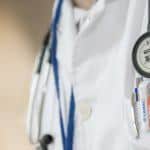
Episode #23 of the LeanBlog Podcast features a panel of Lean leaders from the Group Health Cooperative, a consumer-governed, nonprofit health care system that coordinates care and coverage. Based in Seattle, Group Health and its subsidiary health carriers, Group Health Options, Inc. and KPS Health Plans, serve over 500,000 members in Washington and Idaho. GHC has been on a Lean journey, as documented on their “Daily Kaizen” blog. Joining us on the Podcast are three of their Lean Leaders:
- James Hereford, Executive Vice President, Strategic Services and Quality
- Dr. Ted Eyan, Medical Director of Health Informatics and Web Services
- Lee Fried, Manager of the Strategic Consulting team at Group Health
In this Podcast, they discuss how GHC got started with Lean, their early “point improvement” successes, and their transition to a more systemic approach to a Lean management system through their “model line” efforts.
Click here for the main LeanBlog Podcast page with all previous episodes.
Show Notes and Approximate Time, Episode #23
- 1:15 James: Overview of the Group Health Cooperative (GHC)
- 2:00 Lee: How GHC got started on their Lean Journey in 2004, initial drivers
- 3:05 “RPIW” = Rapid Process Improvement Workshop (like a kaizen event)
- 3:30 Improved cost, quality, and delivery at the same time, in the lab, “wasn't believed possible in healthcare” and got senior management attention
- 3:55 Started with “point improvements”
- 4:15 Brought in some external consultants, education for the senior leadership team
- 4:30 Then moved from point improvements to large cross-departmental projects (e.g., health plan and delivery)
- 6:12 Looked at how to optimize the Electronic Medical Record system (involving IT and caregiver teams)
- 7:30 The model line, moving beyond point improvements and into cultural change –claims processing and customer service center (700 employees), HPA = Health Plan Administration
- 8:30 Had to make sure they weren't losing gains from earlier lean efforts — started doing more to fully ingrain lean concepts into the management practices and culture
- 9:15 Three components to the “Model Line” 1) Standard work of the daily management system 2) Value Streams and RPIW's to “turn the organization on it's side,” from functional organization to process organization and 3) hoshin kanri (policy deployment), building discipline around planning (goals and the means)
- 10:40 Ted: Have you had to adapt the lean management model to fit into a healthcare environment?
- 11:00 “Copy the thinking and the philosophy, not the tools”…. “What's the tool you can use? Your Brain!”
- 11:30 Focused on providing the right care at the right time, rather than relying on technology (or relying on “tried and true” technology)
- 12:15 “Lean Thinking blew my mind, everything had a corollary in medical care.”
- 12:30 “Toyota puts a lot of care and compassion into building cars, and so do we in taking care of people.”
- 12:48 “There things we don't want flexibility around” – certain medical situations that call for standard care
- 13:20 How did GHC try to get physicians on board and participating with Lean? “Patient at the center of care” is easy to get agreement with
- 14:00 “We want to take care of patients, and this helps you do it better… the system is more responsive.”
- 14:42 James: Are there advantages to being an integrated delivery system? “Our opportunity is so much greater…”
- 16:30 Ted: “If it can't be done at Group Health, it can't be done anywhere.”
- 16:50 Can GHC create more value through proactive or preventative health measures, ala TPM?
- 17:20 The goal is “lifelong health for our members… working with patients before they get sick.”
- 17:45 James: What have the benefits and results of the Model Line area been?
- 18:35 ThedaCare and John Touissant showed great humbleness even with their success
- 19:00 Doing as many kaizen events as you can wasn't enough.” Wanted to fundamentally change the leadership model, not the “all knowing and all doing” with the staff “checking their brain at the parking lot.”
- 20:00 The VP over the HPA area fully embraced Lean and change himself20:45 Had a rigorous, step-by-step method of teaching the skills and doing daily practice. The biggest change was getting the middle managers and VP to change the way they interacted with supervisors, that was the foundation for the operational changes (workcells, etc.)
- 22:00 Lee: RPIW's changed the thinking of a lot of folks, but it didn't get high enough to change the behavior of the leaders
- 22:50 Changing core thinking before changing core processes has led to better sustainment
- 23:10 James: Where GHC hopes this goes… the Model Line needs to be a model to learn from, applied in other areas, forcing the organization to think more about value streams and less about traditional budgeting processes
- 24:00 GHC now has a place in GHC to see lean (as opposed to continued visits to Genie or Virginia Mason Medical Center)
- 27:00 What kind of feedback are you getting from employees about Lean? (lab example)”This is the most amazing experience I have ever had in all of my experience at Group Health”
- 29:00 Ted on helping doctors and professionals meeting their goals
- 30:00 Lee: it can be hardest on the middle managers, having to change their ways
If you have feedback on the podcast, or any questions for me or my guests, you can email me at leanpodcast@gmail.com or you can call and leave a voicemail by calling the “Lean Line” at (817) 372-5682 or contact me via Skype id “mgraban”. Please give your location and your first name. Any comments (email or voicemail) might be used in follow ups to the podcast.
Please scroll down (or click) to post a comment. Connect with me on LinkedIn.
Let’s work together to build a culture of continuous improvement and psychological safety. If you're a leader looking to create lasting change—not just projects—I help organizations:
- Engage people at all levels in sustainable improvement
- Shift from fear of mistakes to learning from them
- Apply Lean thinking in practical, people-centered ways
Interested in coaching or a keynote talk? Let’s start a conversation.
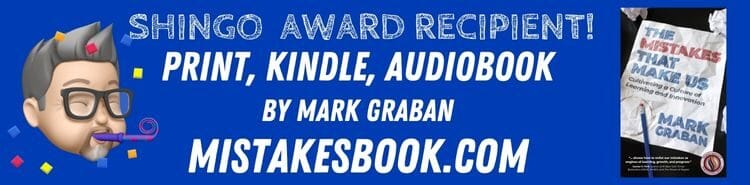
[…] Kaiser Permanente, who I met in person for the first time after years of phone calls and emails (my podcast with him when he was with Group Health, his blog and his […]
[…] by Mark Graban on November 22, 2011 · 0 comments Today, I’m linking to a post from a new blog written by the Ohio State University Fisher College of Business (“Think Op-Ex“). The post “What’s in a name?” features thoughts from James Hereford, formerly of Group Health (part of the group being interviewed in my old podcast). […]