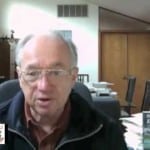
Here is LeanBlog Podcast #7, a new discussion with our friend Norman Bodek, President of PCS Press and the author of many books, including Kaikaku: The Power and Magic of Lean. In this Podcast, we discuss Toyota's response to recent quality problems and recalls along with other Lean leadership topics.
For earlier episodes, visit the main Podcast page, which includes information on how to subscribe via RSS or via Apple Podcasts.
LeanBlog Podcast #7 Show Notes and Approximate Timeline
- 1:40 What are Norman's thoughts on Toyota's recalls and their response of adding time back into the product development process to build in quality?
- 2:08 “When your model is being attacked, it's unnerving. Very often, people are looking for an excuse to not do something.”
- 2:50 Yes, Norman buys Toyota
- 2:57 The book 40 Years, 20 Million Ideas: The Toyota Suggestion System
- 3:50 How Toyota invests in people, their training and development and how “lifetime employment was a brilliant concept” because that investment in people is an investment in the company.
- 5:45 A few years ago, Norman visited Toyota Georgetown, why was the number of suggestions dropping? Employees had been getting $20 per suggestion, no matter how small and so employees “played the game and played it well.” So, Toyota stopped the program.
- 7:55 “The greatest respect you can show somebody is asking their opinion and listening to their ideas.”
- 8:10 Norman suggests that Toyota should have just changed their system to pay $20 for an idea “if it was worth $20.”
- 8:40 “Lifetime employment” or “lifetime improvement?”
- 9:10 As employees, do we learn and improve for the sake of “me” and “my career” or for “the company?” Norman says it's “sad” that I don't want to improve for the company's sake.
- 10:00 Although Toyota Georgetown does not have “lifetime improvement,” they have never laid off a worker.
- 10:10 Are Toyota “temp” workers treated differently? Do they get a similar sense of commitment for ideas and suggestions?
- 11:15 How “Quick and Easy Kaizen” focuses on what's good for the worker? How do you make your work more interesting and easier? Norman says, “The result will be better quality, safety, customer service, productivity…”
- 12:30 Back to Toyota's product development and quality
- 13:10 Motorola and product development engineers improving the process
- 14:00 “How can you ask employees to be innovative rather than needing to have everything controlled by management, as we do in America?”
- 14:55 Norman says, “Management is not trained extensively, as they should be”
- 16:10 Working every day to improve, as employee, in a highly competitive world
- 16:30 Sending work to China for cheaper labor to do non-value added work versus eliminating waste? Why?
- 17:40 What about Toyota describing product development problems as “bonehead mistakes?” Is that not showing “respect for people?”
- 18:00Toyota tries to take waste development out of the development process without working them too hard.
- 20:20 Why Norman likes the theme of “respect for people”
- Click here for Norman's Books and Videos from Amazon.com
If you have feedback on the podcast, or any questions for me or my guests, you can email me at leanpodcast@gmail.com or you can call and leave a voicemail by calling the “Lean Line” at (817) 372-5682 or contact me via Skype id “mgraban”. Please give your location and your first name. Any comments (email or voicemail) might be used in follow ups to the podcast.
Please scroll down (or click) to post a comment. Connect with me on LinkedIn.
Let’s work together to build a culture of continuous improvement and psychological safety. If you're a leader looking to create lasting change—not just projects—I help organizations:
- Engage people at all levels in sustainable improvement
- Shift from fear of mistakes to learning from them
- Apply Lean thinking in practical, people-centered ways
Interested in coaching or a keynote talk? Let’s start a conversation.
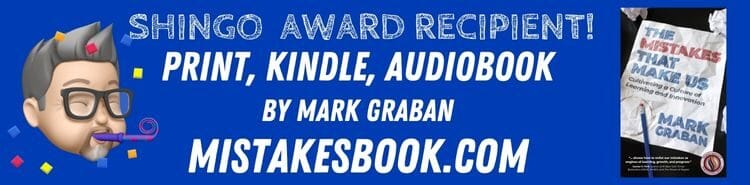