Toyota Talent is the third, and newest, book in the “Toyota Way” series:
- The Toyota Way
, written by Dr. Jeffrey Liker
- The Toyota Way Fieldbook
, by Liker and David Meier
- Toyota Talent
, Liker and Meier
In this trilogy of books, each is very different and has its own unique place in the Lean literature. These books are unlike a series of novels, such as the Harry Potter series (I presume, not having read them), where you necessarily have to read all of them.
The Toyota Way is an outstanding overview of the Toyota methodology, philosophy, and management system. The book does an excellent job of describing how Toyota is, in a high-level manner that can be applied across industries, including the gap between manufacturing and healthcare. The Toyota Way is one of the very first books I would recommend to any executive or manager to get a sense of the overall Toyota system (helping them avoid the urge to implement selected lean tools without understanding the entire system.
The Toyota Way Fieldbook was not, as some might have thought, simply a paperback version of The Toyota Way. The Fieldbook was an altogether different book, with a different purpose. As effective as The Toyota Way was, the Fieldbook was necessary for filling in the gaps in a reader's mind, someone who thought, “Ok, I know how Toyota is…. but how do *I* get there??” The Fieldbook is more of a guide for “how to implement” the Toyota Production System. The Fieldbook is one I would recommend to managers or active practitioners in a lean transformation.
Now, the Toyota Way team is setting out to write what should be considered an altogether new trilogy and series of books — related to The Toyota Way and the Fieldbook, but with a different purpose. The three books in this series are going to be:
- Toyota Talent
- Toyota Process
- Toyota Problem Solving
These books will, I would assume, follow a similar structure and tone, each diving deep (Very deeply, based on Toyota Talent) into a single core idea in the Toyota Mindset.
Toyota Talent is *NOT* a book only for H.R. professionals. If you think that developing people is the job of H.R., then don't even bother reading this book. Developing people, getting the most out of your organization's human potential, is the job of every leader in a lean organization. If your idea of developing people is to fire your “bottom 10%” each year, replacing them with better talent then, again, save your $20 and buy another Jack Welch tome. I saw a copy in an airport bookstore the other day, which was nice to see, but it also struck me as odd, since that seems like the executive market that the publisher is targeting. I'm happy for Liker and Meier if that helps sell more copies.
So who *should* read this book, then? Well, I think different parts of the book have different audiences. The first section, Getting the Organization Ready to Develop Exception People, consists of four overview chapters. For the executive reader, I'd recommend the first two chapters, which provide a concise summary of the Toyota Way philosophy and how developing people supports lean and, more importantly, long-term business success.
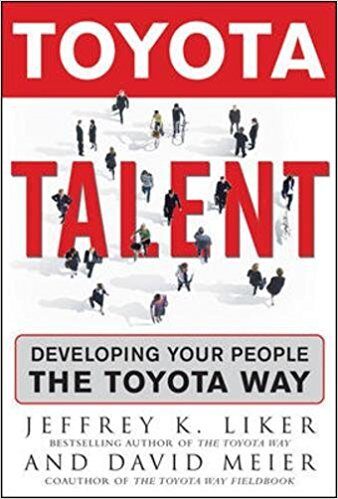
So I'm saying the executives shouldn't bother learning the details of Toyota Talent? In a perfect world, or an ideal lean organization, maybe executives would eat this stuff up. But, I think it's more realistic to have executives read the first few chapters so they can understand what their organization will be implementing. If time is tight, the rest of the book might contain too much detail. Let the line leaders and implementors digest the content and start implementing, coaching the executives with the distilled version (and key points) of Toyota Talent. If you disagree with that approach, please comment using the link at the end of this post.
Now, to the meat of the book. Toyota Talent really breaks new ground, rather than re-hashing things we've all read before. Unless you have a strong background in the Training Within Industry methodology, much of the book will be an eye opener, giving you approaches and tools that can be implemented immediately. Toyota Talent is written more along the lines of the Fieldbook, in the sense that the authors give you specifics that can be implemented, rather than just a description of Toyota's system.
