See this article:
Society of Manufacturing Engineers: “Quality Scan: Six Sigma Isn't Lean“
The SME author, Geoffrey Mika, makes an attempt to debunk the idea that Lean + Six Sigma = “Lean Sigma.” He compares it to trying to cross-breed his Cat and his Poodle into something called a “Catoodle.”
Here is an image I created to illustrate this:
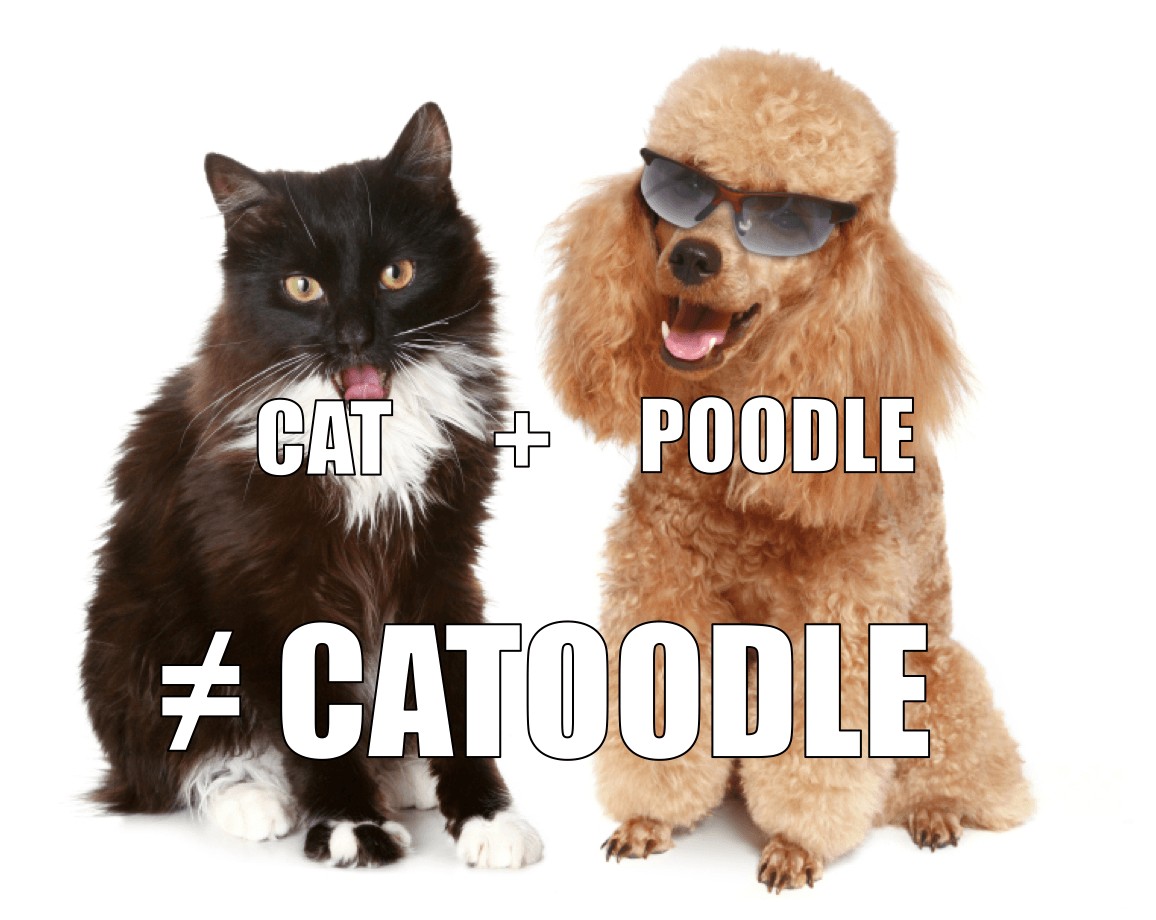
Mika has some pretty harsh words:
“Six Sigma is not a stand-alone philosophy which the average worker on the floor can embrace, like the Toyota Production System. It's a management tool for a very select few, certainly not worth the effort required to train an entire workforce on how to use or apply it. Like the Catoodle, there is no Lean Sigma.”
