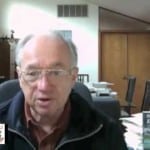
Here is the second LeanBlog Podcast, featuring author and consultant Norman Bodek, President of PCS Press.
The first one can be found here and you can visit the main Podcast page, which includes information on how to subscribe via RSS or via Apple Podcasts.
LeanBlog Podcast #2 Show Notes and Timeline
- More on airport near misses here and here
- 2:55 Respect for people, the key difference between Toyota and American companies who aren't maximizing lean
- 4:45 Why managers are responsible — not setting up the process properly and not giving power to the people who are in contact with the customer
- 6:00 Toyota realized that to give people respect, you have to give them power
- 6:30 In his first trip to Japan in 1981, Norman didn't see people waiting in the factories
- 6:55 How “jidoka” and the separation of man and machines allowed one person to run seven machines
- 8:21 Why it's OK to have the machine wait instead of having people wait
- 8:31 Norman is speaking at the Lean Accounting Conference
- 9:30 “The machine should be no bigger than five times the size of the part.”
- 10:45 How do we get managers to take responsibility for the design of the system?
- 11:55 How Fujio Cho changed the “line stop” by adding time buffers, so the whole factory doesn't shut down — why Taiichi Ohno wouldn't have liked that
- 12:20 Ohno liked the whole plant to shut down because it forces you to find the root cause
- 13:32 Why you don't criticize people as a manager, how to bring out creative ideas
- 14:54 “Toyota was the most ruthless organization in Japan… Ohno was a terror… but from this comes the most humanistic management system.”
- 15:34 “A Toyota manager is told to ask, not tell.”
- 16:55 “Blame closes people up like an oyster.”
- 18:39 Why we should want people to make their own work easier and more interesting
- 19:25 “If we want to compete with the Toyotas of the world, we have to learn how to bring out the best of our people.”
- 19:38 “We send work to China and Toyota comes here to make cars.”
- 19:50 Discussion of Toyota's hiring approach and selectivity
- 22:10 Our management system is broken…
- 23:00 How healthcare is better about no layoff pledges along with lean and how
that helps
If you have feedback on the podcast, or any questions for me or my guests, you can email me at leanpodcast@gmail.com or you can call and leave a voicemail by calling the “Lean Line” at (817) 372-5682 or contact me via Skype id “mgraban”. Please give your location and your first name. Any comments (email or voicemail) might be used in follow ups to the podcast.
Here is an amazon.com link to Norman Bodek's Books, and in particular:
Please scroll down (or click) to post a comment. Connect with me on LinkedIn.
Let’s work together to build a culture of continuous improvement and psychological safety. If you're a leader looking to create lasting change—not just projects—I help organizations:
- Engage people at all levels in sustainable improvement
- Shift from fear of mistakes to learning from them
- Apply Lean thinking in practical, people-centered ways
Interested in coaching or a keynote talk? Let’s start a conversation.
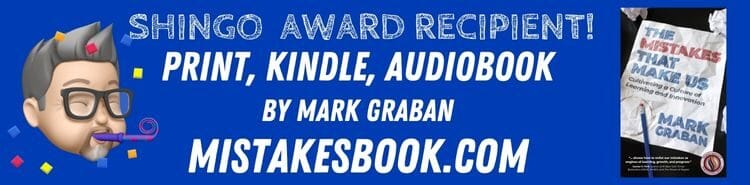
My name is Ed, and I’m currently an Assistant Manager at a Toyota Manufacturing facility in Indiana. Norman’s comments about Toyota are dead on. We here at Toyota think of problems as true opportunities. I’ve worked at GM & Ford alike, and the differences between the typical US manufacturing system and TPS are significant. It all boils down to identifying waste, Kaizen, and how you treat people. One last key note is that many companies read lean manufacturing books, implement the ideas and call themselves lean. This isn’t so, to be lean, it also takes a culture change in your organization, one which takes some, years to generate.
Hi Ed – Thanks for your visit to the blog and for your comments. Please come back often and let us understand more about the Toyota Production System and let us know if we (or I) are wrong about anything Toyota related.