Rabbit, the idea that nobody designs a perfect system. What matters is how quickly you innovate.
Newt told of how the Wrights would test their plane over land, so each time it failed and crashed, they could repair the wood structure and try again. The Wrights had anticipated this failure by bringing extra wood from Ohio to North Carolina.
Contrast that to the Smithsonian approach of a big bang development process:
Underwritten by a $50,000 War Department contract, Langley tested an airplane on Oct. 7, 1903. Resembling a giant dragonfly, the “Aerodrome” (search) was 54 feet long and had two 48-foot wings.
When launched from a houseboat on the Potomac River, the Aerodrome “simply slid into the water like a handful of mortar,” reported observers. The effort was so dismal the New York Times editorialized that one million to 10 million years would be needed to develop an airplane.
After another failure on Dec. 8, Langley blamed faulty launch equipment — not his design. The discouraged War Department ended the project.
Nine days later, the Wrights flew their airplane 100 feet in 12 seconds — seemingly, straight into the history books.
Since the plane was in the Potomac, it was a total loss and they couldn't learn from the experience.
While, politically, Newt probably intends the story to point out the foibles of central government, it's illustrative in many ways. Is a hospital's EMR system a “big bang” that HAS to be right (is assumed to be right) the first time? Or are they taking an iterative Wright Brothers approach?
I'll be blogging soon about seeing Eric Ries, the Lean Startups guy, who tells similar stories about software startups – not surprisingly, the iterative approach works far better than the big bang development approach.
Please scroll down (or click) to post a comment. Connect with me on LinkedIn.
Let’s work together to build a culture of continuous improvement and psychological safety. If you're a leader looking to create lasting change—not just projects—I help organizations:
- Engage people at all levels in sustainable improvement
- Shift from fear of mistakes to learning from them
- Apply Lean thinking in practical, people-centered ways
Interested in coaching or a keynote talk? Let’s start a conversation.
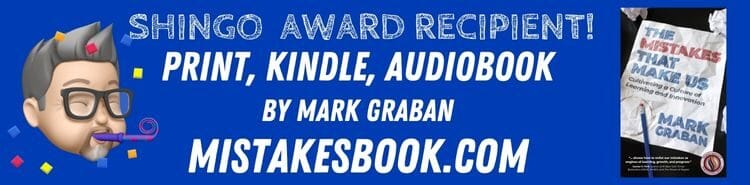
Mark, I've read about Newt Gingrich's speeches involving process improvement in other places. While it's nice to see someone talking about process improvements at a "federal" level, I don't think Newt is the right guy to give that attention to. I could not support him in good conscience, knowing how he acted during his time in the House. He is still too wrapped up in political matters to be something that other process improvement people can follow.
[…] using the “one big swing” approach – and they missed. It reminds me of the story Newt Gingrich told about the Smithsonian’s “big bang” approach to trying to build an airplane in an attempt to beat the Wright Brothers. Their one big swing sank […]
[…] by Mark Graban on June 10, 2011 · 0 comments I met Newt Gingrich at the Ontario Hospital Association conference in late 2009, as I blogged about here: “Meeting Newt Gingrich, a Lean Champion.” […]
there have been 8 Presidental Candidates sign the pledge to use Lean Six Sigma to remove $500B in Government waste. Newt Gingrich is a member of the LinkedIn Lean Six Sigma Group where you can also discuss where you can join in on the conversation. We will bring other leaders in too. I am glad all the leaders (except Obama), but I did say leaders, are supporting the Lean Six Sigma Methodology.
A comment like that makes this seem far from a bi-partisan effort.