There are certainly parallels between aspects of Lean and Six Sigma (PDCA and DMAIC), and they can be complementary approaches.
But, in my most recent experiences with Six Sigma people (in manufacturing and at a hospital), I was thoroughly unimpressed with the results of Six Sigma. I saw lots of training and lots of green belt certificates, but few results and no culture change. I've seen “analysis paralysis” beyond belief — using complex Minitab and statistical tools to solve a problem (such as materials shortages) that was easily solved in a day using lean tools and common sense (put in visual controls and a kanban system).
I couldn't care less what fancy formulas you use if you can't fix anything or can't get results.
One hospital I visited showed me data that showed “the amount of time you waited for cancer treatment did not correlate with patient age.” Why would they have even thought there would be a correlation? How stupid. Just because you have data on 1) patient waiting time and 2) the age of each patient doesn't mean you should run Six Sigma statistical tests. Was there a reasonable explanation that the cancer treatment center staff was discriminating against older (or younger) patients by making them wait longer?
Episodes like that kill any enthusiasm I might have ever had for Six Sigma.
Please scroll down (or click) to post a comment. Connect with me on LinkedIn.
Let’s work together to build a culture of continuous improvement and psychological safety. If you're a leader looking to create lasting change—not just projects—I help organizations:
- Engage people at all levels in sustainable improvement
- Shift from fear of mistakes to learning from them
- Apply Lean thinking in practical, people-centered ways
Interested in coaching or a keynote talk? Let’s start a conversation.
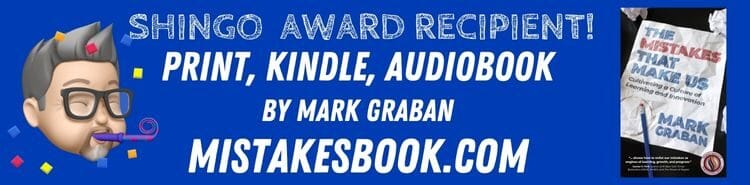
The worst thing about six sigma is that the leave all the skills in a handful of “experts.” These folks are to solve all the problems for everyone else. I saw a six sigma black belt sit at his desk and do a project by asking someone to email them the data, then emailed back the answer a few weeks later. So much for gemba. So much for involvement.
Don’t mistake the bus drive for the bus! Six Sigma is a tool and like any tool it can be used incorrectly. But it can work well in combination with Lean. Like any project if you’re not involving the workers doing the work you’re going to fail – that’s the same for Six Sigma, Lean, TQM or other practices.
As a tool of reduction of cycle time, waste, complexity, handoffs etc. VSM spans across Measure Analyze and Improve sections of the Six Sigma process. In reverse application if through Kaizen workthroughs a problem is identified of variation and defects, a 6S project on that area may help.
Just my 2 cents.
Tim C.
Good points by Tim C. There are many orgs (ITT, Cat, Ecolab) that are successfully using Lean and Six Sigma together to improve speed and quality of their processes.
If you refer to the combination as “Lean Six Sigma”, we can modify Mr. Kaizen Sinsei’s analogy a bit: he owns both a cat and a poodle. Why? Honestly, I can’t imagine:)but the idea is that they each make unique and complementary contributions to the household. No need to blend them at a genetic level and try to make each something it’s not – just use them together.
Not every company is Toyota. If combining Lean and Six Sigma gives an organization a path forward, then I think we should support it.
I think part of the debate is “do you combine lean and six sigma into a single methodology?” I agree that six sigma can be very useful. It can be applied or misapplied, much like lean.
But, I think lean is more of a holistic business strategy than six sigma is. I see six sigma as more of a “tool”. I think, as JP said, that lean and six sigma can and should co-exist, but that doesn’t make it “lean sigma”. Calling it “lean sigma” reeks of executive laziness (having to boil it down or dumb it down into a single thing, instead of understanding two things and how they fit together).
J&J has a methodology called “Process Excellence”, which has 3 pillars: Lean, Six Sigma, and Design Excellence. They don’t have 2 pillars, “lean sigma” and “design excellence.” I like how they view it and how they have the methodologies work together.
Six Sigma is a powerful methodology for working on complex problems for breakthrough. It does not bring any new tools to the mix, but it does bring tools to bear that lean does not, for solving a different set of problems. I would agree that Lean is more of an ongoing process management, continuous improvement system. Either approach can be used incorrectly (and both have, many times). Without the constancy of purpose from leadership, without statistical and systems thinking, and without some understanding of how people fit into the systems, ANY approach will fail.
I personally miss the TQM days, when we tried to build a quality (process management) system appropriate to the organization. A complete system will include at least components for process creation, ongoing process management, and process improvement. Unfortunately, after Deming died, too many splintered and specialized consulting groups picked up on methodologies like Six Sigma and TPS and turned them into competing approaches.
Mark,
I realize this is a rather old post (2006!), but I just read it and feel I have to comment. I read your blogs quite regularly because I find your posts insightful and applicable to my work. With this post, however, you to sound an awful lot like those who criticize lean because of some bad experiences (ie L.A.M.E.) Six Sigma is no different in that it’s application can often be misguided. I am currently a lean practitioner in healthcare, but my roots are Six Sigma. One of the things I’ve learned is that not every problem is a Six Sigma project. God knows I’ve seen many people try to build a Black Belt project around a preconceived solution in order to get their “certification”. I think we’d all agree this is wrong (let’s call it Lame Sigma). Six Sigma is about identifying and eliminating sources of variation in a process. If properly applied, it can be very powerful. A Six Sigma project should definitely include going to the Gemba and involving those closest to the work (part of the Measure phase). Yes, there is a focus on analysis of objective data, but that’s not a bad thing if project selection was done wisely. I’d be very happy to share some examples of Six Sigma applied properly (if you’re interested).
One thing I will note is most examples of six sigma in the wild I like LAME lean examples. You have poorly adopted half (if that) hearted efforts to do something and slap on the name six sigma and a few training sessions with belt certifications. Those efforts are more bad than good.
Here is a post of mine from 2006 also http://management.curiouscatblog.net/2006/03/15/six-sigma-wont-fix-bad-management/ If you want to give six sigma a fair shake look at what people like Roger Hoerl http://curiouscat.net/authors/144-Roger-Hoerl say. I would suggest a Deming based approach myself but if you want to give six sigma (or lean six sigma) a try use the ideas of people like Roger.
Steven-
OK, fair enough. I didn’t mean to sound that anti-six sigma.
But I’ll stand by my argument that there is no such thing as “Lean Six Sigma” or “Lean Sigma.” There might be “Lean and Six Sigma” but I think there are enough differences in the philosophy that we can’t just jam them together. Six Sigma certainly can be compatible with Lean.
Mark
Mark,
I’ll definitely agree with you on the “arranged marriage” of Lean and Six Sigma. One thing my Six Sigma training has taught me, however, is the value of objective data and how to do proper analysis. Since I left manufacturing for banking (and now healthcare), I haven’t had much use for “hardcore” Six Sigma tools such as regression and DOEs. I think lean practitioners would be well served, however, to learn more basic tools such as types of distributions, hypothesis testing and analysis of variances. I’ve seen far too many instances of chasing metrics changes that are due to nothing more than random fluctuation. This can be paticularly harmful when trumpeting savings of Kaizen events. Six Sigma tools can keep you honest in this regard.
We are on the same page about presenting data that’s not a statistically significant improvement…
I’d be curious to hear your thoughts on this more recent post about the use of SPC and run charts instead of simplistic two data point comparisons for events or other projects.
Link: https://www.leanblog.org/2010/10/consulting-case-studies-need-statistical-validity/
I gave it a read and I think you’re bang on, despite what your friend Tripp may say!