This is from the 3rd edition of my book Lean Hospitals. I've copied and pasted from the book with no additional edits, although I'll bold italic some parts for emphasis. I'll some closing thoughts at the end.
For a more complete PDF excerpt, click here (requires Dropbox access).
I also posted this on LinkedIn and there was a little bit of discussion generated if you want to check it out.
———————–
Kanban: A Lean Approach to Managing Materials
Kanban is a method that builds on the concepts of standardized work, 5S, and visual management to give health systems a simple yet effective method for managing supplies and inventory. Kanban is a Japanese word that can be translated as “signal,” “card,” or “sign.”19 A kanban is most often a physical signal, such as a paper card or a plastic bin, that indicates when it is time to order more, from whom, and in what quantity; it can also be an electronic signal that is sent by an automated cabinet or computer system. See Figures 6.10 (Children's Health, Dallas) and 6.11 (Rouge Valley Health System, Ontario) for examples of a laboratory kanban card and a pharmacy shelf that has been nicely organized and set up with kanban cards.
The kanban approach is sometimes mistakenly thought of as a system that just focuses on low inventory levels when its goals are actually to support the patients and the employees by ensuring needed supplies are in the right place, in the right quantity, and at the right time and to ensure the availability of material with the lowest required inventory levels. Kanban systems typically have fewer stockouts and better availability of materials than traditional materials management methods.
Trade-Offs with Inventory
In any system, there are trade-offs between high availability of materials and increased inventory costs, especially when the use of supplies is not perfectly predictable or steady. This is certainly the case in hospitals.
Generally speaking, the cost of inventory rises as we want to be more certain that we never run out. Industrial engineering and supply chain management principles teach us that inventory levels must unfortunately increase exponentially if we are to approach a guarantee of 100% availability for an item.
While our primary goal is to keep patient care flowing and ensure staff have the supplies they need, we sometimes have to look at the trade-offs and costs involved. This trade-off can be seen with expired or obsolete inventory. We cannot expect constant availability yet also insist there be zero wasted inventory. For example, if a hospital's blood bank needs to ensure that it never runs out of O-negative blood, it is inevitable that some waste (expired blood that has to be destroyed) will occur since it might be difficult to perfectly predict blood usage. Other industries, such as manufacturing, might not want to run out of a particular item because the cost of shutting down an automotive assembly line for an hour is very high. That, however, does not compare to the cost of a life lost because a critical blood component, medication, or supply was not available. When the cost of stockouts is high, we have to err on the side of excess inventory. For items that are less critical, or have a close substitute, we can more easily allow some risk of stockouts.
Another trade-off to consider is the frequency of ordering from outside vendors. If we order less often, we can order in larger quantities. This often leads to volume discounts from vendors, or we can spread out fixed ordering costs (such as the labor cost of cutting a purchase order and the often fixed shipping cost from the vendor) across more material. The downside with ordering less frequently is that we have higher inventory management costs, which include
- Cash tied up in inventory
- Space required for storage
- Labor required to move, count, and maintain inventory
- Risk of damage, obsolescence, or expiration
Ordering more frequently also reduces the overall risk of stockouts because we can reevaluate actual usage and respond more quickly if we are ordering small amounts weekly instead of large amounts quarterly.
The kanban method allows us to quantify an optimal reorder point for supplies. This formula considers a number of factors, including
- Average usage or demand for an item
- How frequently we consider reordering (often daily or weekly)
- The vendor's lead time for replenishing items
- Safety stock, considering the variation usage and variation in replenishment time and the cost of stocking out
The amount of safety stock required will depend on the amount of variation involved with a given part. If an item is critically important, has highly variable usage, and comes from an unreliable vendor who might deliver more in two days or two weeks, the hospital would hold a relatively high amount of safety stock.
The New York Health and Hospital Corporation (HHC) is using “just in time” ordering to replenish materials, as part of their Lean program called Breakthrough. As many organizations do in conjunction with their supply chain redesign efforts, HHC rationalized the variety of rubber gloves that are available. Instead of 20 different colors and thicknesses, there are now just two options available (in different sizes, of course). This saves HHC $4 million a year on gloves alone.33 In keeping with the principle of respect for people, changes like this should be made with significant staff and clinician participation, rather than being mandated from the top.
[End of Excerpt]
As I've written before on LinkedIn, I think it's unfair to blame “just in time” for the shortages of PPE, ventilators, and medications as we currently see in New York (and in other locales around the world). These shortages might also, sadly, be coming to your town.
Hospitals that have been “practicing Lean” to varying degrees (using JIT / kanban or other various strategies) are facing shortages. So are the hospitals that were NOT using Lean to any extent. I don't think hospitals that believed in stockpiling inventory have enough right now. The federal “strategic reserves” don't have enough supply (and that was intended to back up hospitals).
It's not accurate to say “Lean means low inventory.” I think it's more accurate to say that Lean means “better planning and problem solving.” It means identifying risks (through processes like “strategy deployment” and JIT really means having a fast, responsive supply chain that can quickly respond to reasonable spikes in demand.
The spike in demand right now has meant that hospitals that tried “high inventory” for critically important items don't have enough. Those who thought, “We'll just order more when it's needed” don't have enough. There are no easy answers, but the quick answer of blaming JIT doesn't seem accurate or helpful.
Please scroll down (or click) to post a comment. Connect with me on LinkedIn.
Let’s build a culture of continuous improvement and psychological safety—together. If you're a leader aiming for lasting change (not just more projects), I help organizations:
- Engage people at all levels in sustainable improvement
- Shift from fear of mistakes to learning from them
- Apply Lean thinking in practical, people-centered ways
Interested in coaching or a keynote talk? Let’s talk.
Join me for a Lean Healthcare Accelerator Trip to Japan! Learn More
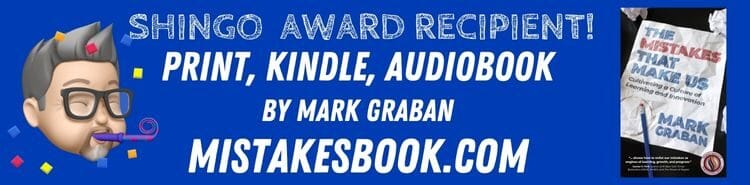
Mark, It’s an important point you’re making here, especially as we start to come out of this and fingers start pointing. It seems a good opportunity to better integrate supply chain functions, which will likely lead back to manufacturing flexibility. I haven’t heard that there are material shortages, just long ramp up times. May be some opportunities there, rather than scapegoating JIT.
Totally agree Mark. Wow, I was just going to make webinar for hospitals in Indonesia about lean in this pandemic state. because i saw what you said about blaming lean for shortage of PPEs or leaders feeling guilty for not being a faithful lean practitioners as they thought about minimal inventory. Thank you for reminding these specific paragraphs of your book.