My guest for Episode #395 is Michael Parent. He is Managing Director of his firm Michael Parent Consulting Services and he is a Lean Six Sigma Black Belt with the AAA Auto Club Group. Michael has a BS in Industrial and Operations Engineering from the University of Michigan and an MBA from William & Mary. Michael and I are both from the same home town, by the way — Livonia, Michigan.
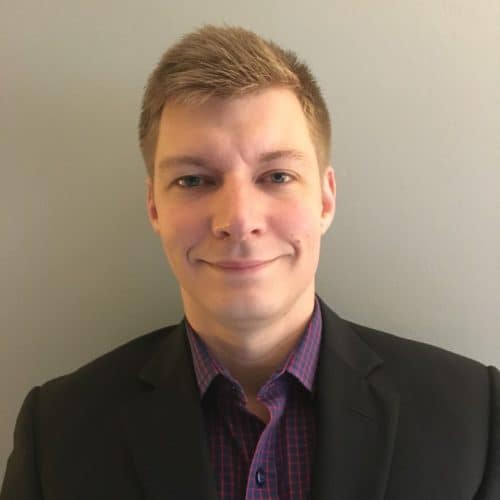
In today's episode, Michael first shares what he learned working for Bridgestone, a “typical Japanese company, ” as he puts it. He learned, among other things, that “culture is everything.”
We then talk about the LSS project that he led in HR and Talent Acquisition for the AAA Auto Club Group. What was the problem statement? “Time to fill” a position. What was the approach for the project? Who was involved and how? What was Michael's role as a facilitator? What was learned about the current state and variation in the work? How were the results and benefits determined? And, what were his lessons learned from this work?
His case study is available to read through iSixSigma.com.
You can listen to the audio or watch the video, below. I hope you enjoy the discussion.
Streaming Audio Player:
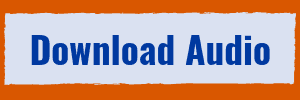
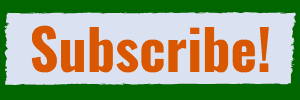
Video of the Episode:
For a link to this episode, refer people to www.leanblog.org/395.
Questions, Topics, and More
- Michael, please introduce yourself and tell us how you first got introduced to Lean and Six Sigma?
- Michael on Twitter
- Tell me about the Lean Six Sigma project that you wrote about related to HR and Talent Acquisition — what initiated this project?
- What was the problem statement? What was the goal? — time to fill
- What was the approach for the project? Who was involved and how?
- Facilitator not expert
- Gaining buy in?
- What was learned about the current state? Variation in the work?
- The case study talks about adopting standardized work — was there resistance to this and how was that addressed?
- How were the results and benefits determined?
- Dashboards and ongoing management?
- What were your lessons learned from the project?
- Lessons learned about Lean in office settings like HR and recruitment?
- Other types of projects that you've been working on? Working remotely?
- Tips for how to engage in virtual VSM?
- Structure of Belts at AAA? Working toward MBB?
Thanks for listening or watching!
What do you think? Please scroll down (or click) to post a comment. Or please share the post with your thoughts on LinkedIn – and follow me or connect with me there.
Did you like this post? Make sure you don't miss a post or podcast — Subscribe to get notified about posts via email daily or weekly.
Check out my latest book, The Mistakes That Make Us: Cultivating a Culture of Learning and Innovation: