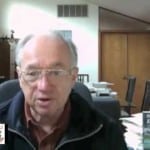
Here is LeanBlog Podcast #11, once again with Norman Bodek of PCS Press and the author of many books, including Kaikaku: The Power and Magic of Lean.
In this Podcast, we discuss a topic posed by a podcast listener, Bruce from Akron Ohio: how do you educate your top leadership about lean?
Norman and I discuss the perspectives of CEOs and executives toward lean, change, and their organizations and some examples of lean problem solving approaches.
It's a long podcast (about 40 minutes), so I'd suggest you check out the show notes to find times of specific topics if you want to jump around.
LeanBlog Podcast #11 Show Notes and Approximate Timeline
- 1:20 Question from Bruce in Akron again, how do you educate your top leadership about lean?
- 2:00 Norman spoke at the Lean Accounting Summit, even many CFO's were asking how to get their leadership on board, as if they were powerless
- 3:50 Norman tells a story about a President of a $2B company asking him, “how can I get my people to deliver quality?” After two weeks in Japan, he said, “Now I understand, it's not them, it's me.”
- 6:15 Developing a Quality and Productivity Plan, getting input from multiple company presidents within a corporation
- 9:00 Building consensus among 12 company presidents
- 11:00 Long-term strategic plans for Japanese companies
- 13:30 How do we educate our top leadership? Should we buy them books like Norman's “Kaikaku“?
- 13:50 Norman likes to ask, “If not me, who?” Who is going to do it? How are we going to empower people to work “bottom up” If you're a middle manager, you have take charge, quit living with fear
- 15:30 Is the boss necessarily smarter than you?16:20 A great story about convincing a boss to NOT outsource to Asia by asking him “what do you really want?” and working toward the cost reduction targets. How many companies go to China just to join that bandwagon?
- 17:50 “At this rate, we'd all better learn to speak Chinese,” Norman says
- 18:10 Schwinn bicycle outsourced to Taiwan, then the company learned and took over design, etc. and became a big brand, Giant bicycles. They didn't need Schwinn anymore.
- 19:20 People at all levels of the organization point fingers up and down about why we can't do lean
- 20:30 The waste of not utilizing human talent, that provides the most opportunity
- 20:45 Why do we outsource to China before we've reduced waste and made the most of people here, instead of re-organizing our plants to avoid outsourcing?
- 21:40 A lot of companies say they want to empower employees, but do they know how?
- 23:50 Should every employee be their own boss? Norman gives an example of employees and the boss working together in a problem solving example
- 26:10 Norman got chewed out by a client for telling a worker what to do to solve some defects, he was told “that's not what you're here for…” It's a lesson Norman forgets sometimes, you have to ask employees, not tell.
- 30:30 Toyota still has a hierarchy of leadership and “bosses” within the factory, how does that fit with Norman's idea of everyone “being their own boss?”
- 31:30 Why are front line employees typically powerless?
- 33:45 Why do some bosses think that information = power, so they withhold information?
- 34:45 Ohno set a goal of “remove this warehouse in one year” and didn't tell people how (other than “retrain people as mechanics”), he expected them to figure out the solution
If you have feedback on the podcast, or any questions for me or my guests, you can email me at leanpodcast@gmail.com or you can call and leave a voicemail by calling the “Lean Line” at (817) 372-5682 or contact me via Skype id “mgraban”. Please give your location and your first name. Any comments (email or voicemail) might be used in follow ups to the podcast.
Visit the main LeanBlog Podcast page with all previous episodes.
Please scroll down (or click) to post a comment. Connect with me on LinkedIn.
Let’s work together to build a culture of continuous improvement and psychological safety. If you're a leader looking to create lasting change—not just projects—I help organizations:
- Engage people at all levels in sustainable improvement
- Shift from fear of mistakes to learning from them
- Apply Lean thinking in practical, people-centered ways
Interested in coaching or a keynote talk? Let’s start a conversation.
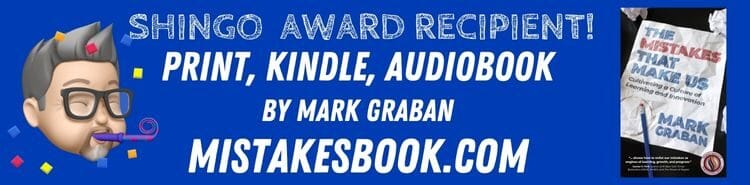
I think the idea of everyone being their own boss isn’t realistic at all. Is there any large organization in the world that runs that way? Even Toyota has managers, granted they manage different than traditional managers do. It’s not a good use of my time to hear about how everyone should magically be their own boss, that doesn’t help me be more lean. Lots of other good ideas from Norman, though, as usual. Just keep it realistic.
It would be very useful if something like http://www.veotag.com/ is used for the next LeanBlog Podcast
Osvaldo