If you're an active lean change agent (as a line manager or a consultant), this book is a must read. The book demystifies the world of Standardized Work and breaks it down into something concrete and practical. The book not only explains how to develop and implement a standardized work system, it also (in typical Toyota style), explains much of the “why” — why do we implement standardized work?
The book sets a tone of not standardizing for the sake of standardizing. The methodology focuses on figuring out what matters, and doing so by getting input from the value adding employees. Focusing on safety and quality is a key part of Toyota Talent‘s methodology. The book gives a method for breaking down the work content of existing jobs, using highly repetitive manufacturing examples as well as a highly variable healthcare environment (a nurse in a hospital). The method is presented in a way that DOES make sense for both environments, which might be a surprise to many readers.
Toyota Talent covers the entire standardized work process:
- Deciding what to standardize
- Breaking work content down and documenting standardized work
- How to train in a highly effective manner
The book builds upon the Training Within Industry methodology, as written about in other books. But, Toyota Talent explains how Toyota built upon the TWI framework to create something uniquely Toyota, but adaptable to almost any environment.
Even with my caveats (and maybe my cynicism about executive attention spans), I highly recommend Toyota Talent. It carves out a very unique, and helpful, place in the lean literature. It's a very readable book, written in a down to earth and practical style.
Have you also read the book? What did you think? What did you find to be helpful?
If you have questions, I can try to line up responses from Liker or Meier, in another blog post (maybe David will post or comment himself) or via a Podcast interview.
Updated: David Meier *has* agreed to do a Podcast interview, so let me know (via a comment or email) if you have a question for him.
Please scroll down (or click) to post a comment. Connect with me on LinkedIn.
Let’s work together to build a culture of continuous improvement and psychological safety. If you're a leader looking to create lasting change—not just projects—I help organizations:
- Engage people at all levels in sustainable improvement
- Shift from fear of mistakes to learning from them
- Apply Lean thinking in practical, people-centered ways
Interested in coaching or a keynote talk? Let’s start a conversation.
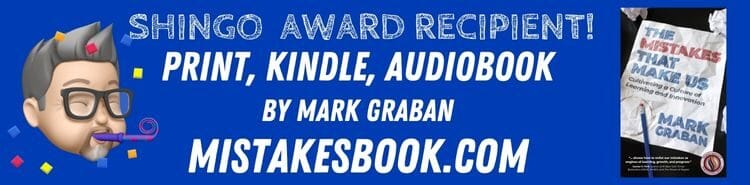
Thanks for the synopsis on the book. Sounds really good.
As far as a question for the Podcast or a general question for Mr Meier, do they have a timeline for the Toyota Process and Toyota Problem Solving books?
Mark,
Thanks for this thoughtful post. Being a TWI Zealot, I viewed my copy (got mine before Amazon!) as the biggest gift to the TWI community in decades.
Being a “heavy user” of TWI, particluarily Job Instruction, one question that often comes up is documentation. We are an ISO shop, and have developed many forms of documentation over the years. Many people rightfully view JI as “good tool, but yet another document”.
We have been using the Job Breakdown Sheet as a standard work document (our work is not yet synchronized enough to do a combination table format). We use an 11×17 format that looks much like a Toyota Standardized Work Chart (work elements/key points on the left, work diagram on right).
The question that arises is that this format does not provide a complete description of the job. It only includes the steps and key points, which by definition are only the 10-20% of the job that really makes a difference for a quality, safe outcome.
People have suggested that we should also have a document that attempts to spell out the whole job. The idea being “someone can read it and do the job”. My take is that we never really do that, and most people learn a job throught 1-on-1 training, which the JBS is designed to improve.
Either way, I’m interested in David’s thoughts on this. How many documents would a typical Toyota job of moderate complexity, perhaps an internal engine assembly operation or die changeover task, have and what kind of information is contained in each? Some of this is included in the book, but I still lack the whole picture…
Thanks, Jeff
I looked over the book expecting to find more details about the process structure like the famous DNA aritcal outlines.
Gerry
[…] Podcast #35 is another discussion with David Meier, co-author of the book Toyota Talent, written with Dr. Jeffrey Liker. In this podcast, we follow up our previous discussion (Podcast […]